обзор типов линий и установок
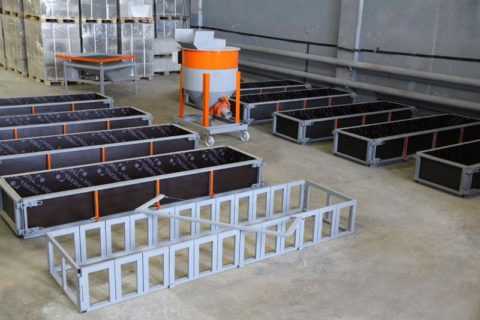
Производство блоков из газобетона
Еще не так давно, производство популярного материала в виде строительного камня было возможно лишь в условиях завода. Но с усовершенствованием технологий такая возможность появилась не только у мелких предпринимателей, но и у самих застройщиков.
На данный момент существует большое количество различного оборудования, предназначенного для изготовления данного представителя ячеистых бетонов. Комплекты отличаются между собой по ряду признаков, а в первую очередь ценовой категорией и объемом выпуска.
В данной статье мы будем рассматривать оборудование для производства газобетонных блоков разного типа, и проанализируем сам процесс изготовления изделий. А также сравним материал, произведенный в домашних и заводских условиях.
Содержание статьи
Общая технология производства газобетона
Предварительно, пожалуй, рассмотрим общий принцип технологического процесса. Ведь для полноценного обзора линий оборудования, нам нужно иметь представление о том, как именно изготавливается газобетонный блок.
Необходимое сырье
Для приготовления газобетонной смеси, понадобится наличие следующего сырья:
- Цемент марки не менее М400;
- Вода;
- Известь негашеная;
- Гипс;
- Песок кварцевый;
- Алюминиевая пудра.
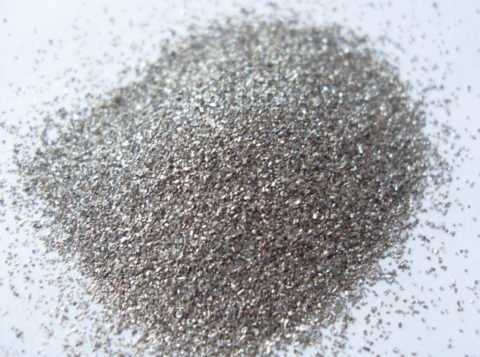
Алюминиевая пудра
Также не помешает добавить в раствор пластификатор. Основное его предназначение – повышение пластичности раствора, что предотвращает растрескивание изделий на стадии сушки и твердения.
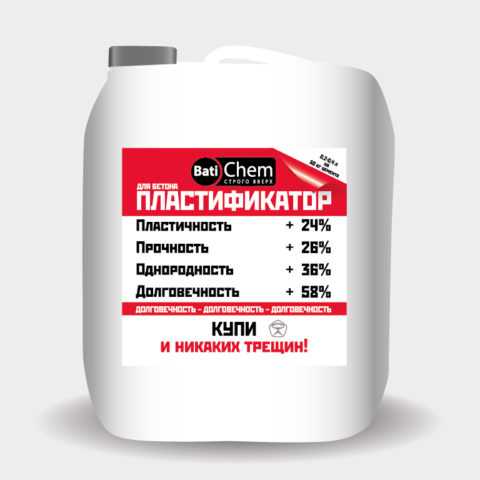
Пластификатор
Другие химические добавки также используются. Как правило, они добавляются с целью повышения качеств готовых изделий.
Пропорции сырья вместе с добавками
Обратите внимание! Вышеуказанный состав является классическим. Многие компоненты могут заменяться. В этом случае набор числовые значения свойств также будут варьироваться.
- Кремнеземистый компонент может быть представлен в виде: песка, золы и иных вторичных продуктов промышленности;
- Тип вяжущего также может быть разным: цементным, шлаковым, известковым, смешанным, зольным.
Примерное содержание пропорций – следующее:
- 50-60% — цемент;
- 20-40% — песок;
- 1-10% — известь;
- До 1% — вода.
На заметку! При желании повысить плотность изделий, следует увеличить количество цемента. В этом случае также изменится и масса готового материала, и коэффициент теплопроводности.
Пропорции в зависимости от желаемой плотности
Основные этапы
Краткая инструкция выглядит следующим образом:
- Первым делом взвешиваются компоненты и смешиваются в необходимых пропорциях. При изготовлении своими руками это делается вручную, в заводских условиях, как правило, в автоматическом режиме.
- Все ингредиенты попадают в смеситель, где и происходит смешивание.
- Следующим этапом станет формовка. Формы наполняются примерно на 1/3, так как при порообразовании смесь попросту может вытечь.
- Следом, после завершения процесса вспучивания, выжидается некоторое время до частичного застывания.
- Далее производят резку единого пласта или просто распалубку, если формы используются уже готовых типоразмеров.
- Последним этапом станет автоклавирование либо отправление блоков на сушку при неавтоклавном способе производства.
Обратите внимание! Ход процесса может несколько отличаться в зависимости от того, какое оборудование для изготовления газобетонных блоков используется. Однако в целом, общий принцип будет аналогичным.
Типы установок и линий
Теперь перейдём непосредственно к обзору типов оборудования.
Конвейерный тип
Оборудование для газобетона конвейерного типа отличается:
- Максимальной автоматизацией производства;
- Минимальным участием работников;
- Высокой стоимостью;
- Большими объемами производства;
- Полной комплектацией;
- И, как правило, наибольшей рентабельностью.
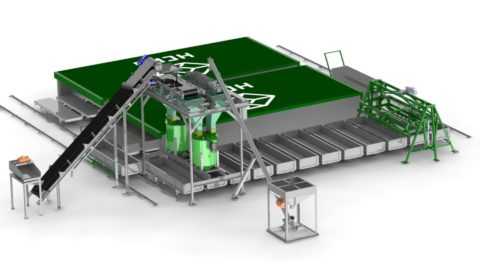
Большая конвейерная линия
Рассмотрим подробнее комплектацию и возможности такого газобетонного оборудования на примере линии популярного китайского производителя, являющегося дилером компании Премиум Кирпич Плюс.
В стандартный комплект входят:
- Емкости и бункеры для сырья;
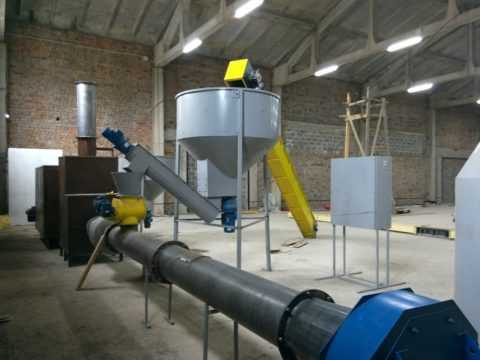
Бункер для сырья
- Ленточные конвейеры для транспортировки компонентов;
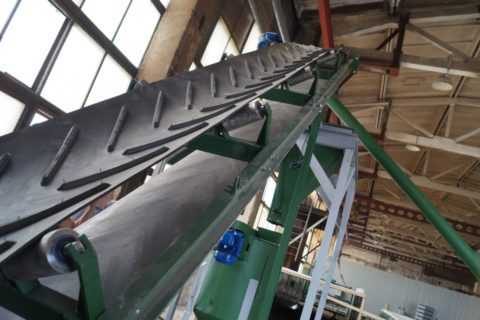
Ленточный конвейер
- Узел растворосмесительный;
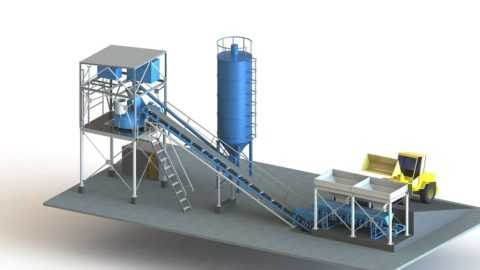
Узел бетоно-растворный
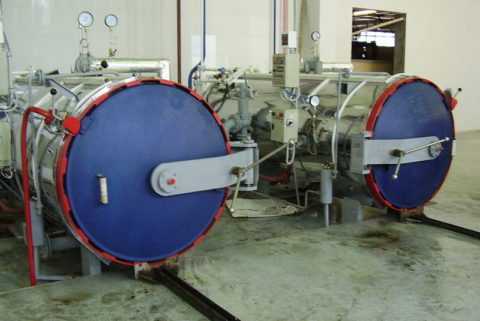
Автоклавы
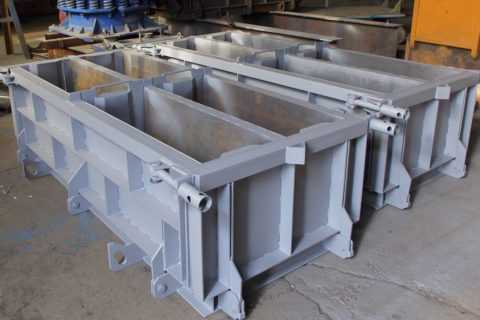
Сборная форма для блоков
- Резательный комплекс;
- Транспортер перемешивающий;
- Дробилки;
- Тележки;
- Узел для автоматического управления линией;
- Погрузчик вилочный.
Такое оборудование для производства стоит около 55 000 000. Согласитесь, сумма, не маленькая. Однако при этом, производительность составляет около 300 тысяч метров кубических в год. Площадь, необходимая для размещения такой линии должна быть около 4000 м2.
В качестве альтернативы, можно рассмотреть возможность приобретения конвейерной линии в бывшем употреблении. Это – своеобразный риск, однако стоимость ее значительно ниже.
Также стоит обратить внимание на мини линию конвейерного типа «Иннтех-100». Ее производительность значительно ниже и составляет 100 м3 в сутки. Цена ее – около 3 000 000.
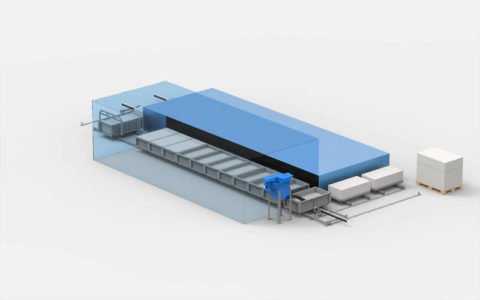
Мини конвейерная линия
Данная линия характеризуется неподвижным смесителем. Формы передвигаются по рельсовому транспортеру как тележка. Компоненты подаются и дозируются в автоматическом режиме. Резательный комплекс – механический.
Больше всего среди производителей ценятся линии известных немецких производителей оборудования. Они отличаются высокой продуктивностью, долговечность в использовании. С их помощью можно изготавливать блоки самого высокого качества.
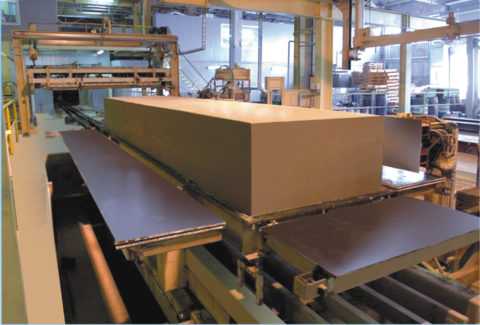
Немецкое оборудование для изготовления газоблока
Видео в этой статье продемонстрирует принцип работы оборудования для изготовления газобетона.
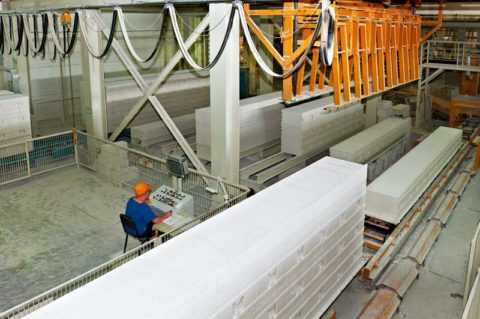
Производство газобетона Поревит
Стационарный тип
- Такой тип оборудования гораздо менее дорогостоящий. Однако и производительность ее гораздо ниже и составляет около 50 м3 в сутки.
- Как правило, в комплект таких линий входят дозаторы компонентов и ленточный транспортер, который и подает ингредиенты в смеситель.
- Однако полностью автоматизированным такой комплект назвать уже нельзя. Для полноценной работы требуется наличие как минимум нескольких человек.
- Необходимая квадратура для размещения производства и склада составляет около 500 м2.

Линия стационарного типа для производства газобетонного блока
В качестве примера, кратко рассмотрим комплектацию и возможности линии АСМ-1МС.
- Производительность составляет около 60 м3;
- Для работы потребуется привлечение 3-4-х человек;
- Песок и цемент подаются в автоматизированном режиме.
Комплектация:
- Смеситель для вяжущего и иных компонентов;
- Конструкция для резки блочного массива с пилами;
- Формы и поддоны;
- Транспортер.
Мобильные установки и мини-линии
Такое оборудование для производства блоков газобетонных идеально подойдет для начинающих предпринимателей либо застройщиков, желающих изготовить изделия для собственных нужд.
При помощи мобильной установки можно произвести исключительно только газоблок неавтоклавного твердения. Ниже мы рассмотрим основные его отличия от основного конкурента.
Такой оборудование требует наличия сети в 220 Вт, в то время как другие типы машин требуют подключения к сети в 360 Вт. Объем производства составляет около 2-10 м3 в сутки.
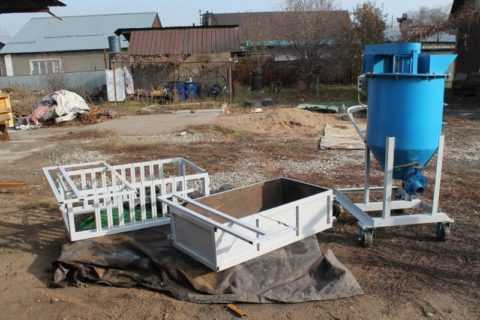
Установка мобильная для изготовления газобетона
Рассмотрим характеристики установки на примере комплекта Газобетон 500Б.
Установка газобетон 500 Б
- В комплект входит: смеситель, соединительные рукава и компрессор. Для производства необходимо участие нескольких человек.
- Практически весь процесс работ происходит с участие человека. В автоматическом режиме производится только смешивание.
- Дозирование также придется производить самостоятельно.
- Объем выпуска 3 м3 пористой смеси.
- Емкость для смешивания- 500 литров.
Мини-линии более производительны. С их помощью возможно изготовление вплоть до 25 м3 в сутки. Для мелких предпринимателей – отличный вариант начать свое дело.
Принцип их устройства – аналогичен мобильным установка, больше – мощность и объем смесителя.
Подробнее об автоклавировании
Теперь давайте более подробно поговорим об автоклавной обработке газоблока и разберемся, в чем заключаются основные различия между изделиями самостоятельного производства и материалом, выпущенным в условиях завода.
Что представляет собой автоклавная обработка?
При помощи автоклавной обработки удается повысить качества готовых изделий.
- Разрезанные на типоразмеры блоки помещаются в автоклав и обрабатываются под действием давления выше атмосферного водяным паром, при этом преобладает высокая температура.
- Обработка длится в течение 12-ти часов.
- По окончании обработки, блоки практически сразу можно использовать в строительстве, ведь марочной прочности они уже достигнут.
- Неавтоклав же набирает прочность в течение 4-х недель.
- При автоклавной обработке повышаются такие качества как: прочность, плотность, долговечность. Изделия становятся менее хрупкими
Стоит отметить, что изготовление блоков автоклавного твердения возможно только в заводских условиях.
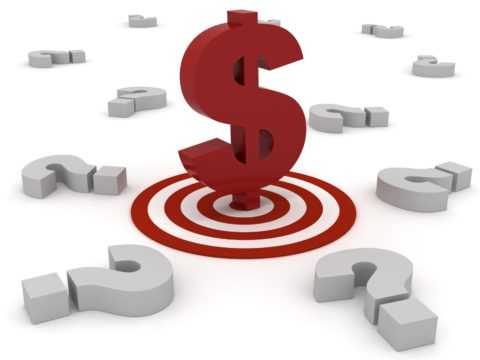
Процесс автоклавирования
Сравнение автоклавного и неавтоклавного газоблока
А теперь сравним свойства автоклавного газобетона и изделий, достигающий прочности естественным способом.
Характеристика | Сравнительный анализ |
![]() Сочетание плотности и теплопроводности | За счет специализированной обработки в автоклаве, изделия синтезного твердения отличаются лучшим сочетанием показателей плотности и теплопроводности. |
![]() Морозостойкость и долговечность | В соответствии с ГОСТ, требования к марке по морозостойкости к неавтоклавному блоку несколько ниже. Точные сроки долговечности обоих изделий не установлены опытным путем, в силу недостаточного времени существования материала на рынке строительных материалов. |
![]() Внешний вид и геометрия изделия | Автоклав имеет практически идеальную геометрию. Неавтоклавный блок, изготовленный в домашних условиях в данном отношении серьезно ему уступает. |
![]() Требования к оборудованию и сложность производства | Оборудование для газобетона автоклавного, в целом, отличается лишь наличием автоклавов. Технология производства – аналогична, порядок – тоже. |
![]() Хрупкость | Неавтоклавные блоки больше уязвимы к механическому воздействию, они более хрупкие. |
![]() Стоимость | Автоклавные изделия дороже примерно на 10%. |
![]() Усадка | Неавтоклавные блоки больше подвержены усадке. Показатель составляет до 1 мм/м2. |
В заключение
На современном рынке существует большое количество различных комплектов оборудования для производства газ
beton-house.com
Мы на You Tube![]() Услуги предприятияСамое популярноеНовости
|
Видео запуска автоматизированного завода по производству газобетона В Казахстане Газобетон (строительный материал) – популярный в строительной сфере материал, прочный, но достаточно легкий. Для его изготовления требовались промышленные мощности, но сегодня технологии меняются. Появляется модернизированное оборудование для производства газобетона, которое позволяет производить его в рамках небольших производств, а некоторые модели – в домашних условиях. Оборудование для изготовления газобетона можно условно разделить на 5 основных категорий:
Купить оборудование для производства блоков можно на нашем сайте. Мы являемся производителями, поэтому готовы при необходимости предоставить вам сертификаты качества и гарантии. Если вам требуется подробная консультация по техническим вопросам, помощь при выборе модели – звоните нам по телефону, у наших сотрудников есть ответы на все вопросы. |
metembeton.ru
Необходимое оборудование для производства газобетона
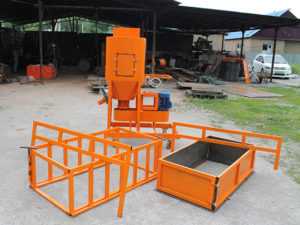
Мини-завод по производству неавтоклавного газобетона
Раньше изготовление газобетонных изделий было только на заводах. Теперь оборудование для производства газобетона может устанавливаться на небольших площадках или даже во дворе собственного дома.
В зависимости от количества необходимых блоков можно приобрести оборудование в виде мини-завода, поставить мобильную установку для получения блоков различной плотности.
Технология получения газобетона
Газобетон относится к разряду ячеистых бетонов. Состоит он из смеси нескольких компонентов:
- песок — 20-40%;
- известь — 1-5%;
- цемент — 50-70%;
- вода чистая — 0,25-0,8%;
- пудра алюминиевая — 0,04-0,09%.
Песок используется просеянный, его фракции не превышают 2,1 мм. Глины в нем должно содержаться не больше 7%. Цемент нужен качественный — марки М400 или М500. Алюминиевая пудра применяется в качестве газообразователя. В состав могут включаться еще некоторые компоненты: пластификаторы, ускорители твердения. Для изменения свойств газоблоков в смесь добавляют шлак, гипс или опилки. Этими добавками можно изменить плотность блоков. Ведь материал для изготовления фундамента должен быть прочнее, чем для перегородок. Теплоизоляционные блоки желательно делать более легкими и пористыми. Для этого можно полностью исключить из его состава песок.
Производство газобетонных изделий бывает автоклавное и неавтоклавное. Второй вариант производится гораздо проще, но имеет низкую прочность, недостаточную точность геометрических размеров. Автоклавные изделия бывают обычно более однородной структуры и низкой теплоемкости. Такие блоки используются в условиях России для возведения стен толщиной до 400 мм.
Изготовление блоков
Для производства газоблоков не требуются особо сложные установки. Нужно лишь точное выполнение технологических циклов. Изготовление может выполняться в следующем порядке:
- подготовка компонентов;
- введение газообразователя;
- укладка раствора в формы;
- разрезание блоков;
- созревание изделий;
- автоклавирование.
Все необходимые компоненты взвешиваются и всыпаются для перемешивания в смеситель. Минут через 10-15 к ним добавляют алюминиевую пудру, которая сразу же вступает в химическую реакцию с находящейся в смеси известью. В результате реакции смесь наполняется газом в виде пузырьков по всему объему. Это является сигналом к выкладке раствора в формы для газобетона или на специальный лоток толстым слоем. На лотке производят разрезку массы на блоки особыми пилами. Созревают полуготовые блоки в течение 10-18 часов. После этого блоки помещаются в автоклав. Это особая печь, состоящая из герметичной камеры с температурой 190°C. В ней материал обрабатывается горячим паром под высоким давлением. Далее готовый материал вынимается из автоклава и раскладывается для просушки.
Неавтоклавный строительный материал просушивается в течение 3-7 суток естественным образом. Далее блоки складируются в помещение для набора полной прочности. Происходит это обычно 30 суток. Только по истечении этого срока можно перевозить газобетон к потребителю, упаковав его в специальную термоусадочную пленку.
Оборудование для изготовления блоков
Для газобетонных блоков обычно комплектуется технологическая линия, состоящая из:
- смесителя;
- активатора;
- дозатора;
- режущего приспособления;
- автоклава;
- форм.
Все это оборудование бывает разной мощности. Она обычно варьируется в пределах 10-150 м³ в сутки. Самое дорогое в этом наборе — автоклав. От него и зависит стоимость готового продукта. В домашних условиях это производство чаще всего становится нерентабельным.
Оборудование можно разделить на такие виды:
- стационарная линия;
- конвейерная линия;
- мини-линия;
- мини-завод;
- мобильная линия.
Стационарная линия оборудования для газобетона может производить от 60 м³ продукции в сутки. Для ее складирования требуется примерно 500 м² площади. С управлением линией вполне справятся 2 человека.
Конвейерная линия может выпускать за сутки 75-150 м³ готовой продукции. Размещения оборудования для производства газобетонного блока требует площади более 600 м². Обслуживают его 8 человек.
Мини-линия рассчитана на суточный выпуск около 15 м³ изделий. В состав линии входит смеситель и формы. Для организации производства и установки оборудования требуется 2 человека и 140-160 м² площади.
Установка мини-завода гарантирует выпуск готовых блоков от 25 м³ в сутки. Это немного больше, чем с помощью мини-линии. Отличает мини-завод лишь наличием в его составе поддонов, бака с водой, оборудования для разрезания газобетона.
Мобильные линии часто используются при строительстве личных домов. Они позволяют снизить расходы на треть. Для получения качественного газобетона оборудование подключается к розетке 220 В. В составе линии может быть:
- неподвижный смеситель;
- передвижные формы для заливки раствора;
- установка для разрезания блоков.
Производительность линии достигает 100 м³ в сутки.
Заключение по теме
На протяжении многих тысячелетий человек строит для себя жилье. За эти годы значительно изменились технологии и материалы для строительства. В наше время актуальным стало строительство с использованием газобетона в виде блоков. Раньше блоки выпускались только на заводах, сегодня их производство можно наладить дома. Для этого нужно иметь желание, приобрести оборудование и установить все это на подготовленной площадке. Для выпуска газобетона нужно иметь чистую теплую воду, кварцевый песок, алюминиевую пудру марки ПАП-1, известь, портландцемент М400 или М500 и еще несколько добавок для улучшения качества продукции. Получив все это, можно начинать собственный бизнес по выпуску стройматериалов, имеющих большой спрос. При строительстве собственного дома материал сократит расходы примерно на треть.
Для собственного производства лучше всего приобрести небольшую стационарную линию, с помощью которой можно делать неавтоклавный газобетон. Обслуживать установку могут 2 человека. При таких силах можно ежесуточно выпускать около 60 м³ отличных блоков. Каждый такой искусственный камень весит примерно 30 кг и заменяет собой около 30 стандартных кирпичей. Газоблок весит в несколько раз легче кирпича, поэтому не требует строительства капитального фундамента и использования грузоподъемной техники. Материал отлично обрабатывается ручными инструментами: пилой, стамеской, сверлом. В наше время газобетон занимает ведущее место среди других строительных материалов.
kamedom.ru
Оборудование для производства автоклавного газобетона
Автоматизированная линия для производства стеновых и перегородочных блоков из автоклавного газобетона по прогрессивной виброударной технологии.
Краткие характеристики оборудования для производства автоклавного газобетона
- Максимальная производительность (по заливке) – до 250 м3 готовой продукции в сутки.
- Расчетная производительность — до 200 м3 готовой продукции в сутки.
- Готовая продукция — блоки стеновые и перегородочные с маркой по средней плотности D400-D600 с прочностью на сжатие В2-В3,5.
- Объем массива – 1 м3 .
- Время заливки одного массива — около 6 минут.
- Время выдержки массива до резки — 3 — 4 часа.
- Время автоклавной обработки — 12 часов.
- Складской запас цемента — 120 т.
- Складской запас наполнителя — 120 т.
- Установленная мощность оборудования — 240 кВт. (без участка помола)
- Потребление воды — 50 т воды в сутки.
- Обслуживающий персонал — 11 человек.
- Условия размещения — в помещении цехового типа при отсутствии атмосферных осадков и температурой не менее +5 0С.
- Площадь цеха не менее 2500м2.
- Высота в зоне заливки 8,5м.
- Высота остального помещения не менее 4,5м.
Отличительные особенности наших линий по производству автоклавного газобетона
Все основное оборудование располагается на площади 2,5 тысячи кв. метров. Это позволяет поставить завод практически в любом месте, где есть коммуникации, например, рядом со строительной площадкой, производством вяжущего или карьером песка.
- МАЛЫЕ КАПИТАЛОВЛОЖЕНИЯ
Относительно небольшая производительность не требует строительства сложной инфраструктуры (железнодорожная станция, разгрузочные терминалы, административные и вспомогательные помещения и т.д.) Все необходимые сырьевые материалы комфортно доставляются автомобильным транспортом.
- БЫСТРАЯ ОКУПАЕМОСТЬ
Небольшие капитальные затраты, короткий срок запуска предприятия и высокое качество продукции позволят сократить срок окупаемости проекта до 1,5 года.
- КАЧЕСТВО ПРОДУКЦИИ
В проектировании оборудования учитывался весь имеющийся мировой опыт производства автоклавного ячеистого бетона. Газобетонные блоки, выпущенные на нашей линии, соответствуют самым жестким мировым стандартам, как по физико-химическим свойствам, так и по геометрии.
- АВТОМАТИЗАЦИЯ
Все элементы оборудования полностью автоматизированы. Главные пульты оснащены сенсорными панелями управления, работают функции учета и контроля. Автоматическая система управления работает на базе промышленной линейки японских контроллеров от мировых лидеров Mitsubishi и Omron.
Сырье для производства блоков из автоклавного газобетона
- ВЯЖУЩИЕ МАТЕРИАЛЫ
— портландцемент по ГОСТ 31108 и ГОСТ 10178 без добавок трепела, глиежа, трассов, глинита, опоки, пеплов, содержащий трехкальциевый алюминат (С3А) не более 8 % по массе.
Сроки схватывания: начало — не ранее 2 ч, конец — не позднее 4 ч;
— высокоосновная зола, содержащая СаО не менее 40 %, в том числе свободный СаО — не менее 16 %, SО3 — не более 6 % и R2О — не более 3,5 %;
— известь негашеная кальциевая по ГОСТ 9179, быстро- и среднегасящаяся, имеющая скорость гашения 5-25 мин и содержащая активные СаО + МgО не менее 70 %, «пережога» — не более 2 %.
- КРЕМНЕЗЕМНИСТЫЕ КОМПОНЕНТЫ
— природные материалы — кварцевый песок, содержащий SiO2 не менее 85 %, илистых и глинистых примесей не более 3 %, монтмориллонитовых глинистых примесей — не более 1,5 %;
— вторичные продукты промышленности и энергетики: золы-унос теплоэлектростанций, продукты обогащения различных руд, продукты собственного производства («горбушки», обрезки).
- ДОБАВКИ ДЛЯ РЕГУЛИРОВАНИЯ И УЛУЧШЕНИЯ СВОЙСТВ АВТОКЛАВНОГО ГАЗОБЕТОНА
— добавки по ГОСТ 24211;
— доменные гранулированные шлаки по ГОСТ 3476;
— гипсовый камень по ГОСТ 4013.
- ГАЗООБРАЗОВАТЕЛЬ
— алюминиевая пудра или паста на основе алюминиевой пудры
- ВОДА по ГОСТ 23732.
Подготовка и складирование сырья
ВЯЖУЩИЕ (цемент, известь) из цементовозов или прижелезнодорожного разгрузочного устройства при помощи компрессорной установки пневмо-транспортом загружаются в расходные силосы.
ДОБАВКИ (жидкие) заливаются в специальные емкости, где они перемешиваются с водой и доводятся до необходимой температуры, сухие добавки дозируются в мельницу вместе с песком.
НАПОЛНИТЕЛЬ (песок) подается в шаровую мельницу мокрого помола и после этого поступает в специальный шламовый бассейн. В этот же бассейн поступает подготовленная водная смесь из отходов производства (обрезки, горбушки).
ГАЗООБРАЗОВАТЕЛЬ (алюминиевая пудра или паста) загружается в отделение суспензиатора для приготовления водной суспензии.
Смешивание компонентов
Смешивание всех сухих и жидких компонентов происходит в несколько этапов.
На центральном пульте управления заводом производится контроль, обработка и управление всеми важными функциями установки на всех этапах приготовления газобетонной смеси.
Управление всем процессом смесеприготовления осуществляется с пульта управления, расположенного под смесительной башней и рядом с постом заливки смеси в формы.
Дозировка компонентов и процесс смешивания газобетонной смеси происходят полностью автоматически и контролируются компьютером управления, в котором заложены программы рецептов для получения ячеистого бетона требуемого качества.
Оператор в режиме реального времени отслеживает все процессы работы установки. В случае необходимости оператор за короткое время может скорректировать или изменить текущий состав, время перемешивания, температурный режим и другие технологические параметры на электронной панели главного пульта или при помощи компьютера. Также оператор может перевести работу установки в полуавтоматический или ручной режим управления.
Резка блоков автоклавного газобетона
Резка газобетонных массивов осуществляется на резательных станках Риф-1 или на струнном резательном станке.
Автоклавная обработка массива занимает 12 часов и состоит из четырех этапов:
— вакуумирование;
— подъем давления;
— изотермическая выдержка;
— сброс давления и подготовка к выгрузке.
В зависимости от состава смеси, в процессе изотермической выдержки поддерживается температура от 180 до 193 С, давление от 8 до 13 бар.
Управление процессами автоклавной обработки происходит на специальном пульте управления в автоматическом режиме.
Транспортировка автоклавных блоков
Пройдя этап автоклавной обработки, разрезанный массив на тележке выкатывается на разборку. Блоки укладываются на транспортировочные поддоны, стягиваются скреплентой и при помощи погрузчиков подаются на складскую площадку или в складское помещение.
www.promcompany.ru