Технология производства газобетона — АлтайСтройМаш
На сегодняшний день технология производства газобетонных блоков интересует не только людей, планирующих построить свой дом, но и предпринимателей из России, Казахстана, Узбекистана и других стран СНГ, которые решили заняться бизнесом на производстве газобетона.
Почему именно газобетон? Во-первых, благодаря высоким показателям прочности и теплоизоляции, спрос на этот материал постоянно растет. Во-вторых, технология изготовления газоблоков очень проста: вам не потребуются особые знания и умения, чтобы стать производителем газобетона.
Предлагаем подробнее ознакомиться с технологией производства газоблоков.
Неавтоклавный газобетон: технология и требования
1. Производственное помещение обязательно должно быть светлым и хорошо вентилируемым. Требуемая температура воздуха в здании – не менее 20С.
2. Особое внимание нужно уделить отсутствию сквозняков в месте подъема газобетонной смеси в формах.
Если температура в цехе меньше 20С, то необходимо добиться температуры от 20С как минимум локально (в местах подъема смеси в формах). В линиях конвейерного типа необходимо разместить камеру предварительного прогрева и установить ее от поста заливки до поста резки. Оптимальная температура в камере предварительного прогрева – 35-40С.
С подробным рецептом газобетона можно ознакомиться здесь.
Технология изготовления газобетона: пошаговая инструкция
Шаг 1. Заливаем воду в газобетоносмеситель (температура воды 45-60С).
Шаг 2. Включаем смеситель и засыпаем цемент.
Шаг 3. Добавляем химические компоненты: каустическую соду (NaOH) и сульфат натрия (Na2SO4) и засыпаем песок.
Шаг 4. Перемешиваем все компоненты в течение 3-5 минут.
Шаг 5. Добавляем приготовленную суспензию алюминиевой пудры или отмеренную массу алюминиевой пасты (в сухом виде) и перемешиваем 20-30 секунд.
Шаг 6. Пока готовится смесь, форму для заливки нужно подкатить к смесителю. К моменту слива смеси формы нужно почистить, собрать и смазать. После получения готовой смеси нужно выключить смеситель и слить раствор.
Шаг 7. После слива раствора аккуратно перемещаем форму в камеру предварительного прогрева.
Шаг 8. После набора необходимой структурной прочности (1-3 часа) выкатываем форму из камеры предварительного прогрева, срезаем горбушку, снимаем борта и разрезаем массив на отдельные блоки.
Шаг 9. Разрезанный массив перемещаем в камеру окончательной выдержки для набора прочности. Температура выдержки – 50-60С.
Шаг 10. После окончательного набора прочности (в течение 6-8 часов) готовые блоки укладываются на поддон, упаковываются стрейч пленкой и отгружаются на склад.
Технология производства газоблоков – это просто!
Как вы уже поняли, технология производства газобетона не сложнее выпечки хлеба или приготовления плова: вам не нужно иметь специальные знания и навыки, чтобы начать производить качественные газобетонные блоки.
Готовы стать производителем газобетонных блоков?
Подобрать оборудование
Процесс производства газобетона — АлтайСтройМаш
Газобетон – один из самых популярных материалов в сегменте малоэтажного строительства последние десятилетия. И многие решают заняться производством газобетона самостоятельно.
Одни хотят производить материал для своих нужд, но с возможным расширением производства. Другие планируют открыть выгодный бизнес по изготовлению газоблоков на продажу строительным бригадам и компаниям.
И тот, и другой подход, однозначно, выгодный. Потребность в газобетоне постоянно растет, так как люди вместо привычного кирпича выбирают более экономичный материал.
Различают два типа газобетона:
Они имеют общий ГОСТ, но различаются способом производства. Для изготовления автоклавного газобетона необходимо очень мощное оборудование, так как процесс затвердевания должна поддерживать температура 200 ᵒС и давление в 14 атм.
Производство неавтоклавного газобетона требует всего 60 ᵒС температуры, а производственная линия стоит в сотни раз дешевле. Поэтому изготовление неавтоклавного газоблока сегодня более выгодно.
Производственные линии
Чтобы открыть свое производство газобетона, нужно приобрести правильное оборудование.
Оно состоит, в основном, из следующих частей:
- дозаторы,
- смеситель,
- резка,
- толкатели,
- транспортеры сырья,
- формы для будущих газоблоков.
Различают 3 типа производственных линий:
На стационарном заводе смеситель с газобетонной смесью по рельсам передвигается от формы к форме. Такое предприятие может производить в день до 60 м3.
Конвейерная линия помогает уменьшить количество ручного труда на производстве. Здесь смеситель находится стационарно на одном месте, а формы на специальном конвейерном транспортере передвигаются к дозатору с газобетонной смесью. Резка газобетонных блоков осуществляется также в механизированном режиме. Производительность до 150 м3 за сутки.
Мини-завод часто устанавливают для собственных нужд в строительстве. Его стоимость минимальна. Это версия стационарного завода с производительностью 15 м3 за день.
Производительность линий всегда можно увеличить, докупая оборудование.
Производство блоков газобетона
Второй «компонент» производства газобетона – правильное сырье. Смесь состоит из воды, наполнителя (мелкозернистый песок, отходы ТЭЦ, доломитовая мука), портландцемента, химических добавок (каустическая сода, сульфат натрия) и газообразователя (алюминиевая пудра).
Также потребуется специальная смазка для газобетонных форм (можно использовать отработанное техническое масло или растительное сырье).
На 1 куб газобетона требуются следующие пропорции сырья:
- горячая вода – 260-300 литров (40-60 градусов),
- песок – 260-300 кг,
- портландцемент – 260-300 кг,
- химические добавки – 1-3 кг,
- алюминиевая пудра – 0,5-0,7 кг.
Вес сырья рассчитывается на специальных весах, а для газообразователя или добавок подойдут обычные торговые электронные весы. Все сырье должно соответствовать ГОСТам оборудования. Состав смеси напрямую влияет на марку и плотность газобетонного блока.
Технология изготовления газобетона
Технология изготовления неавтоклавного газоблока одинакова для всех линий. Разница будет только в техническом исполнении.
Подогретая до 60 градусов вода подается в бетоносмеситель. Чем ниже температура воды, тем дольше время схватывания готовой смеси. Далее включается смеситель, и туда подается цемент. Смесь перемешивается 5-6 минут.
Химические компоненты взвешиваются в отдельной емкости. Далее песок и реагенты засыпают в смеситель. Смесь перемешивается 5-6 минут.
В самом конце добавляют алюминиевую пудру. Через 30 секунд смеситель выключают.
Во время перемешивания сырья к дозатору подаются смазанные формы. Они должны быть хорошо очищены от остатков бетона.
После заполнения форм их перемещают в камеру предварительного нагрева на 1-3 часа. Там под действием температуры раствор разбухает в 1-4 раза, в зависимости от марки газобетона.
С затвердевшего газоблока срезается верхний слой (горбушка). С формы убирают борта. Специальным инструментом смесь режут на отдельные блоки и снова перемещают в камеру итоговой выдержки на 6-10 часов. После этого блоки выгружают на палеты и перемещают на склад.
Компания «АлтайСтройМаш» уже 20 лет специализируется на линиях по производству газобетонных блоков. Клиенты компании успешно работают во многих городах России, Казахстана и Узбекистана.
Оборудование для производства газобетонных блоков: виды
На сегодняшний день применение газобетонных блоков пользуется большим спросом из-за своей легкости, экологичности и теплоизоляции. Технология производства газобетона несложная, но требует четкой последовательности выполнения действий. Материалы и оборудование доступны и легки в монтаже, а, значит, с их установкой справится не только начинающий строитель, но и дачник.
Виды и конструкция
Оборудование для производства газобетона условно делят на группы:
- мобильные установки;
- стационарные;
- мини-установки;
- конвейерные линии.
Применяют два вида изготовления газобетона – автоклавный и неавтоклавный. Применяя естественный способ твердения газобетонного материала, обеспечивается прочность конструкции и увеличивается несущая способность стен. Блоки, изготовленные автоклавным методом, имеют высокие теплоизоляционные характеристики.
Емкость газобетонных установок выполняется в виде прямоугольника или U-образная. Размеры изделий из газобетона исходят из форм, применяемых на этапе заливки. Преимущество заключается в возможности изготовления по индивидуальным размерам.
Вернуться к оглавлениюМобильные
Перед тем как приступить к строительству поместья, заботятся о материалах и вспомогательных установках, которые необходимы для собственного изготовления неавтоклавного газобетона. Установка для изготовления газобетона включает в своем комплекте:
- компрессор;
- электродвигатель;
- набор для подключения агрегата;
- разливочный шланг;
- инструкцию с описанием технологии, с помощью которой производство газобетона не потребует больших усилий.
Применение установки для замеса бетонного раствора позволяет упростить процесс перемешивания и обеспечить высокое качество материалам. Использование компрессорной установки увеличит производительность на 25% и сэкономит расходные материалы. Установка имеет невысокую цену, но, несмотря на это обладает надежностью и простотой в использовании. Для приготовления газобетонных изделий с помощью агрегата, не нужны специальные навыки, можно просто изучить инструкцию или посмотреть обучающий урок на диске, который идет в комплекте. Мобильная установка не занимает много места, поэтому обустраивать специальное помещение для ее хранения не имеет надобности.
Вернуться к оглавлениюСтационарные
Стационарная установка.
При наличии малой строительной компании пригодится стационарная линия изготовления неавтоклавного газобетона. Такие установки автономны и применения ручного труда не требуется. Хранить стационарные лини нужно в специально оборудованных помещениях. Перемещать установки на строительный объект нужно с использованием специально предназначенного оборудования. Стационарные линии включают в свою конструкцию дозаторы, которые автоматически измеряют нужное количество ингредиентов. Установка состоит из бойлера, в котором греется вода до нужной температуры, вибросита и ленточного конвейера для просеивания и передачи песка.
Стационарная линия размещается на площади в пятьсот квадратных метров, для работ требуется два обученных человека. Материал из оборудования выходит высшего качества, это позволяет закрывать глаза на недостаток установки – большие расходы на приобретение агрегата и занимаемая площадь.
Вернуться к оглавлениюМини-установки
Стационарные линии только в уменьшенном виде представляют собой мини-установки. Изготовление блоков проходит по такой же технологии, как и в стационарных установках, только выход готового материала значительно меньше. Качество материалов также находится на высшем уровне и ничем не уступает блокам, изготовленным в стационарных линиях.
Установка состоит их неподвижных форм и перемещающегося смесителя. Мини-линии работают как от стационарной, так и от передвижной электростанции. Также при необходимости возможно перемещение агрегата по строительной площадке. Такая установка подойдет, когда занимаются малым производством продукции.
Вернуться к оглавлениюКонвейерные
Конвейерные установки для производства газобетона.При больших объемах готовой продукции используют конвейерные установки, которые исключают применение ручного труда. Работа автоматизирована, что позволяет экономить на оплате труда работников. Установка конвейерного механизма требует больших площадей и обслуживающего персонала. Конструкция агрегата включает в себя перемещающуюся форму при неподвижном дозаторе и мешалки. За счет объемов выпуска готовой продукции и высокого качества материалов, обеспечивается соответствующая прибыль, которая в скором времени окупает дороговизну оборудования.
Как правильно выбрать оборудование?
Чтобы готовая продукция имела высокие характеристики качества, к ее выбору подходят с большой ответственностью. Важно найти поставщиков с проверенной репутацией и только потом приобретать у них сырье. Выбирая оборудование, учитывают транспортные расходы. Продукцию берут оптом, а, значит, для нее оснащают складские помещения. Изготавливая бетонный раствор, берут во внимание качество таких материалов: известь, алюминиевая паста, песок и цемент. При производстве бетона на строительном участке оснащают поступление воды. Если изделия включают в себя разные наполнители, то запас дополнительных компонентов обеспечивается заранее.
Совершая покупку, требуйте у поставщиков сертификаты к оборудованию. Коробка без повреждений и при необходимости с маркировкой. На каждое оборудование присутствует гарантийный срок, который указывается в гарантийном талоне.
Технология производства
Изготовление бетонных блоков хоть и несложный процесс, однако требует определенной последовательности в работе. При изготовлении с соблюдением требуемых условий выходит качественная продукция, готовая к применению. Технология по производству включает такие этапы:
- Приготовление раствора на основе песка, цемента, извести и воды.
- Подготовка форм, которые применяются в виде прямоугольника.
- Заливка.
- Сушка.
Подготовка форм
Кассетные формы для газобетона.После приготовления бетонного раствора приступают к заливке в специальные формы. Используя разборные емкости, вручную убирают борта прямоугольника, при сплошных формах процесс является автоматизированным. По составу емкости различают:
- металлические;
- пластиковые;
- деревянные.
В подогретые формы до 50 С заливают смесь на половину емкости, так как бетонный раствор поднимается как дрожжевое тесто. При надобности поверхность выравнивают, срезая неровности струной. Оставляют для выдержки на 10 часов. Заполняя емкости повторно новым раствором, их очищают и смазывают.
Приготовление смеси
Бетонный раствор готовят с засыпки ингредиентов и тщательного перемешивания. Для начала в воду всыпают цемент с известью и в течение 5 минут перемешивают, после чего вливают часть воды с алюминиевой стружкой. Важно тщательно перемешать компоненты смеси, чтобы исключить комочки. В результате консистенция напоминает густую сметану.
Вернуться к оглавлениюЗаливка
После приготовления смеси заливают формы газобетонным раствором. Емкости очищают от остатков смеси и подогревают. Раствор вливают, используя шланг. После чего залитую форму выравнивают и застилают теплоизоляционным слоем.
Вернуться к оглавлениюСушка блоков
Залитый раствор в формы подвергается сушке при 190 С. Продолжительность высыхания занимает 12 ч. в автоклаве. Сушка блоков из неавтоклавного газобетона достигает 48 часов.
Упаковка и хранение
Залитые бетонные изделия выдерживают 28 дней в сухом помещении, без сквозняков и перепадов температур. После изготовления блоков, их упаковывают и складируют на поддон. Упаковывают газобетонную продукцию термопленкой и транспортируют на склад. Нельзя грузить и транспортировать газобетонные изделия навалом, разгружать сбрасыванием.
Хранят продукцию в штабелях, устанавливая поддоны, друг на друга. При продолжительном хранении заготовок, защищаем помещения. Хранение газобетонных изделий в зимний период не отличается от другого времени года. Для избежания попадания влаги в результате осадков, газобетонные конструкции накрывают сверху брезентом. Бетону опасны таяния снега в весенний период.
Вернуться к оглавлениюВывод
Выбирая оборудование для изготовления газобетонных изделий, исходят из своих строительных мощностей, денежных средств и планируемого объема выпуска готовой продукции. На цену влияет мощность агрегата и комплектация. Дорогой механизм для приготовления бетонного блока – конвейерная линия. Цена агрегата оправдывает себя только на крупных производственных цехах.
Газобетонный блок – проверенный строительный материал, который применяется не один десяток лет. Он актуален и по сей день за счет своих преимущественных характеристик и легкости производственного процесса.
Технология изготовления автоклавного газобетона | gazobeton.org
Газобетон – это легкий искусственный материал, полученный в результате твердения поризованной смеси, состоящей из гидравлических вяжущих веществ, тонкомолотого кремнеземистого компонента, воды и добавки газообразователя.
Для изготовления изделий из ячеистого бетона можно применять различные сырьевые материалы, но наибольшее распространение получили следующие:
— портландцемент ПЦ 400 – ПЦ 500, без активных минеральных добавок;
— известь негашеная кальциевая с содержанием CaO не менее 70%;
— кварцевый песок с содержанием кварца SiO2 не менее 85%, а глинистых примесей не более 3%;
— газообразователь алюминиевая пудра (паста) с содержанием активного алюминия не менее 80%.
Технологический процесс изготовления автоклавного газобетона включает в себя:
— прием и подготовку сырьевых материалов;
— приготовление газобетонной смеси;
— формование массивов газобетона;
— разрезку массивов на изделия;
— автоклавную обработку;
— упаковку изделий.
Сырьевые материалы могут поступать на завод различными видами транспорта (чаще всего автомобильным и железнодорожным). Хранение вяжущих предусматривается в специальных силосах.
Кварцевый песок выгружаются в приемный бункер, откуда по ленточному конвейеру поступает на помол для приготовления шлама. Помол производится в шаровых мельницах. Далее песчаный шлам транспортируется в шламбассейны, где гомогенизируется с помощью постоянного механического перемешивания.
Негашеная известь на предприятие поступает в тонкомолотом или комовом виде.
В первом случае, тонкомолотая негашеная известь хранится, по аналогии с портландцементом, в силосах и уже готова к употреблению. Во втором случае, если поступает комовая негашеная известь, на предприятии используется технология приготовления известково-песчаного вяжущего путем совместного сухого помола в шаровых мельницах извести и кварцевого песка.
Приготовление газобетонной смеси производится в дозаторно-смесительном отделении. Портландцемент, известь (известково-песчаное вяжущее), песчаный шлам, шлам из отходов резки, вода и алюминиевая суспензия дозируются в соответствии с установленной рецептурой в специальный смеситель, обеспечивающий высокую гомогенность смеси.
Процесс формования включает разгрузку (заливку) смеси из смесителя в форму и вспучивание смеси. Окончание процесса формования наступает после достижения максимальной высоты вспучивания смеси и прекращения активного газовыделения.
После вспучивания формы с газобетонной смесью выдерживаются на постах, желательно при температуре воздуха не менее +15-20oС до приобретения требуемой пластической прочности сырца. Для ускорения процесса набора первоначальной прочности формы со смесью могут выдерживаться в специальных термокамерах при температуре до +70-80oС. Время выдержки при использовании термокамер уменьшается.
После достижения сырцом пластической прочности 0,04-0,12 МПа (в зависимости от технологии) формы подаются на резательный комплекс. Газобетонный массив калибруется со всех сторон и разрезается проволочными струнами в продольном и поперечном направлениях на изделия требуемых размеров. Метод резки газобетонных массивов в полупластическом состоянии с помощью тонких проволочных струн хорошо зарекомендовал себя и на современных резательных машинах позволяет получать изделия точных размеров с отклонениями от номинальных до ±1,0-1,5 мм. Такая точность позволяет осуществлять кладку блоков на тонкослойную клеевую смесь вместо традиционного цементно-песчаного раствора.
Разрезанные на изделия массивы устанавливаются на автоклавные тележки и загружаются в автоклав. После полной загрузки автоклава начинается тепловлажностная обработка по определенному режиму, включающему плавный набор температуры и давления, изотермическую выдержку при температуре около 190°С и давлении 12 атм, плавный спуск давления и подготовка изделий к выгрузке.
Из компонентов CaO и SiO2, вяжущих материалов и кварцевого песка, а также воды, в условиях автоклавной обработки (высокое давление и температура) происходит образование новых минералов – низкоосновных гидросиликатов кальция, что предопределяет более высокие физико-механические характеристики автоклавного газобетона в сравнении с неавтоклавными ячеистыми бетонами (пенобетон, газобетон).
После завершения цикла тепловлажностной обработки изделия подаются на участок деления и упаковки, а затем на склад готовой продукции.
Основные моменты технологии производства блоков из автоклавного газобетона показаны на видео одного из участников ассоциации ВААГ:
Технология производства газобетона
Благодаря автоклавированию, непосредственно после его окончания газобетон имеет соответствующую прочность, долговечность и морозостойкость. Автоклавирование исключает возможность усадки, а также обеспечивает долговечность газобетона.
Газобетон хорошо подлежит обработке простейшими инструментами: пилится, сверлится, строгается. В него легко забиваются гвозди, скобы. Со временем газобетон становится твёрже. Дома из газобетона сегодня очень популярны в России. К тому же, проекты домов из газобетона и цена на него, доступны всем.
Автоклавная обработка газобетона производится не только для того, чтобы ускорить процесс твердения смеси. Основной смысл состоит в том, что в автоклаве при температуре +180 °С и давлении до 14 бар в газобетоне образуется новый минерал — доберморит. Благодаря этому повышается прочность материала и, что особенно важно, в несколько раз уменьшается усадка. За счет своих характеристик автоклавный бетон имеет гораздо больше способов применения. Он может использоваться, например, в армированных конструкциях — перемычках, панелях, и др. Ячеистый бетон автоклавного твердения имеет пониженную трещиностойкость и морозостойкость. Автоклавная обработка позволяет в более короткие сроки получать изделия с достаточно высокой прочностью при пониженном расходе вяжущего. У автоклавной обработки имеются и недостатки: дорогостоящее оборудование, специфика его эксплуатации, требующая высококвалифицированного обслуживающего персонала, высокая металлоемкость автоклавов, низкий коэффициент использования внутреннего объема автоклава. Мелкосерийное производство при автоклавном способе оказывается экономически невыгодным.
Автоклавный газобетон производится на крупных заводах и на стройплощадку попадает в виде готовых блоков. Изготовление этого материала на малом производстве или изготовление газобетона автоклавного своими руками — невозможны.
Основными компонентами этого материала являются цемент, кварцевый песок (либо зола унос), газообразователи, также возможно добавление гипса и извести. В качестве специализированных газообразователей используются алюминиевые пасты и пудры. Сырьё смешивается с водой заливается в форму и происходит реакция воды и газообразователя, приводящая к выделению водорода, который и образует поры, смесь поднимается как тесто. После набора пластической прочности, массив разрезается на блоки, плиты и панели. Ипользование высокотехнологичного резательного оборудования позволяет разрезать полученный массив с высокой точностью на блоки и плиты.
После этого изделия подвергаются закалке паром в автоклаве, где они приобретают необходимую жёсткость, либо высушиваются в условиях электроподогрева.
Процесс производства ячеистого бетона напоминает выпекание хлеба: в смесителе замешивается вода, цемент, молотый кварцевый песок, тщательно размельченная известь и гипс (не на всех производствах), добавляется газообразователь. В теплой влажной камере смесь поднимается.
Процесс газообразования происходит вследствие химической реакции между гидратом окиси кальция и алюминием; выделяющийся при этом водород вызывает вспучивание раствора, который, затвердевая, сохраняет пористую структуру.
При определении состава газобетона необходимо обеспечить заданную объемную массу и его наибольшую прочность при минимальных расходах порообразователя и вяжущего вещества. При этом структура газобетона должна характеризоваться равномерно распределенными мелкими порами правильной шаровидной формы.
Объемная масса газобетона и его пористость зависят главным образом от расхода порообразователя и степени использования его порообразующей способности. Некоторое влияние на них оказывают температура смеси и количество воды, принятое для затворения смеси, т. е. водотвердое отношение В/Т. Увеличение В/Т повышает текучесть смеси, а следовательно улучшает условия образования пористой структуры, если обеспечивается достаточная пластичная прочность смеси к концу процесса газообразования.
Прочность газобетона зависит также от характера его пористости, размеров и структуры пор и прочности межпоровых оболочек. С увеличением В/Т до оптимального значения, обеспечивающего наилучшие условия формирования структуры смеси, прочность газобетона повышается. Прочность оболочек, в свою очередь, зависит от оптимального соотношения основного вяжущего и кремнеземистого компонента, В/Т, а также условий тепловлажностной обработки. Из этого следует, что применение смесей с минимальным значением В/Т при условии образования высококачественной структуры (например виброспучиванием) позволяет получить газобетон более высокой прочности.
Для изготовления газобетона применяют портландцемент марок 300, 400, 500, удовлетворяющий требованиям ГОСТ 970-61. Производство газобетона предъявляет специальные требования к портландцементу в отношении щелочности цементного теста – рН теста не должна быть ниже 12. Щелочность цемента определяется количеством свободной СаО и суммой Na2О и K2О. По данным работы газобетонных заводов, содержание щелочей (Nа2О, К20) в 1 л раствора цемента не должно быть менее 75 мг. В случае недостаточной щелочности раствора в газобетонную массу следует дополнительно вводить известь или щелочь в виде каустической соды (NаОН).
При применении в качестве основного вяжущего извести особое внимание уделяют значительному количеству активных окиси кальция (СаО) и магния (МgО). Общая активность извести не должна быть менее 75%, количество МgО — не более 1,5%. В производстве можно применять известь. Известь должна быть равномерно обожженной.
Введение извести как добавки к цементу сокращает расход цемента и одновременно увеличивает щелочность раствора, обеспечивая энергичное протекание реакции газообразования:
3 Са(ОН)2 + 2 Аl + 6 Н2О 3 СаО·Аl2О3·6Н2О + 3 Н2
В качестве кремнеземистого компонента в производстве газобетона применяют речной или горный кварцевый песок, золу-унос тепловых электростанций, маршалит и другие материалы. Кварцевый песок для изготовления газобетона и газосиликата должен быть чистым, без примесей глины и органических веществ, с содержанием SiO2 не менее 80%. Присутствие глины замедляет твердение газобетона и уменьшает его прочность. Органические примеси вредно сказываются на протекании реакции газовыделения; вспучивание газобетона при наличии органических примесей ухудшается. Зола-унос может применяться в производстве газозолобетона при содержании SiО2 более 55%. Зола-унос должна иметь незначительное количество сернистых соединений, несгоревших частиц угля и карбонатов кальция.
Важнейшей технологической особенностью получения высококачественных газобетонных изделий максимальной пористости и достаточной прочности является создание оптимальных условий для двух одновременно протекающих процессов газовыделения и газоудержания. Необходимо обеспечить соответствие между скоростью реакции газовыделения и скоростью нарастания структурной вязкости цементного теста или раствора. При этом выделение газа
методы производства и технологические нюансы
В решении целого комплекса строительных задач газобетон, универсальный и современный, станет надежным подспорьем при возведении зданий самых разнообразных размеров, конструкций и назначения – как одноэтажных загородных коттеджей, так и небоскребов, многоэтажных торговых и развлекательных комплексов на каркасной основе.
Среди множества преимуществ газобетона – экологичность, долговечность применения и огнестойкость, легкость в обработке, а также отличные теплоизоляционные свойства. Последняя характеристика весомее, если учитывать низкий удельный вес материала. При этом умеренная стоимость делает газобетонные блоки доступными для всех представителей среднего класса.
Даже человек без строительного образования благодаря несложной технологии применения этого материала с легкостью построит коттедж своей мечты, или любой другой малоэтажный дом.
Технология, которой пользуется любой производитель газобетона, достаточно проста. Газобетон входит в семейство ячеистых бетонов, которое также включает в себя пенобетоны и легкие аэрированные бетоны. Как видно из названия, основная черта отличия этих материалов – ячеистая структура. Малый объемный вес обеспечивается за счет пузырьков газа, которые могут занимать до 85% объема блока. Основными компонентами для изготовления газобетона являются известь, вода, кварцевый песок и, конечно же, цемент. При этом пропорции составляющих и тщательное их дозирование рассчитывается и контролируется с помощью компьютера. Таким образом, газобетономеситель готовит однородную смесь игридиентов на протяжении 4-5 часов. Для того, чтобы в материале появились пузырьки газа, в хорошо вымешанное «тесто» заготовки добавляют водную суспензию измельченного алюминия. Последний, вступая в реакцию с известью, приводит к образованию водорода, который, в свою очередь, является истоком образования большого количества мелких (0,5-2 мм) пор, которые пронизывают материал по всему объему.
Далее по технологии в специальных емкостях происходит так называемое «вспучивание», где будущий газобетон подвергают вибрационным нагрузкам, что приводит к лучшему затвердению и ускорению химических реакций. Газобетон проходит и стадию предварительного твердения, которая сопровождается снятием неровной верхушки, а затем и разрезанием заготовки на ровные блоки. Затем куски газобетона обрабатывают в автоклаве, калибруют фрезерной машиной и отделывают фасадные поверхности.
Применение компьютерного моделирования и прочих современных технологий делает газобетонные блоки однородными и одинаковыми по размеру, как в горизонтальном, так и в вертикальном направлении.
Автоклавная сушка газобетона
Автоклавирование направлено на улучшение технических свойств газобетонной смеси. Газобетонный блок, сформированный и разрезанный, помещают в камеры автоклавирования, где они на протяжении 12 часов подвергаются воздействию водяного пара температурой 190°С. При этом пар нагнетается до повышения уровня давления вплоть до 12 кг/см² и газобетонный блок надежно твердеет, становится более прочным, ограничивает усадку здания, к тому же, более однородным, а следовательно – может быть применен в строительстве в качестве как основного структурного материала, так и с целью звуко- и теплоизоляции. Низкий коэффициент теплопроводности (0,09-0,18 Вт/(м•°С) дает возможность применять газобетонные блоки автоклавного твердения в наших климатических условиях, и даже возводить однорядные стены с толщиной блока всего 375 – 400мм.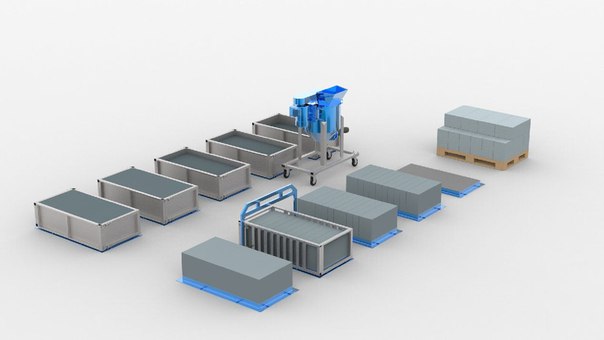
Безавтоклавные технологии сушки газобетонных блоков
Существует и безавтоклавные технологии сушки газобетонных блоков. Для них не требуется какого-то высокотехнологичного оборудования, однако газобетонные блоки изготовленные без участия автоклава характеризуются меньшей прочностью. Если автоклавный газобетон дает усадку 0,3-0,5 мм на метр высоты, то для газобетонных блоков неавтоклавного происхождения эти показатели приближаются к 3-5 мм/м. Выигрывает автоклавный газобетон и по прочности, превышая соответствующие показатели для неавтоклавного в 2-4 раза. Любой крупный производитель газобетона, такой как всемирно известные Ytong или Hebel, предпочитает изготавливать именно автоклавный газобетон.В зависимости от целей использования той, или иной марки газобетон разделяется на три класса:
Теплоизоляционный обладает плотностью в сухом состоянии 300-500 кг/м³ и общей пористотью более 75%. Конструктивно-теплоизоляционный имеет соответствующие показатели на уровне 500-900 кг/м³, то есть, является более тяжелым, в то время как пористость его значительно снижена – от 55 до 75%.
На какие свойства газобетона имеет смысл обратить внимание:
В первую очередь, это его прочность и долгий срок службы. В коттеджном строительстве особой популярностью пользуется пенобетон с небольшой удельной массой 400-500 кг/м³ и высокой прочностью 28-40 кгс/ м². Поэтому газобетон легкоприменим в малоэтажном строительстве бескаркасных зданий высотой до 14 м, а также для создания перегородок.При этом газобетон характеризуется довольно высоким сроком службы, приравнённым к сроку службы кирпича. И хотя производители предоставляют гарантию на 80 лет, уже сегодня становится ясно, что строения из газобетонных блоков могут служить намного дольше, ведь стены подобных зданий восьмидесятилетней давности не дают трещин и характеризуются высокой стойкостью материала.
Качественная теплоизоляция также является одним из достоинств газобетонных блоков, ведь заключенный в порах материала воздух великолепно ограничивают теплообмен.

Объёмный вес газобетона обратно пропорционален его плотности. Именно правильное сочетание этих параметров на уровне объемного веса газобетона до 400-600 кг/м³, обеспечит успешную постройку теплого и прочного дома. Этому будут способствовать также гладкая поверхность и точно контролируемые размеры и формы газобетонных блоков. При постройке из газобетона можно использовать технологию тонкошовной кладки, которая исключает образование «мостиков холода».
Еще одним преимуществом низкой теплопроводности является соответствующая низкая тепловая инертность этого материала. Таким образом, в отличие от кирпичных домов, дома из газобетона прогреваются намного быстрее.
Не последний вопрос при выборе материала для постройки – ценовая политика.
Более лёгкий, газобетон существенно снижает нагрузку на фундамент, а используемая при его укладке технология тонких швов способствует снижению затрат на кладочный раствор почти в шесть раз.

Несмотря на крупные габариты, газобетонный блок не требует дополнительной подъемной техники, так как обладает небольшим удельным весом. Суммируя все вышесказанное, применение газобетона для возведения зданий позволяет увеличить скорость возведения в четыре раза, пропорционально снижая и затраты на строительство.
Безопасность для жильцов
Надёжный производитель газобетонных блоков стремиться использовать только натуральные, экологически нейтральные компоненты. Вследствие этого хороший материал инертен и безопасен для здоровья людей и окружающей среды, так как не выделяет абсолютно никаких веществ. Газобетон относится к «дышашим» материалам и по своей пористости сходен с таким популярным натуральным строительным материалом, как дерево. Однако, в отличие от построек из дерева, постройки из газобетонных блоков характеризуются и легкостью монтажа, и долговечностью, не усыхают, держат форму, не реагируют на перепады температуры и воздействие повышенной влажности.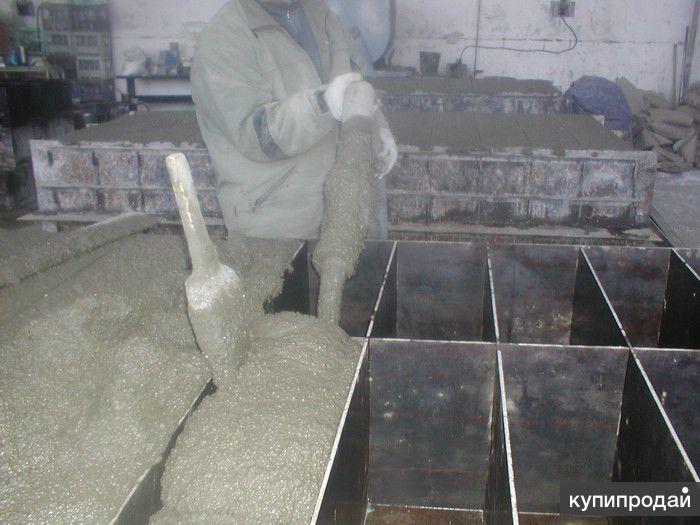
Низкая теплопроводность имеет и еще одно, на этот раз действительно приятное следствие. Стены из газобетона всегда на ощупь теплые, а также выводят лишнюю влагу, препятствуя гниению и появлению плесени на стенах.
Еще один бонус при применении газобетона – его огнестойкость. Он способен выдерживать воздействие огня на протяжении 3-7 часов, при этом не горя и не поддерживая горение, защищая в свою очередь от огня и металлические внутренние конструкции.
Газобетонные блоки обладают также и завидной морозостойкостью, что немаловажно для нашего региона. Испытания, заключавшиеся в восьмичасовом насыщении газобетонного блока водой, а затем в восьмичасовом же заключении в морозильной камере, показали, что он способен при полном водном насыщении всех пор выдерживать полный цикл заморозки и оттаивания.

Разнообразные размеры (ширина может колебаться от 50 до 500 мм) и особенности конструкции газобетонных блоков разных марок говорят о высокой технологичности этого материала. При этом, для средней полосы России оптимальная ширина блока газобетона составляет 375-400 мм, что позволяет строить газобетонные стены в один слой. При этом, используя газобетон, вы можете забыть про утеплители.
Удобен газобетон и в обработке, легко поддаваясь воздействию как ручного, так и электрического инструмента, сверлению, раскалыванию и нарезанию обычной, или электроприводной пилой. Электродрель со спецнасадкой решит вопрос прокладывания штрома под арматуру и проводку, как и создание отверстий под розетки и выключатели. Скруглить блок можно пользуясь шлиф-машиной, потому блоки из газобетона используются и в качестве отделочного материала с хорошими декоративными возможностями: для изготовления колонн, подставок и тумб, а также украшений, имитирующих лепнину.
Перед многими желающими построить свой дом встает выбор между газобетоном и газосиликатом. В чем же разница? Действительно, эти материалы схожи по технологиям изготовления, однако имеется одно существенное отличие, а именно – состав наполнителя. В процессе создания газобетона наполнителем выступает цемент, в то время как при изготовлении газосиликатных блоков в качестве наполнителя идет смесь из молотого кварцевого песка (62%) и извести (24%). Газообразование же всегда идет за счет добавление алюминиевой массы и ее реакции с известью. При этом, обязательным этапом для создания газосиликатов является последующее автоклавирование, в то время как газобетон может сушитбся и без автоклавной обработки. Резюмируя можно сказать, что газосиликат по твердости и теплопроводным свойствам максимально приближен к автоклавному газобетону
Наиболее предпочтительные для покупателя в нашем регионе компании, проверенные и на мировом рынке. Например, всемирно известная компания Ytong стала первым в мире производителем газобетонных блоков автоклавного типа, сразу после изобретения технологии автоклавных ячеистых бетонов в 1924 году. Еще один известный производитель газобетона, торговая марка Hebel, названная так в честь изобретателя, который предложил новейшую технологию производства высокоточных геометрически блоков. Hebel это синоним немецкого качества поддержанного долголетними традициями надежности.
Сегодня обе компании находятся в собственности транснациональная компания Xella – крупный промышленный производитель стройматериалов. Следствием фактического слияния этих двух компаний стало изготовление газобетонов обеих марок по одной технологии и с использованием одного и того же оборудования, которое является представителем традиций качества обеих корпораций. Xella это прекрасное качество и геометрия газобетона по умеренной цене.
| |||||
|
Строительная система из газобетона | Aircrete Europe
Жилой
Строительная система Aircrete имеет уникальное предложение для жилых помещений, при этом при строительстве до 4 этажей она может обеспечить решение на основе панелей, исключая все другие конструкционные строительные материалы, такие как традиционные бетонные колонны.
Для высотных зданий использование перегородок и облицовочных панелей позволяет ускорить реализацию строительного проекта благодаря легкому весу и точности материала.
Кроме того, использование AAC позволяет получить в целом более легкую конструкцию, что приводит к дополнительной экономии (стальной или бетонной) конструкции здания и меньшим требованиям к фундаменту. Облицовочные панели из AAC могут также идеально дополнять существующие строительные конструкции, такие как стальное или деревянное каркасное здание, при этом панели из AAC используются в качестве негорючих изоляционных панелей, обеспечивающих комфорт и безопасность жилой среды.
Промышленное и коммерческое
Для промышленного и коммерческого применения несущие панели AAC могут служить в качестве единой конструкции стены, устраняя необходимость в нескольких слоях различных строительных и изоляционных материалов. Стеновые панели можно устанавливать горизонтально или вертикально и прикреплять к существующим деревянным, стальным или бетонным колоннам.
Стены, полы и крыши на основе AACявляются лучшим выбором строительных материалов для многих промышленных складов и коммерческих торговых центров, что обусловлено ужесточением требований противопожарных нормативов и общим сокращением сроков реализации строительного проекта.
Кроме того, все элементы в системе здания Aircrete обладают превосходными тепло- и звукоизоляционными свойствами. Эти качества обеспечивают выдающиеся преимущества строителям, девелоперам и проектировщикам для любого проекта, от малоэтажных промышленных и коммерческих застроек до высотных сооружений.
Рынок автоклавного газобетона | Размер, доля | Рост, тенденции | Отраслевой анализ | Прогноз
Это исследование рынка определяет H + H, JK Lakshmi Cement, UAL Industries, UltraTech Cement и Xella как ведущих игроков на мировом рынке автоклавного пенобетона (AAC).Комплексный анализ этого рынка также представлен по продуктам (блоки, панели и др.), По конечным пользователям (нежилые и жилые) и по географическим регионам (Азиатско-Тихоокеанский регион, Европа, MEA, Северная Америка и Южная Америка).
Обзор мирового рынка автоклавного ячеистого бетона (AAC)
Согласно отчету об исследовании рынка aac от Technavio, в течение прогнозируемого периода среднегодовой темп роста рынка составит более 7%. Растущее использование AAC в различных формах будет определять перспективы роста рынка до конца 2021 года.AAC также известен как автоклавный бетон, автоклавный легкий бетон (ALC), автоклавный ячеистый бетон (ACC), ячеистый бетон и пористый бетон. Кирпич AAC считается экологически чистым и устойчивым строительным материалом, потому что в нем используется экологически чистый производственный процесс. AAC помогает сократить более 45% парникового излучения, почти 30% экологических отходов и более 50% суммарной энергии на поверхности кирпича. Блоки AAC доступны в нестандартных размерах и в 3-4 раза легче, чем традиционные блоки.Эти материалы требуют меньшего количества стыков, что снижает общую стоимость строительства на 3–5%. В ближайшие годы будет по-прежнему наблюдаться высокий спрос на ААК, поскольку они требуют меньшего количества цемента и стали.
В течение 2016 года на рынок AAC в Европе приходилась основная доля рынка из-за присутствия многих производителей блоков AAC в таких странах, как Польша, Великобритания и Германия. Улучшение свойств AAC, таких как превосходная устойчивость к огню, ветру, солнечным повреждениям и вредителям, будет стимулировать внедрение AAC в течение прогнозируемого периода.Кроме того, рост строительного рынка в Европе также будет стимулировать спрос на эти материалы в этом регионе.
Что у вас на вынос?
Отчет об отраслевом исследовании компанииTechnavio под названием Глобальный рынок автоклавного ячеистого бетона (AAC) поможет вам —
- Выявить скрытые возможности и поисковые решения на рынке автоклавного газобетона (AAC)
- Определите ваших основных конкурентов и что ими движет?
- Помогите вам составить комплексный маркетинговый план, включая все варианты и комбинации
Следующий шаг: Скачать БЕСПЛАТНЫЙ образец отчета | Свяжитесь с нами
Конкурентная среда и ключевые поставщики
На рынке AAC присутствует множество поставщиков, и на нем доминируют мировые поставщики.На рынке наблюдается приток отечественных поставщиков из-за роста индустриализации в развивающихся регионах. Чтобы оставаться конкурентоспособными на рынке, крупные игроки переходят на стратегии M&A. Мелкие и средние поставщики предлагают инновационные возможности, в то время как известные игроки сосредотачиваются на том, чтобы прочно закрепиться на рынке. Эти поставщики все больше конкурируют друг с другом на основе таких факторов, как цена, качество и производительность, инновации и клиентоцентризм.
Ключевые поставщики на этом рынке —
- H + H
- JK Lakshmi Cement
- UAL Industries
- UltraTech Cement
- Кселла
Другие известные поставщики на рынке включают Aircrete Group, AKG Gazbeton, AERCON AAC, Broco, Buildmate Projects, Brickwell, Hebel, Kansal Group, Laston Italiana, RPP Group и SOLBET.
Сегментация по продуктам и анализ рынка AAC
БлокиAAC — это сборные строительные материалы, легкие по весу и обеспечивающие изоляцию, структуру и устойчивость к огню и плесени.Применение блоков AAC снижает массу конструкции, поскольку они легкие по весу, и снижает воздействие землетрясения на здание. Это стимулирует спрос на блоки AAC по сравнению с панелями AAC, и, согласно отчету об отраслевом исследовании, на этот сегмент будет приходиться максимальная доля рынка AAC в течение расчетного периода.
Сегментация по конечным пользователям и анализ рынка AAC
- Нежилое
- Жилой
Рынок AAC для нежилых пользователей составлял основную долю рынка в 2016 году.Правительства как развивающихся, так и развитых стран все больше внимания уделяют развитию общественной инфраструктуры, и это повысит спрос на кондиционеры в этом сегменте. Сегмент рынка будет продолжать доминировать в предстоящие годы, поскольку кондиционеры используются для строительства коммерческих зданий и инфраструктуры, таких как офисные помещения, магазины, рестораны, отели, промышленные здания, школы и больницы.
Ключевые вопросы, на которые даны ответы в отчете, включают
- Каким будет размер рынка и темпы роста в 2021 году?
- Каковы ключевые факторы развития мирового рынка автоклавного ячеистого бетона (AAC)?
- Какие основные рыночные тенденции влияют на рост мирового рынка автоклавного газобетона (AAC)? AAC Каковы проблемы для роста рынка?
- Кто являются основными поставщиками на мировом рынке автоклавного ячеистого бетона (AAC)?
- С какими рыночными возможностями и угрозами сталкиваются поставщики на мировом рынке автоклавного пенобетона (AAC)?
- Какие факторы тенденции влияют на рыночные доли Азиатско-Тихоокеанского региона, Европы, Ближнего Востока и Африки, Северной и Южной Америки?
- Каковы основные результаты анализа пяти сил на мировом рынке автоклавного ячеистого бетона (AAC)?
Technavio также предлагает настройку отчетов на основе конкретных требований клиента.
Автоклавный аэрированный концентрат (АКК) — это легкий сборный пенобетонный строительный материал, который одновременно обеспечивает структуру, изоляцию и огнестойкость. Выявив основные тенденции в предпочтениях потребителей, ключевых игроках рынка, потенциале роста и проблемах, отраслевые эксперты исследовательской фирмы Technavio предоставляют подробный анализ отчетов об отраслевых исследованиях по различным аспектам сектора стекла и керамики, который является неотъемлемой частью часть химической промышленности.
Чтобы определить перспективы роста отрасли, аналитики Technavio применяют комбинацию количественных и качественных методов сбора данных, а также учитывают такие факторы, как размер рынка и спрос на различные продукты в разных географических регионах. В этом предстоящем отчете по рынку AAC также рассматривается рост аналогичных рынков, таких как рынок плоского стекла для строительной отрасли и рынок антибактериального стекла, которые, как ожидается, будут расти со среднегодовым темпом роста более 6% и почти 7% до 2021 года.По мнению наших экспертов по исследованию рынка, ожидается, что экспоненциальный рост спроса на ACC в странах Азиатско-Тихоокеанского региона, таких как Япония, Китай, Индия и Южная Корея, будет способствовать росту рынка ACC в ближайшие годы.
В предстоящем отчете об отраслевом исследовании рынка AAC также определены основные движущие силы, новые тенденции и надвигающиеся проблемы, с которыми в настоящее время сталкивается сектор стекла и керамики. Он также дает представление об изменяющейся конкурентной среде, чтобы дать вам целостную картину будущего направления химической промышленности.