Этапы производства поликарбоната — Все о поликарбонате
В качестве инженерного пластика поликарбонат приобрел большую известность и популярность. Материал является линейным полиэфиром. В промышленности используется только ароматическая группа данного вещества. На его основе создаются композиции, относящиеся к специальным полимерам. В промышленности технология производства поликарбоната разделена на два основных этапа: синтез мелкозернистого полуфабриката и создание из него листового строительного материала. Обычно их осуществляют на разных предприятиях.

Схема листа сотового поликарбоната.
Изготовление исходного сырья
До недавнего времени промышленное изготовление гранул для дальнейшей переработки производилось только методом межфазной поликонденсации. Процесс полимеризации при этом происходит на границе раздела жидкости и газа, то есть двух фаз. Для производства используются двухатомный фенол и угольная кислота (фосген). В реакции также участвуют определенный органический растворитель и пиридин, служащий и катализатором, и акцептором.
К достоинствам данной методики, по которой и сейчас производится свыше 80% полимера, относится невысокая, до 25°С, температура реакции и сравнительно небольшие затраты энергии. Кроме того, она позволяет получать разнообразные виды поликарбоната, в том числе высокой молекулярной массы. Основным недостатком является присутствие в реакции фосгена, обладающего высокой токсичностью. Полученный полимер нуждается в очистке от побочных продуктов и от остатков реагентов. Как следствие, на его промывку уходит много воды. Это, в свою очередь, приводит к большому объему сточных вод. Осаждение полученной массы производится специальным реагентом, к примеру, ацетоном.
Схема монтажа сотового поликарбоната.
Более новая технология производства методом переэтерификации позволяет осуществлять реакцию в расплаве при температуре от 250 до 300 °С. Реакция основана на химическом взаимодействии двух основных ингредиентов: дифенилолпропана и диметилового эфира угольной кислоты. Это позволяет сэкономить на растворителе и обойтись без токсичного фосгена. Недостаток же заключается в том, что выделяется побочный продукт, анизол, мировая потребность в котором ничтожно мала. Из-за этого его просто приходится сжигать. Кроме того, при такой методике увеличиваются расход энергии и затраты на особо чистые реагенты. Наконец, данный способ пока не дает возможности создавать высокомолекулярный поликарбонат.
При необходимости в выделенную и промытую полимерную массу добавляют какой-нибудь краситель. Затем ее сушат, еще теплой пропускают через экструдер для получения крупинок или прутьев, а потом фасуют в многослойные мешки.
Химические реакции, в результате которых получается поликарбонат, являются необратимыми, а синтезированная продукция — нетоксичной.
Поскольку приобрести очень дорогую лицензию на производство гранул могут позволить себе лишь немногие фирмы, большинство предприятий для дальнейшей переработки предпочитает покупать готовое сырье.
Вернуться к оглавлению
Очистка, плавление и экструзия
Схема крепления листов поликарбоната к металлическому каркасу.
На предприятии гранулы из мешков перегружают в специальные бункеры, которые называются силосами. Силос имеет дно в виде воронки, через которую происходит отбор сырья. Гранулы поликарбоната попадают на пневмотранспортер, который доставляет их в устройство для очистки — циклон. Циклон работает по принципу центрифуги, отбрасывая в сторону частички пыли. Затем необходимое количество сырья отмеряют в автоматическом дозаторе, после чего гранулы загружаются в камеру для плавления.
Чтобы улучшить качество материала и придать ему необходимые свойства, в плавильную камеру добавляют определенные присадки. Они смогут предотвратить конденсацию влаги на поверхности листа, наделить его свойством отталкивания воды и грязи. Добавление металлической крошки улучшает отражение инфракрасного излучения и позволяет материалу лучше сохранять тепло. Благодаря ей поликарбонат приобретает модный оттенок «металлика». Смесь постоянно перемешивается и постепенно нагревается до 250-290 °С. Газы, которые при этом выделяются, отводят наружу.
Поскольку даже при такой высокой температуре расплав имеет очень вязкую консистенцию, ровный материал в виде ленты из него удобнее всего формировать путем экструзии, то есть продавливания через особую матрицу — фильеру. Одновременно с этим лента может покрываться тонкой пленкой, защищающей от разрушительного воздействия ультрафиолетового излучения. На завершающем этапе с помощью пресса ленте придают необходимую толщину. При этом происходит окончательное сглаживание неровностей. После этого остается только разрезать ленту на листы необходимого размера.
Экструдер используется для производства поликарбоната различной структуры: как монолитного, так и сотового. Матрица определяет строение получаемого листа.
Вернуться к оглавлению
Технология производства методом литья
Из пластика можно изготавливать не только листовой материал, но и отливать готовые изделия или отдельные детали. Их формируют при помощи литья под давлением, а сосуды — методом выдувного литья. Чтобы создать пленку толщиной всего 125-640 мкм, используется раствор поликарбоната в метиленхлориде. Для этого берут пластик с высокой молекулярной массой.
Перед началом процесса литья под давлением исходный материал высушивают в бункерных сушилках при температуре 110-120 °С. Преимущество такой обработки состоит в отсутствии повторного впитывания влаги при хранении или транспортировке. Затем материал поступает в нагревательный цилиндр, где его доводят путем нагрева до вязко-текучего состояния.
Особенность производства литых деталей заключается в относительно невысоком, до 150-160°С, повышении температуры расплава и разогревании формы до 80-100°С. Процесс осуществляется на литьевом автомате. Он разделен на отдельные технологические этапы. Сначала смыкается форма для заливки, потом осуществляется впрыскивание разогретого материала. В форме происходит его уплотнение под давлением 70-150 МПа. Затем поликарбонат выдерживается в форме еще некоторое время, необходимое для остывания. Наконец, форма размыкается, а готовая деталь вынимается.
Следует заметить, что каждому способу производства поликарбонатной продукции должны соответствовать определенные марки пластика — литьевые, экструзионные, экструзионно-литьевые, а также для выдувного литья. В некоторых случаях производится изменение характеристик полимера путем армирования стеклянными или графитовыми волокнами.
polikarbonatstroy.ru
Сотовый поликарбонат – сайт производителя
Уникальные потребительские свойства поликарбоната PLASTILUX GROUP
- Тройная защита от ультрафиолета и упрочняющие модификаторы вязкости, используемые при изготовлении премиального поликарбоната ROYALPLAST, обеспечивают защиту от града до 2-х раз выше и гарантируют срок службы панелей 20 лет.
- Противопожарная антипиреновая добавка в составе промышленного поликарбоната POLYNEX придаёт материалу самую высокую степень пожарной безопасности Г1 и обеспечивает устойчивость к воздействию огня до 2,5 раз выше.
- Армирующее стекловолокно в декоративных листах КОЛОТЫЙ-ЛЁД до 2-х раз повышает устойчивость к ударным нагрузкам и на 4-5 лет продлевает срок эксплуатации панелей.
- Полые стеклянные микросферы внутри облицовочного поликарбоната SUNNEX на 25% улучшают его теплосберегающие свойства, делая материал незаменимым для любых дачных построек.
- Антиконденсатное покрытие тепличного поликарбоната GREENHOUSE-nano в 2 раза лучше защищает растения от ожогов прямыми солнечными лучами, а специальная селективная добавка увеличивает урожайность овощных культур до 48%.
- Биоцидный активный компонент в составе гигиеничного поликарбоната ULTRAMARIN в 3 раза повышает устойчивость материала к грибкам и плесени, а лёгкость и эластичность листов гарантируют снижение нагрузки на опорные конструкции до 35%.
- Уникальный суперконцентрат красителя, используемый при производстве рекламного поликарбоната БЕЛЫЙ-МАТОВЫЙ, делает цвет панелей снежно-белым и обеспечивает равномерное рассеивание 99,9% света с расстояния всего 2 сантиметра.
Виды и характеристики поликарбоната PLASTILUX GROUP
Основным видом продукции завода ПЛАСТИЛЮКС-ГРУПП является сотовый поликарбонат, или, как его ещё называют, «ячеистый», «структурный», «структурированный», «канальный», «пустотелый». Такое множество названий он получил благодаря ячеистому строению листа и внутренней структуре каналов, расположенных параллельно друг другу на расстоянии от 4,5 до 14 мм. Воздух, находящийся в каналах, обеспечивает отличные теплоизоляционные свойства панелей, а продольные ребра жёсткости – прочность и гибкость. Это даёт возможность использовать сотовый поликарбонат в качестве универсального строительного материала для обшивки различных конструкций.
Существует много разновидностей и типов структур сотового поликарбоната. Белгородский завод ПЛАСТИЛЮКС-ГРУПП производит наиболее популярные из них – однослойные панели с двумя стенками (структура 2R) и двухслойные панели с тремя стенками (структура 3R). Их также называют однокамерными и двухкамерными. Двухкамерный (двойной) поликарбонатный лист отличается от однокамерного тем, что имеет дополнительную горизонтальную стенку по всей плоскости листа, разделяющую его на два слоя – верхний и нижний. Таким образом, в двухслойном поликарбонате формируется в два раза больше воздушных каналов, за счёт чего почти на треть повышается прочность и теплоизоляционные свойства панелей. Листы толщиной от 2,5 мм до 10 мм изготавливаются заводом ПЛАСТИЛЮКС-ГРУПП однослойными (двухстеночными), а от 12 мм до 20 мм – двухслойными (трехстенными).
Однослойный поликарбонат УЛЬТРАМАРИН 4 ммОднослойный поликарбонат УЛЬТРАМАРИН 4 ммОднослойный поликарбонат УЛЬТРАМАРИН 4 мм
Двухслойный поликарбонат ПОЛИНЕКС 16 ммДвухслойный поликарбонат ПОЛИНЕКС 16 ммДвухслойный поликарбонат ПОЛИНЕКС 16 мм
Поликарбонат двухкамерный САНЕКС 12 ммПоликарбонат двухкамерный САНЕКС 12 ммПоликарбонат двухкамерный САНЕКС 12 мм
Однослойный двухстеночный поликарбонат 4; 6; 8; 10 ммОднослойный двухстеночный поликарбонат 4; 6; 8; 10 ммПоликарбонат двухслойный трёхстенный 10; 12; 16; 18 мм
Сотовый поликарбонат – область применения
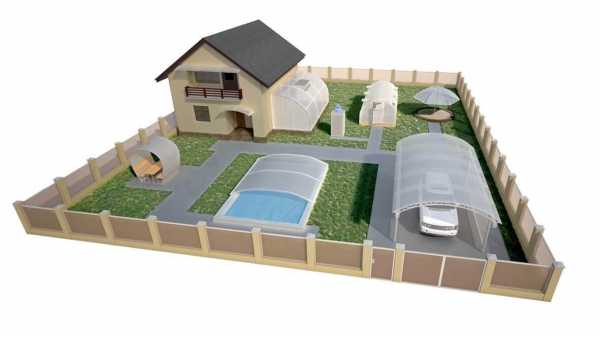
Сотовый поликарбонат появился в Израиле в 1976 году в ходе реализации программы поддержки развития сельского хозяйства и животноводства в жаркой пустыне. В нашей стране использование этого твёрдого пустотелого пластика в качестве покрытия для теплиц до середины 2000-х годов было главной областью применения. После открытия в Казани в 2008 году отечественного завода по синтезу поликарбонатов на базе ПАО «Казаньоргсинтез», в России начала формироваться целая обширная отрасль по изготовлению пустотных поликарбонатных плит. Наличие российской сырьевой базы и большого количества производителей готовой продукции позволило за несколько лет значительно расширить сферу применения сотового поликарбоната и сделать его по-настоящему универсальным.
Сегодня листовой ячеистый поликарбонат является одним из самых популярных строительных и облицовочных материалов, и имеет широкий спектр применения. Это светопрозрачная кровля в промышленности, облицовка фасадов зданий в строительстве и архитектуре, накрытие для дачных строений и навесов, теплоизоляция для балконов и зимних садов, заменитель стекла для веранд и террас. В последнее время поликарбонат широко применяется в качестве перегородок при создании интерьеров офисных помещений, а также в рекламе и дизайне – для изготовления светопрозрачных и светорассеивающих конструкций.
В приведённых ниже таблицах представлено более 200 примеров использования сотового поликарбоната производства завода ПЛАСТИЛЮКС-ГРУПП, в соответствии с выпускаемыми брендами или видами готовой продукции. Эта информация даёт покупателю возможность сделать правильный выбор толщины и марки материала, и подобрать подходящий поликарбонат для витража, навеса, теплицы или любой другой конструкции.
Толщина листа | Применение сотового поликарбоната ROYALPLAST |
4 мм | окна помещений в приморских регионах с сильными ветрами |
6 мм | крыши и навесы для автомобилей |
8 мм | перегородки в летних беседках дорогих ресторанов |
8 мм, 10 мм | ограждения городских фонтанов и водных аттракционов, элитные кованые заборы, ограждения, распашные и откатные ворота, калитки |
10 мм | модульные секции и перегородки для медицинских учреждений |
12 мм, 14 мм | стационарные и раздвижные укрытия для бассейнов, купола |
14 мм, 16 мм | современные оранжереи с боковым освещением, ботанические сады, вертикальные мансардные окна |
16 мм | различные спортивные сооружения, базы отдыха премиум-класса, прибрежные постройки, эллинги, ангары, накрытия для катеров |
16 мм, 18 мм | вертикальное остекление торговых центров, ответственные объекты в муниципальном строительстве |
Толщина листа | Применение сотового поликарбоната POLYNEX |
4 мм | разделители между постами на мойках самообслуживания автомобилей, заменитель стёкол в окнах лестничных площадок многоквартирных жилых домов |
6 мм | остекление первых этажей придорожных мотелей и кемпингов, накрытия для площадок летних кафе, для улицы, навесы для МАФов (малых архитектурных форм), остановочных и торговых павильонов, киосков |
8 мм | фасадные окна в залах ожидания вокзалов и станций, накрытия для входных групп, остекление котельных, цехов, производственных и технических помещений, складов и складских площадок |
8 мм, 10 мм | ограждения прилегающей территории административных зданий и муниципальных учреждений: школы, больницы, детские сады |
10 мм | заборы для охраняемых объектов, автостоянок, парковок |
10 мм, 12 мм | изготовление зенитных фонарей |
12 мм, 14 мм | тоннели и своды надземных пешеходных переходов, светопрозрачные переходы между зданиями |
16 мм, 18 мм | материал для окон промышленных зданий II-IV степени огнестойкости |
18 мм | светопропускающие элементы в шумозащитных экранах для автомагистралей, ж/д переездов, аэропортов, наружная отделка индустриальных объектов, фасадов и стен |
Толщина листа | Применение сотового поликарбоната КОЛОТЫЙ-ЛЕД |
4 мм | получение красочных световых эффектов для дискотек, музыкальных и развлекательных шоу, создание ярких сценических декораций и оригинальных световых композиций |
4 мм, 6 мм | декоративные элементы мебели, раздвижные двери для шкафов-купе с подсветкой, витражи |
6 мм | светорассеивающие и солнцезащитные навесы для затенения, навесы для качелей, разноцветные беседки, изготовление теневых навесов для детских садов |
6 мм, 8 мм | декор витрин магазинов и торговых залов, современные офисные интерьеры в стиле хай-тек, оформление интерьеров для ночных клубов, баров и ресторанов |
8 мм | остекление первых этажей корпусов загородных баз отдыха и детских оздоровительных лагерей, ограждения для детских городков и уличных игровых павильонов, ограждение летних кинотеатров, зон отдыха в общественных местах, танцевальных площадок |
10 мм | красивые заборы, презентабельные ограждения коттеджей и частных домов |
12 мм, 14 мм | оформление спортивных, игровых площадок в школах и детских садах |
16 мм, 18 мм | использование вместо оконного стекла в фитнес-клубах и тренажёрных залах |
18 мм | создание промышленных арт-объектов и дизайнерских фасадов зданий, оригинальные идеи и креативные решения в архитектуре |
Толщина листа | Применение сотового поликарбоната SUNNEX |
4 мм | летние душевые кабины на даче |
6 мм | козырьки над крыльцом, навесы во дворе, материал для стен дачной беседки, уличные декоративные элементы, остекление летней кухни, ограждение шашлычной зоны от ветра, навесы для мангала и барбекю |
8 мм | любые дачные постройки, подсобные помещения, дровники, будки для собак, ограждение территорий лагерного содержания домашних животных: стойло, загон, скотный или птичий двор, утепление стенок для ульев и голубятен |
8 мм, 10 мм | пристройки к дому, бытовки, мастерские, различные хозяйственные сооружения |
10 мм | дачные оранжереи, закрытые садовые павильоны, стационарные парники, зимние теплицы, полупрозрачные заборы, перегородки в дачном доме, в банях и бассейнах |
10 мм, 12 мм | вертикальное остекление небольших производственных и складских помещений, сараев, гаражей |
14 мм, 16 мм | закрытые веранды и террасы |
Толщина листа | Применение сотового поликарбоната GREENHOUSE-nano |
3 мм, 3,5 мм | переносные и стационарные парники для рассады |
4 мм | сезонные приусадебные теплицы арочного типа, садовые и огородные теплицы капельной формы |
6 мм | классическое накрытие для теплиц «домиком» с двускатной или ломаной крышей |
6 мм, 8 мм | пристенные односкатные теплицы с примыканием к дому |
10 мм, 12 мм | вертикальное остекление промышленных теплиц |
12 мм | утепление окон животноводческих комплексов, коровников, свинарников |
14 мм | капитальные фермерские теплицы ангарного типа |
16 мм | стационарные отапливаемые теплицы туннельного типа |
18 мм | тепличные комплексы на основе гидропонных систем |
Толщина листа | Применение сотового поликарбоната ULTRAMARIN |
2,5 мм, 3 мм | комнатные оранжереи |
3,3 мм, 3,5 мм, 3,8 мм | гигиеничный материал для душевых кабин, шторки и ширмы для ванной комнаты |
4 мм, 6 мм | вставки для межкомнатных дверей и перегородок в квартире, внутри помещения, наружная световая реклама, стенды, выставочные экспозиции, лайтбоксы |
6 мм | торговое оборудование, прилавки, модули, витрины, небольшие козырьки и навесы |
8 мм | обустройство гардеробных комнат, хозблоков, кладовых помещений и ниш, открытые летние веранды, террасы, лёгкие ограждения |
10 мм | остекление лоджий и чердаков, непрозрачные перегородки в душевых и туалетных кабинах, санузлах, ванных комнатах |
12 мм, 14 мм | цельный листовой материал для отделки балкона и стен в ванной комнате |
16 мм, 18 мм, 20 мм | светопрозрачные стационарные и раздвижные перегородки в офисных помещениях |
Продажа поликарбоната
ООО «ПЛАСТИЛЮКС-ГРУПП» – одно из крупнейших предприятий по изготовлению и продаже сотового поликарбоната в России. Наша компания принимает активное участие в международных выставках производителей, проходящих в Дюссельдорфе, Москве, Минске, Киеве, Астане. Сотрудники экспортного отдела постоянно ведут работу по популяризации российского поликарбоната за рубежом.
Внутри страны продукция предприятия продаётся оптом и в розницу в большинстве строительных супермаркетов, а также реализуется производителями теплиц. Купить поликарбонат со склада наших дилеров можно в Москве, Санкт-Петербурге, Туле, Нижнем Новгороде, Воронеже, Курске, Ростове-на-Дону, Краснодаре, Симферополе и многих других городах (см. раздел «Где купить»).
Специалисты по оптовым продажам готовы приехать к вам в офис и лично презентовать сотовый поликарбонат. Такие демонстрации производимой продукции проводятся нашими менеджерами в ходе выездных переговоров. Личный контакт – это философия ведения бизнеса нашей компании и лучший способ договориться о справедливой цене, а также установить долгосрочные партнёрские отношения.
Виды поликарбоната от завода ПЛАСТИЛЮКС-ГРУПП
Видеопредставление ПЛАСТИЛЮКС-ГРУПП
polikarbonates.com
Оборудование для производства сотового поликарбоната: станки, сырье и технология
Сотовый поликарбонат — листы, имеющие структуру ячеек. То есть это – лист, состоящий из слоев, разделенных между собой ребрами жесткости в виде сот. Поликарбонат активно применяется для проведения строительных работ и для нужд сельского хозяйства. Производство поликарбоната, при правильном подходе, может стать хорошим бизнесом.
Изготовление сотового поликарбоната: оборудование
Для производства этого материала используется линия экструзии. Существуют разновидности этой линии, которые оснащены также специальным оборудованием, которое используется для нанесения на листы поликарбоната специального слоя, защищающего материал от действия солнечных лучей. Использование экструзионной линии для производства сотового поликарбоната позволяет выпускать лист, имеющий такие габаритные размеры: 4-16\2100 мм. За одну минуту производится 5 метров такого листа.
Выбрав качественное оборудование для производства одноразовой посуды можно запустить прибыльное дело.
Открытие шиномонтажа — отличное решение. Здесь Вы узнаете какое оборудование для этого необходимо.
Состав производственной линии
Линия, которая используется для производства этого материала, состоит из таких основных узлов:
Загрузчик исходного сырья – данная часть производственной линии выполняет функцию загрузки рабочего сырья, из которого будет формироваться лист поликарбоната (гранулы и сыпучий материал). Загруженное сырье проходит предварительную сушку на протяжении 24 часов. Максимальная температура, которая используется для сушки, достигает 150 градусов. Все операции (загрузка, установка времени и температуры просушки сырья) устанавливаются в автоматическом режиме.
- Экструдер – преимущественно используется одношнековый вариант экструдера. Он состоит из прочного сплава стали, что гарантирует его прочность и длительный срок эксплуатации. Функция экструдера заключается в том, что расплавленный исходный материал при помощи шнека выдавливается через формовочные отверстия, что придает сплаву определенную форму.
- Головка – состоит из высококачественной стали. Оборудована отверстием определенного размера. Основное ее предназначение заключается в том, что через отверстие головки проходит расплавленная масса, и в результате она приобретает определенную толщину. В комплекте производственной линии идет три головы, которые позволяют придавать расплавленной массе такую толщину (4-8 мм\9-12 мм\13-16 мм).
- Вакуумный формировщик – основание формировщика состоит из матрицы. Расплавленная масса проходит под матрицей и под действием вакуума вытягивается, приобретая определенную форму. После окончания процесса формировки масса охлаждается.
- Транспортировочная линия – состоит из 8 транспортировочных роликов, диаметр которых составляет 70 мм. При помощи транспортировочной линии лист передвигается к следующему отделу производственной линии для дальнейшей обработки.
- Сушка – камера, в которой при помощи использования инфракрасных лучей происходит сушка формированного листа материала. В камере поддерживается стабильная температура в автоматическом режиме. Мощность данной камеры составляет 40 кВт
- Выгрузочная установка с установленной боковой порезкой – данный отдел линии оснащен мощным мотором, мощность которого составляет 2,2 кВт. На установке смонтировано оборудование, которое выполняет резку поликарбонатного листа. Процесс порезки осуществляется современным дисковым ножом.
В процессе изготовления часто применяются линии по производству сотового поликарбоната, которые оснащены некоторыми дополнительными функциями, например способны осуществлять покрытие листа защитной пленкой и др.
Технология производства поликарбоната
Технология производства сотового поликарбоната довольно сложная и трудоемкая и состоит из нескольких этапов:
- Очистка гранул поликарбоната. От цвета гранул зависит цвет поликарбонатных листов. В специальной центрифуге гранулы очищаются от посторонних элементов и пыли. Далее они подаются для дальнейшей переработки. При некачественной очистке гранул исходный материал не будет иметь чистого цвета, а, следовательно, и не будет отличаться высоким качеством.
- Плавление сырья. При помощи автоматического дозатора отбирается определенное количество гранул, которые потом поступают в специальную камеру, где они из твердого состояния переходят в жидкое. Под действием высокой температуры гранулы расплавляются. На этом же этапе происходит включение разнообразных добавок и присадок, которые придают исходному материалу определенные свойства. Например, металлическую крошку добавляют для придания поликарбонату прочности, красители придают материалу определенный цвет, присадки препятствую накоплению влаги на поверхности поликарбоната, добавки для отражения ультрафиолетовых лучей и др. Все эти добавки и присадки способствуют улучшению качества и характеристик поликарбоната.
- Придание листам формы. В результате использования процесса экструзии расплавленная масса получает сотовую структуру. Структура сотового поликарбоната состоит из двух листов, между которыми находятся ребра жесткости, имеющие сотовую структуру (от сюда и название поликарбоната – сотовый). После завершения данного этапа на конвейер выходят листы определенной толщины (от 4 до 16 мм).
- Узел нарезки. После полного остывания листов при помощи дискового ножа происходит их нарезка. Существует стандартный размер листа поликарбоната (6120\2100 или 1200\2100). При необходимости можно устанавливать другие параметры нарезки листов.
- Контроль качества. Поликарбонат должен соответствовать неким стандартам. Именно поэтому после завершения его нарезки при помощи специального оборудования происходит контроль качества материала (определяется равномерность листа, выявляется присутствие посторонних частиц, определяется равномерность цвета, проверяется надежность материала и пр).
Ознакомившись с советами по выбору оборудования для производства керамической плитки, можно открыть собственное производство и получать постоянный доход.
Открыть собственную автомойку проще, чем Вы думаете. Всё о подборе оборудования здесь.
Чтобы получить качественную металлочерепицу, нужно правильно наладить производство. Подробнее на http://buisiness-oborudovanie.com/dlya-metallokonstrukcij/oborudovanie-dlya-proizvodstva-metallocherepicy/.
После завершения окончательной проверки качества, листы сотового поликарбоната формируются в пачки и на поддонах поступают на склад.
Современное оборудование для производства сотового поликарбоната
На современном производстве используется несколько моделей оборудования, которое используется для производства сотового поликарбоната.
Например, модель Модель FUJ — 150/34 . С линии сходят листы поликарбоната, толщина которых составляет от 4 до 16 мм, а их габаритные размеры достигают таких параметров: 1100\2200 мм.
Довольно большой популярностью пользуются модели SJ90\36 или SJ120\36. Между этими моделями линий по производству сотового поликарбоната нет существенных различий.
Развитие современных методов и технологий способствует созданию все более современных линий, которые используются для производства такого популярного, надежного и недорогого материала, как поликарбонат.
Видео про изготовление сотового поликарбоната
buisiness-oborudovanie.com
Малый бизнес:производство сотового поликарбоната.
Если у вас уже есть бизнес по производству теплиц, парников и прочих дачно-садоводческих конструкций, отличной альтернативой закупке материалов станет собственное производство поликарбоната.
Благодаря востребованности данного материла на рынке, эта бизнес идея подойдет и для открытия предприятия с нуля. Капитальные затраты на запуск производства значительны, но не смотря на это, предприятие может выйти на самоокупаемость менее чем за пол года и полностью окупиться за 30 месяцев.
Сотовый поликарбонат – что это? Сферы применения
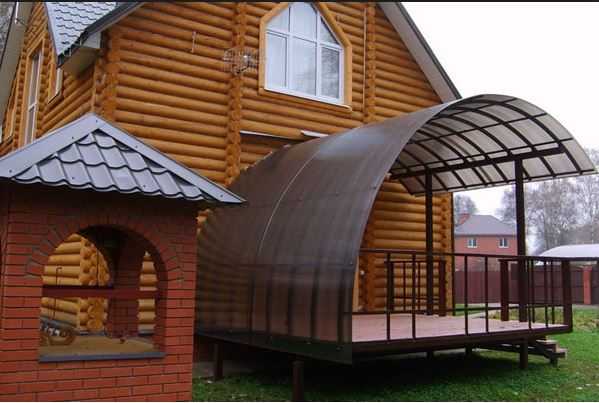
Навес-пристройка, выполненная из поликарбоната
Сотовый поликарбонат – два слоя полимерных листов, укрепленные ребрами жесткости в виде ячеек (сот). Листы материала могут иметь различную толщину и гибкость. Поликарбонат имеет целый ряд полезных свойств. Среди них теплоизоляция, хорошая ударопрочность и антикоррозийность. Важной особенностью материала становится светопропускающая способность. Это делает сотовый поликарбонат незаменимым материалом в промышленном, сельском хозяйстве и на дачных участках. Также поликарбонат может иметь поглощающее ультрафиолет покрытие, что позволяет применять его в отделке и строительстве. Материал нашел свое место в изготовлении фасадов, крыш, внутренней отделки помещений, а также в изготовлении навесов, беседок и других ландшафтных конструкций.
Технология производства сотового поликарбоната
Сырье:гранулы поликарбоната.
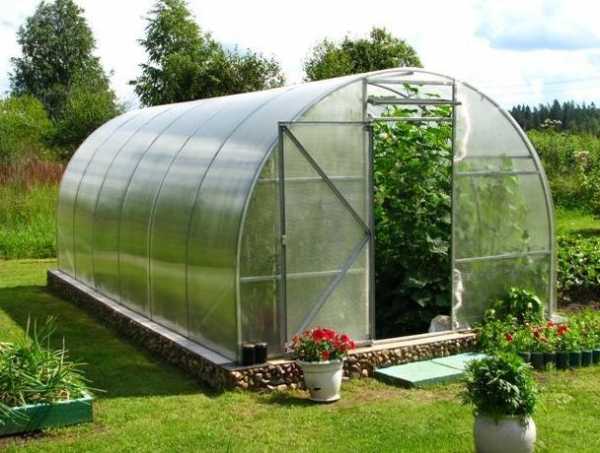
Теплица из поликарбоната
Оборудование:экструзионная линия.
Персонал:
- 4 оператора для посменной работы;
- 2 уборщика;
- Технолог.
Первоначально разберемся, что же такое экструзионная линия
Экструзионная линия – автоматизированная линия потокового производства материалов из полимера. Основные части: экструдера, экструзионные головки, вакуумный калибровочный стол, сухой вакуумный калибратор и системы управления.
Нынешний рынок изобилует предложениями по поставке экструзионных линий из Европы и Китая. Практически все компании-поставщики проводят первичную пуско-наладку оборудования и обучают рабочий персонал линии.
Стоит отметить, что экструзионная линия вещь габаритная. Длина линии, в среднем достигает 40 метров. Поэтому перед покупкой этого дорогостоящего оборудования стоит заранее позаботиться об аренде или покупке достаточных производственных площадей.
Экструзионные линии отличаются не только габаритными размерами и мощностями, но и своей производственной мощностью.
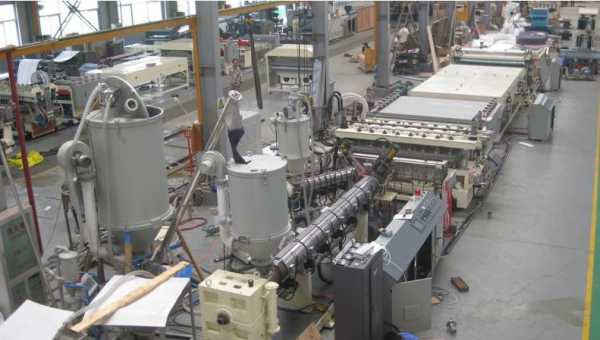
Экструзионная линия для производства сотового поликарбоната.
Технологию производства сотового поликарбоната можно разделить на несколько этапов.
- Подготовка сырья. Гранулы поликарбоната производятся в различных цветовых вариациях, на производство поступают в плотных мешках, защищающих материал от попадания влаги и грязи. Пред подачей на линию, гранулы стоит взвесить и очистить от попавшей пыли.
- Плавление полимера. Поступившие в цех плавления гранулы, переходят в состояние жидкости. На этом этапе добавляются различные вещества для улучшения характеристик будущих листов. Каждый производитель старается держать рецептуру в секрете. Именно для этого на предприятии должен работать химик-технолог. Специалист должен разработать необходимую рецептуру, и следить за ее соблюдением. В процессе работы рецептура может изменяться и усовершенствоваться. Это позволит производить поликарбонат, имеющий различные свойства.
- На следующем этапе полученная полимерная масса, в процессе экструзии формируется в листы необходимых размеров и форм.
- После того как листы сформированы, пластику нужно остыть. Благодаря своим уникальным свойствам полимер остывает достаточно быстро, после чего листы покрываются защитным слоем, режутся и приходят на этап упаковки и фасовки.
Вся технология производства сотового поликарбоната автоматизирована. Но, не смотря на «умную» технологию, процесс должен проходить под руководством и наблюдением человека. Особое внимание уделяется электро безопасности, используйте силовые кабели от надёжных поставщиков. Заказать силовой кабель в ПВХ-изоляции можно на сайте компании ООО «МЭК ЭЛЕКТРИКА» (Контакты: г. Москва, Дмитровское шоссе, д. 87 +7 (499) 322-78-78).
На качество производимой продукции может повлиять любая, даже незначительная мелочь. Именно по этой причине в цехе производства сотового поликарбоната должна соблюдаться чистота, не допускается скопление пыли и производственного мусора. Желательно, что бы весь персонал цеха соблюдал правила по поддержанию чистоты и имел специальную рабочую униформу.
Бизнес процессы
На этапе составления бизнес-плана, кроме выбора помещения и оборудования, стоит уделить внимание сооружению склада готовой продукции. Хранение готовой продукции должно осуществляться при температурах от 0 до +25 градусов. Не допускается избыточная влажность помещения. Склад готовой продукции должен быть изолирован от попадания солнечного света, так как ультрафиолет негативно сказывается на качестве поликарбоната.
Отдельное внимание также нужно уделить логистике и формированию каналов сбыта. Реализацию можно осуществлять как оптом, так и в розницу через строительные рынки, специализированные магазины, а также путем прямого распространения в строительные и сельскохозяйственные отрасли.
Для развития производства сотового поликарбоната, как и любой другой деятельности, обязательно необходимо формировать положительный имидж компании. Не забывайте о рекламе, чаще проводите маркетинговые исследования рынка, обучайте и повышайте квалификацию персонала занимающегося сбытом и работой с клиентами.
businessandmoney.ru
Как производят поликарбонат — Все о поликарбонате
Благодаря универсальным техническим характеристикам, таким как легкость, прочность, коррозийная стойкость, поликарбонаты являются очень востребованным материалом в различных отраслях промышленности: в производстве автомобилей, электротехнической, электронной промышленности, в производстве предметов бытового потребления и т.д. Составляя серьезную конкуренцию металлу и стеклу, за счет увеличения потребления конструкционных материалов доля литого и сотового поликарбонатов на мировом рынке с каждым годом завоевывает все новые позиции.
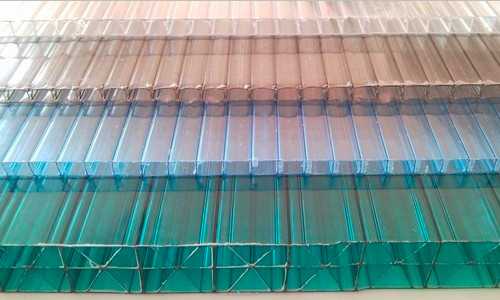
Поликарбонат это материал, обладающий следующими свойствами: устойчив к морозам, способен выдержать кратковременный нагрев до 153 ºС, а также циклические перепады температур от +100ºС до -253ºС.
Производство поликарбоната — сложный технологический процесс, в основе которого лежит использование двухатомного фенола и угольной кислоты.
Поликарбонат является линейным полиэфиром этих двух составляющих компонентов. В зависимости от природы, поликарбонаты разделяются на алифатические, жирноароматические и ароматические. Практическое значение имеет лишь ароматический поликарбонат. Поликарбонаты относятся к разряду аморфных, инженерных пластиков, а изготовленные на их основе композиции — к специальным полимерам.
Достоинства поликарбоната
Схема структур сотового поликарбоната.
Широкий диапазон использования литого и сотового поликарбоната обусловлен универсальными термическими, оптическими и механическими свойствами данного материала. Так, поликарбонат обладает высокой прочностью и жесткостью в сочетании с довольно высокой стойкостью к различным ударным воздействиям, в том числе и при повышенной или пониженной температуре.
Поликарбонат — морозостойкий, оптически прозрачный материал, способный выдерживать кратковременный нагрев до 153ºС и циклические перепады температур от +100ºС до -253ºС. Поликарбонат устойчив к агрессивному воздействию окислителей, растворов солей, кислот, но не обладает устойчивостью к действию щелочей, органических растворителей и концентрированных кислот.
Читайте также:
Поликарбонат: размеры листов и другие характеристики.
Инструкция по монтажу поликарбоната на металлический каркас своими руками.
О том, какой поликарбонат выбрать для навеса, читайте здесь.
Вернуться к оглавлению
Современные технологии изготовления поликарбоната
Процесс создания поликарбоната базируется на использовании одной из следующих технологий: поликонденсации, переэтерификации или межфазной поликонденсации.
Поликонденсация — это метод синтеза полимеров, базирующийся на реакциях замещения мономеров и/или олигомеров, которые, взаимодействуя между собой, образовывают побочные низкомолекулярные соединения.
Переэтерификация диарилкарбонатов проводится с ароматическими диоксисоединениями (так называемый нефосгенный способ). В качестве диоксисоединения выступает 2,2-бис-(4-оксифенил) пропан (диан, бисфенол А).
В промышленном производстве поликарбоната в настоящее время используется способ, базирующийся на межфазной поликонденсации. Согласно данному методу производится взаимодействие динатриевой соли бисфенола А с фосгеном в присутствии оснований. Протекающие при взаимодействии процессы практически необратимы. Данная технология используется для производства 80% поликарбоната в мире.
Наша отечественная технология также применяет метод межфазной поликонденсации фосгена с бисфенолом А. Очевидными недостатками данного метода является высокая токсичность реагента, склонность к образованию побочных продуктов и необходимость последующей очистки образующегося полимера от изначально применяемых реагентов и побочных компонентов.
Схема устройства оптического поликарбоната.
Производство полимеров на основе новейших технологий ориентировано на нефосгенный метод выпуска, который базируется на процессах взаимодействия диметилового эфира угольной кислоты (ДМУК) и дифенилолпропана. Подобное решение позволяет перевести технологическую процедуру получения ПК из фазы жидкого состояния в расплав, исключить экологически опасный фосген и существенно увеличить объемы производства.
Бесфосгенный метод по всем параметрам, кроме энергетических расходов, превосходит традиционные технологии. Но пока и он не лишен некоторых недостатков, в число которых входит побочное выделение анизола, не имеющего на данном этапе полезного применения в том объеме, который образуется в ходе нефосгенной реакции. Мировое потребление анизола в настоящее время составляет до 7 тыс. тонн, поэтому излишки материала отправляются на сжигание. Еще одним существенным минусом нефосгенной технологии является невозможность получения ряда марок поликарбоната — высокомолекулярного поликарбоната и сополимеров на основе поликарбоната.
Поликарбонатный гранулят, как известно, является основой для производства листов поликарбоната, в число которых входит и сотовый поликарбонат. Этот материал представляет собой листы ячеистой структуры, выполненные из полимера в виде сот, которые состоят из двух слоев, соединенных посредством внутренних ребер жесткости между собой. Сотовый поликарбонат — легкий, устойчивый к коррозийным процессам, ударопрочный материал с хорошими теплоизоляционными и светопрозрачными свойствами.
На рынке, помимо обычного сотового поликарбоната, можно встретить и более долговечный его аналог — полимер, покрытый специальным защитным слоем, устойчивым к ультрафиолетовому излучению. Благодаря своим универсальным свойствам сотовый поликарбонат очень востребован в строительстве и сельском хозяйстве. В зависимости от толщины, он выступает в качестве прекрасного материала для оборудования навесов, арок, крыш, витрин, перегородок, бассейнов, теплиц, балконов, автобусных остановок, вокзалов, стадионов и т.д., поэтому в число целевых потребителей материала входят автостоянки, муниципалитет, рекламные и дизайнерские компании, АЗС, подрядчики, тепличные хозяйства и сельскохозяйственные предприятия.
Вернуться к оглавлению
Изготовление сотового поликарбоната
Для производства сотового поликарбоната используются поликарбонатные гранулы. Изготовление материала включает в себя прохождение гранулами цикла определенных технологических процессов. Производство сотового поликарбоната предполагает наличие:
Схема воздействия солнечных лучей на поликарбонат.
- гранул поликарбоната;
- специализированного оборудования;
- специальных химических добавок.
Вначале закупается поликарбонатный гранулят. Стоит учитывать, что, в зависимости от цвета гранул (которые могут быть белыми, цветными и прозрачными), в конечном итоге получится материал определенной цветовой гаммы. Поэтому при покупке стоит обращать внимание на цвет сырья.
После взвешивания, сортировки, очистки от пыли для производства листов гранулы поступают на плавление.
В камере плавления гранулы переходят из твердого состояния в жидкое, к ним добавляются специальные компоненты, способствующие улучшению характеристики будущего материала. В конечном итоге образуется однородная смешанная масса.
Далее начинается процесс экструзии, в ходе которого бесформенная масса преобразуется в нужную структуру, монолитную или сотовую. Помимо основного процесса экструзии, поликарбонатная масса одновременно подвергается соэкструзии тонкой пленкой, поглощающей ультрафиолетовое излучение, что способствует сохранению превосходной прочности материала.
На следующем этапе прозрачный или цветной сотовый поликарбонат в виде тонких пластин, скрепленных между собой прочными ребрами жесткости, подается на конвейер.
После остывания пластины поликарбоната нарезаются на нужные размеры, складируются и в многослойных, защищенных от проникновения влаги мешках поступают на хранение.
polikarbonatstroy.ru
Производство
Производственная линия
1 2 3 4 5 6 7 8 9 101Дозатор (из бункера сырье подается в дозатор) 2Экструдер (расплавка гранул) 3UV-дозатор 4Голова (объединение основного сырья с UV-защитой, формирование структуры листа) 5Калибратор (вакуумное выравнивание и стабилизация листа) 6Тянущие элементы 7Печь (снятие поверхностных напряжений, дополнительная стабилизация листа) 8Упаковщик (нанесение защитной пленки) 9Нож (резка листа заданного размера) 10Транспортер готовой продукции
О производстве
Компания АО «КАРБОГЛАСС» — один из самых первых российских заводов производителей листов сотового поликарбоната. В декабре 2006 г. был осуществлен запуск первой линии по выпуску листов сотового поликарбоната. С января 2007 г. сотовый поликарбонат выпускается под собственной торговой маркой CARBOGLASS®.В настоящий момент завод развивается быстрыми темпами и постоянно расширяет ассортимент выпускаемой продукции. Ежегодно мощности производства АО «КАРБОГЛАСС» увеличиваются, закупается новое оборудование.
На сегодняшний день сотовый поликарбонат выпускается на четырех линиях (3 линии в г. Голицыно, одна линия в г. Красноярск). Совокупная производственная мощность четырех линий составляет до 1 100 тонн в месяц.
Так же непрерывно работают две линии по выпуску поликарбонатных профилей. Общая производственная мощность составляет 62 тонны в месяц.
Запущен проект модульные системы CARBOGLASS pro. Это принципиально новый отечественный материал для создания легких светопрозрачных конструкций. Данные системы не только не уступают мировым аналогам, но и превосходят их по ряду показателей, таких как удобство монтажа и надежность эксплуатации. Производственная мощность линии составляет до 80 тонн в месяц.Летом 2013 года, осуществлен запуск новой линии для производства монолитного поликарбоната. Производственная мощность линии составляет до 400 тонн в месяц.
Сотовый поликарбонат — листовой материал, который производится из высококачественного поликарбоната методом экструзии, что подразумевает расплавление гранул и выдавливание этой массы через особую форму (фильеру), которая определяет строение и конструкцию листа. Уникальная конструкция фильеры и адаптера позволяет получать листы с равномерным распределением толщины стенок и УФ — защитного слоя. Данные особенности производства обуславливает высокую механическую прочность и продолжительный срок службы листа.
В производстве листов CARBOGLASS® используются высокотехнологичные экструзионные линии компании «OMIPA S.p.a.» (Италия). Сырьем для производства листов и профилей служит гранулят ведущих мировых производителей — Styron, Kafrit, Covestro, Казаньоргсинтез.
По данным зарубежного интернет-портала pc-sheets.com завод «КАРБОГЛАСС» входит в ТОП-10 мировых производителей листового поликарбоната.
Ассортимент профилей собственного производства:
- торцевые поликарбонатные профили (UP-профиль)
- соединительные неразъёмные профили (HP-профиль)
- соединительные разъёмные профили (HCP-профиль)
- коньковые профили (RP-профиль)
- угловые профили (FCP-профиль)
- пристенные профили (FP-профиль)
Все поликарбонатные профили компании «КАРБОГЛАСС» имеют специальный защитный УФ — слой, нанесенный методом соэкструзии. УФ — защита препятствует разрушению профилей под действием солнечного света и способствует длительному сроку эксплуатации.
Наличие квалифицированного опытного инженерного персонала и лаборатории, оборудованной самым современным оборудованием, позволяет выпускать продукцию (к примеру навесы из поликарбоната), отвечающую самым высоким требованиям наших клиентов. Система менеджмента качества предприятия сертифицирована по стандарту ISO 9001:2008.carboglass.ru
виды, характеристики, плюсы и минусы, особенности монтажа
В индустриальном и частном строительстве полимерные изделия стали применять еще в 70е прошедшего столетия. Полувековая практика доказала и на деле подтвердила многочисленные преимущества использования синтетической продукции. Однако не все еще знакомы с ее вескими приоритетами.
Более того, есть люди, вообще не представляющие, что такое поликарбонат, какими техническими характеристиками и технологическими плюсами он привлекает строителей, как в конструкциях и сооружениях работает совсем не новый, но не всем еще известный материал.
Чтобы получить полноценные ответы на интересующие вопросы, стоит разобраться со спецификой полимерного продукта и особенностями его производства.
Популярность и востребованность поликарбоната в строительстве обоснована рядом приоритетных качеств, свойственных только полимерным материалам. Его необычайная легкость сочетается с достаточно высокой прочностью и с устойчивостью к ряду внешних воздействий.
Полимерный листовой материал активно вытесняет хрупкое и тяжелое силикатное стекло. Его гораздо активнее и охотнее применяют в остеклении строительных конструкций.
Используя поликарбонат, обустраивают террасы и оранжереи, сооружают навесы, козырьки над входными группами и крыши беседок. Служит кровельным покрытием, светопроводящим элементом панорамных окон, облицовкой стен.
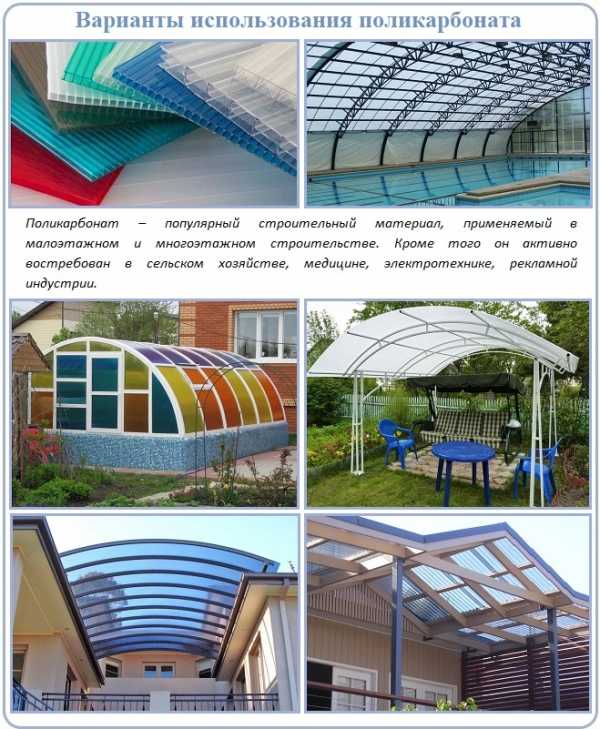
Поликарбонат в отличие от стекла может держать довольно внушительную нагрузку без растрескивания и деформаций. Он подходит для перекрытия больших пролетов, не создает рискованных ситуаций, возникающих при разрушении масштабного панорамного остекления.
Материал синтетического происхождения не требует крайне бережного отношения во время транспортировки, доставки к месту работы и производства монтажных работ. Прост в обработке, не создает осложнений в раскрое. Во время работы с ним практически не бывает не пригодных для дальнейшего применения отходов и испорченных кусков.
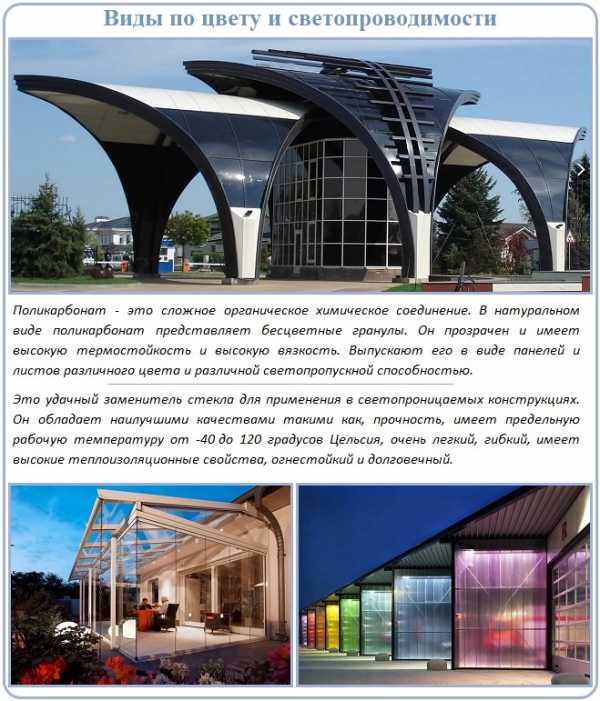
По структурным показателям листовой поликарбонат делят на два подвида, это:
- Монолитный. Материал с монолитной структурой и равными характеристиками по всей толщине. На срезе лист выглядит как привычное нам стекло, но отличается в 200 раз большей прочностью. Гнется, правда до заданных производителем пределов.
- Сотовый. Материал с характерными «сотами», если смотреть на его срез. По сути, это два тонких листа, между которыми расположены дистанционные продольные перегородки. Они-то и формируют сотовую структуру, а также служат ребрами жесткости.
Обе разновидности подходят для формирования округлых поверхностей, что совершенно невозможно при использовании стекла. Но желающим реализовать интересную идею следует учитывать радиус изгиба, который обязательно указывается изготовителем материала в технической документации.
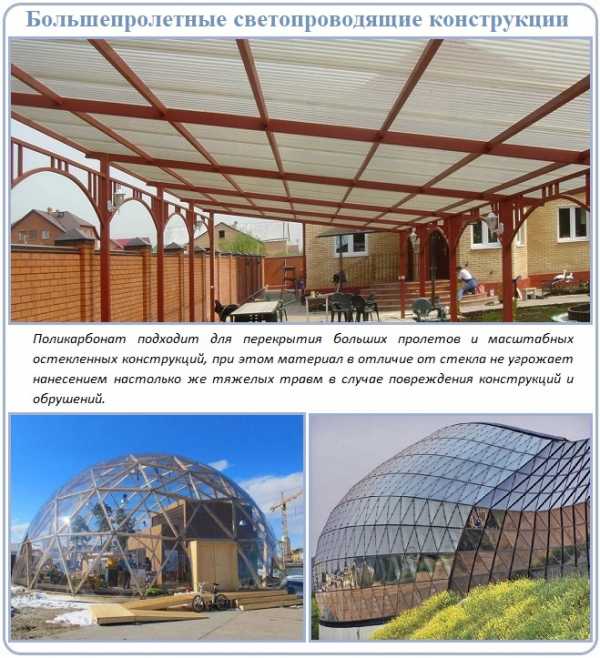
Получают оба вида материалов в результате поликонденсации двух химических компонентов: хлорангидрита дефинилопропана и угольной кислоты. Создается в итоге вязкая пластичная масса, из которой формируется монолитный или сотовый поликарбонат.
Для того чтобы получить полноценное представление об обеих разновидностях, разберемся со спецификой их производства и особенностями применения.
Монолитные поликарбонатные листы
Исходный материал для производства монолитного термопластического полимера поставляется в формате гранул. Изготовление проводится по экструзионной технологии: загружают гранулы в экструдер, где его перемешивают и расплавляют.
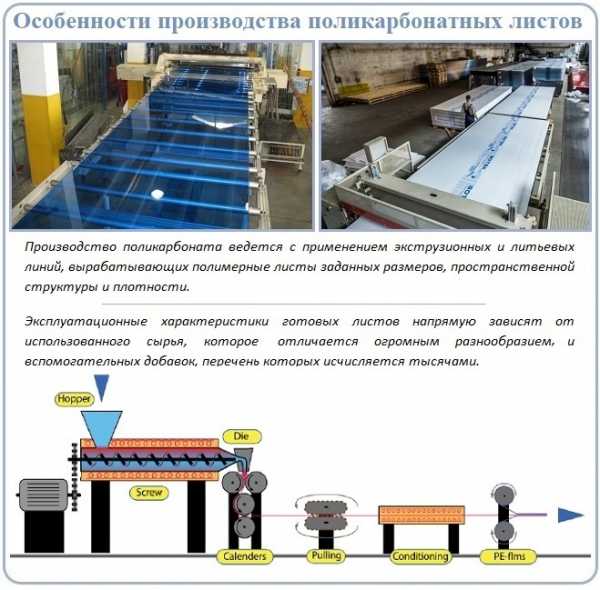
Размягченная равномерная массы продавливается через фильеру экструдера – плоскощелевое устройство, на выходе из которого получается полимерная плита равной толщины во всех точках. Толщина плитного поликарбоната варьирует от 1,5 мм до 15,0 мм. Одновременно с толщиной плите придают требующиеся габариты.
Монолитные полимерные плиты выпускают в обширном ассортименте, они отличаются:
- По светопроводящим качествам. Бывают прозрачными, пропускающими до 90% светового потока, и матовыми, практически не проводящими свет.
- По рельефу. Бывают плоскими и волнистыми. Полимерный прозрачный и не проводящий свет шифер это одна из разновидностей монолитного поликарбоната.
- По цвету. В предложенном покупателям изобилии торговых позиций есть материалы разнообразного колера.
Среди положительных качеств монолитного поликарбоната значится нулевое влагопоглощение. Он совсем не впитывает атмосферную воду и бытовые испарения, потому не гинет и не создает условия для расселения грибковых колоний.
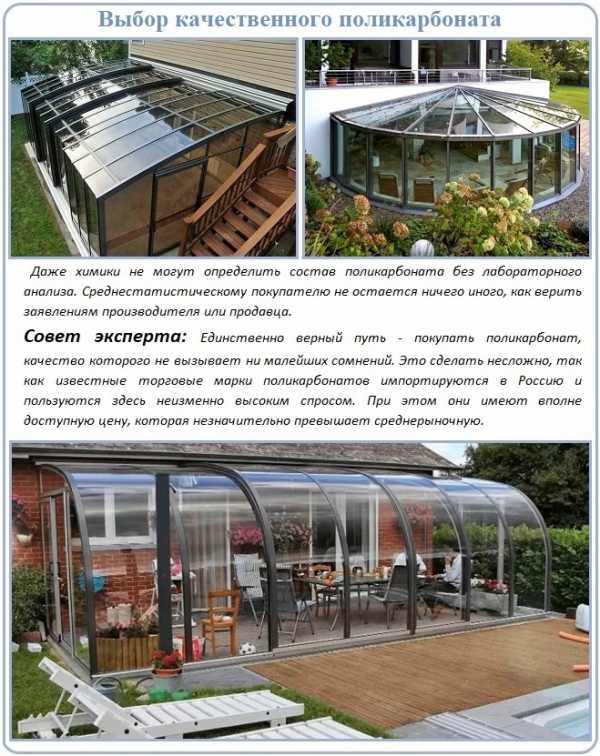
Монолитный вариант не боится низких и высоких температур, отлично работает в широком диапазоне. В жаркую погоду, как и все полимеры, склонен к линейному расширению, что требуется в обязательном порядке учитывать при проектировании и проведении монтажных работ.
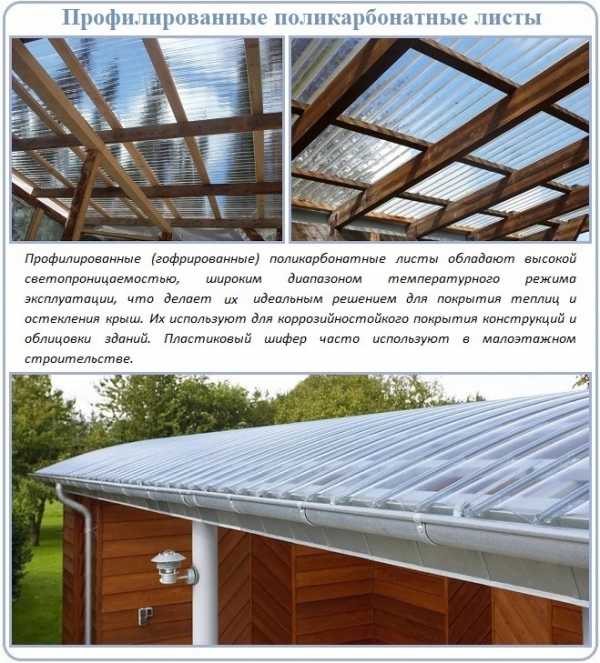
Сотовые поликарбонатные панели
Производство сотового полимерного материала отличается от изготовления монолитного собрата только формой фильеры. При продавливании через нее создается многослойный материал с длинными продольными каналами малого сечения.
В сформированных фильерой каналах находится воздух, благодаря чему существенно увеличиваются изоляционные качества полимерного продукта, вместе с тем значительно уменьшается вес.
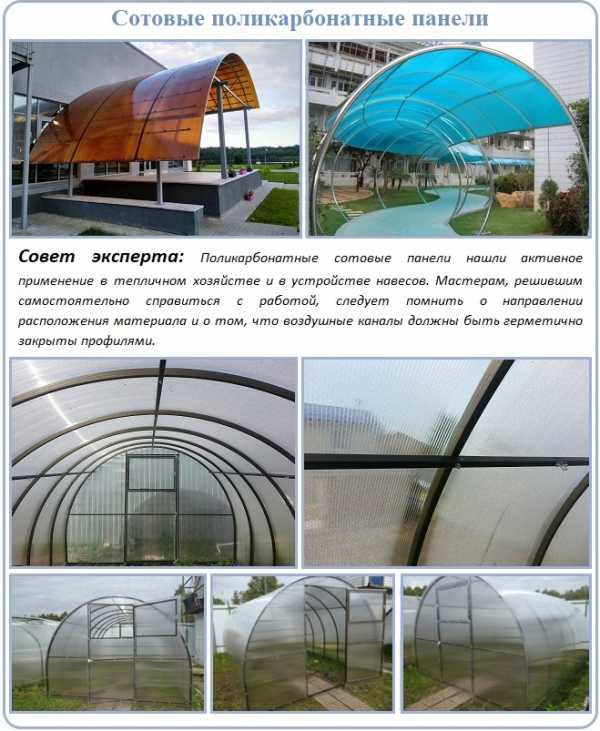
Позиции из сотового ассортимента различаются:
- По общей толщине панели. В распоряжении архитекторов и дизайнеров сейчас есть сотовый материал толщиной от 4,0 мм до 30,0 мм. Естественно, чем толще лист, тех хуже он гнется и меньше подходит для формирования округлых плоскостей.
- По цвету и светопроводящим качествам. Ввиду особенностей структуры сотовый поликарбонат не может проводить более 82 % световых лучей. Колоритная гамма не уступает монолитной номенклатуре.
- По числу слоев и форме сот. Слоев в сотовой панели может быть от 1го до 7ми. Ребра жесткости, являющиеся одновременно с тем дистанционными элементами и стенками воздушных каналов, могут располагаться строго перпендикулярно к верхней и нижней поверхности листа или быть к ним же под углом.
Созданные ребрами-перемычками каналы можно смело отнести как к плюсам материала, так и к его минусам. Несмотря на совершенную неспособность самого поликарбоната впитывать воду, они как раз наоборот, могут «подсасывать» влагу из расположенных рядом грунтов и растений, запросто пропускают в себя бытовые испарения.
Для того чтобы в каналы не проникала вода, которая, кстати, ощутимо снижает приоритетные изоляционные качества сотового поликарбоната, при выполнении монтажных работ их следует закрывать гибкими профилями – линейными монтажными деталями. Их применяют как для защиты края, так и для соединения смежных листов в одну конструкцию.
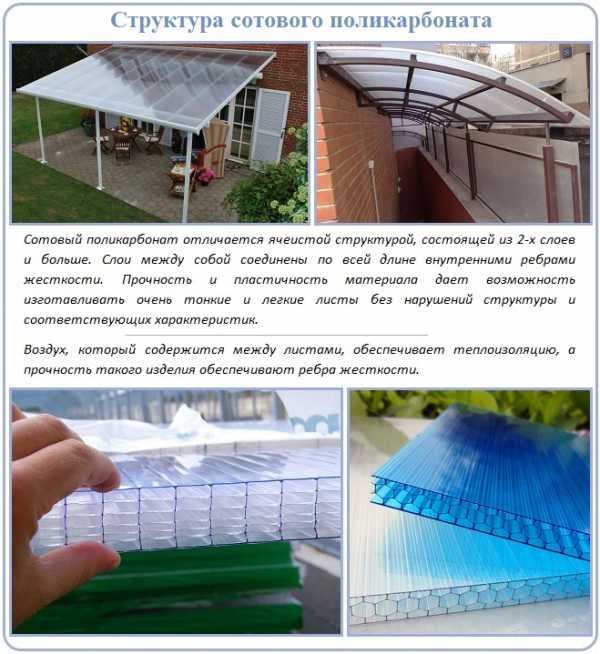
Поликарбонатные панели – отличный стройматериал, но все же и он не лишен недостатков. Он пропускает ультрафиолет группы А и Б. К минусом отнесем чувствительность к воздействию солнечного света, склонность неравномерно рассеивать лучи и способность поддерживать горение.
Рассмотрим, какими методами производители полимерных листов борются с отрицательными свойствами. Так мы поймем, на что следует обращать внимание, выбирая поликарбонат для частного строительства.
Нанесение защиты от ультрафиолета
Существенным минусом созданных из поликарбоната плит не зря признают способность пропускать ультрафиолетовую составляющую солнечного излучения, вредную для, например, растений в теплице. Далеко не полезна она и для отдыхающих под навесом, и для купающихся в бассейне с полимерным павильоном.
Кроме того УФ негативно действует на сам поликарбонатный лист, который желтеет, мутнеет, в итоге разрушается. С целью защиты материала и обустроенного с его помощью пространства внешняя сторона снабжается слоем, играющего роль надежного барьера от разрушающих лучей.
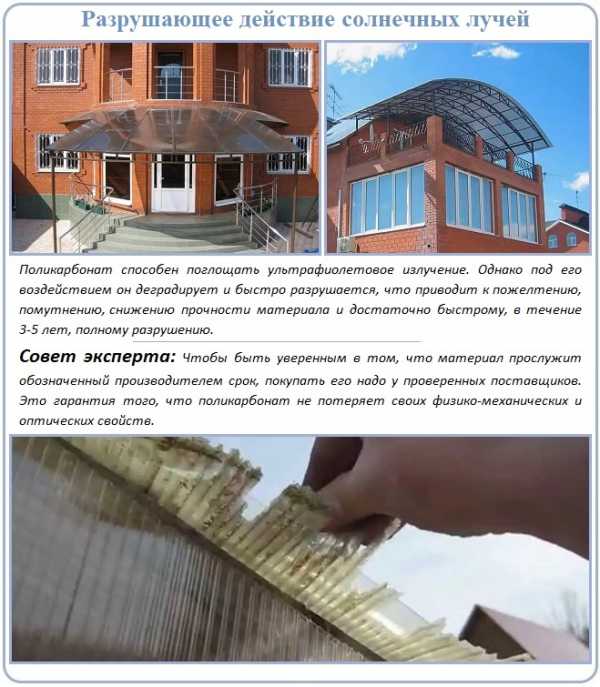
Раньше защитный слой выполнялся лаковым покрытием, к недостатком которого относилась неравномерность нанесения, способность растрескиваться и быстро мутнеть. Его и сейчас можно встретить на контрафактной продукции, так как у производителей подобных изделий нет ни оборудования, ни составов для выполнения правильной защиты от УФ.
Качественный поликарбонат не покрывается защитной оболочкой, она как бы вплавляется в его верхний слой. Метод подобного нанесения называется коэкструзией. В результате смешивания двух веществ на молекулярном уровне создается щит, непроницаемый для ультрафиолетового излучения.
Толщина созданного путем вплавления слоя всего лишь пара десятков микрон. По сути, он представляет собой тот же поликарбонат, но обогащенный УФ-стабилизатором. В ходе эксплуатации слой не трескается, не крошится и не осыпается, а верой и правдой служит владельцам ровно столько, столько эксплуатируется поликарбонатная панель.
Отметим, что наличие стабилизатора не определяется визуально, его наличие подтверждает только техническая документация от производителя, дорожащего собственной репутацией. Для того чтобы можно было определить эту вещество в поликарбонате, в процессе ее вплавления вносят еще и оптическую добавку.

Рассмотреть оптическую добавку можно под обыкновенной ультрафиолетовой лампой, но сам стабилизатор вы не увидите никогда. Поэтому лучше покупать материал в ответственных магазинах, закупающих поликарбонат у проверенных поставщиков. Только в этом случае «напороться» на контрафакт будет практически невозможно.
Еще запомните, что стабилизатор ультрафиолета не вносится на всю толщину листа. Такая концентрация просто нерациональна, да и цена бы на продукт выросла бы в сотни раз. Поэтому уверения продавца или изготовителя материала в том, что стабилизирующее вещество внесено на всю мощность, можно с полным основанием расценивать как обман и желание продать подделку.
Сторона, с которой вплавлен стабилизатор, обозначается на материале как «верхняя». Устанавливать поликарбонатные листы нужно только так, чтобы она создавала внешнюю поверхность и первой встречала солнечные лучи. Только в этом случае защита от ультрафиолета стопроцентно выполнить возложенные на нее обязанности.
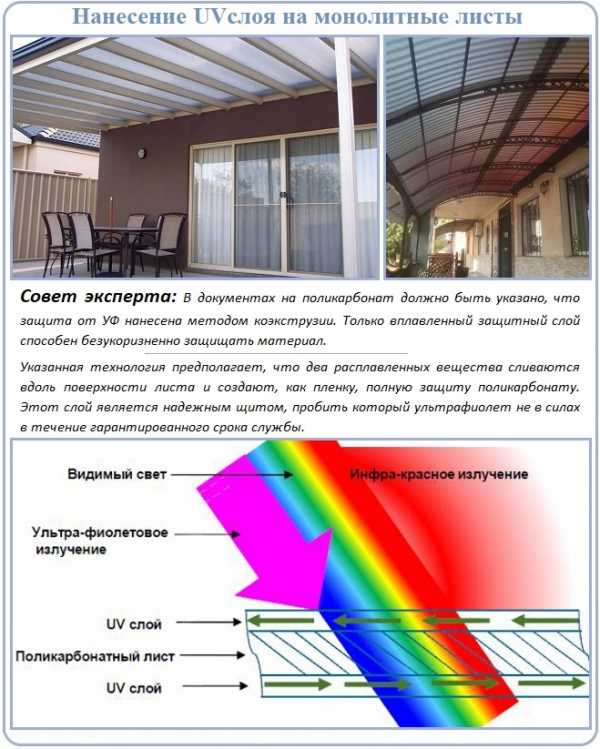
Добавка для рассеивания света
Способность рассеивать свет – свойство, весьма полезное в тепличном хозяйстве. Поэтому обращать на него внимание следует, если поликарбонатные листы покупаются для сооружения теплицы.
Светорассеивание обеспечивает более полный охват освещаемой территории за счет перенаправления солнечных лучей, гарантирует равномерность поставки света ко всем находящимся в закрытом объекте растениям. К тому же, рассеянные лучи внутри теплицы дополнительно отражаются от различных поверхностей, что еще дополнительно усиливает поток света.
Свойство распределять равномерно солнечные лучи у монолитных листов гораздо выше, чем у сотовых панелей. А так как в обустройстве теплиц используется преимущественно сотовый вариант, то о проценте светорассеивания нужно обязательно осведомиться у продавца или найти о нем информацию в паспорте продукта.

Нужно запомнить, что:
- У сотового прозрачного материала данное свойство обычно не превышает 70-82%.
- У непрозрачных цветных модификаций варьирует в пределах от 25 до 42%.
Преломлять и рассеивать свет поликарбонат начинает после введения в состав дифьюзера LD – микроскопических частичек, формирующих указанный эффект.
Эта добавка вносится при производстве прозрачных панелей, благодаря чему способность пропускать свет у монолитных листов повышается до 90% (данные для материала толщиной 1,5 мм). Ее добавляют при изготовлении белого поликарбоната, светопроводящая способность которого варьирует в итоге в диапазоне от 50 до 70%.
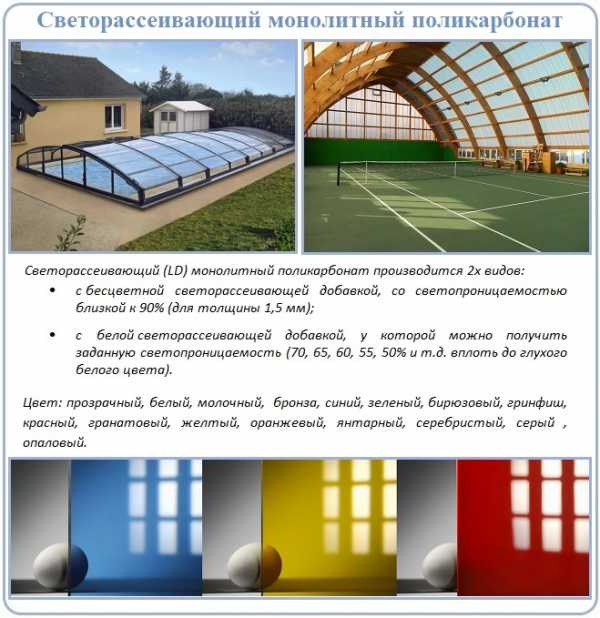
Введение ингибитора против горения
Как и все полимерные соединения, поликарбонат без использования специфических добавок будет поддерживать огонь. После внесения ингибиторов это качество ощутимо понижается. Монолитные листы и сотовые панели долго сопротивляются возгоранию и не выделяют отравляющих токсинов во время горения.
Стандартный монолитный поликарбонат относится к Г2 группе по параметрам возгорания, сотовый к Г1. Т.е. монолитные листы являются умеренно горючими, а сотовые панели слабогорючими.
По желанию заказчиков монолитные листы также могут быть изготовлены с соответствием требованиям группы Г1. Покупатель в этом случае должен получить сертификат на продукт с соответствующими характеристиками. По показателям воспламеняемости, способность распространять огонь и токсичности тоже могут быть вариации.
Исключение явления внутреннего дождя
Сотовый поликарбонат весьма популярен в сооружении теплиц, веранд, крытых павильонов для бассейнов, оранжерей, террас. Использование полимерных панелей практически исключает движение воздуха или существенно снижает его скорость. Ситуацию усугубляет специфический крепеж, используемый в строительстве, обеспечивающий герметичность.
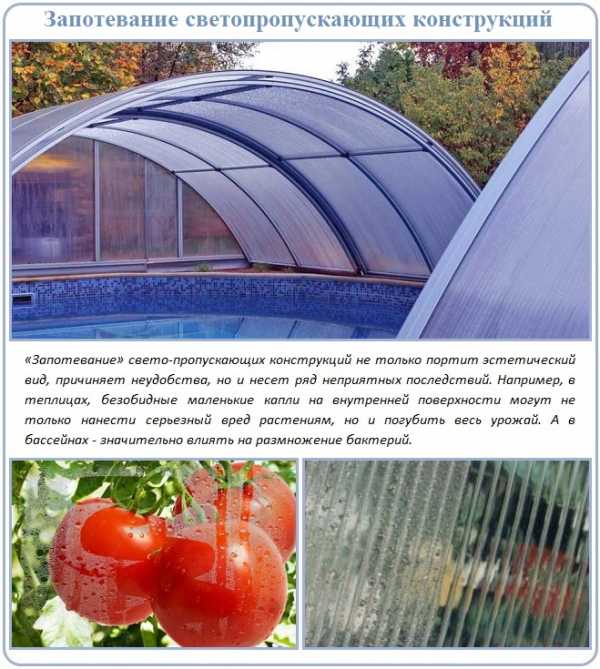
Несмотря на наличие вентиляционных компонентов в устраиваемых из поликарбоната конструкциях выпадение конденсата полностью исключить практически невозможно. Естественные испарения и конденсат оседают на внутренней поверхности, снижают светопроводимость.
Конденсат и парообразная вода отрицательно воздействуют на растения, способствуют их загниванию в герметичных теплицах. Негативное влияние оказывается на деревянные детали конструкций, на поверхности которых расселяется разрушительный грибок. В крытых бассейнах формируется нездоровая атмосфера.
Как устранить запотевание? Да нанесением противотуманного покрытия, получившего технический термин Антифог (против тумана). После его нанесения на внутренней поверхности поликарбонатных конструкций испарения и конденсат не задерживаются вследствие изменения натяжения на поверхности капель.

Многокомпонентный состав формирует условия для равномерного распределения воды по полимерной поверхности. Вода вступает во взаимодействие с ним, а не с соседними аналогичными молекулами. Испарения и конденсат в итоге не превращаются в крупные капли, создающие угрозу растениям и людям при выпадении, а быстро испаряются.
Учет термического расширения
Для того чтобы сооруженная с применением поликарбоната конструкция не деформировалась, необходимо учитывать, что в результате термического воздействия листы и панели способны увеличиваться в размерах.
Поликарбонатный стройматериал рассчитан на нормальную работу в температурном интервале от -40º С до +130º С. Естественно, при плюсовых значениях полимер будет изменяться в линейном направлении.
Учет теплового расширения обязателен на стадии разработки проекта, а сведения о линейном размере теплового расширения крайне важен для проектировщика.
Средние значения тепловых расширений для полимерных панелей составляет:
- 2,5 мм на каждый погонный метр для прозрачного, молочного материала для и продукции близких к молочному цвету светлых тонов;
- 4,5 мм для материала темного колорита: синих, серых, бронзовых образцов.
Кроме проектировщиков способность к тепловому расширению должна учитываться монтажниками, т.к. крепеж нужно устанавливать особым способом. Для того чтобы у листов и панелей была возможность двигаться, отверстия для саморезов сверлят больше диаметра их ствола, а также используют метизы с большими шляпками и компенсаторами.
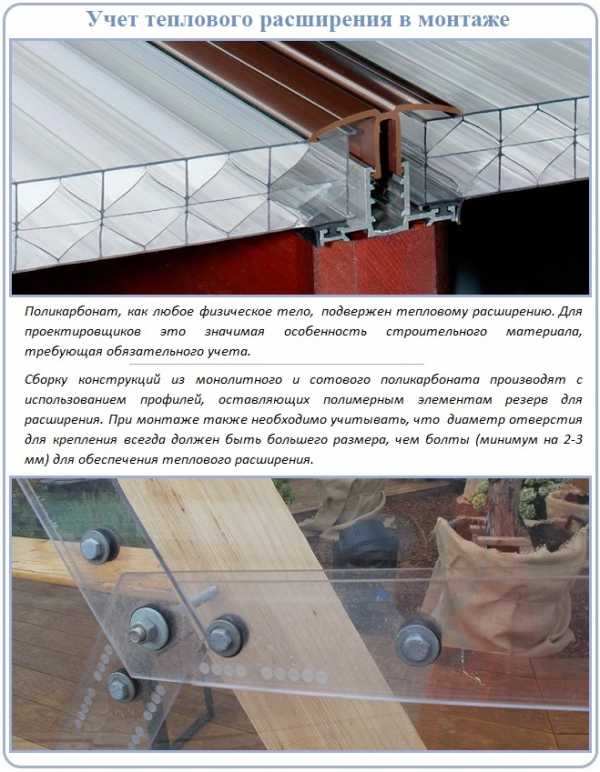
Сотовые панели и монолитные полимерные листы укладывают так, чтобы между ними оставался зазор. Тогда при расширении у полимерных элементов будет резерв, благодаря которому они не станут «выталкивать» друг дружку, упираясь краями. Зазор этот закрывает в конструкциях гибкий профиль.
Если при проектировании и сборке конструкций тепловое расширение учтено, сооружения без проблем прослужат больше, гарантированного производителем срока. Устроенные с помощью поликарбонатных листов и панелей компоненты не будут трескаться и крушиться от натяжения и переизбытка напряжения.
Самостоятельным домашним строителям также следует помнить о склонности полимерных листов и панелей к расширению при термическом воздействии, как прямом, так и косвенном, то есть происходящем в условиях повышения градуса в окружающем пространстве.
Видео № 1 поможет наглядно ознакомиться с видами поликарбоната и понять, в чем из отличия:
Видео №2 представит советы по выбору сотовых поликарбонатных панелей для сооружения теплицы:
Видео № 3 вкратце ознакомит с типоразмерами и сферой применения сотового поликарбоната:
Предложенная нами информация не просто знакомит заинтересованных посетителей с популярным стройматериалом и спецификой его применения.
Мы постарались вам объяснить, как выбрать достойный вашего внимания продукт, который прослужит гарантированный срок и, наверняка, гораздо дольше. Учет приведенных в описании критериев и советов необходим для достижения положительного результата, как в приобретении, так и в сооружении.
krovgid.com