технологические отличия и показатели. Какой метод получения цемента выбрать?
Существует несколько методов изготовления цемента: мокрый, полусухой, комбинированный и сухой. Основными способами, которые применяются на ведущих заводах, являются сухой и мокрый.
Мокрый способ производства цемента
Схема изготовления цемента мокрым методом представлена на рисунке ниже.
Производство начинается с извлечения из карьеров твердого известняка, который впоследствии дробится на куски различного размера. Затем куски измельчаются в дробильных агрегатах, пока размеры частей известняка не будут превышать 8-10 мм.
Затем на мини-завод транспортируют глину из карьера и обрабатывают ее в вальцевых дробилках до той степени, пока размер кусочков будет достигать от 0 до 100 мм.
Далее измельченную смесь отмачивают в болтушках. В результате получается шлам из глины, влажность которого составляет до 70 %.
Затем он поступает в мельницу, где происходит процесс смешивания и размалывания с известняковой массой.
После этого шлам влажностью около 40 % направляется в вертикальный бассейн, в котором выполняется окончательный процесс корректировки. Эта операция имеет исключительное значение, так как на этом этапе обеспечивается химическая формула состава произведенного шлама.
Только после того как шлам пройдет контроль качества, он допускается к последующим этапам. Далее цементная масса транспортируется из вертикального оборудования (бассейна) в горизонтальный, в котором происходит хранение смеси перед поступлением в печь обжига. В горизонтальном бассейне сырьевая масса постоянно помешивается механическим путем с применением сжатого воздуха. Благодаря этому шлам не выпадает в осадок и полностью гомогенизируется. Если в процессе изготовления цемента применяются сырьевые компоненты, что имеют неизменный химический состав, то корректировка химического состава шлама осуществляется в горизонтальном бассейне.
Затем шлам направляется в печь для обжига, в которой он превращается в клинкер. Полученная клинкерная основа цемента поступает в промышленный холодильник для охлаждения. После этого клинкер подвергается дроблению и подается в бункеры мельниц. Там клинкерная масса повторно измельчается.
Если для процесса обжига шлама используется твердое топливо, то возникает необходимость в строительстве дополнительного помещения для хранения и подготовки угля. Когда в производственном процессе применяется жидкое или газообразное топливо, то схема обжига клинкерной смеси имеет упрощенный вид.
В завершение цемент перенаправляется из бункеров мельниц в специальные помещения для хранения. На этом производственном этапе лаборанты осуществляют контроль качества продукции и определяют марку цемента. Только после этого продукция направляется в упаковочные аппараты.
Сухой способ производства цемента
Схема изготовления цемента сухим методом представлена на рисунке ниже.
Во время производства цемента сухим методом используется другая технологическая схема. Глина и известняк, добытые из карьера, после дробления направляются в сепараторную мельницу, где осуществляется помол, смешивание и сушка сырьевых компонентов. Полученная смесь направляется к смесительным аппаратам, где выполняется окончательное смешивание с применением сжатого воздуха. На данном этапе осуществляется корректировка химического состава цементной смеси.
Если применяется глинистый компонент, то сырьевая смесь подается для смешивания в шнеки, в которых происходит частичное увлажнение водой. На этом этапе образуются прочные гранулы, что имеют влажность не более 14 % — далее они поступают в печь для обжига.
При сухом методе производства процесс обжига сырья может выполняться в различных печах, здесь особое внимание уделяется приготовлению сырьевой массы. Дальнейшие этапы технологического процесса осуществляются так же, как и при мокром методе производства.
Особенности полусухого способа производства
Схема изготовления цемента полусухим методом представлена на следующем рисунке.
Полусухой метод производства цемента очень похож на сухой, но отличия все же есть.
Размер муки, что проходит стадию гранулирования, составляет 10-20 мм, а влажность 11-16 %. Сырье обжигается в печах Леполь и после этого образовавшиеся гранулы направляются на конвейерный кальцинатор.
Из печки выделяются газы, что проходят сквозь гранулы на решетке. В результате этого происходит их нагрев до 900 ºС и они полностью высушиваются. Во время такой термообработки выполняется декарбонизация смеси на 22-30 %, что важно для производства. По завершению этих процессов сырье направляется в печь, где и завершается процесс изготовления цемента. Обжиг гранулированного цемента может происходить в шахтных печах. При этом гранулирование выполняется с частицами угля, после этого цемент направляется на хранение.
Комбинированный метод производства цемента
Схема изготовления цемента комбинированным методом отображена на рисунке ниже.
Этот метод основывается на подготовке сырьевых компонентов по мокрому способу, а их обжиге – по схеме полусухого способа. Полученный в сырьевой мельнице шлам влажностью 30-45 % поступает в специальный фильтр, в котором он обезвоживается до влажности 15-20 %. Далее сырьевая смесь смешивается с пылью, что снижает влажность до 12-14 %.
Затем смесь поступает на обжиг, который выполняется в печах полусухого метода изготовления цемента. Остальные операции комбинированного метода не отличаются от этапов мокрого способа производства.
Методы производства выбирают исходя из технико-экономических и технологических факторов: свойств сырьевых компонентов, однородности и влажности смеси, наличия мощной топливной базы и других.
Полезное и важное по теме:
Поделитесь статьей с друзьями:
Мокрый и сухой способ производства цемента: основные отличия
Так называемые «мокрая» и «сухая» технология производства цемента являются самыми распространенными способами получения этого незаменимого строительного материала.
СодержаниеСвернуть
Российские цементные заводы используют преимущественно «мокрый» метод, в то же время практически все зарубежные производители связующего работают по «сухой технологии».
Отличия мокрой технологии производства цемента от сухой
Обе технологии имеют свои преимущества и свои недостатки. Основной недостаток, которым отличается мокрый способ производства цемента – значительная энергоемкость процесса, отражающаяся на себестоимости конечного продукта. Сухая технология отличается большей экологической опасностью и соответственно большими капитальными затратами на устранение данного фактора. Рассмотрим оба способа производства цемента подробнее.
«Мокрая» технология производства связующего
Технологическая схема мокрого способа предусматривает раздельную первичную обработку компонентов клинкера. Измельченные «ингредиенты» загружаются в специальное оборудование для кратковременной выдержки под слоем воды. После этого компоненты клинкера, мокрыми, попадают в специальные мельницы, где их перемалывают до состояния порошка и тщательно перемешивают.
Подготовленный таким образом шлам подается в вертикальные и горизонтальные «шлюмбассейны» на корректировку необходимого соотношения «ингредиентов». Следующей технологической операцией идет печной обжиг откорректированного шлама и охлаждение промышленными холодильными установками. Полученный таким образом клинкер измельчается до мелкодисперсного порошка – цемента. Далее производятся: лабораторный анализ на соответствие цемента требованиям ГОСТ, фасовка и отправка потребителю.
Преимущества «мокрой» технологии
- Меньшие технологические затраты на измельчение сырья. Такие компоненты как мел и глина хорошо размокают в воде при первичной обработке в бассейнах. Соответственно процесс их измельчения происходит намного проще и легче;
- Транспортировка, усреднение и корректировка шлама происходит проще и экологически безопаснее, чем аналогичные операции при сухой технологии;
- В разы меньшее пылеобразование;
- Конструкция печей обжига шлама проста, надежна и имеет высокий Коэффициент Использования пространства – от 0,89 до 0,91;
- Имеется принципиальная возможность использовать сырьевые компоненты «пестрого» химсостава и хорошей гомогенизации шлама.
Недостатки
- Большой удельный расход тепловой энергии на обжиг сырья для производства цемента. Сырье поступающее на обжиг, имеет среднюю влажность 35-45%. Соответственно для испарения влаги и прогрев компонентов требуется порядка 5 450-6 800 кДж/кг тепловой энергии или 35% тепловой мощности печи. Поэтому часть обжиговой печи работает как сушильный агрегат со всеми вытекающими «неприятностями»;
- Высокая материалоемкость обжиговых печей при небольшой производительности.
Указанные недостатки выливаются в относительно низкую производительность труда, значительные технологические и эксплуатационные расходы, обуславливающие относительно высокую себестоимость производства.
«Сухая» технология производства связующего
В этом случае основное производственно-технологическое оборудование аналогично мокрому способу. Изменения заключаются в принципиально иной технологической схеме производства клинкера. После предварительного измельчения компоненты клинкера подаются в сушильные барабаны, причем каждый компонент подается в отдельный барабан.
Следующая операция обусловлена видом и влажностью глины. Все остальные компоненты корректируются по указанным параметрам глины. Суть операции заключается в незначительном увлажнении (не более 13% влажности) шлама и последующую подачу на обжиг. Соответственно небольшой влажности энергетические затраты на обжиг небольшие, а печи менее металлоемки и менее габаритны. Операции, следующие после обжига шлама, аналогичны предыдущему способу производства цемента.
Преимущества «сухой» технологии
- Относительно невысокий удельный расход тепловой энергии расходуемой на обжиг клинкера – 2 900-3 700 кДж/кг;
- Меньший на 30-40% объем печных газов при аналогичной производительности и возможность их вторичного использования для сушки компонентов. Это позволяет существенно снизить энергозатраты на производство клинкера и требует меньших капиталовложений на обеспыливание;
- Относительно меньшая металлоемкость обжиговых печей при большей производительности по сравнению с «мокрой» технологией.
Производственная мощность печей при «сухом» способе – от 3 000 до 5 000 тонн продукта в сутки, что на 100-200% мощнее аналогичного оборудования работающего по «мокрой» технологии;
- Отсутствует необходимость в наличии мощных источников технологической воды.
Недостатки
- В разы большее пылевыделение, обуславливающее сложность обеспечения санитарных норм и охрану окружающего пространства;
- Относительная сложность конструкции обжиговых печей;
- «Капризность» обжиговых печей по отношению колебаний химсостава сырья, его дисперсности и степени важности;
- Относительно низкий Коэффициент Использования печей – от 0,7 до 0,8;
Более высокая трудоемкость энергоемкость на помол компонентов, обусловленные их низкой влажностью.
Сухой способ производства портландцемента — Справочник химика 21
Существует два основных способа производства портландцемента мокрый и сухой. В первом случае шихта подвергается мокрому помолу с добавлением воды, в результате чего получается вязкая суспензия—пульпа (шлам).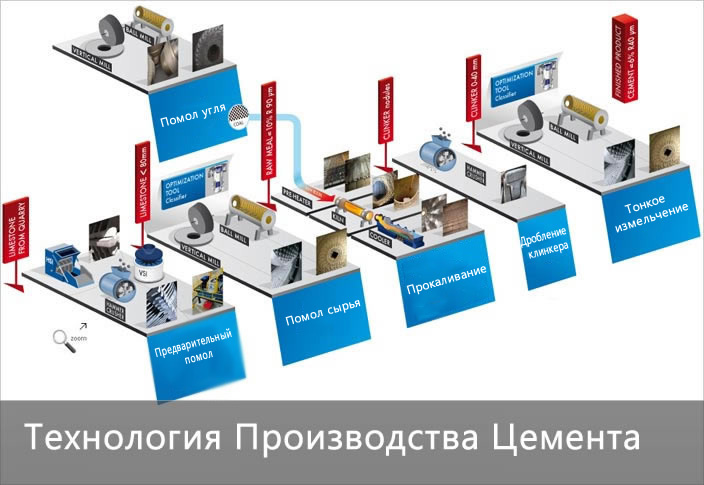
Сухой способ производства портландцемента во вращающихся печах [c.139]
Сухой способ производства портландцемента в автоматических шахтных печах [c.142]
Дальнейшие технологические операции при сухом способе производства портландцемента — подготовка гидравлических добавок и гипса, помол цемента, его хранение и отправка потребителю —остаются аналогичными рассмотренным при мокром способе. [c.43]
СУХОЙ СПОСОБ ПРОИЗВОДСТВА ПОРТЛАНДЦЕМЕНТА [c.40]
Отличительной особенностью измельчения клинкера по сравнению с помолом сырьевых материалов лри сухом способе производства портландцемента является более высокая твердость клинкера. Кроме того, для получения цемента размалываемые зерна должны иметь заданный гранулометрический состав. Последними исследованиями установлено, что цемент, содержащий в определенном сочетании мелкие и относительно крупные зерна, обладает наиболее высокими физико-механическими показателями. [c.277]
Сырье к обжигу готовят двумя способами — мокрым и сухим. В соответствии с этим и способы производства портландцемента подразделяют на мокрый и сухой. [c.158]
Измельчают и перемешивают тонкоиз.мельченные материалы или в присутствии воды, или в сухом виде. В зависимости от этого различают два основных способа производства портландцемента — мокрый и сухой. При мокром способе подготовка и смешивание сырьевых материалов осуществляются в присутствии воды, а при сухом материалы измельчают и смешивают в сухом виде. [c.35]
Сухой способ преобладает в Японии, Швеции, ФРГ, Италии. В этих же странах, а также в США все шире начинает применяться комбинированный способ производства портландцемента. [c.35]
Комбинированный способ производства портландцемента заключается, как отмечалось ранее, в подготовке сырьевых материалов по мокрому способу, а обжиге — по схеме сухого способа. Основные технологические операции и последовательность их выполнения при комбинированном способе получения клинкера следующие [c.43]
Грануляцию сырьевой смеси применяют при сухом или ком бин ированном способах производства портландцемента. Грануляцию проводят для того, чтобы получить из сырьевой муки или из шламового сухаря , прочные зерна (гранулы), обеспечивающие хорошую газопроницаемость слоя материала при обжиге в шахтных печах или на решетках конвейерного кальцинатора (см. обжиг по сухому способу). [c.168]
Сырье к обжигу готовят двумя способами — мокрым и сухим.
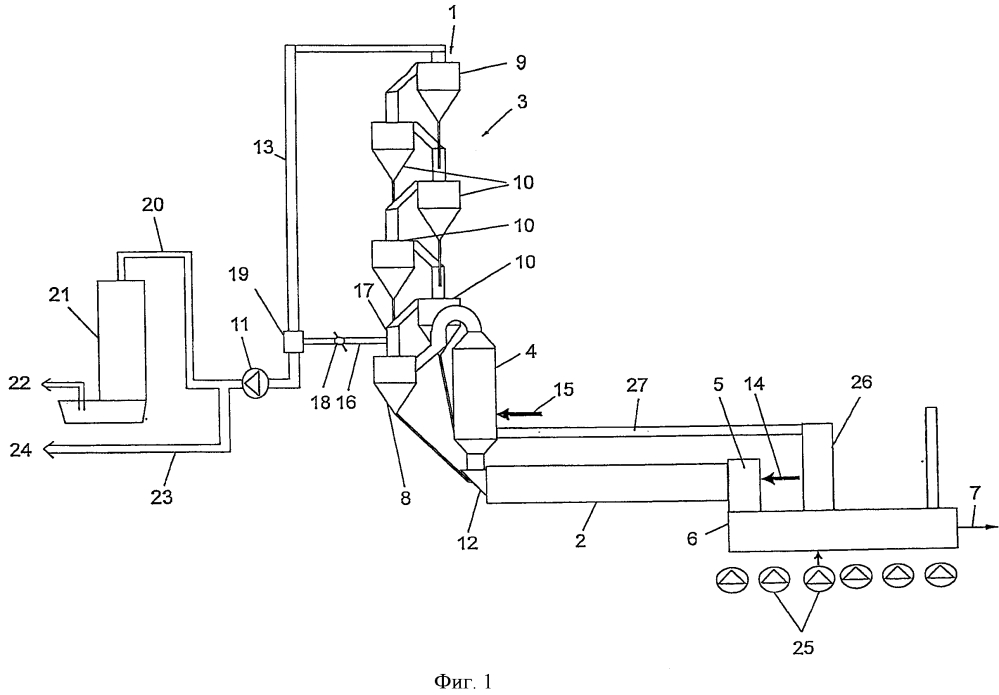
Производство портландцемента ведут двумя способами — мокрым и сухим, из которых у нас используют почти исключительно первый. При этом способе все виды сырья после их измельчения дроблением смешивают и подвергают размолу в водной среде в шаровых мельницах. Полученный шлам — густая суспензия, содержащая 35—40% воды, поступает на усреднение в большие бассейны, где тщательно перемешивается. Здесь хранится его запас и отсюда он поступает на обжиг во вращающуюся печь. Этот аппарат является типовым и применяется для проведения обжига во многих производствах. Печь представляет собой (рис. 50) стальной барабан 1 длиной до 185 м и диаметром до 5 м, футерованный шамотным и хромомагнезитовым кирпичом, установленный почти горизонтально, лишь с небольшим наклоном (2—5°) для непрерывного перемещения шихты. На барабан надеты стальные кольца — бандажи 2, посредством которых (при вращении печи от электромотора 4 и шестерен 5) происходит ее качение по опорным роликам 3. Шлам непрерывно подается в печь питателем 6 и нагревается движущимися противоточно раскаленными топочными газами, образующимися при сгорании в противоположной части печи топлива—каменноугольной пыли, жидкого котельного топлива или природного газа. [c.133]
Производство портландцемента ведут двумя способами — мокрым и сухим, из которых у нас используют почти исключительно
Линия по производству цемента
Характеристики производственной линии цемента
Цементная производственная линия — это проект по строительству производственной линии, состоящий из ряда вспомогательного оборудования, которое используется для производства цемента.Наш коэффициент возврата удовлетворенных клиентов при поддержке нашего квалифицированного специалиста по цементному заводу , мы успешно устанавливаем цементные заводы в Индии, Страны Средней Азии, Южной Америки и Южной Африки. Проектирование процесса поставки Great Wall 、 гражданское строительство 、 комплектное оборудование 、 установка и пробный запуск 、 технические услуги 、 генеральный подряд. Наша полная производственная линия: линия по производству цемента 6000 т / д, линия по производству цемента 5000 т / д, линия по производству цемента 3000 т / д, линия по производству цемента 2500 т / д, линия по производству цемента 1500 т / д, линия по производству цемента 500 т / д, 300 т / Д строительство линии по производству цемента.
Как ведущий производитель цементных заводов, компания Great Wall Machinery Co., LTD предлагает все виды качественных цементных заводов под ключ, установку оборудования, оборудование для цементных заводов, установку тяжелой промышленности и заводы по производству удобрений.Помимо цементных заводов мы также известны поставщиками промышленных шестерен и производителями оборудования, такими как шаровые мельницы , вращающиеся печи, ленточные конвейеры, вертикальная мельница и другое оборудование для транспортировки материалов для оборудования цементных заводов и т.
Мы производим все типы погрузочно-разгрузочного оборудования и складских единиц для цементных заводов, такие как: ковшовые элеваторы, конвейеры, заслонки и воздушные заслонки, а также комплектные упаковочные единицы. Мы также предоставляем услуги по техническому обслуживанию существующих цементных заводов по всему миру.
1.Своевременная и быстрая доставка
Chaeng Machinery оснащена большим сталелитейным цехом и цехом механической обработки, которые обеспечивают быстрое и качественное производство сопутствующего оборудования линии по производству цемента. Кроме того, товар доставляется в срок, что сокращает временные затраты покупателей.
2. Отличный сервис
Компания предоставляет клиентам всесторонний сервис, включая разработку проектов, обучение работе, наплавку валков, обслуживание жерновов, техническую поддержку и т. Д., Благодаря чему клиенты могут безопасно использовать нашу продукцию и производить ее эффективно.
3. Зрелый генеральный подрядный проект
Компания имеет высококлассную техническую команду и сотрудничает с главными специалистами вертикальных валковых станков . Компания может разработать подробный генподрядный проект в соответствии с реальной ситуацией клиентов и предоставить комплексные услуги под ключ от строительных проектов до производства и эксплуатации.
4. Передовая технология производства цемента сухим способом
Линия по производству цемента, запущенная компанией, использует хорошо зарекомендовавшую себя новую технологию приготовления цемента сухим способом, которая эффективно снижает потребление тепла, снижает производственные затраты и повышает эффективность.
Технологический:
1. Измельчение : в процессе производства цемента большая часть сырья должна быть измельчена. Известняк является самым большим сырьем для производства цемента, поэтому дробление известняка занимает важное место при дроблении материалов на цементных заводах.
2. Предварительная гомогенизация : Технология предварительной гомогенизации сырья обеспечивает начальную гомогенизацию сырья с помощью научных технологий укладчика и регенерации во время процесса хранения и регенерации сырья, гарантируя, что измельченный сырьевой материал имеет возможность хранения и гомогенизировать.
3. Гомогенизация сырья : В сухом процессе производства цемента стабилизация ингредиента сырья является предпосылкой для спекания клинкера, система гомогенизации сырья используется для стабилизации ингредиента сырья на входе в печь.
4. Предварительный нагрев и разложение : Мы используем предварительный нагреватель для завершения предварительного нагрева сырья, частично заменяем возможности вращающейся печи и уменьшаем длину вращающейся печи. Материалы завершили обмен теплового газа внутри вращающейся печи в состоянии приостановки и предварительного нагрева.
5. Право разделения газа и твердого вещества : Когда воздушный поток с порошком материала попадает в циклон и вынужден вращаться в кольцевом пространстве между цилиндром циклона и внутренним цилиндром при движении вниз.
6. Прекальцинирование : Технология прекальцинации Great Wall — это технологический прорыв в процессе кальцинации цемента. Он добавляется между подогревателем и обжиговой печью с использованием дымохода хвостовой части печи, устанавливает устройство впрыска топлива, так что процесс эндотермического экзотермического разложения карбоната в процессе сгорания топлива и сырья в печи разложения быстро переводится во взвешенное или псевдоожиженное состояние. , так что степень разложения сырья в печь увеличивается до 90%.
7. Спекание : После завершения подогревателя и прекальцинатора, следующий процесс осуществляется в обжиге клинкерной печи. Карбонат быстро растворяется, и во вращающейся печи происходит серия твердофазных реакций, в которые вводится минерал. По мере приближения температуры материала жидкость превратится в минералы, растворенные в жидкофазной реакции и образующие большое количество. После обжига клинкера температура стала снижаться. Наконец, охладитель цемента / клинкера, передающий температуру охладителя печи для последующей транспортировки, складских библиотек и цементной мельницы, может выдерживать температуры горячего клинкера, регенерируя явное тепло, улучшая термический КПД системы и качество клинкера.
-Китайская компания Henan Zhengzhou Mining Machinery Co., Ltd.
Производительность: 50 т / д-3000 т / д
Основные материалы: известняк, глина, гипс, летучая зола, шлак
Основное оборудование: цементная мельница, цементная печь, рукавный фильтр
Введение
Мы предоставляем полный спектр услуг, включая проектирование, изготовление, установку.Мы проектируем и производим оборудование для новой линии по производству цемента сухим способом, производительность которой варьируется от 50 т / сут до 3000 т / сут
Наше преимущество
1
Высокая эффективность
Линия по производству цемента использует передовые технологии и оборудование для повышения технического уровня и обеспечения проектных показателей. Новая пятиступенчатая циклонная система предварительного нагрева, высокоэффективный охладитель с решетчатой решеткой, многопроходная горелка для измельчения угля, тепловентилятор Дэвисона, струйный импульсный пылеуловитель, а также элеватор с цепной доской, цепной конвейер, принятый в этой производственной линии, может убедиться, что технология является более совершенной по сравнению с другими производственными линиями того же масштаба.
2
Энергосбережение
Были приняты меры для экономии энергии и снижения потребления. с помощью подъемника с цепным бортом и воздушных направляющих повышается надежность системы и снижается потребление энергии при транспортировке.
3
Охрана окружающей среды
Были приняты эффективные меры, чтобы гарантировать строгие стандарты защиты окружающей среды. Во всех точках пылеулавливания установлены различные эффективные пылеуловители в соответствии с различными характеристиками отходящего газа.
4
Высокая степень автоматизации
В процессе работы мельницы нет ручного управления, что обеспечивает автоматическое управление с долгосрочным, стабильным, эффективным, делает процесс фрезерования более стабильным, реализует тонкую работу производства.
Технология производства
Добытый известняк доставляется в дробилку для дробления ленточным конвейером , известняк после дробления, глина, железный порошок и т. Д. Измельчаются в порошок шаровой мельницей или вертикальной мельницей , а затем транспортируются по желобу подачи воздуха. в бункер гомогенизации сырьевой смеси для хранения и дальнейшего перемешивания материалов.Сырьевая мука должна попасть в систему разложения предварительного нагрева после гомогенизации, где степень разложения составляет около 95%, и сырая мука кальцинируется в клинкер во вращающейся печи , — с образованием клинкера. Клинкер, гипс и смесь перемалываются в цемент высокой тонкости помола на цементной мельнице . Порошковый классификатор используется для регулирования крупности цемента, что позволяет экономить энергию. Машина для упаковки цемента и автомат загрузки используются для доставки цемента в мешки, а устройство для наливов цемента — для разливки цемента с завода.
Технологическая карта
Конфигурация
Линия по производству цемента сухим способом (25-200 т / день) Конфигурация
Вместимость | 25т / д | 50 т / д | 100 т / д | 150 т / д | 200 т / д | |
Вращающаяся печь | Спецификация | Φ1.4 × 33м | Φ1,6 / 1,9 × 36 м | Φ2,2 × 45 м | Φ2,5 × 50 м | Φ3 × 60 м |
Вместимость | 1т / ч | 2т / ч | 4т / ч | 6т / ч | 8т / ч | |
Кальцинирование Температура (℃) | 1450 | 1450 | 1450 | 1450 | 1450 | |
Сырьевая мельница | Спецификация | Φ1.2 × 4,5 м Обрыв | Φ1,5 × 5,7 м Обрыв | Φ1,83 × 6,1 м Обрыв цепи | Φ1,83 × 6,1 м Замкнутый контур | Φ2,2 × 6,5 м Замкнутый контур |
Вместимость | 1.7т / ч | 4,5т / ч | 9т / ч | 12т / ч | 16т / ч | |
Мощность двигателя | 55кВт | 130 кВт | 210кВт | 210кВт | 310кВт | |
Цементная мельница | Спецификация | Φ1.2 × 4,5 м Обрыв | Φ1,5 × 5,7 м Обрыв | Φ1,83 × 6,1 м Обрыв цепи | Φ1,83 × 6,1 м Замкнутый контур | Φ2,2 × 6,5 м Замкнутый контур |
Вместимость | 1.4т / ч | 3,5т / ч | 6.5т / ч | 8т / ч | 12т / ч | |
Мощность двигателя | 55кВт | 130 кВт | 210кВт | 210кВт | 310кВт |
Конфигурация новой линии по производству цемента сухим способом (300-1500 т / сут)
Вместимость | 300т / сут | 700 т / д | 1000 т / д | 1500 т / д | |
Предпусковой подогреватель | C1 | 2-Φ2500 | Φ3500 | Φ4800 | 2-Φ4000 |
C2 | Φ3600 | Φ4800 | Φ4800 | Φ5800 | |
C3 | Φ3600 | 2-Φ3700 | Φ5200 | Φ5800 | |
C4 | Φ3600 | Φ4800 | Φ5200 | Φ6200 | |
C5 | Φ3600 | Φ4800 | Φ5200 | Φ6200 | |
Кальцинатор | Спецификация | Φ2200 | Φ2800 | Φ4800 | Φ5200 |
Вращающаяся печь | Спецификация | Φ2.8 × 44м | Φ3 × 48 м | Φ3,2 × 50 м | Φ3,5 × 54 м |
Вместимость | 12,5т / ч | 30т / ч | 42т / ч | 63т / ч | |
Температура прокаливания (℃) | 1450 | 1450 | 1450 | 1450 | |
Сырьевая мельница | Спецификация | Вертикальная валковая мельница Φ1700 | Сухая мельница Φ3.2 × 7 + 1,8 м | Сухая мельница Φ3,5 × 10 м | HRM2800 Вертикальная валковая мельница |
Вместимость | 30т / ч | 50т / ч | 85т / ч | 130 ~ 160т / ч | |
Мощность двигателя | 400 кВт | 1000 кВт | 1250кВт | 1250кВт | |
Цементная мельница | Спецификация | Φ2.4 × 13м Обрыв | Φ3 × 11 м Замкнутый контур | Φ3,2 × 11 м Замкнутый контур | Φ4,2 × 13,5 м Замкнутый контур |
Вместимость | 22т / ч | 42т / ч | 64т / ч | 95т / ч | |
Мощность двигателя | 800 кВт | 1250кВт | 1400кВт | 3550кВт |
Наша компания | Девня Цемент
Девня Цемент АО — крупнейший производитель цемента в Болгарии, расположенный в городе Девня, работает с 4 декабря 1958 года.Компания — лидер местного рынка . С 1998 года было вложено много средств в приобретение и модернизацию процессов и производственных мощностей. Убедившись в большом потенциале роста и развития строительной отрасли в Болгарии, компания делает шаг вперед в строительстве новой линии по производству клинкера и сухого цемента . На современном высокотехнологичном предприятии внедрены лучшие существующие технологии производства цемента.Таким образом, компания укрепила свои позиции в качестве ведущего производителя цемента и инновационной строительной продукции с многочисленными наградами за свои достижения в различных областях.
АО «Вулкан Цемент» — шлифовальный центр, расположенный в городе Димитровград Хасковского района, действует с 16 октября 1947 года. Завод имеет большие производственные мощности по помолу цемента и мелкозернистого камня, современное оборудование для упаковки и паллетирования готовой продукции. в бумажных мешках по 25 кг и 50 кг, а также установку для биг-бегов, силосохранилище, построенную железнодорожную инфраструктуру для доставки и отправки товаров и материалов.В шлифовальном центре используется клинкер фирмы Devnya Cement, что обеспечивает гарантированно высокого качества готовой продукции.
Терминал Дамяница — это логистический центр, расположенный в селе Дамяница Благоевградского района. Он работает с 1978 года и выполняет функцию доставки цемента навалом и фасованным цементом в Юго-Западную Болгарию и Македонию.
Heidelberg Beton — это новейший бренд HeidelbergCement Group в Болгарии, целью которого является обеспечение высококачественного бетона и удовлетворение требований каждого клиента.Первый завод по производству товарных смесей бренда находится в Варне. Вы можете найти весь ассортимент продукции на этом веб-сайте в разделе «Продукция».
Компании входят в состав HeidelbergCement Group. Знак качества и качества почти в 50 странах мира.
За более чем 145 лет с момента основания в 1873 году компания HeidelbergCement превратилась из местного производителя цемента с одним заводом в Гейдельберге в одного из ведущих мировых производителей строительных материалов.