Система автоматизации оборудования производства автохимии
Компания ПРОЕКТ-П разработала для компании «Эверклин» (г. Москва) систему автоматизации оборудования производства автохимии. Торгово-производственная компания «Эверклин» разрабатывает, производит и реализует под торговой маркой LERATON автохимию и товары для автомойки и детейлинга. В целях расширения и модернизации предприятия было приобретено технологическое оборудование для производства моющих средств (автохимии), сконструированное по собственным эскизам инженеров компании. Оборудование представляет собой четыре химических реактора, каждый из которых выполняет свою функцию в технологии производства автохимии.
Функциональные требования к системе автоматизации производства автохимии
- Дозирование воды в реакторы с помощью двух насосов с разной производительностью и счетчика воды в ручном и полуавтоматическом режимах.
- Дозирование сырья (реагентов) в реакторы №1, №2 и №3 из двух емкостей с помощью насоса дозатора и счетчика сырья в ручном и полуавтоматическом режимах.
- Наполнение рубашек реакторов №1 и №2 водой в ручном и полуавтоматическом режимах.
- Управление и регулировка оборотов мешалок реакторов №1, №2 и №3 в ручном и полуавтоматическом режимах.
- Барботирование воздухом сырья в реакторах №1, №2, №3 и №4 в ручном и полуавтоматическом режимах.
- Контроль температуры теплоносителя в рубашке и температуры сырья в реакторах №1 и №2 в ручном и полуавтоматическом режимах.
Подбор оборудования АСУ определялся по двум критериям: отечественный производитель и низкая стоимость оборудования. В связи с этим автоматизированная система управления разработана на базе программируемого логического контроллера ОВЕН ПЛК110 и модулей ввода-вывода линейки ОВЕН Мх10, частотных преобразователей и панели оператора. АСУ состоит из пульта управления, исполнительных механизмов и датчиков.
Основное оборудование пульта управления
- программируемый логический контроллер ОВЕН ПЛК110-220.30.Р – 1 шт.;
- модуль дискретного вывода ОВЕН МУ110-224.
16К – 1 шт.;
- модуль аналогового ввода ОВЕН МВ110-224.8А – 1 шт.;
- модуль аналогового вывода ОВЕН МВ110-224.8И – 1 шт.;
- преобразователи частоты – 2 шт.
Краткое описание автоматизированной системы управления
Главное меню панели оператора состоит из восьми разделов: РЕАКТОР 1, РЕАКТОР 2, РЕАКТОР 3, РЕАКТОР 4, МНЕМОСХЕМА, ЖУРНАЛ, ГРАФИКИ, СИСТЕМА. С помощью экранов РЕАКТОР 1…4 оператор производит управление соответствующими реактору технологическими подпроцессами: дозирование воды и сырья, управление мешалкой, барботирование, а также контролирует температуру воды в рубашке и продукта в реакторе. Управление осуществляется в полуатоматическом режиме, перед запуском какого-либо подпроцесса оператор вручную открывает/закрывает ручные задвижки и клапана и запускает необходимый подпроцесс для выбранного реактора.
На экране МНЕМОСХЕМА отображаются состояния исполнительных механизмов (насосов и клапанов), показания датчиков температуры, значения счетчиков воды и сырья. Также на мнемосхеме присутствуют кнопки навигации М, Р1, Р2, Р3, Р4 – для перехода между разделами МЕНЮ, РЕАКТОР 1…4 соответственно и кнопка С – сброс аварии (звука). В правом верхнем углу экрана расположена кнопка РУЧНОЕ УПРАВЛЕНИЕ, по нажатию на которую все исполнительные механизмы переходят в ручной режим управления.
Ручное управление осуществляется нажатием на соответствующий исполнительный механизм. На экране ЖУРНАЛ отображается хронология событий технологического процесса и аварийных ситуаций. На экране ГРАФИКИ – графики температуры воды в рубашке и продукта в реакторах №1 и №2. На экране СИСТЕМА задаются настройки панели оператора: дата, время, пароль доступа.
Оборудование для производства моющих средств
Главная
» Оборудование
» Моющих средств
Оборудование для производства моющих средств компании Россмаш:
Оборудование для производству синтетических моющих средств (паст)
• Реактор
• Резервуар
• Резервуар
• Насос для вязких продуктов
• Гомогенизатор
• Дозатор-полуавтомат
• Трубопроводная обвязка и
запорная арматура
• Пульты управления
Принцип работы:
Ингредиенты загружаются в реактор, оснащенный мешалкой специальной конструкции (обеспечивающей многозонность обработки).
Циркуляция продукта осуществляется насосом для вязких продуктов, обработка продукта — в трехступенчатом роторно-кавитационном
гомогенизаторе-диспергаторе. Далее продукт поступает в промежуточную емкость, где происходит его охлаждение и накопление.
Готовый продукт подается насосом в расходную емкость и далее на фасовку
Оборудование для производства синтетических моющих средств:
Линия производства порошкообразных СМС
Состав линии |
|
|
Смесители и реакторы amixon® для производства моющих средств и металлических мыл
В больших
промышленные предприятия, прецизионные машины выполняют самые разнообразные задачи,
гомогенизаторы периодического действия. Например,
непрерывно работающие большие смесители для гомогенизации трех,
четыре или пять потоков твердых веществ для сильнодействующих моющих средств, безопасных для цвета
моющие средства и мягкие моющие средства.
компоненты дозируются сверху по рецепту и выгружаются
вниз в гомогенизированном виде путем подачи 2, 3 или 4 постоянно работающих
разливочные машины одновременно. Эта вертикаль
Система смешивания перемешивает особенно мягко и может опорожняться до очень высокого уровня.
степень по завершению производственного цикла.
Постоянно работающие грануляторы-смесители производят ровные круглые гранулы из порошкообразных поверхностно-активные вещества путем наращивания грануляции. Частицы – уплотненные и без мелких частиц – затем легко дозировать, наполнять и транспортировать.
Еще
особенность касается окончательного смешивания моющих средств для посудомоечных машин
таблетки/прессованные твердые вещества. Они состоят
различных рецептов, которые часто окрашиваются. Они сигнализируют о расширенных функциях и обозначают
«ополаскиватель», «сухой эффект», «очистка
бустер» или «умягчитель воды» или также «аптечка
таблетка». Высокопроизводительные таблеточные прессы
может собирать таблетки из нескольких компонентов. Однако для этого необходимо смешать порошок и
смачивается особо щадящим прецизионным смесителем, так что порошковые массы должны быть
прессованные обладают специфическими характеристиками текучести и когезии. Такие смесители должны быть самоочищающимися до очень высокой степени.
степень.
Кроме
очистки, мыло также служит смазкой при формовании металлических материалов, для
Например, при глубокой вытяжке для изготовления ванн или кузовов автомобилей, а также при «холодной глубокой вытяжке и
краже» труб. Так наз.
металлические мыла, такие как стеарат магния, стеарат кальция и стеарат натрия
называются стеараты и получают путем этерификации стеариновой кислоты в
наличие оксидов/гидроксидов металлов с расщеплением глицерина. Металлическим мылом называют все виды мыла, содержащие
ни соли натрия, ни соли калия. Как воск,
белые порошки, они нерастворимы в воде. Металлические мыла служат, например, добавкой в
производство лекарств и косметики, производство кормов для животных и в пищу
добавки в качестве «добавок текучести».
В
Европейский патент №. 0330 097, описаны методы, в которых порошкообразные щелочные
металлические мыла могут быть изготовлены на основе стеариновой кислоты. Он также содержит описание того, как справа
температуры и с использованием подходящей системы смешивания металлические мыла приводят к
в виде мелкодисперсных сыпучих порошков светлого цвета. Как только фаза самопроизвольно перейдет из жидкой
до твердого состояния применяется вакуум для остаточной сушки. Другие патентные документы, такие как немецкий патент
приложение DE4019167А1, объясните изготовление порошкообразных щелочно-нейтральных
металлических мыл в виде двухстадийного метода с целью получения
малопыльный, хлопьевидный, сыпучий порошок. Если смотреть
в портфелях крупных производителей стеаратов видно, насколько широка
возможность применения металлических мыл растягивает: эффективны стеарат кальция и стеарат цинка
стабилизаторы в производстве пластмасс и позволяют использовать ПВХ для питья
водопроводные трубы. Пластик ПВХ стабилизирован
против вымывания. Кроме того, стеарат кальция
смазочная добавка для подшипников качения. Стеарат магния с размером частиц от 3 до 15 мкм
имеет очень большую площадь поверхности и служит в минимальных концентрациях в качестве
эффективное средство для улучшения текучести сыпучих материалов всех видов. Однако здесь важно, чтобы процесс смешивания
происходит во всем пространстве, мягко и точно в равной мере. Сильное сдвиговое перемешивание снижает текучесть. Объем производства современных таблеточных прессов
было бы немыслимо без стеарата магния. В различных составах стеараты металлов
цинк, натрий, барий, литий и алюминий оказывают совершенно различное действие: например, как химические поглотители кислоты, как
пропитки, в качестве вспомогательных средств для вулканизации резины, в качестве смазочных материалов в
металлообработке, как гидрофобизаторы в производстве строительных материалов, как
разделительные составы или усилители адгезии, в качестве шлифовальных средств при притирке поверхностей
или в качестве матирующих агентов для красок/лаков, в качестве загустителей/эмульгаторов в кремах,
шампуни и продукты питания или для гидрофобизации абсорбирующих материалов.
цепочка производства металлического мыла очень сложна и имеет очень индивидуально в соответствии с философией процесса, типичной для соответствующей компании. Этап процесса «смешивания порошка» важны в нескольких моментах: первоначально для сбора и подготовки сырьевой смеси, а затем для проведения синтезов. Гидроксиды указанных металлов представлены в виде порошка, как и подходящие масла и смазки. Массу нагревают и гомогенизируют до образования суспензия или расплав с низкой вязкостью, который после были добавлены небольшие количества катализатора или масса была нагрета. Затем реакция продолжается при сильном нагревании. разработка при закрытом корпусе реактора и повышении давления в системе кратно атмосферному давлению. Однажды переход завершен, в реакторе синтеза создается вакуум, чтобы подсушить и охладить массу. В идеале В этом случае образуется мелкий сыпучий белый порошок, который попадает в в максимально возможной степени.
Реактор омыления для производственных предприятий
производитель мыловаренных заводов
— РЕАКТОР ОМЫЛЕНИЯ —
Реактор омыления представляет собой сосуд высокого давления, используемый для быстрого и полного омыления суспензий, состоящих из нейтральных жиров, жирных кислот или смеси оба вещества.
Soaptec — итальянская компания, специализирующаяся на проектировании, строительстве и продаже реакторов омыления для новых заводов, предназначенных для производства кускового мыла, или для установки на уже существующих заводах.
Наша компания предлагает как продажу по каталогу, так и изготовление на заказ.
Наша команда, состоящая из высококвалифицированных техников и инженеров, способна реализовать реакторы для омыления в соответствии с потребностями клиентов, с учетом каждой детали и в полном соответствии с запросами клиентов.
РЕАКТОР ОМЫЛЕНИЯ—
Характеристики и технические характеристики
Благодаря соответствию большинству национальных и международных стандартов, реакторы омыления Soaptec используются на предприятиях по всему миру. В частности, они разработаны в соответствии с UNI и ASME, гл. VIII, отд. 1, хотя по желанию заказчика возможно приведение сосудов под давлением и их внутренних компонентов в соответствие с другими стандартами.
Клиенты также могут запросить сертификацию в соответствии со стандартом ASME, проверив реакторы омыления нашими инспекторами-партнерами.
Кроме того, Soaptec осуществляет строгий контроль производимой продукции для проверки ее общего качества.
Сопротивление и прочность реакторов омыления Soaptec исключительны. Для обеспечения максимальной надежности и долговечности все части изделия, контактирующие с мылом, изготовлены из нержавеющей стали AISI 316. Опорная юбка изготовлена из окрашенной углеродистой стали.
Наконец, наша компания оснащает все реакторы омыления аксессуарами, приборами и клапанами производства ведущих компаний в этой области, таких как Endress + Hauser и Spirax Sarco.
За прошедшие годы компания Soaptec разработала современный реактор омыления, который сочетает в себе отличные характеристики с максимальной простотой использования благодаря двум особенностям: вертикальному развитию и разделение камеры на секции.
В отличие от продуктов конкурентов, наши реакторы имеют вертикальное развитие. Это сводит к минимуму общую занимаемую площадь машины, делая установку более функциональной.
Реакторы омыления Soaptec разделены внутри на четыре секции конструкциями диафрагмы, которые обеспечивают хорошее перемешивание мыла при его прохождении через корпус.
Панель управления реактора омыления оснащена системой Scada (диспетчерское управление и сбор данных), которая позволяет быстро и интуитивно контролировать и регулировать температуру, давление и расход.
В соответствии с требованиями заказчика дозировка сырья измеряется с помощью высокоточных расходомеров, которые управляют дозирующими насосами или дозирующими клапанами через систему ПЛК (программируемый логический контроллер).
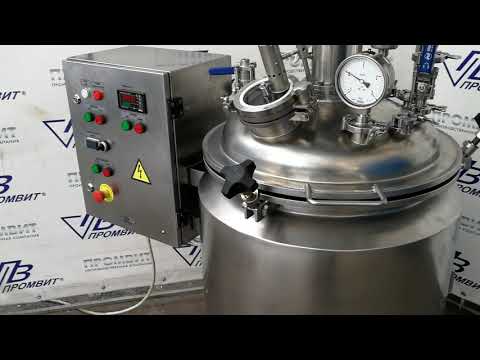