Технология производства пенопласта | Delo1
Пенопласт полистирольный ГОСТ 15588-86 (скачать 102К)
Пенополистирол — белое однородное вещество, имеющее структуру из склеенных между собой шариков, упругое на ощупь, не имеет запаха, является отличным тепло — звуко изолятором.
ПЕНОПОЛИСТИРОЛ — экологически чистый, нетоксичный, тепло- и звукоизоляционный материал, применяемый в строительстве на протяжении уже более 60 лет.
Пенополистирол является нейтральным материалом, не выделяющим никаких вредных для человека и его окружения веществ, не подвержен разложению под воздействием микроорганизмов и не имеет ограниченного срока годности (100 лет минимум).
Пенополистирол производят в огнестойком (самозатухающем) исполнении.
Горючесть пенополистирола по ГОСТ 15588-86 | |
1.![]() | 85 — 90°C |
2. Начало плавления | 240°C |
3. Начало процесса термодеструкции пенополистирола с выделением газообразных продуктов | 280-290°C |
4. Температура возможного воспламенения пенополистирола | 360-380°C |
Влага не влияет на теплоизолирующие свойства этого материала и не вызывает образование в нем бактерий и плесени, что позволяет широко использовать пенополистирол также и в пищевой промышленности.
Пенополистирол отлично переносит присутствие асфальтовых эмульсий, рубероида с асфальтовым покрытием, цемента, гипса, извести, воды и всякого рода грунтовых вод. Температура окружающей среды не оказывает отрицательного влияния на физические и химические свойства пенополистирола
Пенополистирол очень хорошо «держит» тепло. Закладка пенополистирола в наружные стены жилых домов позволяет в несколько раз снизить теплопотери. 12 см пенопласта соответствуют по своей теплопроводности: 50см дерева, 180см кирпича, 4м бетона!
Пенопласт (пенополистирол) применяется:
Для тепловой изоляции в качестве среднего слоя ограждающих конструкций при утеплении жилых домов, складов, гаражей, дач, при текущем и капитальном ремонте жилых и производственных зданий и сооружений, при строительстве ангаров, боксов, крытых площадок. Пенополистирол также незаменим при утеплении трубопроводов, овощехранилищ, промышленных холодильниках, транспортных вагонах, автофургонов, для упаковки продукции при транспортировке, для теплоизоляции наклонной кровли.
1. Вспенивание (однократное или многократное).
Гранулы ПСВ попадая в камеру предвспенивателя, вспениваются (надуваются) превращаясь во всем хорошо знакомые шарики. При многократном вспенивании уже вспененные гранулы подаются еще раз в камеру предвспенивателя, где они еще больше увеличиваются в размере (надуваются). Многократное вспенивание нужно, если Вам необходимо получить пенопласт низкой плотности. Например, для пенопласта с фактическим весом 12 кг, достаточно однократного вспенивания, а если нужен пенопласт с фактическим весом ниже 12 кг, то потребуется вспенивать гранулы дважды или трижды. Причем перед каждым вторичным вспениванием гранулы должны вылежаться 12 — 24 часа в бункере вылеживания.
2. Вылеживание.
3. Формовка.
После бункера вылеживания гранулы засыпаются в блок форму, где под действием пара происходит формовка блока пенопласта. Расширяясь в замкнутом пространстве, шарики пенопласта «склеиваются» между собой образуя монолитный блок.
4. Резка.
После того, как блок пенопласта достали из формы его необходимо выдержать не менее суток, перед тем как резать. Это обусловлено тем, что блок пенопласта выходит из блок-формы, как и гранулы из предвспенивателя, влажным, а иногда и просто мокрым. Если же резать мокрый
Упрощенная технологическая схема производства пенопласта.
Исходные материалы и ресурсы для производства пенопласта:
— полистирол суспензионный вспенивающийся типа ПСВ-С
— вода
— электроэнергия
— пар (парогенератор может быть электрическим, газовым или дизельным)
Схема химических процессов производства пенополистирола | ||
Производство пенопласта — безотходное: весь некондиционный материал дробится и добавляется к предварительно вспененному полистирольному грануляту перед формованием его в блоки пенопласта в количестве 5-10% от свежего сырья.
Для лучшего представления о технологии производства пенополистирола Вы можете посмотреть видео ролик.
Технология производства пенопласта (пенополистирола) — ООО «ПК ВикРус»
Главная / Технология производства пенопласта (пенополистирола)Содержание:
- Предварительное вспенивание гранул.
- Кондиционирование предварительно вспененных гранул.
- Формование пенополистирольных блоков.
- Кондиционирование пенополистирольных блоков.
- Разрезание пенополистирольных блоков на плиты.
- Использование пенополистирольных отходов.
1. ПРЕДВАРИТЕЛЬНОЕ ВСПЕНИВАНИЕ
В качестве сырья используется вспениваемый самозатухающий полистирол, содержащий 5-6% смеси пентана и изопентана, являющейся вспенивающим фактором. Эта смесь содержится в гранулах полистирола в растворенном виде.
Сырье имеет вид гранул, получаемых путем суспензионной полимеризации стирола. Оно содержит вещество, снижающее горючесть -антипирен.
После подогрева до температуры 90-100°С, под действием улетучивающегося пентана гранулы увеличивают свой объем (процесс вспенивания) примерно в 30-65 раз. В промышленной практике для вспенивания полистирола используется водяной пар, который проникает также внутрь гранул и способствует действию пентана.
Международное обозначение вспениваемого полистирола: EPS самозатухающий FS.
Хранение:
Хранить исключительно в заводской, плотно закрытой таре или контейнерах, установленных в проветриваемых помещениях или под навесом, далеко от источников тепла и огня. Рекомендуется хранить сырье при температуре, не превышающей 20°С.
Продукт, хранимый при рекомендуемой температуре, следует использовать не позднее 3-6 месяцев с даты исследования продукта, указанной в сертификате качества. Продукт из частично опорожненной или поврежденной тары следует использовать немедленно.
В производственных помещениях можно хранить сырье в количестве, не превышающем его среднесуточный расход.
1.2. Переработка вспениваемого полистирола .
Окончательная плотность готового продукта определена уже на этапе предварительного вспенивания.
Важным показателем является контроль давления при процессе вспенивания, для непрерывных предвспенивателей 0,015-0,03 МПа, для циклических 0,015-0,02 МПа.
Во вспенивателе два способа изменения мнимой плотности продукта:
- путем изменения количества подаваемого сырья;
- путем изменения уровня вспениваемого материала в рабочей камере;
Первый и второй способ оказывают влияние на время нахождения вспениваемого материала в рабочей камере. Третий способ влияет на температуру в камере.
Влияние времени нахождения сырья во вспенивателе на мнимую плотность продукта представлено на рис.1.2.
Если время нахождения сырья во вспенивателе слишком продолжительно, то гранулы начинают усаживаться и плотность растет; при слишком высокой температуре вспененные гранулы могут образовать комки. Оба эти явления могут происходить одновременно. И оказывать непосредственное влияние на качество конечного продукта.
Плотность
Продолжительность предварительного вспенивания
Рис.1.2. Зависимость между мнимой плотностью и продолжительностью вспенивания
С целью получения низкой плотности (< 12 кг/м3) применяют двухступенчатое вспенивание. Двухступенчатое вспенивание проводят с помощью того же самого оборудования, которое используется для одноступенчатого вспенивания, с подачей предварительно вспененного сырья через систему вторичного вспенивания.
С целью достижения оптимальных результатов вспенивания гранулы перед вспениванием второй ступени должны быть насыщены воздухом (процесс кондиционирования).
Предварительно вспененные гранулы поступают в сушилку с кипящим слоем, в которой теплый воздух (темп. примерно 30-40°С) проходит через перфорированное днище сушилки, сушит и продвигает гранулы в направлении выгрузочного вентилятора.
Воздушная струя должна распределяться таким образом, чтобы процесс сушки и перемещения гранул протекал равномерно по всей длине сушилки (регулировка осуществляется с помощью заслонок в воздушных камерах сушилки).
Одним из чрезвычайно важных факторов, оказывающих влияние на вспенивание полистирола, является продолжительность хранения сырья. Чем старше сырье, тем продолжительнее вспенивание и тем труднее достичь требуемой мнимой плотности вспененных гранул. Поэтому срок хранения сырья в герметичной упаковке ограничен до шести месяцев.
1.3. Техническое оснащение узла предварительного вспенивания
a) вспениватель ВП-03
b) система вторичного вспенивания СВВ-1
c) поточная сушилка гранул СС-106
d) выгрузочный вентилятор ВПВ-2,5
2. КОНДИЦИОНИРОВАНИЕ ПРЕДВАРИТЕЛЬНО ВСПЕНЕННЫХ ГРАНУЛ
2.1. Основы процесса кондиционирования гранул
В ходе кондиционирования воздух проникает внутрь вспененных гранул вследствие образовавшегося в них вакуума, а из вспененных гранул в атмосферу выпускается влага в виде пара и пентан, не прореагировавшие остатки процесса полимеризации сырья. Указанный газообмен возможен благодаря газопроницаемости полистироловых оболочек.
Рис.2.1. Гранулы вспениваемого полистирола в процессе кондиционирования
Скорость диффузии воздуха внутрь гранул обусловлена, главным образом, мнимой плотностью, температурой окружающей среды и размером гранул. Целью удаления влаги с поверхности гранул в сушилке с кипящим слоем является получение 100% мнимой поверхности, через которую осуществляется газообмен.
Скорость испарения пентана также зависит от плотности, температуры окружающей среды и размера гранул. Из крупных гранул пентан испаряется медленнее, чем из гранул малого диаметра, что обусловлено соотношением между поверхностью гранулы и ее массой.
2.2. Техническое оснащение узла кондиционирования гранул
Силосы, используемые для кондиционирования вспененных гранул, изготовляются в виде легкой металлической конструкции стеллажного типа с контейнерами из ткани, пропускающей воздух.
При перемещении вспененных гранул с помощью струи воздуха, на поверхности гранул накапливаются сильные электростатические заряды. Поэтому чрезвычайно важно тщательно заземлить все металлические элементы силосов, транспортных трубопроводов и остального оборудования.
2.3. Параметры кондиционирования гранул
Температура окружающей среды в цехе кондиционирования гранул не должна быть ниже 15°С, при более низкой температуре продолжительность кондиционирования увеличивается. В летний период, при температуре свыше 20°С время кондиционирования сокращают, а при более низких температурах — продлевают.
При транспортировке свежих гранул в силосы, их мнимая плотность увеличивается в результате столкновений со стенками трубопровода. Поэтому при установке параметров вспенивания необходимо учитывать увеличение плотности при транспортировке.
3. ФОРМОВАНИЕ ПЕНОПОЛИСТИРОЛЬНЫХ БЛОКОВ
3.1. Характеристика процесса формования
При выработке блоков вспененные гранулы свободно засыпают в камеру формы до ее полного наполнения. Затем в форму подают насыщенный сухой водяной пар под давлением 0,2-0,4 МПа, что приводит к дальнейшему увеличению объема гранул. В связи с тем, что гранулы находятся в закрытой камере, сначала заполняется свободное пространство между ними, а затем гранулы сцепляются друг с другом.
1) наполнение 2) продувание 3) запаривание 4) охлаждение 5) расформовка
Рис.3.1.2. Пример фазового цикла формования блоков с использованием вакуума
1) наполнение 2) вакуум 3) продувание 4) запаривание — рост | 5) запаривание — выдержка 6) выпуск 7) вакуумное охлаждение 8) разгрузка |
Важным фактором при запаривании блока является подача в камеру в свободное пространство между гранулами соответствующего количества пара в кратчайшее время. Для этого необходима соответствующая вентиляция (продувание), целью которой является удаление воздуха перед началом процесса запаривания. Недостаточная продолжительность продувания приводит к неоднородной плотности и плохому спеканию блока.
Важно также поддерживать постоянную высокую температуру формы, в противном случае значительно растет расход пара (рис.3.1.3) и пар становится мокрым, что снижает качество сцепления гранул.
Рис.3.1.3. Примерный расход пара в зависимости от температуры формыДавление, которое блок оказывает на внутренние стенки формовочной камеры, составляет примерно 0,08 МПа. Для того, чтобы блок можно было вынуть из формы без его повреждения, это давление необходимо уменьшить до величины около 0,01 МПа. Время, необходимое для уменьшения давления блока, то есть время охлаждения, зависит от марки пенопласта. Рис.3.1.4. Примерное время охлаждения блока в зависимости от продолжительности кондиционированияВ фазе продувания и охлаждения применяется вакуум с целью интенсификации процесса запаривания и ускорения процесса охлаждения.3.2. Техническое оснащение узла формования
a) блок форма УЦИП 1030.
b) установка вакуумирования ВУ-3,3 с аккумулятором вакуума АВ-1.
c) система вакуумной загрузки и охлаждения блоков.
d) компрессорная установка СБ4/Ф-500
e) аккумулятор пара ПН-5000
f) котел паровой
4. КОНДИЦИОНИРОВАНИЕ БЛОКОВ
4.1. Краткая характеристика процесса кондиционирования блоков
После окончания процесса формования блоки кондиционируют. Кондиционирование проводится с целью снижения влажности и устранения внутренних напряжений, возникающих при формовании. Кроме того, при этом протекают процессы диффузии газов и выравнивания давления внутри гранул с атмосферным давлением, подобные процессам, происходящим при кондиционировании предварительно вспененных гранул.
В процессе кондиционирования блоков очень важную роль играет очередность их использования, соответствующая очередности формования, то есть при отборе блоков для разрезания следует начинать с самых «старых».
5. РАЗРЕЗАНИЕ ПЕНОПОЛИСТИРОЛОВЫХ БЛОКОВ НА ПЛИТЫ
5.1. Характеристика процесса резки пенополистирола
Разрезание блоков осуществляется с помощью реостатной проволоки, нагретой до соответсвующей температуры.
Все отходы подаются в измельчитель, откуда в измельченном виде пневматически транспортируются на вторичное использование.
5.2. Требования по качеству
Внешний вид
Окраска пенополистироловых плит должна быть такой же, как окраска предварительно вспененных гранул полистирола.
Необходимо проводить выборочную проверку плит — по крайней мере 2 шт. на длине каждого блока.
Если плиты отвечают предъявляемым требованиям, то после укладки в стопки они направляются на упаковку.
Если отклонение от требуемых размеров превышает допустимую величину, то следует еще раз проверить по одной плите на всей длине блока, определить причину, произвести соответствующую корректировку промежутков между отрезками реостатной проволоки.
Проверить таким же образом размеры плит, полученных в результате разрезания следующего блока.
Плиты, которые не отвечают предъявляемым требованиям, направляются на вторичное использование.
6. ИСПОЛЬЗОВАНИЕ ПЕНОПОЛИСТИРОЛЬНЫХ ОТХОДОВ
Отходы используется вторично в производстве блоков.
6.1. Техническое оснащение узла
a) дробилка пенополистирольных отходов
b) технологический силос
6.2. Система измельчения
Устройство предназначено для измельчения пенополистироловых отходов, в результате чего получают крошку, используемую в качестве добавки к гранулам полистирола при производстве пенополистироловых блоков. Размеры получаемой таким образом крошки составляют до 15 мм.
Интересно? Оставьте закладку, что бы вернуться сюда позже!
Пенопласт в Ставрополе — Пенополистирол
Пенопласт в Ставрополе – является одним из лучших тепло-, гидро- и звукоизоляционных материалов в строительстве. Купить недорогой пенопласт вам предлагает компания «СтавПолистэр». Уже более 50 лет пенопласт лидирует среди других изоляционных материалов за счет высоких эксплуатационных характеристик, а также благодаря своей дешевизне.
Его механические и химические свойства сделали его таким популярным материалом, а небольшой вес и простота монтажа закрепили завоеванное лидерство. Он легко поддается обработке с помощью ножа или ручной пилы, легко склеивается с другими материалами и способен выдерживать большие механические нагрузки.
Основные характеристики и преимущества пенопласта действительно неоспоримы:
- Не вступает в реакцию с кислотами, щелочью и спиртом,
- Инертен к извести, цементу, бетону, песку и другим строительным материалам,
- При использовании пенопласта не требуется дополнительно устанавливать пароизоляцию,
- Монтаж пенопласта в Ставрополе не требует особых навыков и инструментов,
- Благодаря легкому весу не оказывает дополнительной нагрузки на фундамент и несущие конструкции здания.
Мы производим и доставляем пенопласт по Ставрополю, Ставропольскому краю, всему Южному Федеральному Округу и России!
Всегда в наличии следующие марки пенопласта, которые различаются по плотности:
- Пенопласт ПСБ-С-15 — имеет крупные зерна и её используют, как правило, для внутреннего утепления помещения.
Такой пенопласт хорошо удерживает тепло.
- Пенопласт ПСБ-С-25 — более плотная с мелкими зернами. Именно этот вид пенопласта используют для отделки и утепления фасадов зданий, с последующим нанесением штукатурки или других декоративных покрытий.
- Пенопласт ПСБ-С-35 — используетя для утепления крыш и изготовления теплых полов. Пенопласт 35-й плостности используют рекламщики для изготовления объемных стендов, фигур и букв — вывесок, обрабатывая и окрашивая их в нужные цвета.
- Пенопласт ПСБ-С-50 — считается самым долговечным, прочным и влогоустойчивым. Он является самым лучшим по уровню теплоизоляции из всех перечисленных марок. Его технические данные дают безграничные возможности применения в строительстве: укладка полов в специальных сооружениях и помещениях (мастерские, гаражи, промышленные холодильные установки и т.д.)
Лист пенопласта используется при производстве трехслойных панелей в крупнопанельном строительстве жилых домов, а также в качестве теплоизоляции при монолитном строительстве. Учитывая тот факт, что использование пенопласта в строительстве позволяет значительно снизить себестоимость затрат и на материалы, и на работы, становится очевидной его высокая популярность и крупные закупки оптом.
Пенополистирол в Ставрополе незаменим и при реконструкции старых зданий, когда увеличение нагрузки на несущие конструкции может стать опасным. Не менее популярен это материал и в следующих областях: при строительстве трубопроводов, при утеплении стен, полов и кровель, при строительстве бесподвальных помещений для утепления фундамента.
Заказать пенопласт от производителя по низкой цене вы можете, позвонив в Компанию «СтавПолистэр» по телефону +7 (8652) 56-57-20.
Изготовление и производство пенопласта листового, пенополистирола, заказ пенопласта в любом количестве
Пенопласт – это материал, предназначенный для утепления помещений, который представляет собой вспененные (ячеистые) пластические массы. Этот материал, в рамках своих свойств и качеств, не имеет аналогов на российском рынке.
Пенопласт очень легкий, это обусловлено тем, что основной объем занимает газ, плотность же материала значительно ниже. Что также способствует широкому спектру его применения.
Области применения:
- Утепления стен строения, для повышения теплоизолирующих показателей.
- Звукоизоляция стен, межквартирных и междуэтажных перекрытий.
- Конструкционный отделочный и строительный материал (декоративные изделия).
- Изготовление поплавков, спасательных поясов, бакенов, легких лодок.
- Упаковка продуктов питания, посылок, электротехники.
- Наружная реклама.
- и другие.
Преимущества:
- Жароустойчивость. Большим плюсом в применении данного материала является его жароустойчивость. Температура вспыхивания в два раза превышает температуру вспыхивания древесины. Пенопласт не является токсичным, не плавится и не «дышит». Возгорание может произойти только при непосредственном контакте с огнем, более того если непосредственного контакта больше нет материал затухает через 4 секунды.
- Устойчивость к высокому давлению. Способен годами выдерживать давление и деформацию, не изменяя своих физических свойств, и не разрушаясь. Например, пенопласт применяют при строительстве взлетно-посадочной полосы для самолетов.
- Долговечность. Прослужить долгие годы. Данное свойство было проверено в ходе лабораторных исследований. Может выдержать кратковременные перепады температуры от низких в – 180 градусов до высоких – в + 95 градусов.
- Удобство. Пенопласт легкий в работе материал, не требует специальных навыков или оборудования.
- Устойчив к воздействию кислот, минеральных масел, щелочей и воды.
- Не содержит питательных вещество для микроорганизмов и бактерий.
- Легко склеивается при помощи клея, цементных и гипсовых растворов.
- Является экологически чистым материалом, не образует пыль, не имеет запаха.
- Не является токсичным, не содержит пагубных для озонового слоя веществ.
Пенопласт – это материал, обладающий отличными теплоизоляционными свойствами, отличными характеристиками и преимуществами при низкой себестоимости.
Стиропласт — производство пенопласта в Чехове
ООО «Стиропласт» является заводом по производству пенопласта и строительных изделий. Запуск производственных мощностей завода состоялся в 2002 году. Находится предприятие в Московской области в городе Чехов по адресу: улица Комсомольская, владение №3. Руководителем и учредителем ООО «Стиропласт» является Валюхов Александр Александрович.
Производство
Завод строительных материалов по производству и реализации пенополистирола получил широкую известность не только в Москве, но и во многих регионах благодаря качеству продукции. Для изготовления пенопласта запустили автоматические, а также полуавтоматические линии. К слову сказать, используется здесь самое современное оборудование. Так что каждая производственная линия выпускает до 180 кубометров пенополистирола. Как известно, в сутки здесь производится до 500 кубометров изделий. Крупнооптовые партии продукции здесь производятся всего лишь за 3 дня.
Изготовление пенопласта высокого качества обеспечивается жестким контролем за производством со стороны отдела техконтроля. Немаловажный момент — наличие собственной лаборатории, которая проверяет продукцию на каждом производственном этапе. А также важным условием получения качественных пенополистирольных плит ПСБ-С является использование высококачественного сырья.
Продукция
Пенопласт, производство которого осуществляет завод «Стиропласт» уже не первый год, изготавливается путем вспучивания полистирольных гранул с последующей формировкой массы в плиты. Нарезка изделий выполняется по задаваемым размерам.
При желании всегда можно заказать пенопласт производство. Кроме всего прочего, можно заказать производство материала, в который добавляется антипирен.
Благодаря тепло- и звукоизоляционным характеристикам, изделия применяются в разных промышленных сферах, а также в частном секторе. Как известно, пенопласт Чехов получил широкую востребованность в строительстве для теплоизоляции наружных стен и кровельных покрытий. Специалисты, давая оценку изолирующему материалу, подчеркивают его экологичность, а также экономическую выгоду.
К тому же важным достоинством плит ПСБ-С является их долговечность и высокие прочностные показатели при сжатии. Так что изолирующий материал получил широкое применение в решении производственных задач, при выполнении ремонтных работ, транспортировке различной продукции. Кстати, применяется он даже в качестве создания декоративных элементов.
Сферы применения
Методы изготовления пенопласта предполагают применение разных технологий. Этот фактор позволяет значительно расширить сферу его применения. Например, сегодня используется пенопласт завода «Стиропласт» для:
- Гидроизоляции и утепления. Конструкция плит предполагает нанесение на них с двух сторон сетки со шпатлевкой. Так что стены, перекрытые строительным материалом, получают эффективную защиту от различных воздействий и обеспечивают надежную гидроизоляцию.
- Утепления перекрытий и кровли.
Этот фактор позволяет в частном доме сократить расходы на отопление помещения на 20%.
- Утепления подвала. Утепление пенопластом гарантирует сохранность тепла в подвале, а также на первом этаже. К тому же материал не позволит оседать сырости на стенах. В подвалах плиты укладываются на песок и им же присыпаются. Монтаж пенобетона на бетонные полы гарантирует хорошую теплоизоляцию на протяжении десятков лет.
- Строительства. Современные технологии сегодня предлагают множество новых методов строительства коттеджей, туннелей, мостов, а также дорог с использованием пенополистирольных блоков. Изготавливаются они из полистирола с добавлением антипиреновых составов, обеспечивающих устойчивость материала к возгоранию. Стены из данного материала тоньше, чем кирпичные (бетонные), однако сохранность их технических характеристик будет наблюдаться на протяжении 80-100 лет. Высокие прочностные показатели блоков позволяют их использовать даже при строительстве взлетно-посадочных линий.
Как правильно выбрать пенополистирол и купить его?
ООО «Стиропласт» реализует собственную продукцию. Так что клиенты имеют возможность купить пенопласт от производителя цена которого будет существенно меньше, чем цена этой же продукции в торговых точках.
Клиентам и предприятиям, желающим пенопласт опт купить, завод «Стиропласт» готов предоставить гибкую и выгодную систему скидок. Для того чтобы узнать точную стоимость изделий, можно изучить находящийся на сайте прайс-лист. А также всегда возможно связаться с менеджером компании по телефону. Специалист ответит на все интересующие вопросы, подскажет, какую марку изделия стоит выбрать в данном случае, и расскажет, какое изделие будет лучше сохранять тепло.
Если вам нужны теплоизоляционные плиты из пенополистирола, обращайтесь в компанию «Стиропласт» по телефону +7 (495)723-85-93. Заказы здесь формируются быстро. Доставляется продукция завода не только в Москву, Подмосковье, но и во многие другие регионы России.
Бизнес план производства пенопласта с расчетами
Несмотря на появление новых материалов, производство пенопласта остаётся актуальным. Материал активно используют при строительстве и упаковке в Европе, США и в развивающихся странах Азии.
Почему пенопласт так популярен?
- Функциональность. Пенопласт применяют в строительстве, торговле и судостроении для изготовления теплоизоляционного материала, упаковки или понтонов.
- Стоимость. Пенопласт обладает высокими теплоизоляционными свойствами, но стоит дешевле.
Преимущества бизнеса по производству пенопласта:
- Низкий порог входа;
- Рынок сбыта;
- Высокая маржинальность при правильно построенном сбыте;
- Простой технологический процесс.
Ключевые риски бизнеса:
- Непроработанный план продаж;
- Удаленность предприятия от пунктов реализации, которая увеличит стоимость доставки;
- Поломка оборудования.
Эти факторы могут стать причиной больших остатков на складе, остановить производство и сократить прибыль.
Общий объем производства пенопласта в мире составляет 25 млн тонн. Среднегодовой рост отрасли — 2,5-3,5%. В России, то годовой темп роста выше — 10%. Это связывают с высокими темпами строительства и ростом торговли.
Из-за высокой стоимости транспортировки, многие производители работают на крупных локальных рынках, поэтому основные конкуренты — небольшие региональные предприятия. Большая часть предприятий работает на Урале и в Сибири — в местах, где добывается сырье для изготовления пенопласта. Кроме того, здесь сосредоточено большое количество торговых и производственных предприятий.
Закупать сырье лучше на нефтехимических заводах или у оптовых поставщиков.
Для запуска производства нужны: инвестиции, цех, оборудование и 5 сотрудников. Работники будут производить порядка 60 м3 продукции в день.
Общая площадь производственного помещения — 250 м2. Из них 50 м3 необходимо выделить под склад. В помещении должны быть высокие потолки, вентиляция, водоснабжение и электричество.
Технология производства:
- Гранулы загружают в предварительный вспениватель.
Там, под воздействием пара, гранулы начинают вспениваться.
- Затем гранулы отправляют в сушилку.
- Высушенные гранулы загружают в бункер для дополнительной просушки и затем заполняют блок-формы. Формы выдерживают под давлением и охлаждают.
- Готовые блоки разрезают на листы. Остатки помещают в дробилку для повторного производства.
Изготовление изделий из пенопласта под заказ в Москве
Буквы из пенопласта
Объемные буквы из пенопласта – новинка современного рынка, которая помогает быстро и эффективно привлечь внимание потенциальных клиентов к своей компании!Вывески
Качественная, грамотно подготовленная реклама – обязательная составляющая успеха любой компании. Она привлекает к себе внимание потенциальных клиентов.Фигуры
Фигуры из пенопласта — максимум преимуществ от компании «ТОП-Пенопласт»! Современные и недорогие решения для декорирования любых пространств.Садово-парковые скульптуры
Наибольшую популярность в наши дни приобрели садово-парковые скульптуры из пенопласта, которые выступают прекрасной альтернативой каменному, деревянному и металлическому декору.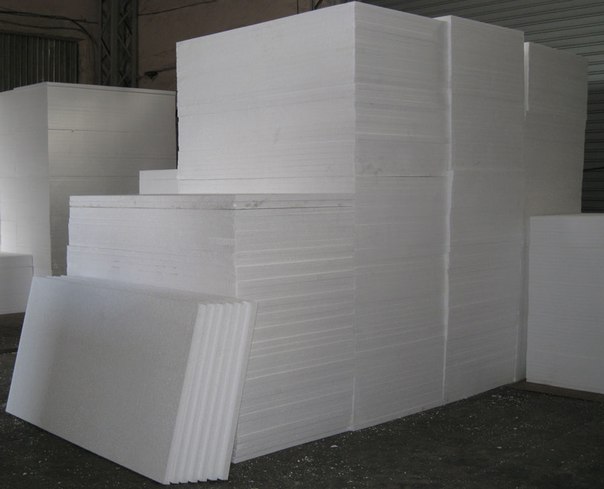
Муляжи
Муляжи из пенопласта – выгодный и доступный рекламный продукт! Очень часто при оформлении торговых и выставочных залов, проведении рекламных компаний или театральных постановок.Фасадный декор
Фасадный декор из пенопласта – роскошные решения для внешнего оформления Вашего дома! Они создают особый образ дома, придавая ему индивидуальность и помогая выразиться его владельцу.Резка пенопласта
Фигурная резка пенопласта – современное оборудование для максимальной точности, которое позволяет создавать фигуры любой сложности.Шары из пенопласта
Шары из пенопласта – создайте гармонию в своем доме! Они с легкостью заменят елочные игрушки, внесут гармонию в любой интерьер и просто создадут праздничное настроение.Светящиеся вывески
Светящиеся объемные буквы видны со многих ракурсов и в то же время неоновые трубки хорошо защищены от воздействий как атмосферы, так и вандалов.
Упаковка
Упаковка из пенопласта – надежная защита для самых хрупких предметов! У нас Вы можете приобрести продукцию, которая обеспечить высокую степень защиты бытовой техники, мебели, стеклянных изделий.Макеты
Макеты из пенопласта – мы создадим для Вас настоящие шедевры! Обращайтесь в «Топ-пенопласт», здесь Вас ждут настоящие профессионалы, для которых нет ничего невозможного!Реклама из пенопласта
Качественная, грамотно подготовленная реклама – обязательная составляющая успеха любой компании. Она привлекает к себе внимание потенциальных клиентов.Буквы для свадьбы
Практически ни одна свадьба не обходится без яркой фотосессии. Красивые кадры обеспечат долгую память об этом событии, а объемные буквы из пенопласта придадут фотографиям дополнительную изюминку.Изготовление пенопластовых МАКЕТОВ И МОДЕЛЕЙ точно в срок и по лучшим ценам в Москве!
Товары из пенопласта являются прекрасным украшением интерьера или фасада дома, оригинальной деталью любой рекламной компании, неотъемлемым атрибутом свадебной или новогодней вечеринки, изысканным элементом фотосессии! Данный список можно продолжать бесконечно.
Если Вы хотите купить предметы из пенопласта от производителя по лучшим в Москве ценам, обращайтесь в компанию «ТОП-Пенопласт».
ПРИМЕНЕНИЕ ТОВАРОВ ИЗ ПЕНОПОЛИСТИРОЛА И ИХ ОСНОВНЫЕ ПРЕИМУЩЕСТВА
В последнее время пенопластовые атрибуты используются практически повсеместно: в упаковочной и пищевой индустрии, в строительной отрасли, в бытовой сфере, для утепления стен, полов и потолков, во флористике, в дизайне интерьеров, в организации праздничных мероприятий и проведении рекламных компаний. Элементы из экструдированного пенополистирола зачастую применяются при отделке фасадов зданий, дверных и оконных проемов, потолков, а пенопластовые фигуры нередко можно увидеть в парках, скверах и на заднем дворе многих загородных домов.
Пенопласт прочно занял свое место в архитектурно-декоративном оформлении, вытесняя традиционные материалы, такие как камень, мрамор или гипс.
В первую очередь, это связано с его преимуществами:
- при изготовлении изделий из пенопласта им можно придать любую форму, так как данный материал очень легко обрабатывается;
- возможность производства деталей из пенополистирола с идеально ровной поверхностью без каких-либо швов;
- малый вес материала;
- легкость и удобство монтажа, без применения специальных средств;
- стойкость пенопластовых элементов к внешним воздействиям – ветру, дождю, воздействию ультрафиолета и перепадам температур;
- экологичность — производство изделий из пенополистирола абсолютно безопасно и нетоксично;
- долговечность – благодаря специальным покрытиям пенопласт не подвержен образованию грибка или плесени, гниению и поражению насекомыми;
- пожаробезопасность – в случае возгорания пенопласт быстро самозатухает;
- доступная стоимость изделий из пенопласта, так как это самый недорогой материал, используемый к примеру для архитектурного оформления.
ОСОБЕННОСТИ ИЗГОТОВЛЕНИЯ ТОВАРОВ ИЗ ПЕНОПОЛИСТИРОЛА
Компания «ТОП-Пенопласт» занимается производством изделиЙ из пенопласта практически любого размера и сложности. Вы всегда можете заказать у нас буквы из пенопласта, слова и надписи, пенопластовые фигуры и фигурки, элементы фасадного декора и многое другое. Кроме того, мы рады предложить Вам производство макетов на заказ по Вашему индивидуальному эскизу.
Наши специалисты могут предложить Вам изготовление элементов декора из экструдированного (пенопласта повышенной плотности) и обычного пенопласта по весьма привлекательным в Москве ценам.
Производство изделий из пенопласта осуществляется на современных станках с ЧПУ, методом фигурной и контурной резки, позволяющих изготовлять любые детали с максимальной точностью.
После этого все атрибуты тщательно зашкуриваются, грунтуются и покрываются краской, а в случае необходимости и специальными составами, защищающими их от неблагоприятного внешнего воздействия.
В ряде случаев для придания пенопластовым моделям большей устойчивости, детали могут закрепляться на металлический каркас.
Для всех клиентов, заказавших у нас поделки из пенопласта, мы можем оказать услуги по их доставке, а в случае необходимости монтажу в пределах Москвы и Московской области. Доставка готовых изделий возможна также и в другие регионы РФ.
Мы все еще не убедили Вас в том, что пенопласт – это модно, современно и надежно? Знакомьтесь с нашими работами, эстетичность и разнообразие которых станет для Вас приятным сюрпризом!
НАШИ КЛИЕНТЫ
Разработка одностадийного процесса производства пенопластовых древесностружечных плит с использованием жесткого пенополиуретана :: BioResources
Шалбафан А., Чайдарре К. К., Веллинг Дж. (2016). «Разработка одностадийного процесса производства пенопластовых древесностружечных плит с использованием жесткого пенополиуретана», BioRes. 11 (4), 9480-9495.Реферат
Смоделированный одностадийный процесс был разработан для производства пенопластовых ДСП с использованием жесткого полиуретана в качестве внутреннего слоя. Результаты показали, что различные методы, используемые для разделения поверхностного слоя (несмолированные частицы и распыленная вода) и впрыскивания пены (открытая система и закрытая система), не влияли на характеристики панелей. На механические свойства (например, прочность на изгиб и прочность внутреннего скрепления) в основном влияла толщина поверхностного слоя, в то время как на водопоглощение и отрыв краевого винта влияла структура ячеек пены. Использование распыленной воды для отделения поверхностного слоя удвоило выделение формальдегида (FE) панелей.Добавление мочевины (из расчета 10% сухой смолы) к распыляемой воде имело положительный эффект снижения конечного FE. Более того, увеличение толщины поверхностного слоя имело прямую линейную зависимость от FE.
Скачать PDF
Полная статья
Разработка одностадийного процесса производства древесностружечных плит с вспененным сердечником с использованием жесткого пенополиуретана
Али Шалбафан, а, * Камран Чупани Чайдарре, а и Йоханнес Веллинг b
Смоделированный одностадийный процесс был разработан для производства вспененных древесностружечных плит с использованием жесткого полиуретана в качестве внутреннего слоя. Результаты показали, что различные методы, используемые для разделения поверхностного слоя (несмолированные частицы и распыленная вода) и впрыскивания пены (открытая система и закрытая система), не влияли на характеристики панелей. Механические свойства (, например, прочность на изгиб и прочность внутренней связи) в основном зависели от толщины поверхностного слоя, в то время как на водопоглощение и отрыв краевого винта влияла структура ячеек пены. Использование распыленной воды для отделения поверхностного слоя удвоило выделение формальдегида (FE) панелей.Добавление мочевины (из расчета 10% сухой смолы) к распыляемой воде имело положительный эффект снижения конечного FE. Более того, увеличение толщины поверхностного слоя имело прямую линейную зависимость от FE.
Ключевое слово: ДСП; Легкий; Бутерброд; Полиуретан; Жесткая пена
Контактная информация: a: Отделение науки и технологии древесины и бумаги, Факультет природных ресурсов и морских наук, Университет Тарбиат Модарес, Нур, Иран; b: Институт исследований древесины Тюнена, 21031 Гамбург, Германия; * Автор для переписки: ali. [email protected]
ВВЕДЕНИЕ
Многослойные конструкции демонстрируют многообещающие легкие характеристики для использования в морской и авиационной промышленности и используются на протяжении десятилетий (Gruenewald et al .2015). Кроме того, легкие плиты значительно снижают общие выбросы парниковых газов (Feifel et al .2013). Использование сэндвич-стратегии в мебельной промышленности не очень хорошо развито из-за трудоемких производственных методов, которые по-прежнему препятствуют широкому применению.Вторым важным этапом изготовления многослойных конструкций является соединение сборных обшивок и легкого внутреннего слоя. Основными методами производства (которые уже представлены на рынке) являются либо периодический процесс, когда предварительно изготовленные слои склеиваются и собираются вместе, либо процесс, при котором вспенивающая жидкость для формирования материала сердцевины вводится между двумя предварительно изготовленными лицевыми слоями ( Аллен 1969; Ли и др. .2014). Недостатками этих процессов являются отсутствие одновременного изготовления всех слоев вместе и некоторые ограничения в отношении технологий производства.
Среди всех процессов одностадийный процесс ( на месте, вспенивание) демонстрирует большой потенциал для упрощения производственного процесса, а также для соединения сэндвич-оболочек и сердцевины (Zenkert 1997). Луедтке (2011) и Шалбафан и др. . (2012) показали, что одностадийный процесс формирования многослойных структур имеет большой потенциал для производства легких вспененных древесностружечных плит. Характеристики материалов основного слоя, например. , их термореактивная или термопластичная природа, создают проблемы в одностадийном производственном процессе.В случае термопластичных материалов внутреннее охлаждение для стабилизации панелей необходимо на заключительной стадии производства пресса. Шалбафан и др. . (2012) отметили, что материалы внутреннего слоя должны иметь расширяемую твердую гранулированную форму, которая будет использоваться в одностадийном процессе производства пенопластовых древесностружечных плит. С другой стороны, использование термореактивных вспененных материалов в качестве материалов внутреннего слоя не требует внутреннего охлаждения, но такие материалы (расширяемые термореактивные твердотельные грануляты), которые соответствуют требованиям для одностадийного производственного процесса, еще не доступны на рынке.
Полиуретан (ПУ) — это полимер, состоящий из органических звеньев, соединенных уретановыми связями. Большинство используемых ПУ — это термореактивные полимеры, которые не нужно охлаждать для стабилизации (Sonnenschein and Koonce 2012). ПУ обычно образуются в результате реакции между компонентами полиола (PO) и изоцианата (ISO) и имеют жидкую фазу перед вспениванием, что представляет проблему для вспенивания на месте . Различные пенополиуретаны (мягкие, эластомерные и жесткие) могут быть произведены в зависимости от типа полиолов, используемых для получения пены (Ionescu 2005).Полиолы с числом ОН от 300 до 500 предпочтительно используются для получения жестких пенополиуретанов, которые представляют собой простые полиэфирполиолы и полиэфирполиолы. Жесткие пенополиуретаны могут изготавливаться с плотностью от 40 до 1000 кг / м 3 , в зависимости от их полиольной структуры. Более низкая плотность (<60 кг / м 3 ) подходит для изоляционных материалов, тогда как более высокая плотность (> 500 кг / м 3 ) подходит для декоративных применений (Ionescu 2005). Пенополиуретаны высокой плотности могут иметь отличные характеристики в различных областях применения, но эффект легкости, необходимый для многослойных структур, в этих пенах больше не существует.Чтобы получить легкие панели на древесной основе, внутренний слой должен иметь значительно меньшую плотность (<300 кг / м 3 ), чем обычные панели. Когда плотность внутреннего слоя ниже, достигается формирование более легких панелей. Смесь двух различных полиолов (используемых для изоляционных и декоративных целей) может обеспечить легкость конструкции и отличные характеристики пены.
В этом исследовании два разных полиола, один из которых обычно используется для изоляции, а другой — для декоративных целей, были смешаны вместе для достижения желаемой плотности пены и лучшей обрабатываемости. Целью данного исследования является производство древесностружечных плит из вспененного материала в моделируемом одностадийном процессе (с учетом проблем, упомянутых выше) с использованием жесткого полиуретана в качестве внутреннего слоя. Для моделирования одноэтапного производственного процесса необходимо использовать методы разделения поверхностных слоев. Следовательно, были изучены эффекты различных методов, используемых для разделения поверхностного слоя и впрыска пены в смоделированном одностадийном процессе. Также были проанализированы механические и физические свойства изготовленных таким образом панелей.
ЭКСПЕРИМЕНТАЛЬНАЯ ИНФОРМАЦИЯ
Материалы
Обычные мелкие частицы древесины, в основном бука и тополя (≤ 2 мм), использовались для облицовочных слоев и поставлялись местным заводом по производству древесно-стружечных плит в Иране. Частицы смешивали со смолой на основе формальдегида мочевины (UF) (12%) (Amol Resin Ltd. , Иран) и сульфатом аммония (1%) в качестве отвердителя. Смола UF имела содержание твердого вещества и pH 62% и 7,1 соответственно. Заданная плотность поверхностного и нижнего слоев поддерживалась постоянной на уровне 700 кг / м 3 .Толщина поверхностного слоя варьировалась (3, 4 и 5 мм для каждого из двух лицевых слоев), соответственно, изменялась и соответствующая плотность панели (300, 370 и 440 кг / м 3 ).
Смесь простого полиэфира (Kupa 501) и сложных полиэфирполиолов (Kupa 150) смешивали с полимерным метилендифенилдиизоцианатом (pMDI) для получения центрального слоя. Используемые химические вещества были поставлены компанией Jazb Setareh Co., Иран. Заданная плотность подготовленного центрального слоя поддерживалась постоянной на уровне 120 кг / м 3 .
Подготовка образца для испытаний
ДСП с пенопластом (толщиной 19 мм) были произведены в смоделированном одностадийном процессе, состоящем из четырех последовательных стадий. Панели были изготовлены с различной толщиной поверхностного слоя 3, 4 и 5 мм, и, соответственно, толщина внутреннего слоя пенопласта варьировалась на 13, 11 и 9 мм соответственно. Процесс, использованный в этом исследовании, описан на рис. 1. В идеальном промышленном одностадийном производственном процессе используются четыре последовательных этапа: уплотнение поверхностного слоя, разделение поверхностного слоя, впрыскивание пены и стабилизация панели.Можно сказать, что наиболее сложными этапами являются отделение поверхностного слоя и нагнетание пены. Следовательно, были применены различные методы разделения слоев и впрыска пены, чтобы определить их эффект на таких сложных этапах.
Рис. 1. Разработка технологического процесса производства пенопластовых ДСП в промышленных масштабах |
Иллюстрированный одностадийный производственный процесс (рис. 1) был сначала смоделирован в лабораторном масштабе. Для начала два поверхностных слоя (после смола частиц и формирования мата) уплотняли до отверждения УФ-смолы (в конце секции прессования). Затем поверхностные слои были разделены в лабораторном масштабе благодаря использованным методам разделения. После образования нижнего слоя и перед формированием лицевого слоя были выполнены различные методы разделения с использованием либо несмолистых древесных частиц, либо метода распыления воды. Обычные мелкие несмолистые частицы древесины (400 г / м 2 ) использовали в качестве разделительного материала между двумя слоями.Количество распыленной воды поверх нижнего слоя составляло 60 г / м 2 , чтобы образовалась паровая масса (на стадии подготовки поверхностных слоев) между двумя слоями для разделения слоев. Более высокое количество распыляемой воды могло бы повлиять на образование пены и связь между лицевыми и сердцевинными слоями. Следовательно, необходимо поддерживать как можно более низкий уровень распыляемой воды. Для удаления несмолистых древесных частиц или плохо связанных частиц между поверхностью и нижним слоем после отделения поверхностного слоя, но перед стадией впрыска пены, использовался отсос (пылесос).
На этапе впрыска пены также использовались два разных метода; Для этого использовался либо деревянный каркас (закрытая система), либо четыре небольших деревянных кубика (открытая система). Высота деревянного каркаса и деревянных кубиков была такой же, как толщина слоя пенопласта (13, 11 или 9 мм), и они располагались поверх нижнего слоя. Затем смесь компонентов пены впрыскивалась (заливалась) на нижний слой и, соответственно, сразу на него укладывался верхний поверхностный слой.После этого вся сборка была помещена на второй пресс (без зон нагрева), чтобы сохранить желаемую толщину панели (стабилизация панели). Рисунок 2 иллюстрирует смоделированный одностадийный процесс производства пенопластовых панелей в лабораторном масштабе.
В таблице 1 показаны составы переменных панели. Чтобы подтвердить влияние методов разделения лицевого слоя на свойства панели, контрольные образцы (с использованием периодического процесса) также были изготовлены без каких-либо методов разделения (где каждый поверхностный слой был изготовлен отдельно).
Таблица 1. Технологии производства древесностружечных плит с пенопластом
* Не смолистые древесные частицы, используемые между нижним и поверхностным слоями.
** Распыляемая вода, используемая поверх нижнего слоя.
Составы пены
Полиол простого полиэфира на нефтяной основе (Kupa 501) и полиол сложного полиэфира (Kupa 150) использовали после определения их гидроксильного числа (450 мг КОН / г и 306 мг КОН / г, соответственно) и содержания воды (0.15% и 0,1% соответственно). Сводка типичных физических и химических свойств обоих полиолов (от поставщиков) приведена в таблице 2. Химические вещества: полимерный метилендифенилдиизоцианат (pMDI), кремниевое поверхностно-активное вещество — полисилоксановый эфир, катализатор — диметилциклогексиламин и пенообразователь — ГФУ R-141b использовался в полученном виде. Содержание групп NCO в pMDI составило 31% (согласно паспорту поставщика).
Таблица 2. Физико-химические свойства полиолов
* Ароматический полиэфирный полиол.
** Значения, проверенные экспериментально.
Таблица 3. Составы и реакционная способность жестких пенополиуретанов
Методика рецептуры жесткого пенополиуретана представлена в таблице 3. Он был приготовлен двухэтапным методом. Полиолы смешивали с катализатором, поверхностно-активным веществом и вспенивающим агентом для получения гомогенной смеси в соответствии с процедурой приготовления. Затем смесь полиолов смешивали с pMDI (приблизительно 10 с) перед инъекцией.Данные о реакционной способности жесткого пенополиуретана были получены в ходе «чашечного теста» и представлены в таблице 3 (Ionescu 2005).
Характеристики панелей
Чтобы охарактеризовать новые произведенные панели и изучить влияние различных методов разделения слоев и инъекции полиуретана, а также влияние толщины поверхностного слоя, были проведены механические и физические испытания. Прочность на изгиб (EN 310 (1993)), прочность внутреннего сцепления (EN 319 (1993)) и сопротивление выдергиванию торцевого / краевого винта (EN 13446 (2002)) были определены в качестве основных механических свойств.Физическое поведение (EN 317 (1993)) панелей было охарактеризовано путем измерения разбухания по толщине и тенденции водопоглощения после длительного выдерживания (до 786 ч после погружения в воду). Для каждого варианта панели готовили по три повтора. Случайным образом были отобраны и протестированы три образца из каждой повторности ( n = 9). Перед испытанием все образцы кондиционировали в климатической камере при относительной влажности 65% и температуре 20 ° C до достижения постоянной массы. Физические испытания проводились на неотшлифованных образцах.
Измерения выбросов формальдегида
Чтобы лучше понять свойства этих новых древесностружечных плит из вспененного материала, было проведено испытание на выброс формальдегида. Влияние толщины поверхностного слоя и распыляемой воды (для разделения слоев) на выделение формальдегида панелями было исследовано с использованием колбового метода (EN717-3 (1996)). Раствор мочевины и воды использовали для распыления в качестве метода разделения поверхностного слоя для контроля выделения формальдегида.Количество использованной мочевины составляло приблизительно 10% от твердого содержания смолы для одного лицевого слоя. Более подробная информация о вариантах панелей, используемых для выделения формальдегида, представлена в таблице 4.
Таблица 4. Переменные панели , используемые для измерения выбросов формальдегида
* Каждый поверхностный слой получали отдельно (контрольный образец).
** Для разделения поверхностных слоев использовали раствор мочевины и воды.
Статистический анализ
Двусторонний дисперсионный анализ (ANOVA) механических и физических свойств был выполнен с использованием статистического пакета для программного обеспечения социальных наук (программное обеспечение SPSS, IBM, США). Статистические различия между вариациями оценивались путем множественных сравнений на основе критерия Дункана из-за однородности вариаций. Парный T-тест также использовался для сравнения значений различных методов разделения и закачки. Статистическая значимость была установлена на уровне P <0.05.
РЕЗУЛЬТАТЫ И ОБСУЖДЕНИЕ
Влияние методов разделения поверхностных слоев
Одним из наиболее важных этапов в разработке одностадийного процесса производства панелей с пенопластом является разделение поверхностного и нижнего слоев для впрыска пены. Влияние двух различных методов разделения (несмолистые частицы и распыленная вода) на значения прочности на изгиб (MOR) и внутренней связи (IB) представлены на рис. 3. Значения обоих свойств (MOR и IB) для не- Метод смолистых частиц был немного выше, чем метод распыления воды, но такие различия не были обнаружены статистически значимыми.На прочность на изгиб в основном влияли плотность панели и качество поверхностного слоя, которое было почти одинаковым для обоих типов панелей. На величину внутреннего сцепления в панелях с пенопластом повлияло качество поверхности раздела (лицевой и сердцевинный слой) (Shalbafan и др. . 2013b). В случае метода водного распыления между поверхностным и нижним слоями образовывалась масса водяного пара, которая влияет на отверждение УФ-смолы на частицах, образующих внутренние стороны лицевых слоев.Слабые внутренние поверхности приводят к снижению значений прочности внутреннего сцепления. Кроме того, более высокое содержание влаги в мате (в случае распыляемой воды) может также привести к снижению сшивки клея и, соответственно, к ослаблению характеристик склеивания (Roffael 1993).
Рис. 3. Влияние методов разделения поверхностного слоя на прочность на изгиб и прочность внутреннего соединения |
Сравнение панелей, изготовленных с помощью смоделированного одноэтапного процесса, с панелями, произведенными в периодическом процессе (контрольные образцы), представлено на рис.3. Результаты показали, что контрольные образцы имели значительно более высокие значения MOR и IB, чем образцы, полученные с помощью непрерывных процессов. Как упоминалось ранее, качество поверхностного слоя из-за более плотного поверхностного слоя было причиной более высоких значений MOR в контрольных образцах. Для изготовления контрольных образцов не использовалась методика разделения. Следовательно, отсутствие слабосвязанных частиц привело к лучшему сцеплению с компонентами пены. Некоторые слабые и плохо связанные частицы всегда будут присутствовать на внутренних поверхностях слоев в случае несмолистых древесных частиц и методов отделения водяным распылением, которые влияют на значения внутреннего сцепления.Этих слабых частиц не было в контрольных образцах. Хотя эталонные образцы имели более высокие MOR и IB, чем у панелей с пенопластом, они не могут быть предпочтительнее в мебельной промышленности из-за процесса серийного производства (Shalbafan и др. . 2013b).
Следует отметить, что минимальные требования к значениям IB согласно EN312 / P2 были достигнуты для всех вариантов панели. Хотя MOR почти на 30 процентов ниже, чем EN312 / P2 для панелей, произведенных с помощью разработанного одноэтапного процесса, он все еще находится в желательном диапазоне для специальных применений.
Влияние методов разделения поверхностного слоя на извлечение торцевого винта (FSW) и извлечение краевого винта (ESW) представлено на рис. 4. Результаты показали, что методы разделения не оказали существенного влияния на FSW и ESW. На FSW влияло качество поверхностного слоя, которое было практически одинаковым для обоих методов. На ESW повлияли структуры пены, которые также были одинаковыми для обоих методов из-за схожего состава пены.
FSW контрольных образцов был значительно выше, чем у панелей, изготовленных с помощью одностадийного производственного процесса, поскольку они имели лучшее качество поверхности и нижнего слоя.ESW не претерпел значительных изменений на контрольных образцах, поскольку компоненты пены оставались постоянными во всех вариантах панели.
Рис. 4. Влияние техники разделения поверхностных слоев на извлечение торцевых и краевых винтов |
Влияние методов впрыска пены
Два разных метода (закрытая и открытая системы) использовались для впрыска пены между разделенными слоями. Влияние методов впрыска на прочность на изгиб и значения внутренней связи показано на рис. 5. Результаты показали, что различные системы впрыска не влияют на прочность на изгиб и значения прочности внутренней связи. Следует отметить, что впрыскиваемая (залитая) пенная смесь не выливалась со сторон образца в случае открытого впрыска из-за высокой вязкости и очень короткого времени вспенивания (25 с) пенной смеси. Кроме того, визуальные наблюдения показали, что смесь ПУ в основном перемещалась в направлении высоты (направлении подъема), а ее боковые перемещения были довольно низкими.Полимерный изоцианат (pMDI) добавляли только к смеси полиолов перед инъекцией. Смесь перемешивали примерно 10 с и сразу же выливали поверх нижнего слоя. Сливание смеси происходило сразу после заливки (впрыска) пены, излияния пены не наблюдалось. В конечном итоге можно предположить, что системы впрыска пены не оказывают значительного влияния на процесс вспенивания и, соответственно, на свойства панели.
Фиг.![]() |
На рис. 6 представлены результаты значений отрыва торцевых и краевых винтов для панелей, изготовленных с использованием различных систем впрыска пены.
Рис. 6. Влияние техники впрыска пены на отвод торцевых и краевых винтов |
Результаты показали, что значения FSW и ESW не сильно различались при изменении систем впрыска пены.Значения торцевых винтов в основном зависят от качества поверхностных слоев, которое было одинаковым для обоих вариантов (Shalbafan и др. . 2013b). Значения краевого винта зависят от процедуры вспенивания и полученной структуры пены. Таким образом, можно сделать вывод, что структура пены в обеих системах впрыска почти одинакова, поскольку значения ESW были почти сопоставимы.
Влияние толщины слоя
Плотность панелей и содержание влаги в панелях после двух недель кондиционирования (при 20 ° C и относительной влажности 65%) представлены в таблице 5. Толщина панели оставалась постоянной (19 мм), а толщина поверхностного слоя увеличивалась с 3 до 5 мм. Следовательно, плотность панели была увеличена за счет увеличения толщины поверхностного слоя с 3 (302 кг / м 3 ) до 5 мм (439 кг / м 3 ). Влагосодержание было выше в панелях с более толстыми поверхностными слоями, потому что в более толстых панелях содержится больше гигроскопичных материалов.
Таблица 5. Плотность панели и содержание влаги
* Цифры в скобках — стандартное отклонение
Влияние толщины поверхностного слоя на свойства панели (MOR и IB) показано на рис.7. Значения MOR незначительно увеличились с 9,5 МПа для панелей толщиной 3 мм до 10,5 МПа для поверхностных слоев панелей толщиной 5 мм. Толщина, плотность и структура каждого слоя пенопластовых панелей были наиболее важными факторами, влияющими на прочность на изгиб (Vinson 2005; Link et al .2011). Плотность панелей была увеличена за счет увеличения толщины поверхностного слоя с 3 мм (300 кг / м 3 ) до 5 мм (440 кг / м 3 ). Эта увеличенная плотность панели привела к увеличению прочности на изгиб.Также можно заметить, что древесина стала жестче и прочнее, чем материал полимерного сердечника. Утолщение поверхностных слоев сопровождалось уменьшением толщины внутреннего слоя пенопласта с 13 до 9 мм, и соответственно были получены более высокие значения MOR. Чен и Ян (2012) также обнаружили, что уменьшение отношения толщины сердцевины поверхностного слоя привело к увеличению свойств изгиба сэндвич-панелей.
Значения прочности внутреннего сцепления снизились при увеличении толщины поверхностного слоя с 3 мм (0.От 46 Н / мм 2 ) до 5 мм (0,17 Н / мм 2 ). Шалбафан и др. . (2012) отметили, что преобладающим фактором, влияющим на значения прочности внутреннего сцепления панелей из пенопласта, является качество границы раздела лицевых и внутренних поверхностей. Образцы, приготовленные с толщиной грани 3 мм, разрушились в лицевом слое в непосредственной близости от границы раздела, а для образцов с толщиной грани 5 мм разрушение произошло в середине поверхностных слоев. Как упоминалось ранее, масса водяного пара, образующаяся между поверхностным и нижним слоями, влияет на сшивание клея и, соответственно, дополнительно ослабляет характеристики склеивания в более толстых поверхностных слоях (Roffael 1993).
Рис. 7. Влияние толщины поверхностных слоев на прочность на изгиб и значения внутренней связи |
Значения отвода торцевых и краевых винтов для панелей с разной толщиной поверхностного слоя показаны на рис. 8. Результаты показали, что FSW линейно увеличивается с увеличением толщины поверхностного слоя. FSW увеличивается почти до 30% за счет каждого дополнительного миллиметра толщины поверхностного слоя.Значения извлечения краевого винта существенно не изменились, и значения ESW, безусловно, также зависели от состава пены, но они оставались постоянными для всех вариантов панели.
Рис. 8. Влияние толщины поверхностного слоя на отвод торцевых и краевых винтов |
Влияние толщины поверхностного слоя на набухание толщины и водопоглощение при времени выдержки до 786 ч представлено на рис. 9. Значения набухания по толщине были выше для панелей с более толстыми поверхностными слоями. Значения TS почти достигают максимального уровня (от 5% до 7%) примерно через 48 часов замачивания. Впоследствии увеличение TS было чрезвычайно снижено до достижения 786 часов времени выдержки, в то время как TS существенно не изменилась. На TS панелей с пенопластом влияет толщина поверхностного слоя (Luedtke 2011). Похоже, что деревянные частицы были насыщены после короткого времени (48 часов) замачивания, и это состояние не меняется при продлении замачивания до 786 часов (Shalbafan et al .2013а). Также следует учитывать, что внутренний слой пенопласта не влияет на набухание по толщине из-за его гидрофобной природы.
На рис. 9В показаны значения водопоглощения панелей. Значения водопоглощения (WA) значительно увеличиваются при увеличении толщины лицевого слоя с 3 до 5 мм. Значения WA также неуклонно увеличивались для всех панелей во время замачивания (с 2 до 786 ч), но скорость поглощения воды изменялась во время погружения. Интенсивное впитывание можно наблюдать в течение начального периода замачивания (48 часов), а при более длительном времени замачивания (от 48 до 786 часов) наблюдается почти линейная тенденция.Большая часть воды (> 60%) была впитана в начальный период (48 ч) замачивания. На значения WA в панелях с пенопластом влияли поверхностный слой (толщина и плотность) и структура ячеек пены (пустоты между ячейками и раздробленные ячейки) (Sabbahi и Vergnaud 1993; Link и др. .2011). Следовательно, сравнивая части A и B на фиг.9, можно констатировать, что поверхностные слои являются преобладающими факторами, влияющими на WA в течение начального периода выдержки (48 часов). Вода в основном поглощается как пустотами между ячейками пены, так и раздробленными ячейками при более длительном времени замачивания (от 48 до 786 часов).Также стоит отметить, что WA не прекращалась даже после 786 часов выдержки, что показывает, что вода медленно, но верно проникает во внутренние пустоты образцов (Schwartz и др.
, 1989).
Измерение выбросов формальдегида
Эмиссия формальдегида (FE) из панелей из пенопласта определялась колбовым методом, как показано на рис. 10. Результаты показали, что FE линейно увеличивается при увеличении толщины поверхностного слоя с 3 до 5 мм (коды C, D, и E).Каждый дополнительный миллиметр толщины поверхностного слоя приводит к увеличению FE на 19%. Более высокое количество древесных частиц и смолы, используемой для увеличения толщины поверхностного слоя, приводит к более высокому выбросу формальдегида (Petersen и др. , 1972).
Использование методов разделения поверхностного слоя (, например, , распыление воды или несмолистые частицы) является одним из наиболее важных этапов производства в одноэтапном процессе изготовления панелей с пенопластом. Следовательно, чтобы понять влияние методов разделения (распыление воды) на FE, панель, полученная в результате одноэтапного процесса (код C), сравнивали с контрольной панелью (код F). Результаты показали, что КЭ панелей, изготовленных в смоделированном одноэтапном процессе, почти вдвое больше, чем у контрольных панелей. Причину этого можно увидеть в разбрызгиваемой воде (60 г / м 2 ), используемой для отделения поверхностного слоя. Петерсен и др. . (1972) заявили, что содержание влаги в мате из ДСП влияет на КЭ производимых панелей. Для контроля эмиссии формальдегида изготовленных панелей был применен раствор мочевины и воды (код K) для разделения поверхностного слоя.Сравнение кодов C и K показало, что добавление мочевины уменьшило вдвое (примерно на 50%) КЭ панелей, изготовленных в одностадийном производственном процессе. Мочевина является одним из наиболее эффективных и в то же время самых дешевых поглотителей формальдегида на рынке (Ashaari и др. . 2016; Boran и др. . 2011). Колочный метод подходит только для внутреннего контроля производства древесных плит. Следовательно, официальных предельных значений не публиковалось.
Фиг.![]() |
ВЫВОДЫ
- Это исследование показало, что древесностружечные плиты из пенопласта с использованием жесткого полиуретана в качестве внутреннего слоя могут быть произведены в смоделированном одностадийном производственном процессе.
- Исследование показало, что методы производства (методы разделения и впрыска) не оказывают существенного влияния на характеристики панели, но свойства панелей эталонных панелей и панелей, полученных с помощью моделируемого процесса, значительно различались.Значения MOR, IB и FSW были значительно выше в контрольных панелях из-за лучшего качества их поверхностного слоя.
- Увеличение толщины поверхностного слоя (с 3 до 5 мм) увеличивает значения MOR и FSW и приводит к значительному снижению IB. TS и WA также были увеличены за счет увеличения толщины поверхностных слоев.
- TS и WA были интенсивными в течение начального периода замачивания (48 ч), а затем замедлились.
Результаты показали, что поверхностные слои были почти насыщенными после начального времени выдержки, что отражалось в чрезвычайно низком TS после начального времени выдержки.Однако вода все еще абсорбировалась в конце времени выдержки (до 786 ч), поскольку она мигрирует в пустоты между ячейками пены.
- Увеличение толщины поверхностного слоя приводит к увеличению КЭ образцов. Распыляемая вода как метод разделения почти вдвое увеличивает КЭ из образцов, что можно контролировать, добавляя мочевину в распыляемую воду.
- В целом, древесностружечные плиты из пенополиуретана показали хороший потенциал для использования в мебельной промышленности. Дальнейшие исследования полиуретановой рецептуры потребуются для улучшения структуры пены, которая соответственно может повлиять на характеристики панели.
БЛАГОДАРНОСТЬ
Авторы выражают признательность Иранскому национальному научному фонду (INSF) за финансовую поддержку этого исследования в рамках гранта № 93012950.
ССЫЛКИ
Аллен, Х. Г. (1969). Анализ и проектирование структурных сэндвич-панелей , Pergamon Press, Оксфорд, Великобритания.
ASTM D4672 — 12 (2012). «Стандартные методы испытаний полиуретанового сырья: определение содержания воды в полиолах», ASTM International, Вест Коншохокен, Пенсильвания, США.
ASTM D4699-03 (2013). «Стандартный метод испытания плотности вибрационной упаковки крупных сформированных частиц катализатора и носителя катализатора», ASTM International, West Conshohocken, PA, USA.
ASTM D4890 — 13 (2013). «Стандартные методы испытаний полиуретанового сырья: Определение цвета по Гарднеру и APHA полиолов», ASTM International, Вест Коншохокен, Пенсильвания, США.
ASTM D4878 — 15 (2015). «Стандартные методы испытаний полиуретанового сырья: определение вязкости полиолов», ASTM International, West Conshohocken, PA, USA.
ASTM D4274 — 16 (2016). «Стандартные методы испытаний полиуретанового сырья: определение гидроксильных чисел полиолов», ASTM International, West Conshohocken, PA, USA.
Ашаари, З., Ли, А. М. Х., Азиз, М. Х. А. и Нордин, М. Н. (2016). «Добавление гидроксида аммония в качестве поглотителя формальдегида для древесины сесендук ( Endospermum diadenum ), компрегнированной фенольными смолами», евро. Дж. Вуд Вуд Прод . 74 (2), 277-280. DOI: 10.1007 / s00107-015-0995-9
Боран, С., Уста, М., Гемуеская, Е. (2011). «Снижение выбросов формальдегида из древесноволокнистых плит средней плотности, произведенных путем добавления различных аминовых соединений к карбамидоформальдегидной смоле», Int. J. Adhes. Клеи. 31 (7), 674-678. DOI: 10.1016 / j.ijadhadh.2011.06.011
Чен, З., Янь, Н. (2012). «Исследование модулей упругости сэндвич-панелей с сотовым заполнением из крафт-бумаги», Compos. Часть B-англ. 43, 2107-2114. DOI: 10.1016 / j.compositesb.2012.03.008
EN 310 (1993).«Панели на основе древесины — Определение модуля упругости при изгибе и прочности на изгиб», Европейский комитет по стандартизации, Брюссель, Бельгия.
EN 310 (2010). «ДСП. Технические условия », Европейский комитет по стандартизации, Брюссель, Бельгия.
EN 317 (1993). «ДСП и древесноволокнистые плиты — определение разбухания по толщине после погружения в воду», Европейский комитет по стандартизации, Брюссель, Бельгия.
EN 319 (1993). «ДСП и древесноволокнистые плиты — Определение прочности на разрыв перпендикулярно плоскости плиты», Европейский комитет по стандартизации, Брюссель, Бельгия.
EN 323 (1993). «Древесные плиты — определение плотности», Европейский комитет по стандартизации, Брюссель, Бельгия.
EN 320 (1993). «ДВП. Определение сопротивления осевому извлечению винта », Европейский комитет по стандартизации, Брюссель, Бельгия.
EN 717-3 (1996). «Панели на древесной основе. Определение высвобождения формальдегида — Часть 3: Высвобождение формальдегида колбовым методом », Европейский стандарт, Брюссель, Бельгия.
EN 13446 (2002).«Панели на древесной основе. Определение выносливости крепежа », Европейский стандарт, Брюссель, Бельгия.
Фейфель, С., Поганиц, В. Р., Шебек, Л. (2013). «Использование легких плит для сокращения выбросов в атмосферу в деревообрабатывающей промышленности Германии — перспективы?» Environ. Sci. Евро. 25, 5. DOI: 10.1186 / 2190-4715-25-5
Грюневальд Дж., Парлевлит П. и Альтштадт В. (2015). «Изготовление термопластичных композитных сэндвич-конструкций; Обзор литературы », J.Термопласт. Compos . DOI: 10.1177 / 0892705715604681
Ионеску, М. (2005). Химия и технология полиолов для полиуретанов , Rapra Technology Limited, Великобритания.
Ли, Дж., Хант, Дж. Ф., Гонг, С., и Цай, З. (2014). «Высокопрочные сэндвич-панели на основе древесины, армированные стекловолокном и пеной», BioResources 9 (2), 1898-1913 гг. DOI: 10.15376 / biores.9.2.1893-1913
Линк, М., Колбич, Ч, Тонди, Г., Эбнер, М., Виланд, С., Петучниг, А.(2011). «Пены на основе танинов без формальдегида и их использование в качестве легких панелей», BioResources 6 (4), 4218-4228. DOI: 10.15376 / biores.6.4.4218-4228
Людтке Дж. (2011). «Разработка и оценка концепции непрерывного производства легких панелей, включающих полимерный сердечник и древесную облицовку», докторская диссертация , Гамбургский университет, Гамбург, Германия.
Петерсен, Х., Ройтер, В., Эйзеле, В., и Виттманн, О. (1972). «Zur Formaldehydeab-spaltung bei der Spanplattenerzeugung mit Harnstoff-Formaldehyde-Bindermitteln», Holz Roh Werkst. 31 (12), 463-469. DOI: 10.1007 / BF02613831
Э. Роффаэль (1993). Формальдегид из ДСП и других деревянных панелей , Институт лесных исследований Малайзии (FRIM), Куала-Лумпур, Малайзия.
Саббахи А. и Верно Ж. М. (1993). «Поглощение воды пенополиуретаном. Моделирование и эксперименты », евро. Polym. J. 29 (9), 1243-1246. DOI: 10.1016 / 0014-3057 (93)
-9
Шалбафан А., Веллинг Дж. И Людтке Дж. (2012). «Влияние параметров обработки на механические свойства сэндвич-панелей с легким пенопластом», Wood Mater. Sci. Англ. 7 (2), 69-75. DOI: 10.1080 / 17480272.2012.661459
Шалбафан А., Веллинг Дж. И Людтке Дж. (2013a). «Влияние параметров обработки на физические и структурные свойства легких сэндвич-панелей с пенопластом», Wood Mater. Sci. Англ. 7 (2), 69-75. DOI: 10.1080 / 17480272.2012.684704
Шалбафан А., Людтке Дж., Веллинг Дж. И Фрювальд А. (2013b). «Физиомеханические свойства сверхлегких древесностружечных плит из вспененного материала: различная плотность сердцевины», Holzforschung 67 (2), 169-175.DOI: 10.1515 / hf-2012-0058
Шварц, Н. В., Бомберг, М., и Кумаран, М. К. (1989). «Пропускание водяного пара и накопление влаги в пенополиуретане и полиискоцианурате», ASTM STP 1039, H.R. Trechsel и M. Bomberg (ред.), Американское общество испытаний и материалов, Филадельфия, Пенсильвания, стр. 63-72.
Зонненшайн, М., Кунсе, В. (2012). «Полиуретаны», в: Энциклопедия науки и технологий полимеров , 4 th Ed. , H. Mark (ed.), John Wiley & Sons, Хобокен, Нью-Джерси. DOI: 10.1002 / 0471440264.pst295
Винсон, Дж. Р. (2005). «Сэндвич-конструкции; Прошлое, настоящее и будущее »в: Многослойные конструкции 7; Продвижение сэндвич-структур и материалов: материалы 7-й Международной конференции по сэндвич-конструкциям . О. Т. Томсен, Э. Божевольная и А. Ликегард (ред.), Ольборгский университет, Ольборг, Дания, стр. 29-31.
Зенкерт, Д. (1997). Знакомство с сэндвич-конструкцией , Engineering Material Advisory Services Ltd., Крэдли Хит, Великобритания.
Статья подана: 12 июля 2016 г .; Рецензирование завершено: 4 сентября 2016 г .; Доработанная версия получена и принята: 5 сентября 2016 г .; Опубликовано: 22 сентября 2016 г.
DOI: 10.15376 / biores.11.4.9480-9495
Улучшенные методы производства пенополиуретана
Вы находитесь здесь
Домой »Улучшенные методы производства пенополиуретанаНовые поверхностно-активные вещества делают производственный процесс более экологически безопасным
Метиленхлорид, токсичное химическое вещество, способствующее загрязнению воздуха, недавно было исключено из использования в США. S. полиуретановая промышленность. Это обязательное исключение не позволило производить как можно больший диапазон сортов пенопласта с использованием хлористого метилена, что поставило промышленность США в невыгодное положение с точки зрения конкуренции. Air Products and Chemicals, Inc. при финансовой поддержке AMO разработала новые силиконовые поверхностно-активные вещества, позволяющие эффективно производить весь спектр сортов пенопласта с использованием более экологически безвредного вспенивателя CO 2 . Помимо снижения токсичности, новый процесс потребляет меньше энергии и снижает чистый выброс CO 2 , который влияет на глобальное потепление.
Проблемы при использовании жидкого CO 2 в качестве вспенивающего агента включают быстрое испарение, быстрое образование пузырьков и трудности в поддержании мелкопористой структуры в пене. Новые поверхностно-активные вещества решают эти проблемы путем эмульгирования вспенивающего агента, тем самым сохраняя мелкие ячейки во время вспенивания. Силиконовые поверхностно-активные вещества достигли превосходных характеристик, что привело к более мелкой структуре ячеек (лучший выход), большей высоте пучков (больший выход), лучшему градиенту физических свойств сверху вниз (консистенция продукта) и лучшей совместимости с антипиренами.
Воздействие коммерциализированной технологии
2006 | 2007 | 2008 | 2009 | 2010 | 2011 | ||
---|---|---|---|---|---|---|---|
Экономия энергии (триллион БТЕ) | 0,024 | 0,082 | 0,087 | 0,103 | 0,117 | 0,129 | |
Сокращение выбросов (Тысяч тонн) | Углерод | 0.421 | 1.452 | 1,549 | 1,834 | 2,075 | 2,281 |
НЕТ x | 0,003 | 0,011 | 0,012 | 0,014 | 0,016 | 0,018 | |
SO x | 0,003 | 0,009 | 0,009 | 0,011 | 0,012 | 0,014 | |
Твердые частицы | 0.![]() | 0,000 | 0,000 | 0,000 | 0,000 | 0,000 |
Обзор
Приложения
Может использоваться в производстве пенополиуретана.
Возможности
- Исключает использование токсичного хлористого метилена.
- Увеличивает выход пены за счет более мелкой структуры пены.
- Улучшает совместимость с антипиренами.
Преимущества
Производительность
Увеличивает выход за счет более мелкой ячеистой структуры пены, большей высоты пучков и улучшенных градиентов физических свойств сверху вниз.
Безопасность
Улучшает совместимость с антипиренами.
Сокращение отходов
Снижает токсичность процесса и более эффективно использует вспениватель CO 2 для снижения выбросов CO 2 в атмосферу.
Контактная информация
Марк Листеманн
(610) 481-8590
[email protected]
Air Products and Chemicals, Inc.
Как производится пенополиуретан?
Что такое пенополиуретан?
Пенополиуретан — один из четырех основных типов продуктов, которые могут быть изготовлены из сырого жидкого полиуретана.Они состоят из двух химических веществ, которые при смешивании и нагревании образуют жидкий полиуретан перед дальнейшей обработкой. Эти химические вещества представляют собой полиол, тип сложного спирта, и диизоцианат, побочный продукт нефти, который сильно реагирует со спиртом. Комбинируя их, образуется стабильная длинноцепочечная молекула. Это полимер или пластик, известный как уретан.
Для чего используется пенополиуретан?
Пенополиуретан используется в основном для набивки постельных принадлежностей и мебели. Он гипоаллергенен, нетоксичен и не разлагается со временем. Это означает, что наполненные им подушки всегда будут восстанавливать свою форму, независимо от того, через какое наказание они подвергаются. Кровати из пенопласта также становятся популярными. Прочный слой поролона формирует тело по размеру. Упаковочные арахисы и пенопласты также используются судоходными компаниями по всему миру.
Как производится пенополиуретан?
После того, как два ингредиента были объединены с образованием горячего жидкого полиуретана, они проходят по трубе в головку сопла.Под головкой находится ряд роликов, по которым проходит вощеная бумага. Сопло распыляет мелкую струю горячей жидкости на вощеную бумагу, смешиваясь с потоками углекислого газа, поступающими из другого сопла. Это заставляет полиуретан расширяться при движении вниз по конвейерной ленте, образуя полосу пенопласта. Края пенопласта обрезаются и сжимаются, чтобы он сохранял жизнеспособную форму. Пена состоит из неисчислимого количества крошечных пузырьков газа, захваченных полиуретаном. Если не будет выпущен газ, пена приобретет консистенцию камня.Итак, пена проходит под рядом тепловых ламп. Он сушит пену и заставляет пузыри расширяться, а затем лопнуть, оставляя после себя готовый губчатый пористый материал.
Производство и изготовление гибкого пенополиуретана: Национальные стандарты выбросов опасных загрязнителей воздуха (NESHAP) для зональных источников | Стационарные источники загрязнения воздуха
На этой странице:
Сводка правил
Изготовление гибкого пенополиуретана
Окончательные национальные стандарты по выбросам опасных загрязнителей воздуха (NESHAP) запрещают использование хлористого метилена при производстве пенопласта.Площади источников изготовления гибкого пенополиуретана разрезать или склеить детали из гибкого пенополиуретана
вместе или с другими субстратами, и эти детали затем используются в мягкой мебели, такой как мебель, легковые и грузовые автомобили и некоторые приборы.
Эти стандарты реализуют разделы 112 (d) и 112 (k) Закона о чистом воздухе и основаны на решении Администратора о том, что выбросы от производства гибкой полиуретановой пены вызывают или вносят значительный вклад в загрязнение воздуха, которое, как можно разумно ожидать, представляет опасность для населения здоровье или благополучие.На предприятиях, где работают формованные пенопласты, пенопласты и пены, а также на участках производства пенопластов, которые работают с петлевыми резчиками, должны быть подготовлены и сохранены сертификаты соответствия, подтверждающие, что на предприятии не используются запрещенные продукты на основе хлористого метилена. Местные заводы-источники должны также вести записи, подтверждающие, что используемые ими продукты не содержат хлористого метилена.
Гибкий пенополиуретан Производство:
Последний NESHAP сокращает использование хлористого метилена при производстве пеноматериалов.Эти операции создают гибкую полиуретановую пену, используемую в мягкой мебели, такой как мебель, легковые и грузовые автомобили, а также в некоторых приборах. Эти стандарты реализуют разделы 112 (d) и 112 (k) Закона о чистом воздухе и основаны на определении Администратора о том, что выбросы от производства гибкой полиуретановой пены вызывают или значительно способствуют загрязнению воздуха, которое, как можно разумно ожидать, может угрожать здоровью населения. или благосостояние.
Для источников в зоне производства плитной пены правило требует ограничения выбросов и методов управления для снижения выбросов хлористого метилена из производственной линии, резервуаров для хранения, протекающего оборудования и очистки оборудования.Пределы выбросов для хлористого метилена, используемого в качестве вспомогательного вспенивающего агента (ABA), основаны на формуле, которая варьируется в зависимости от марки производимой пены. Для резервуаров для хранения хлористого метилена требуются системы баланса паров или угольные слои. Практика управления требует, чтобы заводы выявляли и устраняли утечки в насосах и другом оборудовании в сфере обслуживания хлористого метилена. В частности, владельцы или операторы должны периодически проверять утечки оборудования (от ежеквартального для насосов и клапанов до ежегодного для разъемов) с использованием метода 21 EPA (40 CFR часть 60, приложение A).Утечки, которые определяются как значение 10 000 частей на миллион (ppm) или больше, должны быть устранены в течение пятнадцати дней с момента их обнаружения. Использование хлористого метилена для очистки смесительных головок и другого оборудования запрещено.
История правил
12.02.2021 — Правило, предложенное перед публикацией; продление периода общественного обсуждения
11.01.2021 — Предлагаемое правило | Предлагаемые правки правила
28.03.2008 — Прямое окончательное правило с техническими исправлениями
16.07.2007 — Окончательное правило
04.04.2007 — Предлагаемое правило
Дополнительные ресурсы
Информационный бюллетень — Предлагаемые поправки к стандартам по токсичности воздуха для производства и изготовления гибкой полиуретановой пены
Информационный бюллетень: Окончательные стандарты токсичности воздуха для зональных источников в семи отраслях промышленности
Просмотрите сопроводительные документы в папке списка, чтобы найти дополнительные документы, связанные с этим правилом.
Производство гибкой полиуретановой пены: национальные стандарты выбросов вредных веществ, загрязняющих воздух | Стационарные источники загрязнения воздуха
На этой странице:
Сводка правил
Это действие вводит национальные стандарты выбросов опасных загрязнителей воздуха (NESHAP) для новых и существующих заводов, которые производят гибкий пенополиуретан. Исходное правило, основанное на технологии, изданное в 1998 году, регулирует выбросы метиленхлорида, 2,4-толуолдиизоцианата (TDI), метилхлороформа, метилендифенилдиизоцианата (MDI), оксида пропилена, диэтаноламина, метилэтилкетона, метанола и толуола.На хлористый метилен приходится более 98% всех выбросов вредных веществ в атмосферу, производимых промышленностью.
Стандарты сокращают выбросы опасных загрязнителей воздуха (HAP) из всех существующих источников производства гибкой полиуретановой пены более чем на 14 000 тонн в год (т / год), что на 70 процентов ниже базового уровня. В 2014 году EPA оценило остающийся риск и любые обновления технологии и выпустило правило, обеспечивающее повышенную защиту. Окончательные поправки к правилам не приводят к какому-либо количественному сокращению фактических выбросов HAP.Однако, по нашим оценкам, потенциальный рост выбросов в будущем сократится на 735 т / год.
История правил
15.08.2014 — Окончательное правило
11.04.2013 — Предлагаемое правило
10.07.1998 — Окончательное правило
03.02.1997 — Поправка
27.12.1996 — Предлагаемое правило и уведомление о публичных слушаниях
Дополнительные ресурсы
Сводка комментариев и ответов общественности
Основы и цель предлагаемых стандартов
Документ с дополнительной информацией к предлагаемым стандартам
Анализ экономического воздействия (ОВОС) предлагаемых стандартов
Информационные бюллетени
СоответствиеРуководство на простом языке по производству гибкого пенополиуретана NESHAP 40 CFR 63, Subpart III
производителей пенопласта | Поставщики пенопласта
Список производителей пенопласта
Термин «изготовление пенопласта» также может использоваться для описания типов пенопласта, а также различных применений и продуктов, которые могут быть изготовлены из них.
Производство пены создает продукты и материалы, которые обеспечивают такие услуги, как изоляция, герметизация, поглощение жидкости, гашение вибрации, амортизация, защита, звукоизоляция, фильтрация и обеспечение структуры.
Готовая пена используется в широком спектре отраслей, таких как мебель, электроника, автомобилестроение, строительство, здравоохранение, бытовая техника, акустика и фильтрация. Он также используется на нефтяных вышках, спутниках и в метеозондах.
Произведенная продукция Продукция из пеноматериала
Услуги по производству пенопласта позволяют создавать различные типы пенопласта для множества применений.
Пенопласт с открытыми ячейками — это гибкий пенопласт с ячейками, которые пропускают воздух.
Пенопласт с закрытыми ячейками имеет плотные ячейки, изолированные друг от друга. Они не пропускают воздух.
Акустические пены — это ослабленные или не ослабленные гибкие пены, которые соответственно поглощают или формируют звук.
Упаковочные пены — любые пены, используемые для упаковки и транспортировки продуктов.
Связанная пена — это пенопласт, который изготавливается, когда производители склеивают измельченный пенопласт или частицы пены вместе в блок. Связанные пеноматериалы чаще всего используются в качестве амортизирующего материала для ковров.
Гибкий пенопласт обладает некоторой упругостью и обычно используется в постельных принадлежностях и мебели.
Пенопласт на клеевой основе позволяет пользователям удерживать пенопласт на месте.Он также поддерживает постоянное равномерное давление. Пены на клеевой основе популярны в медицине.
Пенопласт обеспечивает амортизацию как мебели, так и спортивного снаряжения.
Формованная пена — это ячеистая пена, сохраняющая свою форму. Если у него достаточно давления для сжатия под давлением, он вернется к своей исходной форме формы, когда вы уберете давление.
Жесткая пена — это влагостойкая и термостойкая пена с закрытыми порами.
Производство пеноматериала — American Excelsior Company
Продукция из пенополиуретана
Примеры изделий из пенополиуретана включают изолированные контейнеры, мягкие сиденья из пеноматериала, защитную прокладку из пеноматериала, изоляционную пену, прокладки для ЭКГ, прокладки для позиционирования рентгеновских лучей и хирургические скрубберы.
Примеры продуктов из пенополиэтилена включают в себя связующий и амортизирующий материал. Подобные материалы используются для обработки, упаковки и транспортировки таких предметов, как одежда, продукты питания, спортивные товары, вывески, мебель и детали компьютеров.
Примеры других изделий из вспененного материала включают прокладки, набивки для стоек, подушки для диванов, изоляцию, набивную пену в тапочках, губки, изоляционную пену, маты, фильтры, вставки из ортопедической пены, уплотнения NVH, фильтрующую пену в кондиционерах, матрасы из пены с памятью и подушки из пены с эффектом памяти.
История Люди начали производить пену и изделия из нее в период между 1920-ми и 1930-ми годами, после того как они научились производить латексную пену. Первыми двумя методами создания полимерных пен были процесс Талалай и процесс Данлоп. Процесс Талалай был первоначально разработан в 1930-х годах братьями Талалай, Джозефом, Леоном и Ансельмом. Позже Джозеф Талалай основал компанию Vita Talalay, базирующуюся в Нидерландах, с заводами в США, Великобритании и Канаде.Процесс Dunlop был запатентован Dunlop Rubber Company в 1929 году.
Благодаря этим разработкам компании по всему миру получили возможность создавать пенопласт для постоянно расширяющегося списка приложений. Одна из причин, по которой применение изготовления пеноматериалов так быстро распространилось в середине 20-го века, заключается в том, что, подстегиваемые спросом во время Второй мировой войны, ученые каждый день открывали и разрабатывали новые резиновые материалы и химические вещества. В 1947 году, например, исследователи из Dow Chemical изобрели пенополистирол или пенополистирол.
Сегодня производители продолжают производить пену для всех видов применения. В последние годы они сделали ряд прорывов, включая разработку нанопористых полимерных пен. Одним из наиболее актуальных направлений нашего времени является устойчивость. Для борьбы с потенциальным воздействием на окружающую среду производственных процессов и отходов пенопласта производители отказались от сжигания лома и теперь повторно используют или перерабатывают его.
Производители могут использовать различные материалы для вспенивания.К ним относятся пластик, каучуки и эластомеры низкой плотности, такие как полиуретан, полиэтилен, сшитый полиэтилен, полиэфир, ПВХ и пенополистирол (ESP).
Пластмассы образуют пену с крошечными, хорошо диспергированными пузырьками газа. Пенопласт легкий, с высоким соотношением прочности и веса.
Пенополиуретан является наиболее часто используемым. Это прочная пена с закрытыми порами, которая может разлагаться как под прямыми, так и под прямыми солнечными лучами.
Полиэтилен является наиболее распространенным материалом для изготовления пенопласта. Пенополиэтилен эластичен, амортизирует, гасит вибрации и изолирует. Производители экструдируют вспененный пенопласт с закрытыми порами в основном в качестве защитного материала.
Один особый тип вспененного полиэтилена известен как Ethafoam, который обладает исключительными характеристиками поглощения ударов.
Сшитый полиэтилен , или XLPE, химически и физически устойчив. В виде пены он гладкий, толстый и очень мелкоячеистый.
Полиэфирная пена — это недорогая пена с закрытыми порами, обладающая адекватными акустическими и упаковочными свойствами.
ПВХ , или винил, является самозатухающим, влагостойким и устойчивым к гниению. Создает мягкую, податливую пену с закрытыми порами, которая хорошо сцепляется с клеями. Он используется в прокладках для предотвращения проникновения воды.
Пенополистирол , или EPS, используется для различных применений, таких как набивка тапочек, изоляционная пена, нефтяные вышки, пенопласт для фильтров в кондиционерах, спутниках и метеозондах.
1.Изготовление пены
Изготовители обычно образуют пену путем смешивания полимеров с газообразователем и другими химическими веществами. Когда они добавляют газообразующий агент, материал расширяется, образуя полосу пены, которая состоит из бесчисленных пузырьков газа внутри материала.
2. Формование пенопласта
После изготовления пенопласта производители могут использовать различные услуги по изготовлению пенопласта, такие как резка пенопласта, высечка, гидроабразивная резка, термоформование и валяние из пенопласта.
Высечка включает вырезание различных форм из полос, листов или блоков пенопласта.
Водоструйная резка в основном выполняет ту же функцию, но использует струю воды под высоким давлением и может резать с большей точностью, чем высечка.
Термоформование — самый популярный метод пенообразования. Во время этого процесса производители изготавливают формы для механической обработки, нагревая объемные вспененные материалы.
Пенное валяние — это еще один процесс образования пены, во время которого производители сжимают и отверждают толстые мягкие вспененные материалы для образования более плотных вспененных материалов.
3. Утилизация лома
На некоторых этапах процесса производства пеноматериала образуется много лома, в том числе в процессе высечки. Во время высечки обрезки пенопласта могут быть результатом изменений в процессе обработки, останова и запуска производственной линии или материала, оставшегося после высечки форм. К тому же лом бывает по истечении срока службы пенопластов.
Итак, после того, как процесс изготовления пенопласта завершен, производителям необходимо утилизировать отходы.Предпочтительный способ сделать это — переработка.
Другой способ утилизации обрезков пенопласта — их сжигание. Однако популярность этого метода за последние несколько десятилетий снизилась. Хотя правительство США в целом считает сжигание пены нетоксичным, рост экологических проблем и ужесточение правил, касающихся выбросов углекислого газа, побудили компании обращаться с пенными отходами путем их переработки.
При подготовке к изготовлению изделия из пеноматериала производители рассматривают такие переменные, как тип материала, который они будут использовать, производственные процессы, которые они будут использовать, форма изделия, толщина изделия и стандартные требования.Одно из важных решений, которое они принимают, — будут ли они создавать ваш продукт из пены с закрытыми или открытыми ячейками.
Пенопласт с закрытыми порами содержит ячейки пены, которые герметизированы и отделены друг от друга, или «закрыты». Пенопласт с закрытыми порами обладает высокой прочностью на сжатие и высокой плотностью. Ячейки расширяются под воздействием нагретого газа, потому что ячейки не ломаются, а молекулы жидкости и газа не могут свободно перемещаться от ячейки к ячейке. Поскольку расширяющийся материал заполняется, пеноматериал с закрытыми порами является идеальным материалом для использования в качестве теплоизолятора.
Пена с открытыми порами легче по весу, губчатая и мягкая. Поверхности пузырьков, или стенки ячеек, разрушены, и все пространства в материале заполнены воздухом. Мягкая и непрочная природа поролона с открытыми порами делает этот материал идеальным для изготовления поролоновых подушек и набивки из поролона. Пенопласт с открытыми порами также вдвое более устойчив к звуку, чем его аналог с закрытыми порами, и поэтому может использоваться в качестве эффективного звукового барьера.
Чтобы ваш продукт работал лучше на вас, производители пенопласта могут создать множество индивидуальных продуктов из пенопласта.Для изготовления изделий на заказ производители используют индивидуальные формы, нестандартные материалы, уникальные цвета и уникальные формы и размеры. Узнайте больше о том, какие индивидуальные варианты пенопласта предлагают конкретные производители пенопласта, обсудив это с одним из их сотрудников.
Преимущества Производство пеноматериала является выгодным процессом по ряду причин. Во-первых, он универсален. С его помощью производители могут изготавливать пенопласт с широким спектром качеств, от экстремальной жесткости до чрезвычайной гибкости. Кроме того, детали, изготовленные из пенопласта, обычно более легкие, чем сопоставимые изделия, изготовленные с помощью других процессов формования.Это особенно выгодно для клиентов, использующих легкие детали, например, производство автомобилей. Еще одна замечательная особенность производства пенопласта — это то, что из него получаются такие хорошие изоляторы, независимо от области применения. Это огромное преимущество для приложений, связанных с акустикой, вибрацией или теплоизоляцией. Кроме того, производство пенопласта является экономичным, особенно если вы ищете продукцию оптом. Это верно в двух случаях, так как производители могут использовать пенопласт.Пенопласт можно измельчить, измельчить и повторно использовать для таких продуктов, как набивка для ковров или наполнитель для подушек и другой мебели. Вторичная переработка позволяет компаниям, производящим пенопласт, вернуть свои инвестиции, которые в противном случае были бы потеряны при сжигании лома.
Если вас интересует готовый пенопласт, вам необходимо обратиться к опытному производителю, который проведет вас через весь процесс. Поскольку изготовление пенопласта является популярным процессом, существует множество компаний, предлагающих услуги по изготовлению пенопласта.К сожалению, не все они одинакового уровня, и их легко разбить. Чтобы помочь вам на вашем пути, мы составили список высококачественных переработчиков пенопласта с самым высоким рейтингом. Вы найдете их информацию зажатой между этими абзацами. Прежде чем вы начнете их изучать, рекомендуем потратить некоторое время на составление собственного списка. Этот список должен включать ваши спецификации, стандартные требования, объем запросов на продукт, бюджет, сроки и предпочтительный стиль доставки.После того, как вы составите свой список, вы можете начать просматривать веб-сайты производителей, которые мы предоставили. Во время просмотра сравнивайте их список продуктов и услуг с вашим списком спецификаций. Выберите трех или четырех и обратитесь к ним. Обсудите свой проект подробно, не оставляя камня на камне. Поговорив с каждым из них, решите, какой из них может предоставить вам лучший сервис, и приступайте к работе. Удачи!
Производство пеноматериала Информационный видеоролик
Как производится пенопласт? производство поролона
Как производится поролон
В поролоне используется другой агент, обычно газ или химическое вещество, выделяющее газ, для создания массы маленьких пузырьков в смеси жидкостей.
Эта смесь может содержать полиолы, полиизоцианаты, воду и добавки, такие как антипирены, наполнители и красители.
Существует множество различных типов вспенивающих агентов, которые способны образовывать клеточную основу, и составитель смеси контролирует вспенивание, регулируя количество воды или используя такие агенты, как поверхностно-активное вещество.
Полиолы и полиизоцианаты в пене представляют собой жидкие полимеры, которые в сочетании с водой вызывают тепловыделение или экзотермическую реакцию. Используя определенные типы и комбинации жидких полимеров, производитель материалов может производить поролон, который может быть гибким или жестким.
Во время процедуры полимеризации молекулы полиолов и полиизоцианатов сшиваются с образованием трехмерных структур.
Невозможно переоценить важность вспенивателей в производстве поролона, поскольку они связаны с гибкостью и жесткостью.
Обычно в эластичных пенопластах используется газообразный диоксид углерода, образующийся при реакции воды с полиизоцинатом.В большинстве жестких пен используются гидрофторуглероды (ГФУ) и гидрохлорфторуглероды (ГХФУ), газы с более высокими уровнями токсичности и воспламеняемости, чем хлорфторуглероды (ХФУ).
Применение пенопласта
Гибкие пенополиуретаны используются для контроля вибрации и поглощения ударов. Они обеспечивают повышенное поглощение энергии с повышенной плотностью, предсказуемыми характеристиками при сжимающей силе и низкой остаточной деформацией при постоянном сопротивлении.
Эти пенопласты не станут шире при сжатии, что делает их хорошим выбором в условиях ограниченного пространства.Различные области применения включают прокладки капота в мобильном оборудовании, амортизаторы для промышленного оборудования и виброизоляторы для бытовой техники.
Полистирол — это жесткие конструкционные материалы, которые отличаются прочностью, легкостью и влагостойкостью.
Они помогают снизить вес продукта и имеют высокое отношение жесткости к массе. Другие типы структурных пен имеют сэндвич-структуру с пенопластом между двумя тонкими, но прочными слоями. Сетчатые пены используются для фильтров и смешиваются с бактерицидами, фунгицидами и другими добавками.
Поролон, из которого изготавливаются эластомерные прокладки, можно прикрепить к вакуумному инструменту для изготовления.
При производстве поролона листовые материалы или экструзии превращаются в готовую продукцию. Гидроабразивная резка позволяет выполнять мелкие и быстрые разрезы, а также исключает неправильные разрезы и отходы материала, связанные с операциями ручной резки. Изготовленные на заказ изделия из поролона также поддерживают использование лент, в которых используется либо система термоактивируемых лент (HATS), либо самоклеящийся клей (PSA).
Для индивидуальных прокладок доступны различные методы склеивания, но не все из них подходят для поролона.
Как производится губчатая резина
Как и поролон, губчатая резина имеет ячеистую структуру и доступна с различной плотностью. Обычно они бывают мягкими, средними и твердыми. У нас есть два типа губчатой резины.
Материалы с открытыми порами содержат открытые, взаимосвязанные карманы с пузырьками газа, которые пропускают воздух, воду и другие химические вещества, когда материал не сжимается.
Губчатая резина с закрытыми ячейками содержит баллонные ячейки, которые удерживают газообразный азот и, таким образом, предотвращают прохождение этих веществ при низких давлениях.
Для производства губчатой резины с открытыми порами бикарбонат натрия добавляют к другим ингредиентам в нагретой форме. Когда незатвердевший бисквит поднимается вверх, как торт, пищевая сода создает открытые взаимосвязанные клетки.
Для изготовления губчатой резины с закрытыми порами добавляется химический порошок, разлагающийся под действием тепла и давления. Выделяющийся газообразный азот помогает придать губчатой резине с закрытыми порами высокие характеристики сжатия и восстановления.
Хотя азот является газом, он не образует пену, как газообразные порообразователи, используемые с поролоном.
Также читайте: Вспененный каучук SBR
Вспенивание — это особый производственный процесс, и поролон в основном содержит открытые ячейки. Хотя некоторые ячейки в поролоне закрыты, эти резиновые материалы не будут проходить испытания ASTM на водопоглощение, стандартное требование для материалов с закрытыми порами.
Как используется губчатая резина
Губчатая резина изготавливается из неопрена, EPDM, нитрила, силикона и многих других эластомерных материалов. Часто из профилей из губчатой резины изготавливают готовые прокладки, которые используются для амортизации и обеспечивают хорошее сжатие и восстановление.
Листы губчатой резины также используются в различных производствах, таких как изготовление, включая операции с добавленной стоимостью, такие как наклеивание прокладок. По сравнению с твердой резиной, губчатая резина более мягкая и менее устойчивая к сжатию; кроме того, губчатая резина по-прежнему имеет высокое отношение прочности к массе.
Пенопласт с открытыми ячейками используется в протезах, медицинских губках, прокладках для электрокардиограммы (ECD), медицинских фильтрах и стерилизационных пакетах.
Для всех этих применений требуются эластомерные компоненты, которые пропускают воду и газы. Пенопластовые или резиновые детали также используются в подъемниках для пациентов, оборудовании больничных палат, которое помогает людям с ограниченными физическими возможностями садиться или вставать.
Губчатая резина с закрытыми порами, изготовленная из фторсиликона, используется в фармацевтическом оборудовании, таком как машины для таблетирования.