Линия сборки поддонов PalletsLine — ПИФ-Мастер СПб 👌
Предлагаемая линия-станок для изготовления поддонов-паллет деревянных не имеет аналогов в России, как по производительности, так и по цене. Используя опыт более сотни предприятий по сборке деревянной тары мы создали для Вас готовое решение «PalletsLine».
Линия изготовления деревянных поддонов проста в эксплуатации и имеет неоспоримые преимущества:
- Изготовление поддонов до 800 шт. (легких) в смену (8 часов)
- Привлекательная цена
- Отсутствие аналогичных предложений на рынке
- Универсальность (размер поддона 600-1300мм., размер шашки 75-150 мм)
- Простота и высокая скорость перенастройки типоразмера (до 10 мин)
- Комплектность (в состав входит все, для установки линии за 2 часа, без привлечения квалифицированного персонала)
Для запуска линии изготовления и производства деревянных поддонов Вам потребуется только подключить компрессор к сети 380 Вольт и соединить воздушные фитинги – линия готова к выпуску готовой продукции.
Для обеспечения максимально заявленной производительности, Вам потребуется 3 человека-сборщика и один подсобный рабочий. Кондуктор сборки настилов позволяет (мы рекомендуем) использовать гвоздь со скосом.
Ниже приведена таблица сравнения различных станков для сборки поддонов:
Наименование станка | PalletsLine МэйнПак | Кондуктор TN1 | Автоматическая линия | Деревянный кондуктор |
Ориентировочная стоимость | 338 000 руб | 270 000 руб | 7 000 000 руб | 7 000 руб |
Производительность, поддонов в смену | 550 | 120 | 600 | 60 |
Требуемый персонал | 3 сборщика, 1 подсобник | 1 сборщик | 2 сборщика, 1 высоко квалифицированный настройщик | 1 сборщик |
Требование к эл.![]() | 50 Гц, 380 В | 50 Гц, 380 В | 50 Гц, 380 В | 50 Гц, 380 В |
Наличие пневмоприжимов | + | + | — | — |
Точность геометрических размеров поддона | + | + | + | — |
Наличие блоков подготовки воздуха и регуляторов давления | + | — | — | — |
Использование самозагибающегося гвоздя гладкий-скос | + | + | + | — |
Регулировка угла наклона кондуктора | + | — | — | — |
Быстрая перестройка на другой типоразмер | + | + | замена матрицы | — |
Оборудование для производства деревянных поддонов: станки, линии, технология
Изготовление поддонов – отличная тема для развития малого бизнеса, поддоны постоянно востребованы в сфере торговли и отраслях производства.
Предпринимателю нужно определиться с объемами производства, именно от требуемой производительности зависит, какое оборудование для изготовления деревянных поддонов выгоднее приобретать, правильно расставить приоритеты.
Производство поддонов
Особых сложностей при выполнении работ нет, но нужно наличие помещения, инструмента, оборудования и сырья. Технологический процесс включает в себя следующий перечень операций:
- распиливание заготовок на доски;
- обрезка доски;
- распиливание заготовок дерева на бобышки;
- торцовка бобышек;
- сборка готового изделия.
Работы простые, их может выполнять каждый, имеющий элементарные навыки и умеющий пользоваться циркулярной пилой, шуруповертом, дрелью.
Так как собранные поддоны не подвергаются никакой обработке – не окрашиваются, не грунтуются, то далее готовая продукция складируется для реализации.
Известно ли Вам, что качественное оборудование для производства гвоздей позволяет изготовить сегодня широкий спектр металлических креплений?
Что мы знаем о сэндвич или SIP панелях? Пройдите по этому адресу , чтобы узнать технологию производства сэндвич-панелей.
Подготовка сырья (древесины) для производства поддонов
Лучше всего для работы подойдет древесина, высушенная до содержания влаги в пределах 18-20%. Дешевле стоит лес с большим содержанием влаги, из него также можно делать заготовки и собирать поддоны.
Но потом готовые изделия все равно нужно будет подсушивать, что потребует и обогрева, и специального помещения, так что все-таки выгоднее сразу платить за лес нужной кондиции, тогда и продукция выйдет более качественной.
Имеет смысл наладить партнерские отношения с производителями пиломатериалов напрямую, без посредника: при более выгодной стоимости будет постоянное поступление сырья хорошего качества.
Можно сэкономить на транспортировке, если помещение по производству поддонов будет располагаться недалеко от источника леса.
Сырьем для поддонов считаются доски 2-3 сортов, бруски или шашки, изготовленные путем склеивания опилок. Требования к пиломатериалам регламентируются ГОСТ 9557-87. Для скрепления деталей понадобятся гвозди.
Доски можно использовать как необрезные, так и полуобрезные. Бруски цельные для шашек обойдутся примерно вдвое дороже, чем клееные.
Деревянные поддоны при небольших объемах можно выполнять без специального помещения и вложения капитала в покупку оборудования. Но если налажен сбыт в приличных количествах, то без обустройства мини-цеха (или большого цеха) не обойтись.
Оборудование для производства деревянных поддонов
Стол для производства поддонов выставляется горизонтально, на нем есть ограничители по ширине и длине заданного поддона; выставляются сначала в специальные гнезда шашки, на них – доски днища, один или двое рабочих (в этом случае они работают одновременно, с двух сторон) крепят гвоздями. По сути, это тоже кондуктор, только примитивный.
Очень поможет ускорить процесс устройство, не занимающее много места, но при помощи этого кондуктора для производства поддонов можно фиксировать размеры готового изделия и контролировать правильность углов; для удобства работы его можно расположить под нужным углом.
Используя такой кондуктор, производительность значительно вырастает, так как рабочий высвобождается от нескольких операций – замеров, фиксации, контроля линейных размеров и прямоугольности. Кондуктор для изготовления деревянных поддонов Palleton имеет производительность в 200 поддонов в смену.
Большой объем готовой продукции можно получить, используя оборудование для производства деревянных поддонов. Следует взвесить, достаточно ли будет покупки кондукторов и станков, или есть необходимость в линии. Полуавтоматическая линия менее производительна, чем полностью автоматизированная, но и стоит на порядок ниже.
Автоматические линии стоят очень дорого, имеют высокую производительность, срок службы таких линии – около 10 лет.
Сравнительно недорогой станок для производства керамзитоблоков позволяет быстро изготовить высококачественный строительный блок.
Салоны красоты сегодня повсюду. Здесь узнайте про итальянское оборудование для салонов красоты.
Или на странице http://buisiness-oborudovanie.com/dlya-xoztovarov/oborudovanie-dlya-izgotovleniya-svechej/ почитайте про оборудование для производства церковных свечей.
Линия для производства поддонов
Отличным помощником может стать станок для автоматической торцовки, компактный и высокопроизводительный. Станок торцовки кубика поддона Optima CT500А безопасен, производителен, с высокой точностью.
Зачищают стороны и углы поддонов при помощи станка обработки поддонов Оптима-А.
Станок для производства поддонов высокого качества, надежный, выпускается итальянской фирмой STORTI. Работает так: рабочие выставляют на стенд шашки и доски в соответствии с заданными размерами поддонов, стенд подает заготовки в станок для скрепления гвоздями.
Линия по производству поддонов полуавтоматическая способна выдать 1-1,5 поддона в минуту, что впечатляет. Такая линия б/у обойдется намного дешевле.
Пример такой полуавтоматической линии – PalletsLine.
Примером автоматических линий могут служить автоматы фирмы STORTI. Их основа – гвоздезабивной станок, один или 2. Производительность первой линии – 1,5 поддона в минуту, второй – 5 шт. в минуту.
Информацию можно обобщить, выделив главные моменты:
- производство такой тары, как поддоны, выгодно и постоянно в спросе;
- попробуйте наладить отношения с лесопроизводителями напрямую;
- определитесь с рынками сбыта поддонов, чтобы не работать на склад;
- трезво оцените, готовы ли вы вложить немалый капитал в приобретение серьезного оборудования изначально;
- если стартовый капитал ограничен или отсутствует, попробуйте при помощи стола и кондуктора наработать капитал и расширить рынок сбыта.
Видео о производстве поддонов
Republished by Blog Post Promoter
Сборочная линия для производства деревянных поддонов любого размера
Состав и описание:
Линия станков представляет собой столы-шаблоны с пневматическим приводом для сборки качественного и геометрически правильного деревянного поддона по заданным размерам. Задачей комплекта является оптимизация процессов сборки поддона, путем соединения нескольких разных функций станков в единую функцию, а именно — одновременное подрезание углов со всех четырех сторон на последнем этапе сборки
поддона.
Достоинства:
- Не требуется времени на перемещении поддона к станку для подрезания углов, так как эта операция производится одновременно с процессом сборки;
- Специальные пильные диски, с вольфрамовыми твердосплавными зубьями, обеспечивающими чистый и ровный рез;
- Отдельные группы всех элементов на каждый узел дают возможность удобной настройки и обслуживания;
- Не требует высокой квалификации персонала;
- Не требует большого количества сотрудников;
- Низкие затраты на ремонт и обслуживание;
- Быстрая переналадка станков для изменения типа размера выпускаемой продукции.
Технические характеристики
- Возможность изготовления станка под размер поддона заказчика: от 600х600 мм до 6000х2500 мм
- Необходимое давление пневмо-системы: 8 Атм
- Диаметр пильных дисков: 150 мм
- Мощность двигателя привода пилы: 1200 Вт
- Количество оборотов пильного диска в минуту: 10000 Об/мин
- Электрическое напряжение: 220 V
- Потребление электроэнергии: 1 КВт на 250 поддонов
- Положение наклона в градусах: 60/70/80
Гарантия:
- На все производимое нами оборудование, предоставляется гарантия 12 месяцев.
Связаться с нами
Автоматическая линия для производства поддонов CHT
Преимущества
| |
Опции, описания
СОСТАВ ЛИНИИ
CHТ 02 ГИДРАВЛИЧЕСКАЯ ГВОЗДЕЗАБИВОЧНАЯ ЛЕНТОЧНАЯ МАШИНА
Гвоздезабивочная машина CHT отличается наличием на столе оператора цепи с 7 шаблонами, что сильно оптимизирует процесс сбивки. Обычно в линии со средней производительностью поддон сбивается на двух таких машинах. Сначала сбивается нижняя часть, затем на второй машине верхняя.
- Гидравлическая гвоздезабивочная машина DELTA СНТ 02 для производства деревянных поддонов с максимальными рабочими размерами 1400 мм в длину и 1200 мм в ширину.
- Конструкция из стальных труб высокой прочности.
- Гидравлическая клепка с амортизирующими цилиндрами с масляной средой, гидравлическая установка с масляной средой с низким уровнем шума, электроклапан с пропорциональным контролем направления и постепенным регулированием продвижения клепки.
- Теплообменник для поддержания постоянной температуры масла в гидравлическом контуре.
Это позволяет тяжелые условия использования оборудования без повреждения самого контура.
- Движущаяся штанга с молотками на ходовых валиках из специальной закаленной и хромированной стали.
- Сцепление перекладины на стальных втулках с шаровой рециркуляцией; автоматическая смазка с выдержкой времени и программируемым периодом работы от 6 до 12 месяцев.
- Безопасность в соответствии с нормами ЕС.
- Автоматизированная последовательность операций, контролируемых P.L.C. (Processing Loading Control).
- N. 26 PZ 01 Молотки из оцинкованной стали, с индивидуальной пневматической блокировкой, с исключением не используемого молотка.
- Использование гвоздей «в россыпь» позволяет существенно снизить стоимость производства.
- Механизм подачи гвоздей с пневматическими цилиндрами с масляной средой на 15 гвоздей каждый (Ящики с гвоздями)
- Самовыравнивающаяся клепальная шпала, которая может автоматически выравнивать уровень над заготовкой перед фазой клепки.
GPT 180° (RB 10) ЛЕНТОЧНЫЙ ПЕРЕВОРАЧИВАТЕЛЬ
Предназначен для автоматического переворачивания поддонов без остановки конвейера линии.
- Конструкция из высокопрочной стали
- Переворачивание на 180°.
- Ленты с ячеистой структурой.
- Два отдельных электромотора.
- Регулировка натяжения лент.
- Цементированные и закаленные движущиеся колесики.
- Устройства для обеспечения безопасности в соответствии с нормами.
- Возможность использования переворачивателя в качестве транспортера.
CHТ 02 ГИДРАВЛИЧЕСКАЯ ГВОЗДЕЗАБИВОЧНАЯ ЛЕНТОЧНАЯ МАШИНА
Гвоздезабивочная машина CHT отличается наличием на столе оператора цепи с 7 шаблонами, что сильно оптимизирует процесс сбивки. Обычно в линии со средней производительностью поддон сбивается на двух таких машинах. Сначала сбивается нижняя часть, затем на второй машине верхняя.
- Гидравлическая гвоздезабивочная машина DELTA СНТ 02 для производства деревянных поддонов с максимальными рабочими размерами 1400 мм в длину и 1200 мм в ширину.
- Конструкция из стальных труб высокой прочности.
- Гидравлическая клепка с амортизирующими цилиндрами с масляной средой, гидравлическая установка с масляной средой с низким уровнем шума, электроклапан с пропорциональным контролем направления и постепенным регулированием продвижения клепки.
- Теплообменник для поддержания постоянной температуры масла в гидравлическом контуре. Это позволяет тяжелые условия использования оборудования без повреждения самого контура.
- Движущаяся штанга с молотками на ходовых валиках из специальной закаленной и хромированной стали.
- Сцепление перекладины на стальных втулках с шаровой рециркуляцией; автоматическая смазка с выдержкой времени и программируемым периодом работы от 6 до 12 месяцев.
- Безопасность в соответствии с нормами ЕС.
- Автоматизированная последовательность операций, контролируемых P.L.C. ( Processing Loading Control).
- N. 13 PZ 01 Молотки из оцинкованной стали, с индивидуальной пневматической блокировкой, с исключением не используемого молотка.
- Использование гвоздей «в россыпь» позволяет существенно снизить стоимость производства.
- Механизм подачи гвоздей с пневматическими цилиндрами с масляной средой на 15 гвоздей каждый (Ящики с гвоздями)
- Самовыравнивающаяся клепальная шпала, которая может автоматически выравнивать уровень над заготовкой перед фазой клепки.
TIM T6 МАРКИРОВОЧНАЯ МАШИНА С 6 КЛЕЙМАМИ
Предназначена для маркировки поддона путем выжигания клейм на наружных поверхностях шашек (от 2 до 6 клейм).
- Конструкция из стальных труб соответствующего размера.
- Моторизованный цепной транспортер.
- 6 боковых клейм.
- 2 сопротивления по 600 Вт каждое.
- Пневматические цилиндры с соединениями из VITON, предназначенные для работы при высоких температурах.
- Боковая направляющая против искривления.
- Возможность исключения не используемых цилиндров.
- Автоматическое управление при помощи концевых переключателей.
- Регулируемая температура печати.
- Регулируемое время печати.
- Клейма в поставку не входят.
- Оборудование для вытяжки дыма не входит в поставку.
SMTB ФРЕЗЕРОВОЧНАЯ МАШИНА ДЛЯ СНЯТИЯ ФАСОК
Предназначена для фрезерования внутренних поверхностей боковых досок поддона для удобства захода вилки погрузчика.
- Конструкция из труб большой толщины.
- Экструдированные моторы по 2.25 кВт каждый.
- Ручная регулировка глубины разреза.
- Втулки с шаровой рециркуляцией.
- Пневматические цилиндры, чтобы гарантировать сцепление с фрезой без вибраций.
- Крепления для вытяжки пыли (вытяжка не включена в поставку).
- Суммарная мощность 15 кВт.
TGAN СТАНОК ДЛЯ ОБРЕЗКИ УГЛОВ
станция предназначена для подрезки углов сбитого поддона. Углы подрезаются 4-мя дисковыми пилами с пневмоподачей.
- Регулировка глубины шага нарезки на цементированных перекладинах.
- Втулки качения с шаровой рециркуляцией.
- Пневматические цилиндры для автоматической нарезки при помощи концевого переключателя.
- Движение на перекладинах и втулках с шаровой рециркуляцией.
- Крепления для вытяжки пыли.
- Лезвия большого диаметра (опционально лезвия для обтесывания).
- 4 экструдированных мотора из алюминия по 2.25 кВт каждый со страховочным тормозом.
RBF АВТОМАТИЧЕСКИЙ ПЕРЕВОРАЧИВАТЕЛЬ ПОДДОНОВ
- Электрический вилочный переворачиватель поддонов.
- Предназначен для переворачивания поддонов на 180° вокруг горизонтальной оси перед подачей в штабелирующее устройство.
- Выполнен из независимых стальных элементов.
IMP/MAG ГИДРАВЛИЧЕСКИЙ ТРАНСПОРТЕР ВЫГРУЗКИ
Предназначен для автоматической укладки поддонов в штабель для последующей транспортировки или сушки.
- Конструкция из стальных труб соответствующего размера.
- Транспортировочная цепь типа «жалюзи» из нержавеющей стали
- Цепь движется по направляющим, изготовленным из материала Polyzen.
- Электромотор, управляемый инвертером
- Поперечная регулировка на перекладинах и втулках с шаровой рециркуляцией
- Гидравлическая платформа для штабелирования готового продукта.
- Автономная контрольная установка
- Регулируемые пневматические стопоры выравнивания
- Мощность кВт 4,75
оборудование, технология, рентабельность. Европоддон :: SYL.ru
Поддоны (паллеты) являются незаменимыми на любом складе. С их помощью перемещается и хранится груз, разгружаются товары, облегчается их учет и многое другое. Как осуществляется производство поддонов, на каком оборудовании, какова технология их изготовления и рентабельность, читайте в статье.
Общие сведения
Поддоны впервые были изготовлены в Соединенных штатах Америки в начале 20 века. На них складировали груз при его перевозке в вагонах, поэтому размеры поддонов соответствовали их габаритам. На сегодняшний день эти размеры считают стандартными, но область применения паллет намного расширилась.
В нашей стране большую популярность приобрели поддоны, размеры которых соответствуют европейским стандартам: 120х80 сантиметров. В настоящее время освоено производство поддонов разного типа и размера в зависимости от параметров груза.
Классификация
В зависимости от способов погрузки и расположения грузов различают:
- Двухзаходные поддоны и четырехзаходные. Это зависит от того, как вилы автопогрузчика вводятся под дно паллет: с двух сторон или с четырех.
- Однонастильные поддоны (одностороннее размещение груза) и двухнастильные (груз размещается по обеим сторонам).
- Поддоны с однократным и многократным использованием. Первые используются при транспортировке груза в отдаленные районы или другие страны. Возвращать их оттуда проблематично или нерентабельно.
- Складные поддоны и неразборные.
Производство поддонов
Технология зависит от способа изготовления паллет, который бывает ручным, частично автоматизированным (используется вспомогательное оборудование) и с применением автоматической производственной линии.
Любой способ будет рентабельней при наличии собственной пилорамы. Стартовый капитал для приобретения материала и необходимого оборудования очень скоро окупится. Уже через несколько месяцев производство поддонов начинает приносить прибыль. Оборудование, к которому относится ленточная рама, кромкообрезной и торцовочный станок, обычно используется при выполнении других работ, связанных с обработкой дерева.
Ручной способ
Производство деревянных поддонов таким способом не отвечает высокому качеству, поэтому крупные компании приобретают их не охотно. Но невысокая цена и отсутствие информации о способе производства, которую умышленно скрывают изготовители, привлекает покупателей и поддоны быстро раскупаются.
Мастеру для работы нужно немного: пиломатериалы, гвозди и молоток. Производительность труда при таком способе небольшая, 80-150 единиц продукции за 8 часов работы.
Полуавтоматический способ
Изготавливая поддоны с привлечением вспомогательного оборудования, повышается производительность труда. За одну рабочую смену, равную восьми часам, можно изготовить 300-600 поддонов. Такой способ производства паллет является самым распространенным. Используется следующее оборудование:
- Пистолеты гвоздезабивные (нейлеры), которые бывают пневматическими, электрическими и газовыми.
- Стол монтажный для сборки паллет.
- Станок, на котором обрезаются углы поддонов.
- Линия комплексной сборки. В ее состав входит несколько станин, каждая из которых осуществляет определенную операцию с поддоном.
Автоматический способ
Линиями, оснащенными станками и агрегатами, может располагать завод по производству поддонов, который выпускает большой объем продукции или небольшой цех. Выбор отечественных и зарубежных автоматических линий в настоящее время очень большой, но наиболее привлекательными являются два типа:
- В основу первого входит гвоздезабивная машина СНФ-02. Такая линия за одну минуту производит полтора поддона. Обслуживают линию два оператора и один погрузчик.
- Второй тип автоматической линии основан на использовании двух гвоздезабивных машин.
Производительность составляет 5-7 паллет за минуту. Преимущество такой линии в переключении станка на изготовление поддонов с другими размерами.
Технология производства паллет из дерева такова:
- Сначала в шаблоны гвоздезабивной машины закладывается пиломатериал в виде брусков или досок.
- Затем ножки и основная часть поддона сбиваются за один проход машины по 2-м шаблонам.
- После того, как гвозди забиты, шаблон вместе с ножками возвращается оператором назад, а ножки помещаются в шаблон основной.
Европоддоны
Они предназначены для того, чтобы на них складировать товар. Благодаря паллетам повышается технологичность всех процессов при перевозке любых товаров. На строительные объекты кирпич, бетон, цемент и прочие материалы доставляют на европоддонах.
Они изготавливаются их ольхи, осины, ели, сосны, влажность которых должна быть не меньше 24%. Европоддон, размеры которого соответствуют европейским стандартам (800х1200 миллиметров), состоит из строганных досок. Не следует путать эти поддоны с американским аналогом, размеры которого больше – 100х100 сантиметров.
Все элементы скрепляются ершенными гвоздями, которые обеспечивают высокую прочность. Европоддон, размеры досок которого неодинаковые, состоит из 20 элементов. Общий вес паллета небольшой (10 килограммов), но на нем перевозятся грузы массой до 2,5 тонн. Это достигается за счет того, что шашки размещены, а доски по ширине чередуются правильно.
Оборудование
Если деревянные паллеты производятся для собственных нужд, небольшими партиями, используется универсальное оборудование для производства поддонов. Раскрой бревен поперек производится цепной ручной пилой. Выпилить брус и раскроить его на доски можно на лесопильной раме или распиловочном горизонтальном станке. На торцовочном агрегате, пилы которого расположены снизу и сверху, раскраивают брус на шашки и торцуют доски в размер.
При образовании на заготовках дырок от выпавших сучков их заделывают пробками. Специальных станков для таких операций в нашей стране не производят, а на импортное оборудование цена очень высокая. Поэтому пробки изготавливают на сверлильных станках, которые оснащены полыми сверлами.
Для крупного предприятия, которое специализируется на производстве деревянных поддонов, этого оборудования недостаточно. Для обеспечения нужной мощности нужна специальная техника и станки.
Предъявляемые требования
Производство поддонов осуществляется из древесины мягких лиственных и хвойных пород деревьев, а также березы. Для изготовления паллет используется низкосортный пиломатериал. Его влажность не должна быть больше 25 процентов.
Пороки на древесине не допустимы: чужеродные включения, рак, острые или тупые обзолы, повреждения механического характера и трещины, идущие от торцов в глубину на 5 сантиметров и больше.
Заготовки для поддонов должны быть цельными, сращивать их запрещается. В местах установки крепежных деталей и на ребрах крайних досок настила снизу не допускается присутствие сучков. Если они во время обработки досок отпали, образовавшиеся отверстия заделываются пробками из дерева той же породы. Поддоны должны быть обязательно промаркированы.
Обработка паллет
На каждом поддоне обязательно ставится клеймо, подтверждающее прохождение фитосанитарной обработки согласно действующим стандартам с указанием названия партии, страны-изготовителя, метода обработки. На европоддонах дополнительно указывается, под каким номером выпущена партия и год ее изготовления. Обработку поддонов производят тремя способами:
- Фумигацией – когда для обработки используется бромистый метил, нейтрализующий всех вредителей и болезни. Этот способ не пользуется популярностью у производителей, так как после санитарной обработки свойства древесины изменяются: поверхность поддона покрывается тонким слоем состава. На таких паллетах хранить продукты нельзя.
- Тепловой обработкой, которая заключается в том, что поддоны на длительный срок помещаются в камеры с высокой температурой. Вредоносные бактерии в таких условиях нейтрализуются. Недостатком обработки является дороговизна оборудования.
- Камерной сушкой, которая является распространенным и наиболее эффективным способом. Заключается он в следующем: пиломатериалы для производства поддонов помещают в камеру с определенной температурой и влажностью и выдерживают какое-то время. Технология автоматизирована, камера оснащена датчиками. Как только значения температуры и влажности достигнут необходимой величины, приборы автоматически выключаются.
Кто покупает поддоны?
Продажа поддонов в розницу не имеет смысла. Нужно искать оптовых покупателей среди крупных компаний. Потенциальными приобретателями паллет могут быть:
- Компании, перевозящие грузы во все страны мира.
- Предприятия, производящие товар: станки, мебель, бытовую технику и прочее.
- Тепличные и фермерские хозяйства, сбывающие продукцию.
- Центры торговли и крупные рынки.
- Компании, специализирующиеся на оказании складских услуг, которые берут на хранение различные товары.
Рентабельность
Бизнес по производству паллет — очень выгодное дело. Рентабельность производства поддонов зависит от того, какова стоимость сырья. Поэтому начинать такой бизнес предпочтительней в регионах с развитой индустрией деревообработки. Здесь сырье можно приобрести по выгодной цене.
Рентабельность обсчитывается следующим образом. Зная стоимость одного кубометра доски можно высчитать себестоимость готового поддона. При продаже цена на него увеличивается. Производительность линии по изготовлению паллет известна. Легко высчитать количество выпускаемых поддонов за час, день, месяц, год. Из суммы годового дохода вычитаются расходы на налоги, оплату коммунальных платежей, заработную плату всему персоналу предприятия. Оставшаяся сумма и будет чистой прибылью.
Оборудование для изготовления поддонов — Общие
Чем наше предложение отличается от других? Тем, что мы не даем заоблачные теоретические, рекордные, а чаще всего из головы взятые цифры. Некоторые продавцы подобного оборудования заявляют «космическую» производительность, но достаточно взять в руки калькулятор, представить себе реальный процесс производства и все встанет на свои места.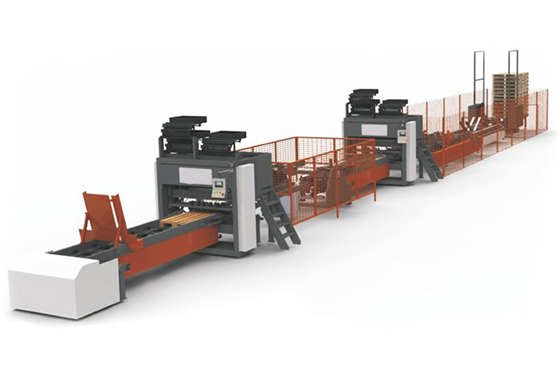
К основным требованиям можно отнести следующие:
Паллетный рынок России требует недорогие качественные поддоны. При этом конкурентность рынка чрезвычайно велика. Рынок завален дешевыми поддонами. Для того, чтобы выжить, производитель должен снижать себестоимость поддонов. При этом затраты на оборудование должны быть невысокими, так как большая часть производителей не может позволить себе дорогие вливания в производство. Да и зачастую в этом просто нет экономического смысла.
Снижать себестоимость поддонов можно следующими способами:
— использование более дешевой древесины (не всегда возможно из-за увеличения количества брака поддонов, связанного с плохим деревом)
— использование более дешевой рабочей силы (проблема кадрового вопроса все еще сильна, плюс квотирование иностранной рабочей силы)
— использование более дешевых гвоздей (цена на гвозди колеблется в небольших пределах и существенную разницу, которая могла бы дать конкурентное преимущество, Вы не увидите)
— использование гвоздей других размеров с хорошими крепежными свойствами (вполне возможно, главное, чтобы это удовлетворяло заказчика и соответствовало требованиям ТУ и ГОСТ)
И наконец:
— оптимизация производства: снижение себестоимости за счет применения новых технологий сборки поддонов при помощи пневматических инструментов, изготовление большего числа поддонов меньшим количеством сотрудников (при этом можно сохранять существующие оклады), уменьшение площади производства за счет оптимизации размещения оборудования (снижение стоимости аренды, высвобождение площадей под другие виды деятельности)
С одной стороны, можно решить задачу оптимального производства путем покупки автоматической линии по сборке поддонов. Однако , в данное время, такие линии обладают рядом существенных недостатков:
— дороговизна. Стоимость полной линии начинается от 150 тысяч евро, что не по карману большинству производителей поддонов
— необходимость в качественных калиброванных гвоздях (ведет к импорту этих гвоздей из-за границы, так как российские производители не в состоянии изготавливать калиброванные гвозди для сборочных линий. А это существенно увеличивает стоимость поддона. Использование некачественных гвоздей ведет к частой остановке линии для извлечения застрявшего гвоздя, что негативно сказывается на производительности линии)
— необходимость в качественных деревянных заготовках (так как линии имеют маленький допуск по заготовкам) ведет к удорожанию стоимости поддона
— для работы необходимо привлекать только подготовленных рабочих (чем профессиональней специалист, тем выше его стоимость)
— ремонт и обслуживание только квалифицированными специалистами (чаще специалисты вызываются из-за границы, что ведет к дополнительным тратам и увеличивает время ремонта, срок ожидания запчастей тоже немаленький)
— большое потребление электроэнергии, необходимость в высокопроизводительном компрессоре и дорогой системе очистки воздуха
Предлагаемое нами оборудование не имеет недостатков автоматических сборочных линий и способно полностью удовлетворить требованиям, предъявляемым производителями поддонов:
— невысокая стоимость оборудования и инструментов
— низкие затраты на электроэнергию
— высокая производительность (450 поддонов в смену 8 часов, с учетом обеденного перерыва и того, что Ваши сотрудники не роботы)
— маленький штат сотрудников (всего 4 человека)
— не требуется высокой квалификации персонала
— отсутствие лишних регулировок оборудования
— небольшая площадь производства
— низкие затраты на ремонт и обслуживание
— использование недорогих гвоздей с хорошими крепежными свойствами
— использование заготовок с оговариваемыми допусками
Оборудование для организации паллетного производства
Направление деятельности:
- Изготовление и ремонт поддонов, настилов

Штат сотрудников: 4 человека
1. Система вращающихся кондукторов револьверного типа для сборки поддонов при помощи пневматических гвоздезабивных инструментов
В комплекте 4-е кондуктора + вращающаяся станина
Производительность: 450 штук поддонов за 8-и часовую смену (реальная подтвержденная производительность, теоретически: до 1600 поддонов в смену ).
Персонал: 2 человека
Не требует ни электрического, ни воздушного питания
Простота и надежность конструкции обеспечивает не ограниченный срок годности и отсутствие поломок, даже при работе неквалифицированных операторов
Требует минимального ухода
Обеспечивает выдержанную геометрию поддона
Обеспечивает любой диапазон производимых размеров поддонов (под заказ)
Обеспечивает любой диапазон используемых брусков (шашек) (под заказ)
Отсутствие регулировок кондуктора обеспечивает постоянную выдержанную геометрию поддона и обладает неоспоримым преимуществом перед регулируемыми кондукторами: со временем у них меняются допуски и геометрия (эта конструктивная особенность, от которой не избавиться)
Прижимное устройство брусков и досок для правильной геометрии поддона
Самозагибание гвоздей при креплении дополнительных досок существенно экономит время на эту операцию
Надежное механическое устройство для извлечения готового поддона
Для работы достаточно 2 гвоздезабивных инструмента (поставляются отдельно)
Возможность оснащения пневмоподвесами для удобства работы с инструментами (под заказ)
Гарантия: 5 лет
Срок годности: не ограничен
Допуск по заготовкам +/_ 3 – 5мм (по желанию заказчика)

-Комперссор поршневой в ременным приводом и чугунной головой, стойкой к перегревам. Производительность компрессора подбирается исходя из требований заказчика
-Гвоздезабивные инструменты имеют увеличенный ресурс и предназначены для работы в тяжелых условиях при производстве подднов. Невысокая стоимость инструментов (качество превышает цену). Низкая стоимость ремонта и обслуживания. Практически любую поломку можно устранить в самое короткое время прямо на производстве.
P.S. Почему мы предлагаем остановить свой выбор именно на инструментах Airon или Fasco? Опять же, это выбор профессиональных производителей поддонов!
Инструменты Airon отлично показали себя на российском рынке. Спрос на эти инструменты уже давно держится на высоком уровне. И основная тому причина: высокое качество инструментов, невысокая стоимость и крайне низкие расходы на обслуживание. И ко всему одна из важнейших составляющих: полное сервисное обслуживание и полное обеспечение запасными частями и комплектующими. Кто работает инструментами, тот понимает, о чем идет речь. Если инструмент не может быть отремонтирован в самое короткое время – то производство несет потери. Сотни производителей поддонов стали приверженцами именно этой марки. Хотя предложений на рынке полно: и японские «МAX» (сделанные в Тайланде), и немецкие «BеA» (тот же «МAX», только другого цвета), и канадские «Optima» (в Канаде не делают гвоздевых инструментов), и немецкая «Prebena» родом из Тайваня, и китайские «Мix» (дешевая копия «МAX»).
Инструменты Airon изготавливаются на американском заводе в Тайване и раньше поставлялись только на рынок США. При этом завод занимается изготовлением этих инструментов уже почти 30-и лет!!!! Вдумайтесь в эту цифру……
Что касается инструментов Fasco, то они изготавливаются по лицензии компании МAX в Италии. Хочу подчеркнуть, что завод Fasco находится в Италии и делает инструменты более 40 лет. При сохраненном качестве, цена на инструменты на 30% меньше, а запчасти дешевле почти в два раза. Все объясняется просто: в этом случае Вам не приходится платить за бренд «МAX» или «BеA», Вы платите только за инструмент.
-Шланги, соединения, фильтра, маслораспылители, хомуты производства Италии, Чехии, Германии для обеспечения работы инструментов
Пневматический гвоздезабивной инструмент Airon С33/90-А3 (США)
(38-90мм)
Легкий надежный гвоздезабивной инструмент 3,6 кг для работы с гвоздями до 90мм
Ввертыш носовой части в десятки раз снижает стоимость обслуживания, связанную с износом носовой части. Низкая стоимость обслуживания в совокупности с высоким ресурсом сделали эту модель самой популярной в своем классе.
Пневматический гвоздезабивной инструмент Airon С25/65-А1 (США)
(25-65мм)
Легкий (вес 2,6кг) надежный инструмент для работы с гвоздями до 65мм. Низкая стоимость
обслуживания. Самая популярная модель в своем классе
Пневматический гвоздезабивной инструмент Airon С29/70-А1 (США)
(40-70мм)
Инструмент для гвоздей до 70мм
Отличается чрезвычайной надежностью при работе в сложных условиях. Низкая стоимость обслуживания.
Компрессор СБ4/С 270LB75 (Беларусь)
производительность на выходе : 750 л/мин.,
производительность на всасывание: 880 л/мин.,
ресивер: 270 литров,
Давление: 10 атм.
мощность двигателя: 5,5 кВт, 380В, 50Гц
Вес: 206 кг.
Габаритные размеры: длина 1650мм, ширина 510мм, высота 1150мм)
Ременной привод (уменьшен шум, повышена производительность)
Чугунная головка блока цилиндров не склонна к перегреву,
Надежный к скачкам и перепадам электроэнергии двигатель,
Блок управления производства Германии
Несколько ступенчатых систем защиты для безопасности,
Возможность регулировки выходного давления,
Удобный кран для слива конденсата
Высокий ресурс компрессора, обеспечивающий непрерывную работу 6-и гвоздезабивных инструментов
Пневмолиния
Пневматическая линия для гвоздезабивных инструментов формируется исходя их индивидуальных требования заказчика и условий производства.
Шланги производства Чехии.
Соединения, влаго-маслоотделительные фильтры, маслораспылители, регуляторы давления, штуцера, муфты производства Camozzi (Италия).
3. Торцовочный станок (для получения заготовок доски и бруска)
Производительность за один пропил:
— до 16 досок
— 3 бруска 145х 75мм
— 4 бруска 100 х 75мм
Диск 400- 450мм
Посадка диска 50мм
Боковая подача диска
Конструкция пилы обеспечивает минимальное количество отходов при распиловке доски и бруска при этом гарантирует максимальную точность пила с минимальными допусками
Регулируемый упор для заготовок
Регулируемый прижим
Дополнительная защита для безопасности оператора
Легкая замена пильного диска (без съема кожуха)
Специальный механизм предотвращающий «уход» диска
Регулировка длины хода
Резиновая регулируемая втулка для предотвращения металлических трений между узлами
Выход для системы стружкоудаления
Гарантия 1 год
4. Углообрезной станок со столом
Подача диска сверху вниз
Регулируемый угол пропила
Регулируемая высота пропила
Механическая подача пилы при помощи ножной педали
Защитный кожух для безопасности оператора
Легкая замена пильного диска через специальное отверстие
Регулировка натяжки ремня двигателя
Резиновые прокладки между металлическими частями
Стол толщиной 8мм исключает возможность подпружинивания, прогибания и т.д.
Стол для сколотки нижних досок («лыж») и загибания гвоздей
Машина для производства пеллет, Линия по производству пеллет
Линия по производству пеллет
- Измельчитель древесных отходов
- Измельчитель используется для измельчения таких вещей, как древесные отходы, поддоны, кромки плит, торцы древесины, кора, древесные отходы, бетонные отвалы, отходы шпона, упаковочные коробки, кокосы, пальмы и т. Д. Из измельченных материалов можно производить …
- Трехроторная молотковая дробилка
- Трехроторная молотковая дробилка используется для измельчения отходов фанеры, стружки, коры, крупногабаритных хлопьев после просеивания, соломы сельскохозяйственных культур, фруктовых скорлуп, кромок древесных плит, тростника, стеблей хлопка, пальм, кокосов и т. Д.в тонкое бритье. Стружка переработанная …
- СушилкаСушилка использует тепловую энергию для снижения влажности материалов. При нагревании сушильных машин влага из материалов может испаряться и уходить. Таким образом, мы можем получить твердые материалы с заданным соотношением влажности. Целью сушки является использование …
- Пеллетная мельницаПеллетная мельница используется для переработки частиц древесины или соломы в топливные древесные гранулы. Ключевые компоненты пресса-гранулятора включают модулятор, смеситель, электрическую машину, круглую форму и прижимной ролик…
- Охладитель Пеллеты из гранулятора горячие. Охладители используются для понижения температуры гранул до надлежащей температуры. Обеспечивает удобство упаковки, транспортировки и хранения пеллет …
Описание
Линия по производству пеллет в основном включает в себя линию по производству пеллет из биомассы, линию по производству древесных пеллет и линию по производству топлива из мусора. Машина для производства пеллет из биомассы производит различное топливо из пеллет из биомассы стандарта Европейского Союза путем грубого и тонкого измельчения, доставки, хранения, охлаждения и других способов.Этот вид топлива можно использовать для выработки электроэнергии на электростанциях, сжигания котлов на биомассе и бытовых печей на биомассе. Наша компания специализируется на производстве комплектных машин для производства пеллет. Наша идея создания машин для производства пеллет состоит в том, чтобы объединить передовые мировые технологии и низкую стоимость производства в Китае. Получил сертификат CE.
Преимущества машины для производства пеллет
- Компания Panda Pellet уже более 30 лет работает с ведущими европейскими производителями в области обработки древесины, древесно-стружечных плит, древесно-стружечных плит, МДФ и энергии биомассы.Это дает нам силу качества и технологий для производства машин для производства пеллет.
- Компания обладает передовыми идеями ремесленного дизайна, рациональной планировкой и профессиональным опытом. Это позволяет нам осуществлять крупный проект по производству пеллет из биомассы под ключ в стране и за рубежом.
- В течение многих лет мы сотрудничаем с Институтом исследования пеллет Нанкинского университета лесного хозяйства. Мы разрабатываем различные машины для производства пеллет, такие как конвейерное оборудование, складские помещения, сушилки, пылеуловители, брикетировочные прессы и автоматические роботизированные упаковочные системы в соответствии с различными характеристиками древесины и соломы.У нас есть много патентованных технологий машин для производства пеллет.
- Машины для производства пеллет производятся в Китае, что снижает стоимость производства. У нас есть команда экспертов, и они готовы предложить технологические услуги клиентам по всему миру.
Продукты подкласса
Машины для производства пеллет можно разделить на измельчители, сушилки, грануляторы, брикетировочные машины, охладители, пылеочистное оборудование, транспортное оборудование и упаковочное оборудование.
Характеристики
Машины для производства пеллет обладают такими характеристиками, как превосходное качество, современное мастерство, своевременное обслуживание, большая производительность, низкое потребление энергии и долговечность. Кроме того, ими удобно пользоваться.
Применение линии по производству пеллет
Машины для производства пеллет подходят для топливных заводов, котельных, электростанций, деревообрабатывающих заводов (древесно-стружечные плиты, древесноволокнистые плиты, фанера и древесноволокнистые плиты) и мебельных предприятий (заводы по производству половых досок, фабрики деревянных дверей и деревянных каркасных домов).Их также можно использовать в сельском хозяйстве (обработка урожая или сахарного тростника) и на лесных станциях. Кроме того, продукты используются на упаковочных фабриках, бумажных фабриках и в утилизации твердых бытовых отходов.
Платежи, упаковка и транспортировка
Мы предлагаем оплату T / T и L / C.
Машины для производства пеллет упакованы в водонепроницаемую полиэтиленовую пленку и деревянные ящики для наружного применения. Мы предлагаем морские перевозки, наземные, воздушные или морские перевозки.
Beijing Panda Pellet Machinery Co., Ltd специализируется на производстве комплектных линий по производству древесных гранул. Кроме того, мы также предлагаем вспомогательное оборудование, такое как конвейеры, пылеуловители, просеиватели и упаковочные машины. Наши машины для производства топлива из биомассы хорошо продаются во всем мире, например, в Восточной Европе, Юго-Восточной Азии и Южной Америке.
Линия по производству древесных пеллет и линия по гранулированию биомассы для продажи
Почему выбирают ABC Machinery?
Блок-схема процесса гранулирования
- Нет.1 рыночная доля в Китае, построено более 170 линий по производству пеллет по всему миру. Удобно для вашего расследования на месте.
- 10 патентов на инновационные технологии гарантируют качество каждого оборудования для проектов гранулирования для клиентов, например. интеллектуальная система охлаждения, 3-цилиндровый осушитель и т. д.
- Производительность может достигать 150 000 т / год.
- Интеллектуальное управление PLC. Умно и надежно!
Чертежи полной линии по производству древесных пеллет
Это план проекта для средней линии для производства древесных гранул с двумя комплектами грануляторов.
Ниже приводится пример компоновки завода для крупномасштабной промышленной производственной линии (рассчитанной на 4 комплекта грануляторов). Он включает процессы дробления, сушки, гранулирования, охлаждения и упаковки.
Система дробления с пылеуловителем, это серьезное соображение о том, как защитить здоровье операторов. Система пылеулавливания очень важна, мы использовали мешочный пылеуловитель в секции молотковой мельницы и водяной пленочный пылесборник на всей установке.
Система сушки является ключевой частью всего завода по производству пеллет. Барабанная сушилка имеет противопожарное и влагозащитное исполнение. Топливо может быть различным, но в качестве топлива вы можете выбрать только одно.
Этот план был разработан в соответствии с Humanization Design. Он имеет бассейн оборотной воды для сбора пыли во время работы.
Какие виды материалов можно обрабатывать на нашей линии гранулирования?
Эта полная линия по производству пеллет из биомассы может обрабатывать многие виды сырья, такие как скорлупа арахиса, сахарный биогаз, скорлупа / стебель мельницы, опилки, кофейная шелуха, рисовая солома, стебли подсолнечника, стебли хлопка, табачные отходы, стебли горчицы, отходы джута, бамбук. пыль, отходы чая, солома пшеницы, шелуха пальм, шелуха соевых бобов, кокосовая смола и т. д.
Подробная информация об оборудовании линии пеллет
Окорочный станок
— Низкие начальные вложения.
— Высокая производственная мощность.
— Лучший выбор для малых и средних предприятий.
— Самая передовая технология окорки бревен малого и среднего размера.Измельчитель древесины
Измельчитель древесины представляет собой современное оборудование для производства древесной щепы и, в частности, используется на бумажных заводах, заводах по производству гранул, древесно-стружечных и древесноволокнистых плитах.Он режет бревна и небольшие куски дерева на высококачественную стружку одинаковой длины и одинаковой толщины. Он также подходит для колки веток, веток и досок.Просеивающая машина
Грохот цилиндрического типа. Он специально разработан для просеивания крупногабаритных материалов, чтобы они не попали в гранулятор. Таким образом, гранулятор может быть надежно защищен от забивания.Молотковая дробилка / дробилка
— Это специальный измельчитель для щепы, стружки, грубых опилок и т. Д.Помещение для измельчения предназначено для измельчения древесины.— Хорошо сбалансированный ротор делает работу очень стабильной.
— Специальное соединение муфты снижает вибрацию и упрощает установку.
Однослойная сушилка с вращающимся цилиндром
— Ротационная сушилка — лучший выбор для приложений с высокой производительностью, связанных с влажными, рыхлыми, сыпучими материалами и побочными продуктами.— Вращающийся барабан и стратегически расположенные лопасти объединяются для равномерного подъема и опускания продукта через воздушный поток.
— Термостатически регулируемая температура нагнетаемого воздуха обеспечивает точную конечную влажность и чувствительность к изменяющимся условиям продукта.
— Доступны однопроходные или трехходовые конфигурации, соответствующие характеристикам продукта.
— Варианты отопления включают пар, газ, масло и мазут.
Пеллетная мельница (изготовление пеллет)
— Применение аэродинамических технологий и нынешнего круглого принципа снижает температуру в камере гранулирования примерно до 90 ℃. В результате машина может работать непрерывно.— Податчик времени может контролировать скорость подачи, чтобы уменьшить коэффициент блокировки.
— Корпус более прочный, потому что мы используем чугун со сферическим графитом.
— Емкость увеличена после добавления еще одного силового питателя из нержавеющей стали для увеличения площади распределения корма.
Система охлаждения гранулятора
— Применение аэродинамических технологий и нынешнего круглого принципа снижает температуру в камере гранулирования примерно до 90 ℃. В результате машина может работать непрерывно.— Контролирует температуру и выпускает дополнительный пар за счет циркуляции воздуха. В результате он хорошо работает в областях без прессования, что продлевает срок службы кольцевой матрицы и скоб.
— Машина может работать непрерывно.
Охладитель пеллет
— Автоматический контроль периода охлаждения. Это делает свежие гранулы твердыми и сухими. Холодный воздух течет снизу вверх, а гранулы падают сверху вниз, они полностью встречаются и полностью охлаждаются.— Производственные стальные пластины имеют толщину 3 мм.
-Система охлаждения состоит из сосуда, ветрового конуса, нагнетательной системы, загрузочного отверстия, выпускного патрубка, индикатора контроля уровня.
— Это оборудование должно использоваться с питателем воздушного шлюза, охлаждающей ветровой сеткой.
Машина для упаковки пеллет
— Включая автоматические весы, конвейер, термосваривающие устройства для древесных гранул.— Эта машина представляет собой комбинацию автоматического взвешивания и наполнения вместе с транспортной швейной машиной, так что она может автоматически взвешивать, наполнять и шить.
— Компьютерная высокоскоростная штамповка и обработка, а также программируемый процесс управления делают его универсальным для различных упаковок.
— Специальное асейсмическое оборудование гарантирует точный расчет, высокую скорость и стабильную работу в неблагоприятных условиях. Его можно отрегулировать снаружи, что очень удобно в обслуживании.
— Он широко используется для упаковки древесных гранул, гранул кормов для животных и порошковых материалов.
Проекты завода по производству топливных пеллет
Вот несколько фотографий одного из наших проектов для справки.Он разработан и построен для одного из наших клиентов в Чили. Производительность от 4,5 до 6 тонн в час. Не стесняйтесь обращаться к нам за подробным бизнес-планом и стоимостью проекта! Мы всегда здесь, чтобы служить вам!
Проект завода по производству древесных пеллет 4,5 ~ 6 т / ч в Чили
Подробная информация о дробильном участке
Подробная информация о разделе гранулирования
Наши пеллетные заводы построены в следующих странах:
Европа | Германия, Франция, Литва, Ирландия, Италия, Португалия, Чехия, Венгрия, Румыния, Словацкая Республика, Сербия, Черногория, Болгария, Россия, Украина, Польша, Беларусь, Хорватия, Латвия, Швеция |
---|---|
Азия | Китай, Малайзия, Индонезия, Таиланд, Вьетнам, Индия, Шри-Ланка |
Северная Америка | США, Канада |
Южная Америка | Уругвай |
Океания | Австралия |
- Пришлите мне расценки на завод под ключ по производству пеллет из опилок с кольцевой матрицей.У меня есть лесопильный завод в Нигерии, я хотел использовать опилки для изготовления пеллет и древесного угля для барбекю. Диаметр: 4-8 мм. Благодарю.
- Обращаем ваше внимание на то, что ABC Machinery — инжиниринговая компания, специализирующаяся на проектировании, производстве, проектировании, установке и вводе в эксплуатацию проектов «под ключ» в этой области.
В приложении, пожалуйста, найдите каталог для справки. Мы надеемся, что сможем сотрудничать с вашей уважаемой компанией, и надеемся, что это хорошее начало для такого многообещающего взаимовыгодного курса.
Что касается вашего запроса, чтобы предоставить вам правильный дизайн, предоставьте нам информацию ниже:
1. какая емкость вам нужна для гранул и древесного угля для барбекю?
2. какая влажность у вас опилок?
3.Есть ли другой материал, кроме опилок?
4. когда вы планируете начать продвижение?
Жду ответа от вас. - Спасибо за ваш ответ. У меня есть лесопилка в Африке. Я произвел много опилок, я хотел бы превратить их в пеллеты и древесный уголь. Диаметр пеллет будет 4-8 мм, размер угля — 40 мм x 40 мм x 28 мм. влажность опилок 40-50%. Другого сырья нет. Завод будет запущен с апреля 2012 года. Мне нужно производственное оборудование завода.
- Пожалуйста, найдите в электронном письме прикрепленную для вас схему потока, вот описание:
Производство состоит из двух частей: линии гранул и линии брикетов.Основная линия — это линия гранул, две линии будут разделять секцию предварительной обработки, такую как сито предварительной очистки и барабанная сушилка, гранулятор и брикетировочная машина будут получать готовые опилки из барабанной сушилки; затем охладитель и сито будут после гранулятора, когда брикет отправится в печи (мы предоставим вам чертеж печи, чтобы вы могли самостоятельно установить ее на месте) для сжигания на древесном угле.
Блок-схема похожа на то, что мы обсуждали по телефону, пожалуйста, сначала посмотрите, нужно ли что-то изменить. - Здравствуйте, я очень заинтересован в линии по производству поддонов из биомассы. Пожалуйста, пришлите мне предложение на полную производственную линию 6т. Сколько это стоит ? — из Португалии
- Перед отправкой предложения вы можете сообщить некоторую информацию о своем сырье? такие как размер и влажность. Тогда мы сможем убедиться, нужны ли дробилка и сушилка в нашем предложении.
Другой вопрос касается машины для упаковки гранул, есть два вида: одна — это машина для упаковки в небольшие мешки, например, 15-25 кг на мешок, другая — машина для упаковки в большие мешки, например, 800-1000 кг на мешок.Какой из них ты предпочитаешь? - Могут ли эти пеллетные установки и машины перерабатывать топливные пеллеты класса EN plus?
- На то, чтобы гранулятор производил высококачественные топливные гранулы, играет роль множество факторов. К таким факторам относятся зольность менее 0,5 процента и содержание мелкой пыли менее 1 процента для древесных топливных гранул. Нашего завода по производству гранул и оборудования достаточно для производства гранул класса EN plus. Однако обратите внимание, что для достижения желаемых результатов вы должны использовать правильное сырье.Например, если вы используете кору деревьев в качестве сырья, вы должны убедиться, что содержание древесины равно нулю, чтобы содержание золы составляло 0,5 процента.
- Можете ли вы сделать гранулы из травы, соломы или других материалов биомассы?
- Да. Наши машины для производства древесных гранул могут обрабатывать множество видов биомассы, включая коноплю, просо, мискантус и другие, для производства топливных гранул. Однако учтите, что такие материалы производят больше золы по сравнению с древесными гранулами.
Линия по производству древесных пеллет и пеллет
Производство древесных пеллет
Производство древесных гранул — действительно очень квалифицированный процесс, не просто гранулирующий завод, но, вероятно, какое-то другое оборудование для гранулирования, вероятно, будет применено на линии производства гранул . При производстве древесных гранул очень важно знать, как изменять влажность, размер частиц, а также как и когда добавлять связующие.Поскольку сырье различно, производство древесных гранул также требует правильного оборудования и понимания того, как выполнять и настраивать пресс-гранулятор для производства качественных гранул. Производство древесных гранул означает прессование сыпучих древесных материалов в компактные древесные гранулы с одинаковыми размерами, формой и плотностью.
Линия по производству пеллет
Линия по производству пеллет, также называемая заводом по производству пеллет или просто завод по производству древесных гранул.Однако для получения пеллет хорошего качества требуется более глубокое понимание того, как их производить.
Первым шагом на линии по производству пеллет является уменьшение размера сырья для того, чтобы гладко и легко проходить отверстия матрицы.
Во-вторых, вы должны удалить влагу из сырья для последующего процесса гранулирования, сушка также является одним из ключевых критериев при производстве гранул, так как слишком высокая влажность затрудняет сохранение формы гранул и в то же время, как горение Топливо снизит эффективность сгорания пеллет или увеличит зольность.Обычно рекомендуется поэкспериментировать с содержанием влаги в сырье, чтобы получить гранулы высокого качества с минимальным потреблением энергии.
Затем следует самый важный процесс в линии по производству древесных гранул — гранулирование. Поместите подготовленное сырье в гранулятор для обработки древесных гранул, но не забывайте избегать твердых примесей, таких как железо, камни и т. Д., Поскольку эти примеси могут повредить ваши грануляторы.
В-четвертых, охладите гранулы. Обычно древесные гранулы горячие и содержат много влаги после гранулирования из грануляторов.В этом случае дайте им остыть самостоятельно или воспользуйтесь кулером.
И последнее, но не менее важное: правильно упакуйте гранулы для дальнейшего использования. Обычно вы используете профессиональную упаковочную машину.
Линия по производству пеллет из биомассы — Zhengzhou Dingli New Energy Technology Co., Ltd
1. Патентная технология (номер патента: ZL200920089749.2), отдельное оборудование, виды разнообразны, применение для различных материалов, модульные конструкции, оптимизация конфигураций, обеспечение широкого применения производственных линий.
2. Эта производственная линия может в соответствии с требованиями заказчика реализовать интеллектуальное управление, ключевую операцию типа «дурак», параметры работы могут быть автоматическими, производственная линия всегда находится в лучшем состоянии, обеспечивает производственную мощность и качество продукции. .
3. Более 300 пользователей в мире, наша фабрика имеет богатый практический опыт.
4.Площадь покрытия уменьшается на 50% по сравнению с традиционной производственной линией сушки и грануляции, инвестиции в строительство сокращаются примерно на 50%.
5. Внутренняя структура сушилки с различными режимами комбинации эффективных устройств подачи, эффективное регулирование процесса сушки и распределения тепла, высокая степень использования тепла, температура сброса отходящих газов ниже 50 ℃, все конструкции обеспечивают низкую производительность производственной линии. потребление энергии.
6.В технологическом маршруте используется однократная сушка, вторичное дробление, непрерывная подача и регулировка подачи, смешанный процесс комбинирования, расход топлива для формирования частиц 98%, объемная плотность и плотность частиц высокие.Эта производственная линия сушки и гранулирования может реализовать масштаб, непрерывный и стабильный производство, отвечающее требованиям индустриализации топливных гранул из биомассы.
7.Специальная технология контроля золы, она может удовлетворить требования заказчика по содержанию золы ниже 1%.
8. Модульная сборка пыли и очистка конфигурации с рециркуляцией тепла, безопасность и защита окружающей среды.
9. Этот тип смесительной барабанной сушилки поддерживает многие новые энергосберегающие печи с горячим воздухом, высокую эффективность и энергосбережение, управление нагревом, простое управление, снижение энергопотребления примерно на 30%, снижение энергопотребления на 20%, более низкие эксплуатационные расходы .