Производство гиперпрессованного кирпича: состав, оборудование, технология
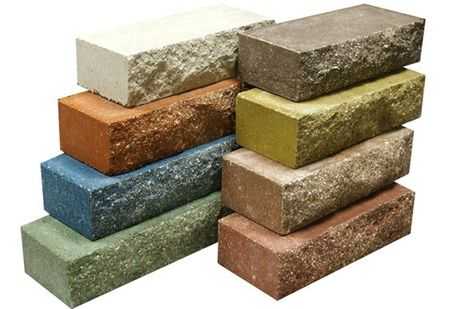
Как делают гиперпрессованный кмрпич?
На российском рынке строительных материалов гиперпрессованный кирпич занял свою нишу не так давно. Но даже за этот короткий период он успел завоевать доверие строителей, профессионалов и новичков.
Сразу поясним, что оборудование для производства гиперпрессованного кирпича не похоже на то, что используется для получения тех же керамических блоков. А соответственно, и технические характеристики, и внешний вид готовых изделий будут отличаться.
Отличная морозостойкость, прочность и привлекательный внешний вид делают гиперпрессованный кирпич отличным материалом при возведении жилых и промышленных конструкций.
В чем же преимущества этой технологии? Как выглядит схема получения гиперпресованных кирпичей?
Преимущества технологии гиперпрессованяи
Технология производства гиперпрессованного кирпича – инновационный метод изготовления материала без обжига и сложной подготовки сырьевой смеси. А ведь именно на стадии обжига при несоблюдении определенных правил в изделиях могут образовываться пустоты, которые негативно сказываются на качестве и долговечности продукции. Сверхплотный гиперпрессованный кирпич этих недостатков лишен.
Еще одно важное преимущество технологии гиперпрессования – энергоемкость производства, что позволяет при минимуме затрат получать высококачественный продукт. Цена сырьевых компонентов и оборудования значительно ниже, чем расходные материалы и станки, используемые при изготовлении других видов кирпичных блоков.
К тому же, технология гиперпрессования кирпича безотходна. Мало того, что в качестве сырья здесь используются отходы других производств, так и сама линия подразумевает переработку брака, полученного в процессе изготовления кирпича
Учитывая, что купить все необходимое оборудование можно относительно недорого, в последние годы в России запускается довольно много мини-заводов, специализирующихся на выпуске гиперпресованного кирпича.
Подготовка сырьевой смеси
Технология получения гиперпресованного кирпича на производстве начинается с дозирования и смешивания компонентов. В качестве сырья здесь используются:
- Отсевы щебня (85-92 %) в качестве заполнителя.
- Портландцемент (8-15 %) в качестве вяжущего компонента.
- Вода (5-12 %).
- Пигменты (2-7 %).
В состав гиперпрессованного кирпича многие производители в качестве заполнителей добавляют доменные шлаки, каменный бой, а также отходы асбоцементных предприятий и электростанций. По действующим стандартам это вполне допустимо, но важно, чтобы количество этих компонентов не превышало определенных показателей. В противном случае, снижаются качественные характеристики готовых изделий.
Для получения пластичной массы все компоненты должны быть строго дозированы согласно рецептуре. Для это используются весы с допустимой погрешностью измерений ±0,5 %.
Отсев щебня, для исключения наличия крупных фракций, прямо в процессе дозирования проходит через вибросито.
Далее дозированная смесь для гиперпрессованного кирпича на конвейерах поступает в бункер, где происходит дробление, тщательное перемешивание всех компонентов и их активация. Сюда подается необходимое по рецептуре количество воды. Для получения гомогенной массы емкость должна непрерывно вращаться. Если на этом технологическом этапе раствор не будет соответствовать определенным стандартам, готовые изделия не обретут нужных свойств.
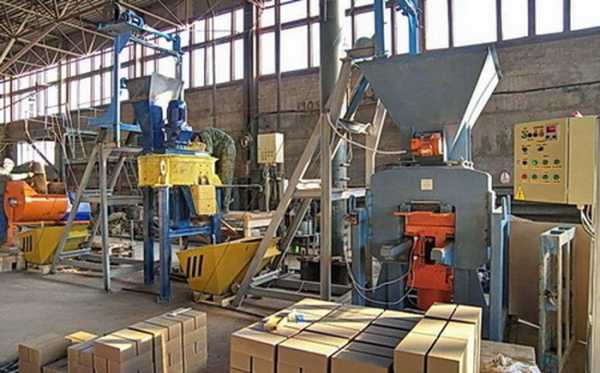
Работающая линия по производству гиперпрессованного кирпича
Формование гиперпрессованного кирпича
Формование изделий – основной и самый важный этап всей технологической цепочки. Именно сейчас изделия приобретают свою геометрическую форму и свойственные им характеристики. Прессовые станки для гиперпрессованного кирпича работают по принципу так называемой холодной сварки, когда мельчайшие фракции веществ сцепляются между собой посредством воздействия на смесь высокого давления.
На стадии формования кирпича технологами контролируются следующие параметры:
- Давление, оказываемое на массу.
- Габаритные размеры кирпича-сырца.
Если какие-то из фактических параметров не совпадают с заданными, работа автомата останавливаться, а те отходы, что образовались, вновь отправляют на переработку. Таким образом получается замкнутый производственный цикл.
Интересные статьи:
Какой выбрать станок для изготовления кирпича Лего?
Как осуществляется обжиг кирпича в туннельной печи?
Пропаривание гиперпрессованного кирпича
Изготовление гиперпрессованного кирпича далее заключается в пропаривании полученного после прессования сырца. В процессе пропаривания готовые изделия набирают до 70 % своей марочной прочности. На этой стадии используются специальные пропарочные камеры, куда на поддонах отправляются сформованные кирпичи. Здесь они в течение 8-10 ч выдерживаются при температуре 40-70 ˚С. В зимний же период время пропаривания следует увеличить.
Пропаривание может и не осуществляться, если технология предусматривает выдержку кирпича-сырца (прямо на поддонах) в течении 1 недели при положительной температуре окружающей среды. Так производители гиперпрессованного кирпича значительно экономят на техническом оснащении.
Складирование готовых изделий
По завершении стадии пропаривания изделия обязательно должны «отстояться» на поддонах при положительной температуре примерно 3 дня. Затем кирпичи либо отправляются на склад для дальнейшего хранения, либо поставляются прямиком на строительную площадку. Несмотря на то, что блоки достигают своей полной прочности только спустя 30 дней после изготовления, уже сейчас они могут применятся по назначению.
Популярные публикации:
Изготовление кирпича из глины своими руками.
Средняя цена оборудования для производства Лего кирпича.
Оборудование для получения гиперпрессованного кирпича
Оборудование для производства гиперпрессованного кирпича различных марок отличается своей мощностью, степенью автоматизации и комплектацией. Все дополнительные опции, конечно, сказываются на конечной цене аппаратов. К примеру, многие современные прессовые станки предназначены для получения не только кирпича, но и других видов продукции – тротуарной плитки и облицовочного декоративного камня.
Производительность современных линий варьируется в пределах 350-4500 тыс. кирпичей/ч.
Высокомощные, полностью автоматизированные технологические линии включают в себя 2 и более гиперпрессов. Но вот оснащать стольким количеством оборудования мини-завод не имеет никакого смысла – затраты будут экономически не оправданы. Вот почему многие производители на начальных этапах закупают линии с минимальной комплектацией.
Среднемощная линия по производству гиперпрессованного кирпича включает в себя следующий набор оборудования:
- Приемные бункеры для сырья.
- Дробилка.
- Дозаторы для воды, отсева и цемента.
- Вибросито.
- Смеситель.
- Гиперпресс.
- Пропарочная камера.
- Конвейеры.
Современные станки для получения гиперпрессованного кирпича поставляются из Китая и Европы. Спросом пользуются также станки отечественных марок – они стоят дешевле, да и их техническое обслуживание осуществлять намного проще. Для снижения расходов на открытие предприятия многие производители покупают б/у линии. Если аппараты исправны, то это никоим образом не сказывается на качестве готовой продукции.
tvoikirpichi.ru
Гиперпрессованный кирпич, оборудование для производства
Гиперпрессованный кирпич, и какое требуется оборудование для его производства, в сегодняшней статье.
На сегодняшний день, когда ощущается дефицит рабочих мест, а там, где они есть – слишком низкая зарплата, многие мужчины задумываются о собственном деле.
Идей для малого бизнеса, с небольшим стартовым капиталом и небольшими производственными площадями – не так уж и мало.
Недавно мы уже писали о том, как изготовить кирпич из опилок и цемента своими руками. А сегодня поговорим о том, как изготовить гиперпрессованный кирпич и какое требуется оборудование для производства.
Гиперпрессованный кирпич оборудование для производства
Из названия уже понятно, что данный вид кирпича изготавливается при высоком давлении, в результате воздействия пресса на кирпичную, полусухую смесь.
Что же служит основой для кирпичной смеси и в каких пропорциях берутся компоненты, вы узнаете из данной статьи.
Прежде чем начать своё дело, следует составить бизнес план, рассчитать все затраты и планируемую прибыль. Найти каналы сбыта готовой продукции.
На количество доходов и расходов влияет то, какое оборудование вы приобретёте. Какая производительность у оборудования, из какой смеси изготавливается кирпич и так далее.
Оборудование
Существуют различные модификации оборудования по производству более десяти различных видов гиперпрессованного кирпича и других строительных материалов.
Сейчас мы коротко расскажем о том, что представляет из себя оборудование по производству гиперпрессованного кирпича.
Производственная линия состоит из 7 главных узлов, о которых мы коротко расскажем.
Производственный процесс начинается с загрузки инертного материала в бункер, объемом около трёх кубических метров.
Бункера могут различаться по внешнему виду и объёму. Однако, это различие не критично и не влияет на производственный процесс.
В бункер загружается исходное сырьё, предназначенное для изготовления кирпичей. Оттуда, по ленте транспортёра оно поставляется в сеялку.
Сеялка предназначена для механического отделения мелких сыпучих материалов от посторонних примесей.
Например, от камней, щебня, других крупных фракций, которые отводятся в противоположную сторону, для исключения возможности смешивания.
Сеялка освобождает исходное сырьё от фракций, размером более трёх миллиметров. Средняя производительность сеялки – до десяти тонн сыпучих материалов в час.
Крупные фракции по боковому транспортёру поступают в молотковую дробилку, для измельчения. После чего повторно отправляются в сеялку.
Просеивающая система отделяет мелкое сырьё, от более крупных частиц. Мелкие фракции транспортируются прямо в смеситель.
Смеситель, он же дозирующий комплекс, предназначен для приготовления смеси из которой формируются кирпичи. Все компоненты смеси подаются в строго запрограммированном объёме и весе.
Смеситель состоит из двух частей:
- весоизмерительного терминала;
- бетоносмесителя.
Дозирующий комплекс предназначен для весового дозирования инертных вяжущих материалов. Таких как: цемент, исходное сырьё, и поточное дозирование воды, с последующим смешиванием.
Подачи сырья в пресс и далее, в аппарат для полусухого прессования строительных материалов, осуществляется в автоматическом режиме.
Вся система управления комплексом полностью автоматизирована. Разгрузка бункера, сеялки, дозатора и смесителя осуществляется через автоматический затвор.
Пневматическая загрузка дозирующих материалов осуществляется как в автоматическом, так и ручном режимах.
Приготовленная дозирующим комплексом смесь поступает по транспорт
kirpichman.ru
оборудование, производство и состав смеси
Основным оборудованием при изготовлении гиперпрессованного кирпича является пресс для гиперпрессования кирпича.
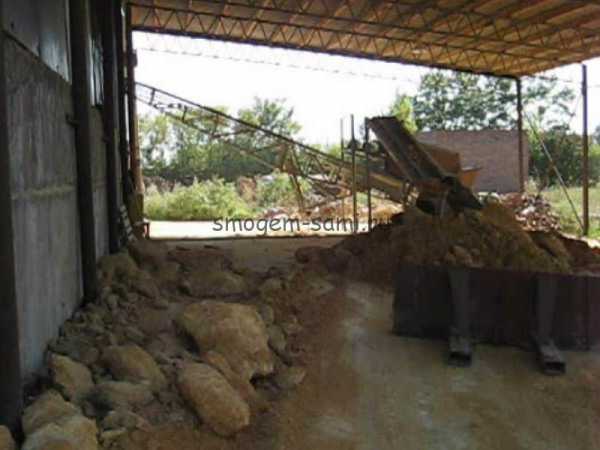
Процесс создания
Сравнительно недавно в строительстве активно стал использоваться гиперпрессованный кирпич, который за время своего существования стал очень популярным строительным материалом среди профессионалов и новичков в строительстве.
Важно отметить тот факт, что процесс создания кирпича методом гиперпрессования и используемое при этом оборудование кардинальным образом отличается от того, которое используется при создании керамических блоков.
Гиперпрессованный кирпич имеет высокую прочность и морозостойкость.
В конечном итоге, это сказывается на отличительных признаках внешнего вида кирпича и его технических характеристиках.
Состав гиперпрессованного кирпича наделяет его самыми лучшими свойствами и качествами:
- устойчивость к морозу;
- высокая прочность;
- привлекательность наружного вида.
Все это повышает спрос на использование гиперпрессованного кирпича в создании промышленных и жилых конструкций.
Преимущества гиперпрессованных кирпичей
Производство гиперпрессованного кирпича представляет собой новейший метод, позволяющий создавать материал без дополнительного обжига и предварительного подготовительного этапа, предназначенного для смеси сырья. А ведь именно эти этапы так важны при создании простого кирпича. Гиперпрессованный кирпич лишен минуса, который заключается в образовании пустот, которые плохо сказываются на долговечности материала.
Производство гиперпрессованного кирпича отличается экономией энергии. Процесс изготовления позволяет получить продукт очень высокого качества при малых затратах. При изготовлении других сырьевых компонентов требуется намного больше оборудования, да и количество требуемого сырья тоже очень высоко. Все это помогает выявить еще один плюс создания материала из гиперпресса.
Схема производства гиперпрессованного кирпича.Производство гиперпрессованного кирпича отличается еще и безотходностью при создании материала.
В производстве применяются отходы разных производств, и само производство предполагает последующую переработку появившегося брака, который может возникнуть при создании кирпича.
В настоящее время все необходимое оборудование для производства кирпича можно приобрети за достаточно небольшие деньги, это объясняет большое количество появившихся маленьких заводов, которые специализируются непосредственно на изготовлении гиперпрессованного кирпича.
Создание сырьевой смеси
Перед тем как приступить к процессу создания материала, необходимо предварительно подготовить специальную смесь, предназначенную для создания гиперпресса. Эта смесь предполагает смешивание компонентов в определенной дозировке. В качестве сырья могут быть использованы следующие компоненты:
- пигмент;
- вода;
- портландцемент, необходимый для создания вяжущего эффекта;
- отсевы щебня (каменный бой, доменные шлаки), применяемые в качестве заполнителя.
Чтобы полученная путем смешивания масса отличалась пластичностью, при производстве очень важно строго соблюдать дозировку. Допустимым отклонением от нормы является погрешность, равная меньше половины процента.
Все необходимые компоненты тщательно смешиваются между собой и проходят процедуру дополнительного дробления. Когда вся смесь готова, в нее добавляется вода в нужном количестве. Именно этот процесс является важным при создании гиперпрессованного строительного материала. Специальное оборудование предполагает создание постоянного вращения, позволяющего приготовить раствор, отвечающий всем требованиям и стандартам.
Процесс придания формы является наиболее важным моментом всей производственной цепочки. Именно на этой стадии изделие получает форму и наделяется нужными характеристиками и свойствами.
Станки, применяемые при изготовлении гиперпрессованного материала, работают по принципу холодной сварки. Современные предприятия оснащены автоматическими прессами, что в свою очередь позволяет очень сильно облегчить процесс контроля.
Размеры гиперпрессованного кирпича.В процессе производства важно контролировать давление, которое оказывается на массу, а также размеры получаемого изделия.
Если что-то идет не так, то работа приостанавливается, созданный продукт идет в переработку, и весь цикл начинается заново.
После прессования изделие подвергается пропариванию. Именно на этом этапе готовое изделие достигает 72% своей прочности. Для пропаривания изделия используются специализированные камеры, в которые направляются готовые заготовки на 10 часов.
После того, как материалы были подвержены процессу пропаривания, они должны настояться в помещении с положительной температурой примерно 3 суток. После этого готовые изделия можно отправить на склад, чтобы осуществить его последующее хранение, или сразу же отправить на площадку со строительством.
Оборудование
Оборудование, необходимое для производства гиперпрессованного материала, отличается:
- мощностью;
- комплектацией;
- автоматизированной степенью.
Каждая дополнительная опция, которая выполняется аппаратом, в конечном итоге отражается на розничной стоимости изделия. Очень многое современное оборудование предназначено для создания не только кирпича, но на нем можно делать и декоративную плитку, камень и так далее.
//www.youtube.com/watch?v=sbd_SmtrsT8
Высокомощная технологическая линия содержит в своем составе 2 и более гиперпрессов. Но затраты при этом на оснащение возрастают в разы, что заставляет подумать о приобретении линии с минимальными комплектациями, которых хватает для выполнения начального этапа создания гиперпрессованного строительного материала.
kubkirpich.ru
Оборудование для производства гиперпрессованного кирпича, тротуарной плитки и других строительных материалов
|
Технология производства
Кирпичи, тротуарная плитка изделия, изготовляются из известняка, ракушечника с добавлением цемента, пигмента (без обжига) различные отсевы и отходы. Марка кирпича: 150-300. Кирпич пустотелый (различной формы пустот) и полнотелый.
Способ пропарки: пар.
Технологические линии автоматические (без ручного труда), очень гибкие, могут изменяться по длине, ширине и высоте, поэтому могут размещаться в любых готовых зданиях так и в строящихся зданиях.
В указанные квадратные метры производственных площадей входит размещение: гиперпресса, технологической линии, пропарочной камеры и бункерного отделения сыпучих материалов и другого оборудования необходимого для изготовления блоков и кирпичей, а также бытовые помещения для персонала.
Параметры (геометрия) блоков и кирпичей и качество идеальное. Срок строительства «под ключ» от 3 до 5 месяцев (в зависимости от годовой производительности завода).
Номенклатура продукции и требования к сырью:
Кроме стандартных, возможно изготовление любых пресс-форм по желанию Заказчика. Сырьевые материалы используемые для гиперпрессования кирпичей должны соответствовать требованиям ГОСТ 8267, ГОСТ 23254, ГОСТ 8268, ГОСТ 8736, ГОСТ 5576, ГОСТ 25818, ГОСТ 25592, ГОСТ 9757.
Фракция известняка, ракушечника с модулем крупности 0,3-0,4 мм;
Количество цемента – 10 – 15 % от массы смеси. Вода – 5 – 7 %. В качестве красителей может использоваться цветной цемент, а также неорганические пигменты (см. ГОСТ 6133).
Краткое описание технологической цепочки (Гиперпрессование):
1. Подача известняка
Инертные материалы (известняк, ракушечник и др.): а) загружаются Ковшевым погрузчиком в Приёмный бункер-питатель(на улице), б) выгружаются Самосвалом или ковшевым погрузчиком в Приёмный бункер-питатель в приямке (на улице).
С этого Приёмного бункера-питателя известняк по нижнему транспортеру расположенному под бункером-питателем передается на наклонный транспортер (на улице).
По наклонному транспортёру известняк подаётся в молотковую дробилку, установленной на эстакаде.
В Молотковой дробилке известняк дробится до фракции 1 мм. – 3 мм.
С Молотковой дробилки измельчённый известняк подаётся на верхний раздаточный транспортёр, который установлен на верху Бункеров–накопителей.
С верхнего раздаточного транспортёра измельчённый известняк при при помощи передвигающего Плужкового сбрасывателя сбрасывается на обе стороны транспортёра и заполняет бункеров-накопителей .
2. Подача цемента
Цементовоз привозит цемент и по пневмоподаче подаёт его наверх Силоса цемента, где запоняет его цементом.
С силоса цемента по пневмоподаче цемент подаётся в весовой бункер-дозатор цемента, который установлен над Бетоносмесителем.
Бункер-дозатор цемента дозирует норму цемента и подаёт её в Шнек цемента.
По шнеку цемента цемент подаётся в Барабан-смеситель.
3. Подача пигмента
Рабочий заполняет пигментом бункер-дозатор пигмента.
Бункер-дозатор пигмента дозирует норму пигмента и подаёт её в Шнек пигмента.
По шнеку пигмент подаётся в Барабан-смеситель.
4. Приготовление цветного цемента
В барабан-смесителе цемент и пигмент тщательно перемешиваются и образуют однородную сухую смесь-цветной цемент.
5. Приготовление рабочей смеси
С бункеров-накопителей, по нижним транспортёрам измельчённый известняк подаётся в Бетоносмеситель(весовой), при этом весовой механизм одновременно дозирует нужную норму.
С барабан-смесителя цветной цемент подаётся в Бетоносмеситель.
Измельчённый известняк и цветной цемент тщательно перемешиваются до однородной сухой смеси.
С ёмкости-дозатора воды подаётся норма воды в бетоносмеситель. Норма подачи воды контролируется датчиком влажности.
В бетоносмесителе все компоненты тщательно перемешиваются до однородной рабочей смеси.
6. Подача рабочей смеси
Из бетоносмесителя, по среднему наклонному транспортёру, рабочая смесь подаётся в бункер Гиперпресса «ВОГЕАН-2» или «ВОГЕАН-4»
7. Гиперпрессование кирпича-сырца
С бункера гиперпресса рабочая смесь питателем подаётся в форму гиперпресса и заполняет её. Происходит двух-стороннее гиперпрессование 2 шт. или 4 шт. за один цикл с давлением = 400 кг/кв.см. Питатель доставляет(новый цикл) рабочую смесь в форму и одновременно перемещает изготовленных 2 шт. или 4 шт. кирпича-сырца на приёмный стол, где формируется з пакет из 16 шт. кирпича-сырца.
8. Доставки кирпича-сырца в пропарочную камеру
С приёмного стола гипепрпресса Укдадчик 1 за один цикл переносит 16 шт. кирпича-сырца на металлический поддон. За два своих цикла Укладчик 1 переносит на металлический поддон 32 шт. кирпича-сырца.
Каретка 4 Подъёмника передвигает металлический поддон, на котором 32 шт. кирпича-сырца, вдоль пропарочной камеры на рамку Подъёмнике и передвигает металлический поддон с кирпичом-сырцом до нужной секции пропарочной камеры.
Подъёмный механизм Подъёмника поднимает рамку на которой металлический поддон с 32 шт. кирпича-сырца до нужного яруса, на нужном отсеке. Всё делается автоматически. Рамка Подъёмника останавливается на нужном ярусе и Толкатель штоком своего гидроцилиндра автоматически заталкивает металлический поддон с 32 шт. кирпича-сырца на ярус.
Пустая рамка Поъёмника, при помощи подъёмного механизма опускается вниз, за очередным металлическим поддоном с 32 шт. кирпича-сырца. Цикл работы Поъёмника: 32 шт./192 сек.(один метал. поддон с кирпичом-сырцом). И так цикл за циклом.
Когда отсек полностью заполнен кирпичом-сырцом, то с обоих сторон отсека закрываются 2 шт. лёгкие ворота(Р= 4 кг). В этот отсек подаётся пар от электро-парогенератора и происходит пропарка кирпича-сырца в течении 7 часов.
Открываются с обеих сторон ворота следующего отсека и новый цикл заполнения отсека кирпичом-сырцом продолжается.
9. Доставка готового(пропаренного) кирпича из пропарочной камеры
С яруса пропарочного отсека металлический поддон с 32 шт. готовым(пропаренным) кирпичом скатывается на рамку Съёмника и при помощи подъёмного механизма опускается вниз. Там при помощи каретки 5 передвигается вдоль пропарочной камеры, где передвигается на промежеточный возвратный ярус.
Пустая рамка Съёмника при помощи подъёмного механизма поднимается вверх, до нужного яруса на нужном отсеке, за следующим металлическим поддоном с 32 шт. готового(пропаренного) кирпича. И так цикл за циклом.
На Промежуточном возвратном ярусе, металлический поддон с 32 шт. готового(пропаренного) кирпича, при помощи каретки 6, передвигается к Укладчику 2, который заберёт 32 шт. готового(гладкого) кирпича. Пустой металлический поддон, при помощи каретка 6, передвинется на Возвратный ярус.
Получив пустой металлический поддон, Возвратный ярус при помощи каретки 1, передвигает его к Гиперпрессу.
Укладчик 2. при помощи: Сжимателя, который сжимает и разжимает кирпичи, каретки 8. которая поднимает кирпичи ввех или вниз и каретки 7, которая переносит 32 шт. готового(пропаренного) кирпича с металлического поддона который был на промежуточном возвратном ярусе на деревянный поддон, который установлен на поворотном кругу Укладчика 2. Поворот делается на 90 градусов. В стопу укладывается 16 рядов вверх. Через два ряда поворот на 90 градусов. Получается стопа по 512 шт. готового(гладкого) кирпича.
Каретка 9, линии отправки на холодный склад, передвигает деревянный поддон с стопой по 512 шт. готового(гладкого) кирпича на поворотный круг Упаковщика.
Поворотный круг Упаковщика вращается и оборачивает стопу по 512 шт. в полиэтиленовую плёнку.
Каретка 9, линии отправки на холодный склад, передвигает деревянный поддон, с стопой по 512 шт. кирпича(гладкого), упакованного в полиэтиленовую плёнку, на улицу. Где автокар перевозит его на холодный склад.
10. Линия колки кирпича (гладкий кирпич: 250мм. х 240мм.) колется пополами получается (2шт. 250мм. х 120мм. (рваный кирпич).
На промежуточном возвратном ярусе, при помощи каретки 9, металлический поддон с 32 шт. готовым(пропаренным) кирпичом доставляется к Укладчику 3, который переносит 32 шт. готового(гладкого) кирпича с металлического поддона на входной приемный стол пресса-колуна. Пустой металлический поддон, при помощи каретки 6 передвигается на Возвратный ярус.
Получив пустой металлический поддон, Возвратный ярус при помощи каретки 1, передвигает его к Гиперпрессу.
Укладчик 3, при помощи:Сжимателя, который сжимает и разжимает кирпичи(гладкие), каретки 11, которая поднимает вверх или вниз и каретки 10, которая переносит 32 шт. кирпича(гладкого) на входной приёмный стол Пресса колуна.
Пресс-колун автоматически колит кирпичи(гладкие) пополам и получается кирпич( рванный) и передвигает рваный кирпич на выходной приемный стол, который автоматически передвигает их под Укладчик 4.
Укладчик 4, при помощи Сжимателя, который сжимает и разжимает рваные кирпичи, каретки 13, которая поднимает вверх или вниз, каретки 12, которая переносит 32 шт.рваного кирпича к Упаковщику на деревянный поддон, который установлен на поворотном кругу где укладывают в стопу 512 шт. рваного кирпича.
Упаковщик автоматически упаковывает стопу 512 шт. рваного кирпича в полиэтиленовую пленку.
Каретка 9, линии отправки на холодный склад, пердвигает деревянный поддон, с стопой 512 шт. рваного кирпича, упакованного в полиэтиленовую плёнку, на улицу. Где автокар перевозит его на холодный склад.
Примечание: когда работает линия колки кирпича (Укладчик 3, пресс-колун, Укладчик 4 ) — то Укладчик 2 не работает и наоборот, когда Укладчик 2 работает — то линия колки кирпича не работает (Укладчик 3, пресс-колун, Укладчик 4 ).
И так цикл за циклом пока пропарочная камера не заполниться полностью. Легкосъемные ворота закрываются и кирпичи пропариваются при помощи пара от электропарогенератора (или газопарогенератора).
В технологической линии два пульта управления:
А) для автоматического управления бетоносмесителем, заслонками бункеров, весами для насыпания нормы, транспортерами – это для приготовления и подачи рабочей смеси в бункер станка.
Б) для автоматического управления изготовлением кирпичей до отправки их на холодный склад.
Все механизмы очень просты и надёжны в эксплуатации. Технологическая линия очень гибкая, как и пропарочная камера. Их можно изменять по длине, ширине и высоте, поэтому их можно приспособить к любым производственным зданиям (площадям).
Формование изделий в прессе происходит в автоматическом режиме, с одновременным контролем параметров качества прессуемого изделия. Пульт управления электронный для управления всеми механизмами и гидрораспределителями с электромагнитным управлением.
Виды выпускаемых изделий на данных заводах:
1. Кирпич 250мм. х 120мм. х 65мм (одинарный)
2. Кирпич 250мм. х 120мм. х 88мм. (полуторный)
3. Тротуарная плитка 200мм. х 100мм. х 70мм. (брусчатка)
|
www.vogean.com
Оборудование для производства гиперпрессованного кирпича, тротуарной плитки и других строительных материалов
|
Технология производства
Кирпичи, тротуарная плитка изделия, изготовляются из известняка, ракушечника с добавлением цемента, пигмента (без обжига) различные отсевы и отходы. Марка кирпича: 150-300. Кирпич пустотелый (различной формы пустот) и полнотелый.
Способ пропарки: пар.
Технологические линии автоматические (без ручного труда), очень гибкие, могут изменяться по длине, ширине и высоте, поэтому могут размещаться в любых готовых зданиях так и в строящихся зданиях.
В указанные квадратные метры производственных площадей входит размещение: гиперпресса, технологической линии, пропарочной камеры и бункерного отделения сыпучих материалов и другого оборудования необходимого для изготовления блоков и кирпичей, а также бытовые помещения для персонала.
Параметры (геометрия) блоков и кирпичей и качество идеальное. Срок строительства «под ключ» от 3 до 5 месяцев (в зависимости от годовой производительности завода).
Номенклатура продукции и требования к сырью:
Кроме стандартных, возможно изготовление любых пресс-форм по желанию Заказчика. Сырьевые материалы используемые для гиперпрессования кирпичей должны соответствовать требованиям ГОСТ 8267, ГОСТ 23254, ГОСТ 8268, ГОСТ 8736, ГОСТ 5576, ГОСТ 25818, ГОСТ 25592, ГОСТ 9757.
Фракция известняка, ракушечника с модулем крупности 0,3-0,4 мм;
Количество цемента – 10 – 15 % от массы смеси. Вода – 5 – 7 %. В качестве красителей может использоваться цветной цемент, а также неорганические пигменты (см. ГОСТ 6133).
Краткое описание технологической цепочки (Гиперпрессование):
1. Подача известняка
Инертные материалы (известняк, ракушечник и др.): а) загружаются Ковшевым погрузчиком в Приёмный бункер-питатель(на улице), б) выгружаются Самосвалом или ковшевым погрузчиком в Приёмный бункер-питатель в приямке (на улице).
С этого Приёмного бункера-питателя известняк по нижнему транспортеру расположенному под бункером-питателем передается на наклонный транспортер (на улице).
По наклонному транспортёру известняк подаётся в молотковую дробилку, установленной на эстакаде.
В Молотковой дробилке известняк дробится до фракции 1 мм. – 3 мм.
С Молотковой дробилки измельчённый известняк подаётся на верхний раздаточный транспортёр, который установлен на верху Бункеров–накопителей.
С верхнего раздаточного транспортёра измельчённый известняк при при помощи передвигающего Плужкового сбрасывателя сбрасывается на обе стороны транспортёра и заполняет бункеров-накопителей .
2. Подача цемента
Цементовоз привозит цемент и по пневмоподаче подаёт его наверх Силоса цемента, где запоняет его цементом.
С силоса цемента по пневмоподаче цемент подаётся в весовой бункер-дозатор цемента, который установлен над Бетоносмесителем.
Бункер-дозатор цемента дозирует норму цемента и подаёт её в Шнек цемента.
По шнеку цемента цемент подаётся в Барабан-смеситель.
3. Подача пигмента
Рабочий заполняет пигментом бункер-дозатор пигмента.
Бункер-дозатор пигмента дозирует норму пигмента и подаёт её в Шнек пигмента.
По шнеку пигмент подаётся в Барабан-смеситель.
4. Приготовление цветного цемента
В барабан-смесителе цемент и пигмент тщательно перемешиваются и образуют однородную сухую смесь-цветной цемент.
5. Приготовление рабочей смеси
С бункеров-накопителей, по нижним транспортёрам измельчённый известняк подаётся в Бетоносмеситель(весовой), при этом весовой механизм одновременно дозирует нужную норму.
С барабан-смесителя цветной цемент подаётся в Бетоносмеситель.
Измельчённый известняк и цветной цемент тщательно перемешиваются до однородной сухой смеси.
С ёмкости-дозатора воды подаётся норма воды в бетоносмеситель. Норма подачи воды контролируется датчиком влажности.
В бетоносмесителе все компоненты тщательно перемешиваются до однородной рабочей смеси.
6. Подача рабочей смеси
Из бетоносмесителя, по среднему наклонному транспортёру, рабочая смесь подаётся в бункер Гиперпресса «ВОГЕАН-2» или «ВОГЕАН-4»
7. Гиперпрессование кирпича-сырца
С бункера гиперпресса рабочая смесь питателем подаётся в форму гиперпресса и заполняет её. Происходит двух-стороннее гиперпрессование 2 шт. или 4 шт. за один цикл с давлением = 400 кг/кв.см. Питатель доставляет(новый цикл) рабочую смесь в форму и одновременно перемещает изготовленных 2 шт. или 4 шт. кирпича-сырца на приёмный стол, где формируется з пакет из 16 шт. кирпича-сырца.
8. Доставки кирпича-сырца в пропарочную камеру
С приёмного стола гипепрпресса Укдадчик 1 за один цикл переносит 16 шт. кирпича-сырца на металлический поддон. За два своих цикла Укладчик 1 переносит на металлический поддон 32 шт. кирпича-сырца.
Каретка 4 Подъёмника передвигает металлический поддон, на котором 32 шт. кирпича-сырца, вдоль пропарочной камеры на рамку Подъёмнике и передвигает металлический поддон с кирпичом-сырцом до нужной секции пропарочной камеры.
Подъёмный механизм Подъёмника поднимает рамку на которой металлический поддон с 32 шт. кирпича-сырца до нужного яруса, на нужном отсеке. Всё делается автоматически. Рамка Подъёмника останавливается на нужном ярусе и Толкатель штоком своего гидроцилиндра автоматически заталкивает металлический поддон с 32 шт. кирпича-сырца на ярус.
Пустая рамка Поъёмника, при помощи подъёмного механизма опускается вниз, за очередным металлическим поддоном с 32 шт. кирпича-сырца. Цикл работы Поъёмника: 32 шт./192 сек.(один метал. поддон с кирпичом-сырцом). И так цикл за циклом.
Когда отсек полностью заполнен кирпичом-сырцом, то с обоих сторон отсека закрываются 2 шт. лёгкие ворота(Р= 4 кг). В этот отсек подаётся пар от электро-парогенератора и происходит пропарка кирпича-сырца в течении 7 часов.
Открываются с обеих сторон ворота следующего отсека и новый цикл заполнения отсека кирпичом-сырцом продолжается.
9. Доставка готового(пропаренного) кирпича из пропарочной камеры
С яруса пропарочного отсека металлический поддон с 32 шт. готовым(пропаренным) кирпичом скатывается на рамку Съёмника и при помощи подъёмного механизма опускается вниз. Там при помощи каретки 5 передвигается вдоль пропарочной камеры, где передвигается на промежеточный возвратный ярус.
Пустая рамка Съёмника при помощи подъёмного механизма поднимается вверх, до нужного яруса на нужном отсеке, за следующим металлическим поддоном с 32 шт. готового(пропаренного) кирпича. И так цикл за циклом.
На Промежуточном возвратном ярусе, металлический поддон с 32 шт. готового(пропаренного) кирпича, при помощи каретки 6, передвигается к Укладчику 2, который заберёт 32 шт. готового(гладкого) кирпича. Пустой металлический поддон, при помощи каретка 6, передвинется на Возвратный ярус.
Получив пустой металлический поддон, Возвратный ярус при помощи каретки 1, передвигает его к Гиперпрессу.
Укладчик 2. при помощи: Сжимателя, который сжимает и разжимает кирпичи, каретки 8. которая поднимает кирпичи ввех или вниз и каретки 7, которая переносит 32 шт. готового(пропаренного) кирпича с металлического поддона который был на промежуточном возвратном ярусе на деревянный поддон, который установлен на поворотном кругу Укладчика 2. Поворот делается на 90 градусов. В стопу укладывается 16 рядов вверх. Через два ряда поворот на 90 градусов. Получается стопа по 512 шт. готового(гладкого) кирпича.
Каретка 9, линии отправки на холодный склад, передвигает деревянный поддон с стопой по 512 шт. готового(гладкого) кирпича на поворотный круг Упаковщика.
Поворотный круг Упаковщика вращается и оборачивает стопу по 512 шт. в полиэтиленовую плёнку.
Каретка 9, линии отправки на холодный склад, передвигает деревянный поддон, с стопой по 512 шт. кирпича(гладкого), упакованного в полиэтиленовую плёнку, на улицу. Где автокар перевозит его на холодный склад.
10. Линия колки кирпича (гладкий кирпич: 250мм. х 240мм.) колется пополами получается (2шт. 250мм. х 120мм. (рваный кирпич).
На промежуточном возвратном ярусе, при помощи каретки 9, металлический поддон с 32 шт. готовым(пропаренным) кирпичом доставляется к Укладчику 3, который переносит 32 шт. готового(гладкого) кирпича с металлического поддона на входной приемный стол пресса-колуна. Пустой металлический поддон, при помощи каретки 6 передвигается на Возвратный ярус.
Получив пустой металлический поддон, Возвратный ярус при помощи каретки 1, передвигает его к Гиперпрессу.
Укладчик 3, при помощи:Сжимателя, который сжимает и разжимает кирпичи(гладкие), каретки 11, которая поднимает вверх или вниз и каретки 10, которая переносит 32 шт. кирпича(гладкого) на входной приёмный стол Пресса колуна.
Пресс-колун автоматически колит кирпичи(гладкие) пополам и получается кирпич( рванный) и передвигает рваный кирпич на выходной приемный стол, который автоматически передвигает их под Укладчик 4.
Укладчик 4, при помощи Сжимателя, который сжимает и разжимает рваные кирпичи, каретки 13, которая поднимает вверх или вниз, каретки 12, которая переносит 32 шт.рваного кирпича к Упаковщику на деревянный поддон, который установлен на поворотном кругу где укладывают в стопу 512 шт. рваного кирпича.
Упаковщик автоматически упаковывает стопу 512 шт. рваного кирпича в полиэтиленовую пленку.
Каретка 9, линии отправки на холодный склад, пердвигает деревянный поддон, с стопой 512 шт. рваного кирпича, упакованного в полиэтиленовую плёнку, на улицу. Где автокар перевозит его на холодный склад.
Примечание: когда работает линия колки кирпича (Укладчик 3, пресс-колун, Укладчик 4 ) — то Укладчик 2 не работает и наоборот, когда Укладчик 2 работает — то линия колки кирпича не работает (Укладчик 3, пресс-колун, Укладчик 4 ).
И так цикл за циклом пока пропарочная камера не заполниться полностью. Легкосъемные ворота закрываются и кирпичи пропариваются при помощи пара от электропарогенератора (или газопарогенератора).
В технологической линии два пульта управления:
А) для автоматического управления бетоносмесителем, заслонками бункеров, весами для насыпания нормы, транспортерами – это для приготовления и подачи рабочей смеси в бункер станка.
Б) для автоматического управления изготовлением кирпичей до отправки их на холодный склад.
Все механизмы очень просты и надёжны в эксплуатации. Технологическая линия очень гибкая, как и пропарочная камера. Их можно изменять по длине, ширине и высоте, поэтому их можно приспособить к любым производственным зданиям (площадям).
Формование изделий в прессе происходит в автоматическом режиме, с одновременным контролем параметров качества прессуемого изделия. Пульт управления электронный для управления всеми механизмами и гидрораспределителями с электромагнитным управлением.
Виды выпускаемых изделий на данных заводах:
1. Кирпич 250мм. х 120мм. х 65мм (одинарный)
2. Кирпич 250мм. х 120мм. х 88мм. (полуторный)
3. Тротуарная плитка 200мм. х 100мм. х 70мм. (брусчатка)
|
vogean.com
Гиперпрессованный кирпич: состав, технология производства, достоинства и недостатки
Лицевой цементно-минеральный кирпич жёсткого прессования или гиперпрессованный кирпич (ГПК) строителями используется в основном в качестве отделочного (облицовочного) материала. Несмотря на его физико-технические характеристики, превосходящие по большинству параметров силикатный и керамический кирпич, есть ряд недостатков (о которых ниже), не позволяющих ему использоваться как кладочный рядовой кирпич. Далее описаны состав, метод и технология производства, а также достоинства и недостатки этого материала.
Ранее была опубликована статья «Кирпичная лицевая кладка на черный шов«, де рассказано о работе с облицовочным кирпичом и используемых для него растворах.
- В состав гиперпрессованного кирпича обязательно входят:
- Цемент средних марок (ПЦ 400, ПЦ 300), в качестве вяжущего элемента – от 8 до 20% от общей массы.
- Отсев известняка (природная прочность до 30 кг/см2), отходы от разработок камня, мрамора, мергеля или строительная тырса, придающие изделию дополнительную прочность, массовая доля которых колеблется от 65 до 85%.
ИНФОРМАЦИЯ: строительная тырса – смесь ракушечника и глины с преобладанием последней.
- железно-оксидный пигмент – 1% от общей массы сырья.
- Вода — процентным содержанием от 8 до 15.
Разность в дозировочных величинах обусловлена тем, что варьируя составляющими можно получать материалы различного назначения: кладочные, тротуарные или сейсмостойкие.
ВАЖНО: на качественные характеристики гиперпрессованного кирпича большое влияние оказывает «свежесть» цемента и чистота воды.
- Технология производства.
Метод «гипер» или двухстороннего прессования заключается в получении материалов путем взаимодействия при сжатии мелко дисперсных частиц проходящего под воздействием избыточного давления. В отличие от одностороннего прессования, где зона избыточного давления покрывает прессуемую массу неравномерно, материал, получаемый методом гипрепрессования имеет мельчайшую структуру (пора 0,07 – 0,3 мм), что уменьшает его влагопоглощение, увеличивает прочность на сжатие и одновременно повышает его теплопроводность до 1,08 – 1,09 Вт/м2.
С другой стороны, метод двухстороннего прессования позволяет уменьшать нормы вяжущего без потерь физических характеристик материала, что позволяет удешевить производственное оборудование.
Непосредственно технология производства. Производственную базу можно разделить на три участка:
- Первичный склад, где осуществляется накопление и подготовка основного сырья к производству. Здесь через грохоты и механические сито происходит измельчение материала, и по механическим транспортёрам масса подается дальше.
- Производственный участок включает в себя несколько подразделений.
— измельчённая масса поступает в смесительный узел, где в неё в необходимых количествах добавляется цемент, вода и цветовой пигмент. Время полного смешивания не превышает 5 минут.
— далее готовая прессовая масса выгружается в ковш подъёмного транспортёра, который доставляет её в полуавтоматический дозатор, расположенный на рампе поверх прессов.
— двигаясь по рампе, полуавтоматический дозатор, управляемый оператором, засыпает сырьё в накопительные бункера прессов.
— прессование одного кирпича длится от 8 до 10 сек, в зависимости от типа получаемого изделия.
На прессах, в зависимости от применяемых матриц, можно изготавливать полнотелые и пустотелые элементы, а также скруглённые и с усечённой гранью.
— готовое изделие рабочим снимается с прессовочного стола и укладывается на поддоны.
Далее изделия отправляются на склад готовой продукции, где материал «зреет» до нужной кондиции.
- готовой продукции не требует особых температурных или специальных условий для окончательной выдержки кирпича и может располагаться на открытых площадках.
Готовый кирпич находится на складе не менее 5 дней и приобретя 50 – 60% своей прочности готов для отправки заказчикам. Полная прочность изделий наступает через 28 дней, что может происходить в готовой кладке.
Часть полнотелых изделий может направляться на складской производственный участок для изготовления декоративных элементов – «колотой четверти».
Для этого используется ножной регулируемый пресс – гильотина. Рабочий, подставляя кирпич под нож, делает надкол на узкой грани. После, располагая его надколотой гранью вниз, отсекает половину элемента. Получается две части, одна из которых имеет вогнутую структуру и в дальнейшем не используется. Выпуклая половина становится элементом декоративной отделки с уникальным структурным рельефом и стоимостью в 2,5 раза дороже обычного полнотелого кирпича.
Такие элементы изготавливаются только по предварительным заказам.
- Достоинства и недостатки гиперпрессованного кирпича
Достоинства ГПК:
- Идеальная геометрия. Она получается потому, что данная технология является безобжиговой и готовые элементы не подвергаются термической обработке, при которой могут происходить незначительные изменения геометрических параметров.
- Низкое влагопоглощение, около 4,8% от общей массы согласно нормам ГОСТ 7025-78.
- Высокая прочность. Кирпич соответствует марке 250 (ГОСТ 379-79).
- Возможность прочностных вариаций (по желанию заказчика).
- Хорошая адгезия. Прочность сцепления раствора с кирпичом около 2,5 кг/см2, что перекрывает требования для кладки 1-ой категории.
- Хорошая морозостойкость. Кирпич не меняет своих характеристик при 150 циклах замораживание/оттаивание.
- Экологически чистый материал, так как в его составе нет вредных примесей.
- Хорошо режется и обрабатывается.
- Разнообразие форм, содержания и фактуры элементов.
- Разнообразие цветовых решений.
Безусловно, с такими характеристиками ГПК должен иметь массовое применение во всех областях жилищного и промышленного строительства, кроме огнеопасных строений. Но есть у него и недостатки, которые не позволяют этому материалу полновесно завоевать рынок.
Недостатки ГПК:
- Высокая стоимость по сравнению с обычным рядовым кирпичом.
- Вес полнотелого кирпича равен 4,5 кг, что превышает вес обычного кирпича почти в два раза.
- Низкая паропроницаемость, что предусматривает в домах, отделанным таким материалом устройство дополнительных систем вентиляции или устройство сквозных воздушных пазух между ним и основными стенами.
- Цветовая погрешность различных партий, не видимая на поддоне, но очень заметная в кладке.
- На длительных сроках эксплуатации, особенно на солнечных сторонах зданий, наблюдается «выгорание» цветового пигмента. Но это практически не заметно, так как цвет меняет вся стена.
- Класть такой кирпич необходимо очень аккуратно, с расшивкой. Это замедляет темпы выполнения строительных работ и ведёт к их удорожанию.
Таким образом, сферы применения гиперпрессованного кирпича ограничиваются отделочными функциями наружных стен нижних этажей, заборами дорогих частных домостроений, постройкой беседок и других сопроводительных строений.
Но можно отметить, что ёмкость рынка ГПК медленно, но уверенно растёт, что позволяет с оптимизмом смотреть в будущее производителям данного материала.
11,993 просмотров всего, 1 просмотров сегодня
smogem-sami.ru
Оборудование для мини-кирпичных заводов на базе гиперпрессов
Кирпичный пресс TITAN 80L (L=Lego) подходит для организации мини-заводов для производства лего-кирпича из отсевов горных пород (известняк, ракушняк, мрамор, доломит, гранит и пр.). Пресс является одним из самых доступных из выпускаемых нами на данный момент и обладает прекрасным соотношением цена/производительность.
Кирпичный пресс TITAN 80L имеет несколько вариантов исполнения. Основным вариантом является пресс с пневмозахватами для выгрузки готовой продукции. Пневмозахваты обеспечивают плавный, предельно аккуратный автоматический съем готовой продукции.
Основным отличием нашего пресса от прессов наших конкурентов является очень высокое удельное давление прессования в пересчете на 1 кирпич (порядка 82 тонн) и полная автоматизация рабочего процесса. Давление наших прессов более чем в 4-5 раз превышает давление прессов наших конкурентов. Система управления на базе контроллера Schneider делает его настройку очень простой и точной. Пресс серии TITAN 80 L разрабатывался с использованием опыта американских, немецких и украинских производителей. Конструкция кирпичного пресса наиболее оптимальна из известных на данный момент. Пресс TITAN 80L позволяет выпускать продукцию с высотой до 70 мм (на некоторых видах сырья – до 88 мм). Указание максимальной высоты изделий условно, ввиду того, что на всех наших прессах мы производим расчеты исходя из показателя уплотнения сырья в 2,4, что является фактически максимальным показателем для наиболее рыхлых видов сырья. При работе с сырьем с меньшим коэффициентом уплотнения удается достигнуть большей высоты изделия.
Гиперпресс TITAN 80L прежде всего предназначен для выпуска высококачественного облицовочного лего-кирпича и облицовочной плитки. Следует сказать, что данный пресс разрабатывался специально для этих целей и он не имеет аналогов в КНР (для внутреннего рынка Китая мы производим очень большие прессы в которых невозможно добиться минимальных допусков критически важных при производстве именно облицовочного кирпича).
В данных прессах используются комплектующие только самых известных фирм (гидравлика фирмы Huade (лицензионный Bosh-Rexroth), электродвигатели Siemens Standard, электроника Schneider). Наш пресс не имеет сложных систем увеличения давления с помощью мультипликаторов, что требует установки очень капризной гидравлики. Мы добиваемся высокого давления прессования и высокой скорости работы прессов за счет надежных цилиндров большого диаметра изготовленных из цельной поковки, высокопроизводительных насосов, внедрения дополнительных цилиндров быстрого хода.
Наш гиперпресс имеет два гидравлических контура – для основных цилиндров высокого давления и цилиндров быстрого хода. Использование цилиндров быстрого хода в совокупности с оптимальностью конструкции позволяет нам существенно увеличить производительность пресса. Кирпичный пресс TITAN 80L является прессом одностороннего действия оригинальной конструкции, который имеет много “ноу-хау”.
titan-machinery.com