Завод по производству ламината
- Защитный слой (оверлей) предназначен для защиты от внешних воздействий.
- Декоративный слой — это специальная бумага, имитирующая структуру и цвет различных пород деревьев или керамической плитки.
- Плита ХДФ — основа ламината, древесноволокнистая плита высокой плотности.
- Стабилизирующий слой предназначен для защиты HDF плиты от деформации и защиты ламината от влаги.
- Замковая система при помощи этих замков панели ламината плотно скрепляются между собой без применения клея.
Ламинат технология
Изготовление ламината из плиты HDF c импрегнацией верхних слоев – это процесс состоящий из следующих этапов:
- облицовывание плиты;
- распил и фрезерование панелей;
- упаковка.
Импрегнация – это пропитывание материала специальными составами. Верхние слои ламината пропитываются смолами с различными добавками, при застывании, которые образуют прочный слой.
Ламинат завод производит ламинат прямого прессования DPL. При технологии DPL происходит одновременное спрессовывание при высокой температуре всех слоев ламината. При этой технологии производства ламината не используется клей, так как применяются слои прошедшие процесс импрегнации, которые при горячем прессовании (до 200°С) плавятся и склеивают поверхности. После отверждения, смола и оверлей превращаются в монолитный поверхностный слой ламината.
Облицовывание плит
Для получения ламинированной плиты необходимо произвести облицовку HDF плиты бумажно-смоляными пленками и оверлеем.
Распилка и фрезерование панелей
Последним важным этапом производства является изготовление ламината необходимого размера. При помощи распиловочного оборудования для ламината листы ламината нарезаются на необходимые размеры.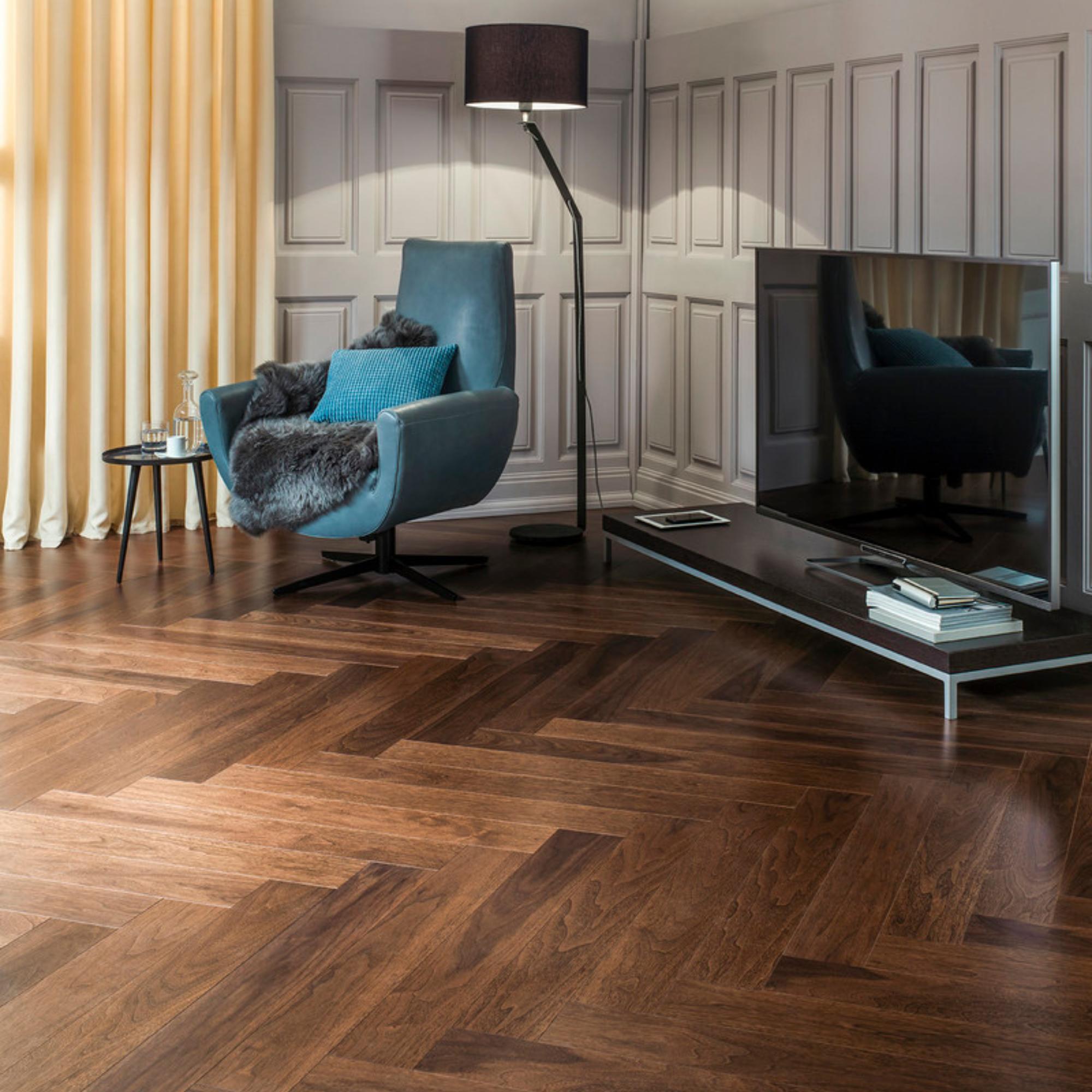
Упаковка
Происходит упаковка в термоусадочную полиэтиленовую (ПЭ) пленку готового ламината.
Оборудование для производства ламината
Состоит из:
- Станок для ламинирования ZYX1400; ZYX1600.
- Станок для распиловки ламината DP-2700.
- Линия для фрезерования замка click на ламинате FHZ525+FHH625.
- Станок для упаковки ламината TS-200.
1. Горячий пресс для ламинирования плит HDF высокого давления
Применяются при производстве ламината. Прессы изготавливаются под различные размеры плит ХДФ: 2800Ч2070 мм, 2440Ч1830 мм, 2440Ч2070 мм. Прессы высокого давления «ZYX» имеют различную производительность и усилие прессования, поставляются с подающим и приемным столом.
Технические особенности
Мощные гидроцилиндры диаметром 380 мм обеспечивают высокое давление — 27,4 кг/см2. Возможно увеличение удельного давления до 30,8 кг/см2; 34,3 кг/см2 или 37,7 кг/см2. |
|
Эргономичный пульт управления. |
Технические характеристики | ||
Модель | ZYX1400 | ZYX1600 |
Общее давление (т) | 1400 | 1600 |
Удельное давление (кг/см2) | 27,4 | 27,4 |
Расположение цилиндров | верхнее | верхнее |
Диаметр гидроцилиндров (мм) | 340 | 380 |
Количество гидроцилиндров (шт) | 6 | 6 |
Производительность (шт/день) | 1200 | 1200 |
Размер плиты (мм) | 2440х1830 | 2800х2070 |
Максимальное раскрытие плит (мм) | 200 | 200 |
Мощность бойлера (КВт) | 31 | 31 |
Габаритные размеры (мм) | 3300х2000х3500 | 3700х2200х3500 |
Масса станка (кг) | 17000 | 20000 |
2. Станок для раскроя ламината DP-2700
Предназначен для распиловки ламината на необходимые размеры для последующего фрезерования замков. У каждого производителя свои размеры ламината.
Технические характеристики | |
Максимальная ширина плиты (мм) |
2700 |
Максимальная высота пропила (мм) | 30 |
Диаметр пил (мм) |
180-250 |
Посадочный диаметр пил (мм) |
75 |
Частота вращения пил (об/мин) |
2500 |
Суммарная мощность (КВт) | 23,7 |
Скорость подачи (м/мин) |
3-15 |
Габаритные размеры (мм) | 2000х3300х1350 |
Масса станка (кг) | 3450 |
3. Линия фрезерования ламината FHZ525+FHH625
Автоматическая высокоскоростная линия предназначена для изготовления замка (Click) на ламинате. Она оснащена дополнительными прирезными шпинделями, что исключает сколы по всему периметру заготовки и гарантирует высокое качество готового изделия. Рабочая поверхность стола оснащена твердосплавными платинами, что обеспечивает долговечность работы оборудования и уменьшает износ поверхности стола. Приемный стол оснащен автоподатчиком заготовок для увеличения скорости подачи до 80 м/мин.
Технические характеристики | |
Автоподатчик | SSJ01 |
Скорость подачи (м/мин) | 20-80 |
Мощность привода подачи (КВт) | |
Габариты (мм) | 3100х600х1400 |
Продольно-фрезерный станок | FHZ525 |
Максимальная ширина обработки (мм) | 250 [270 — опция] |
Минимальная ширина обработки (мм) | 95 |
Скорость подачи (м/мин) | 20-80 |
Мощность привода подачи (КВт) | 9 |
Частота вращения шпинделей (об/мин) | 6000-8000 |
Мощность вертикальных шпинделей | 6х8КВт |
Мощность финишных шпинделей «Click» | 4х6,5КВт |
Мощность двигателя регулировки ширины (КВт) | 1,5 |
Диаметр шпинделей (мм) | 40 |
Диаметр инструмента на шпинделях (мм) | 280 |
Диаметр аспирационных патрубков (мм) | 120 |
Суммарная мощность (КВт) | 83 |
Транспортер | SSJ02 |
Скорость подачи (м/мин) | 20-80 |
Суммарная мощность (КВт) | 2 |
Габариты (мм) | 2880х600х1400 |
Двухсторонний шипорезный станок | FHH625 |
Максимальная длина заготовки (мм) | 2500 |
Минимальная длина заготовки (мм) | 400 [300 — опция] |
Скорость подачи (м/мин) | 10-60 |
Мощность привода подачи (КВт) | 5,5 |
Частота вращения шпинделей (об/мин) | 6000-8000 |
Мощность вертикальных шпинделей | 6х6,5КВт |
Мощность финишных шпинделей «Click» | 4х6,5КВт |
Мощность двигателя регулировки ширины (КВт) | 1,5 |
Диаметр шпинделей (мм) | 40 |
Диаметр инструмента на шпинделях (мм) | 220-250 |
Диаметр аспирационных патрубков (мм) | 120 |
Суммарная мощность (КВт) | 92,6 |
4. Станок для упаковки ламината TS-200
Предназначен для полуавтоматической упаковки в термоусадочную ПЭ пленку готового ламината.
Технические характеристики | |
Максимальные размеры упаковки (мм) | 250х250х4000 |
Температура нагрева воздуха в камере (град) | 150-170 |
Используемая пленка | ПЭ термоусад. от 60 до 120 мкм |
Суммарная мощность (КВт) | 12 |
Габаритные размеры (мм) | 5000х1800х1000 |
Масса станка (кг) | 250 |
Производство ламината: технология и этапы
Какие этапы включает в себя производство ламинированного покрытия?
Технология производства ламината
Первое производство ламинированного покрытия датируется 1970-ми годами. В то время инноватором выступил шведский производитель, который создал двуслойное покрытие, склеенное с помощью специального состава и дополнительно прессованием под воздействием высоких температур. Поверхность покрывали специальными смолами для создания декоративного слоя, а нижний слой обрабатывали фенольными смолами.
Ламинат в привычном его представлении появился только десять спустя. Немецкая компания «Хорнитекс» применила новый подход к производству ламинированных панелей, используя теперь не два слоя, как было раньше, а четыре, создав таким образом напольное покрытие с совершенно иными уникальными техническими свойствами. В состав такого ламината входила фольга и такие виды смол как феноловая и меламиновая.
Технически, ламинатом принято считать только верхний слой покрытия общей ламинированной панели, но для удобства мы будем применять данное определение к напольному покрытию в целом. Производство ламината – достаточно сложный и многоэтапный процесс, так как каждый отдельный слой производится из разных материалов и выполняет определенный вид функции. Четыре слоя делают покрытие износостойким и прочным, предотвращая его преждевременную порчу от механической нагрузки. Тем не менее, каждый производитель сам решает, из скольких слоев будет выпускать ламинированный пол.
Этапы производства ламината:
- Облицовка плиты. Для получения ламели используют специальные технологии: обволакивают панель бумажно-смоляной пленкой и оверлеем, а также применяют различные методы и способы создания непосредственно самих панелей будущего ламината.
- Распил и фрезеровка плит. Последним и самым важным этапом является создание панелей ламината одинакового размера для будущей успешной их укладки в помещении. Для этого листы плиты помещают на специальный конвейер, который распиливает пластины, одновременно вырезая на каждой панели специальные выемки для будущей клик-системы.
- Упаковка готового ламината. После нарезки готовых ламелей, партия тщательно очищается от любой пыли и грязи, оставшейся после процесса производства и аккуратно упаковывается в фирменные коробки.
В настоящее время производство ламината постоянно совершенствуется за счет внедрения инновационных технологий в нескольких направлениях: оптимизация производственного процесса, улучшение замковой системы панелей, расширение разнообразия декоров и оттенков. Благодаря этому ламинированный пол обладает высокими стандартами качества, постоянно улучшает технические параметры и лучше выдерживает любые нагрузки на поверхность!
Компания Kastamonu запустила новую линию по производству ламината
(Казань, 22 марта, «Татар-информ»). Ведущий производитель деревообрабатывающей отрасли в России — компания Kastamonu — запустила третью линию производства. Старт состоялся в марте 2021 года. Благодаря открытию третьей линии совокупный объем выпускаемого предприятием ламината составит 45 млн кв. метров в год.
На новой линии завода Kastamonu будет выпускаться ламинат самых востребованных классов износоустойчивости — 31-го, 32-го, 33-го и высшего — 34-го, который ранее не входил в продуктовый портфель компании. Таким образом, производство удовлетворит самые широкие запросы рынка как в сфере коммерческой, так и жилой недвижимости, предоставляя материалы для разных типов помещений в соответствии с самыми высокими требованиями к качеству и техническим характеристикам продукции.
«Несмотря на охватившую мир пандемию и сложную экономическую ситуацию, мы решили инвестировать в расширение производства. В рекордно короткие сроки — за четыре месяца — мы смогли закупить необходимое оборудование, доставить его на завод и запустили производство конечного продукта. Старт третьей производственной линии состоялся в марте 2021 года. Благодаря открытию новой линии совокупный объем выпускаемого предприятием ламината составит 45 млн кв. метров в год. Мы сможем существенно расширить географию поставок по России, кроме того, есть планы по включению новых стран в экспортные поставки», — заявил генеральный директор Kastamonu Россия Али Кылыч.
Эксперты компании ожидают, что доля Kastamonu в сегменте ламинированных напольных покрытий на российском рынке превысит 30%. Увеличение объема продукции позволит удовлетворить рыночный спрос и запросы дистрибьюторов компании и предоставит конечным потребителям больше возможностей для приобретения качественной продукции. Такое расширение повлияет и на глобальные экономические процессы в отрасли и стране: на рынке деревообработки РФ ощутимо увеличится объем продукции с добавленной стоимостью, а также значительно вырастет доля импортозамещения.
Третья производственная линия завода оснащена новейшим оборудованием, включая высокотехнологичные станки немецкой компании HOMAG — мирового лидера комплексных производственных решений для мебельной и деревообрабатывающей промышленности. Благодаря современному оборудованию и многолетним наработкам Kastamonu в области управления и контроля за качеством на новой линии будет производиться ламинат, соответствующий всем последним требованиям рынка и запросам конечных потребителей, а также международным и российским техническим и экологическим нормам.
Расширение объемов производства значительно усилит позиции и повысит конкурентоспособность компании на рынке деревообрабатывающей отрасли России. Сейчас предприятие успешно сотрудничает с крупнейшими застройщиками, федеральными и региональными торговыми сетями и дистрибьюторами, а также участвует в реализации различных строительных проектов, в том числе программы реновации в Москве.
Партнерский материал
Производство ламината и панелей ОСБ
Вы страстно увлекаетесь техникой и привыкли уделять внимание каждой детали (в обоих смыслах этого слова)?
Это прекрасно! Наше оборудование работает круглосуточно семь дней в неделю. Постоянно нужно что-то отрегулировать, привести в порядок или отремонтировать. Наше производство — это изготовление МДФ/ХДФ панелей, панелей ОСБ, напольных покрытий (Fubo), короткотактный проходной пресс (KT) и прямое нанесение облицовочного материала.
Так как мы регулярно инвестируем в новое оборудование, перед нашими техническими специалистами, даже перед самыми искушенными из них, всегда стоят новые задачи.
Работа в отделах (муж./жен.

• Машинные и системные операторы
• Операторы котельной
• Механики
• Техники по электронному оборудованию
• Инженеры и техники по механическим или электрическим системам
Производство ОСБ
• Машинные и системные операторы
• Операторы котельной
• Механики
• Техники по электронному оборудованию
• Инженеры и техники по механическим или электрическим системам
Короткотактный проходной пресс (KT)
• Машинные и системные операторы
• Машинисты вилочного погрузчика
• Механики
• Техники по электронному оборудованию
• Инженеры и техники по механическим или электрическим системам
Производство напольных покрытий (Fubo)
• Машинные и системные операторы
• Механики
• Техники по электронному оборудованию
• Инженеры и техники по механическим или электрическим системам
Прямое нанесение облицовочного материала
• Машинный и системный оператор
• Красильщик
• Лакировщикr
• Печатник
• Дизайнер цифровых медиа
С нашими текущими вакансиями можно ознакомиться здесь.
назад
Как производят ламинат Kaindl — этапы производства от А до Я
Ламинированные паркет Kaindl производится в г. Зальцбург (Австрия) на оборудовании, которое по праву может считаться одним из самых инновационных и передовых в напольной промышленности. Площадь завода охватывает свыше 12 000 м2 и делится на специализированные зоны складирования, распиловки, сушки, прессования и ламинирования, завод оснащен большой лабораторий по проверке качества выпускаемой продукции. Сегодня австрийский ламинат Kaindl признан лидером на европейском и мировом рынке по объему реализуемой продукции с охватом географии продаж в более чем 40 странах мира.
Производство плиты-основы (HDF) Kaindl
Производство ламината или ламинированных полов начинается с производства плиты-основы High Density Fiberboard (в переводе с англ. – древесно-стружечная плита высокой плотности).
Для производства древесина подвергается окорке (отчистке бревен от коры). Затем она поступает в рубительную машину, в которой уже получают щепу. Щепа, в свою очередь, проходит через систему сит (sit) (механическая сортировка, которая делит на крупную и мелкую фракции). Крупные частицы уходят на производство ДСП, а мелкие — на производство HDF.
Полученная щепа отправляется на щепомойку (бочкообразную емкость объемом около 9000 куб.м). Все мелкие посторонние включения, которые могут оказаться в щепе (грязь, песок, мелкие камешки, стекло и т.п.) вымываются горячей водой и оседают на дне емкости.
Потом в другой емкости она (щепа) нагревается паром до 95-100 градусов Цельсия, для того чтобы обеспечить одинаковую температуру и влажность материала на входе в пресс. Затем масса попадает на несколько минут еще в одну емкость, где под высоким давлением горячего пара нагревается до 165-175 градусов. Прогретая щепа становится очень пластичной. Это необходимо для качественного измельчения.
На рафинере происходит размельчение. На выходе к древесной массе добавляются связующие компоненты, включая смолы, парафиновую эмульсию и, при необходимости, отвердители. Парафин снижает влагопоглощение плиты, карбомид обеспечивает прочностные свойства, отвердитель служит для стабилизации химических процессов, сопутствующих отвердеванию смолы.
Важно отметить тот факт, что все используемые при производстве ламината Kaindl – экологически чистые и безопасные, что позволяет использовать покрытия Kaindl практически во всех типах помещений, включая детские сады и больницы. Предлагаем ознакомиться с коллекциями Kaindl на нашем официальном русскоязычном сайте.
Следующий этап –сушка (длинная вращающаяся труба, диаметром около четырех метров, длина 120 м). Задача сушильного оборудования не только сушить, но и выравнивать влажность материала по объему древесной массы. После сушки древесная масса проходит через воздушный сепаратор, где отбирается крупная фракция волокна (дополнительный контроль качества).
Участок формирования ковра состоит из двух частей — накопительного бункера, где хранится запас древесной массы для работы в течение 6-8 минут, и непосредственно формирующей машины (ряд роликовых направляющих, которые подают и выравнивают волокно на ленте транспортера). Готовый ковер поступает на предварительное прессование, где проходят процессы выдавливания воздуха из объема плиты — на специальном участке с перфорированной лентой, где становится похожим на толстую рыхлую плиту заданной ширины (равной ширине ленты конвейера) и затем подается на главный пресс.
Этап прессования
Итак, главный этап — прессование. Пресс можно условно разделить на три части. На первом этапе — самая высокая температура (200-230 градусов) и самое высокое давление (до 350 МПа). Основная задача этого этапа — формирование поверхности будущей плиты. Основная задача второго этапа — прогревание центральной части ковра (температура — 190-210 градусов, давление — 40-120 МПа). Заключительный этап — калибровка (выравнивание до нужной толщины). Давление на заключительном этапе — 60-150 Мпа, в зависимости от толщины плиты.
На выходе из пресса установлен стенограф, который фиксирует плотность получаемой плиты и равномерность распределения плотности по толщине. Таким образом, контроль качества ведется непрерывно и автоматически.
Затем «бесконечная» лента HDF режется делительной пилой, «на ходу» получаются прямоугольные плиты формата 2800х4140 мм. Эти плиты попадают в веерный охладитель на 20-25 минут. После охлаждения плиты вылеживаются на складе в течение 1-3 суток) — это время необходимо для завершения физико-химических превращений в объеме плиты.
Для дальнейшего ламинирования или фрезерования шлифованные плиты оказываются предпочтительнее. После шлифования плиты попадают на форматизер (позволяет получить любой формат, меньший 2800х4140 мм).Так как для следующего этапа – этапа ламинирования хорошо подходит общепринятый европейский стандарт древесных плит — 2800х2070 мм.
Получение финишного рабочего покрытия — технологии HPL, DPL и Direct Printing
Большинство ламинированных полов сегодня производятся по технологии DPL (Direct Pressure Laminate — ламинат прямого прессования). Технология HPL (про которую было расcказано в первой части статьи) используется только для дорогих коллекций и довольно редко — эта технология довольно дорогая. Третьим вариантом ламинирования является технология прямой печати (DP), используемая только для самых массовых декоров и пока сравнительно небольшим числом производителей. Суть технологии заключается в том, что рисунок печатается непосредственно на плиту HDF, давая некоторый выигрыш в себестоимости.
Для самой распространенной технологии — DPL — в производстве ламинированных полов используются четыре слоя, прессуемые одновременно:
- Верхний слой – прозрачная бумага, пропитанная меламином с добавлением корунда – для обеспечения износостойкости. Этот слой обычно называют «overlay». В зависимости от количества корунда в нем готовое покрытие будет соответствовать более высокому или более низкому классу износостойкости (см. классы ламината).
- Второй слой – декоративная бумага. Это обычная бумага с рисунком. Для получения единого покрытия бумага также пропитывается небольшим количеством связующего клея.
- Третий слой – плита-основа. Сегодня практически все ламинированные полы выпускаются на основе HDF.
Наиболее распространенная толщина — 8 мм. В Западной Европе популярны также толщины 6 и 7 мм, а также — для более дорогих коллекций — от 10 до 14 мм.
- Четвертый слой – компенсирующий – крафт-бумага, пропитанная фенольными смолами. Этот слой нужен для компенсации остаточных напряжений при остывании плиты после ламинирования. Без компенсирующего слоя плита выгнулась бы дугой в сторону декоративного слоя. Дополнительным преимуществом использования компенсирующего слоя является повышение влагостойкости ламинированного пола к влаге, проникающей снизу покрытия — от чернового пола.
Получение панелей и замковых соединений
Последний этап — раскрой ламинированной плиты на панели и фрезеровка (это процесс механической обработки, при котором режущий инструмент (фреза) совершает вращательное движение с одной скоростью, а обрабатываемая заготовка — поступательное движение с другой скоростью) краев панелей. Обычно сначала фрезеруются края по коротким сторонам плиты, а затем — по длинным. Сложное сечение замковых соединений получается несколькими десятками фрез, расположенных последовательно вдоль конвейера, по которому проходит заготовка напольной панели. От точности настройки фрез зависит качество будущего соединения — а значит и качество покрытия в целом: его прочность, визуальная привлекательность (отсутствия ступенек, белых полос и зазоров в стыке панелей), и — в числе прочих факторов — влагостойкость.
Дальше, всем знакомый этап упаковки: готовые панели упаковываются в пачки, пачки запечатываются в полиэтиленовую пленку (обычно под пленку вкладывается инструкция монтажа и описание производителя и коллекции). Пачки укладываются на паллеты и, для защиты от повреждений при транспортировке, закрываются специальными уголками и полиэтиленовой пленкой.
Ламинированные напольные покрытия довольно быстро развиваются. Клеевые соединения изжили себя в истории развития этих покрытий. При таком соединении сами панели стоили немного дешевле бесклеевых, но это не приносило выгоды — для укладки клеевого ламината требовались квалифицированные специалисты, дополнительные материалы и инструменты. Кроме того, такой пол не допускал перенастила и замены поврежденной доски в уже готовом покрытии поверхности.
Сегодня безусловно на рынке доминируют бесклеевые коллекции. Они просты в монтаже, допускают несколько перенастилов и при этом не проигрывают клеевым коллекциям во влагостойкости и прочности. При использовании соединения типа «вкладыш» (click) количество перенастилов практически не влияет на состояние замка и поэтому никак не сказывается на долговечности. Такие замки удобнее и при монтаже — одна панель вкладывается под углом около 40 градусов в отверстие замка соседней панели, после чего без усилия опускается до горизонтального положения. В таком положении панели надежно и плотно фиксируются друг относительно друга, не образуя внутренней полости. Читайте подробнее о том, как укладывать ламинат Kaindl ЗДЕСЬ.
Соединения типа «защелка» (lock) более требовательны при монтаже, а также менее долговечны. При монтаже одна панель вбивается в другую, происходит небольшая деформация при защелкивании замка, следовательно, его состояние немного нарушается. После нескольких перенастилов может появиться видимая щель между панелями. Кроме того, замок-защелка менее стабилен в производстве; уровень брака достаточно высокий.
Наиболее распространенной схемой — удобной для монтажа ламинированных полов даже обычным покупателем — считается схема с замком-вкладышем по длинной стороне панелей и с замком-защелкой по короткой стороне.
Итак, вы полностью ознакомлены с процессом создания ламинированных полов, что обязательно поможет вам при покупке, так как вы сможете выбрать лучшую ламинированную доску по нужным вам критериям.
Технология производства ламината, ламинированных панелей, покрытия: производители, оборудование фото, видео
На рынке отделочных материалов ламинат пользуется большой популярностью и особым спросом, составляя достойную конкуренцию разнообразным видам напольного покрытия, включая паркет и массивную половую доску. Он широко используется в жилых, офисных помещениях и отличается простотой укладки, эксплуатации и ухода, роскошным внешним видом, устойчивостью к механическим нагрузкам и деформации, идеальным дополнением любого интерьерного стиля, разнообразием цветовых решений.
Производство ламината началось в конце 70-х годов прошлого века в Швеции. Современная география его изготовления охватывает многие страны мира, включая Китай, Россию, Украину.
Современные производители предлагают отделочный материал с разнообразными текстурами, рисунками, фотопечатью с оригинальными изображениями. Фактура ламината отличается идеальной картиной достоверности, имитирующей поверхности натуральных материалов.
Разнообразие цветовых решений напольного покрытияНо пальма первенства до сих пор принадлежит европейским компаниям, которые отличаются разработкой новинок, усовершенствованием оборудования для производства ламината и разработкой инновационных технологий. Качество напольного покрытия контролируется Ассоциацией европейских производителей ламинированных полов.
Состав ламинированного покрытия
Структура материалаПервые производители ламинированного покрытия предлагали доску из двух слоев.
На сегодняшний день она состоит из четырех слоев:
- Первый слой прозрачной прочной пленки из смолы выполняет надежную защиту от загрязнений, солнечного воздействия, мелких царапин, химических веществ. Дополнительно на поверхность может наноситься слой лака для придания блеска. Класс ламината определяется качеством исполнения первого слоя.
- Второй слой выполняет декоративную функцию и представляет собой бумагу, пропитанную смолами. Идеальная имитация фактуры древесины, камня, кожи, гранита, мрамора усложняет определение отличий между ламинатом и поверхностью натуральных материалов.
- Третий слой является основным и для его создания используется древесноволокнистая плита, плотность и качество которой определяет свойства, характеристики напольного покрытия. В основе ее изготовления лежит метод прессования древесного материала с клеем. Этот слой при производстве ламината является несущей частью покрытия.
- Четвертый слой предназначен для защиты напольного отделочного материала от деформации, воздействия влаги, паров, плесени, грибка и обеспечения повышенной жесткости, устойчивости.
Он представляет собой картон, пропитанный смолами, парафином или меламиновую пленку большой плотности.
Основные этапы производства напольного покрытия
Производство ламинированного покрытия предусматривает выполнение нескольких этапов.
Современное оборудование и производственное помещение для изготовления ламинатаК основным из них относятся:
- изготовление древесноволокнистых плит с высокой плотностью;
- обработка листов напольного покрытия специальными составами;
- облицовка, каширование ламината;
- распиловка, фрезеровка и упаковка готовой продукции.
Изготовление древесноволокнистых плит
Древесноволокнистые плиты выполняют функцию несущих частей напольного покрытия. Их производство основано на проведении многих операций.
К ним относится:
- измельчение древесины без коры до получения мелкой щепы, служащей сырьем для производства ламината;
- промывка щепы для удаления загрязнений, песка, примесей;
- двухэтапное распаривание щепы паром при температуре 100°С и 175°С для получения материала одинаковой влажности и пластичности;
- измельчение в рафинере до нужной фракции сырья;
- добавление смол, парафина, вяжущих веществ, повышающих плотность плиты и снижающих влагопоглощение;
- сушка щепы в соответствии с технологией производства ламината;
- первичное прессование щепы для формирования поверхности плиты под давлением 300 МПа и температуре 300°С;
- прогревающее прессование материала при температуре 190°С под давлением от 40 МПа до 120 Мпа;
- выравнивание плиты до получения идеально ровной поверхности.
Изготовление древесноволокнистых плит является важнейшим этапом технологического процесса при производстве ламината.
Импрегнация или пропитка плит специальными составами
Подготовленные для дальнейшей обработки плиты, в соответствии с технологией производства ламината, проходят импрегнацию, основанную на пропитывании материала специальными составами.
Для верхнего слоя используются смолы с добавками, позволяющие обеспечить прочный слой после застывания и определяющие степень износоустойчивости, а также срок эксплуатации напольного покрытия. Иногда в состав добавляют частицы корунда, предназначенных для улучшения качественных характеристик отделочного материала.
Облицовочный этап
Облицовка, предусмотренная технологией производства ламинированных панелей, осуществляется двумя способами. Первый из них называют кашированием. Он основан на нанесении клея с отвердителем на верхние слои ламината и последующее их спрессовывание Процесс осуществляется при высоких значениях температуры и в нем могут участвовать поверхности покрытия, прошедшие и не прошедшие этап импрегнации.
Второй способ облицовки предусматривает спрессовывание всех ламинатных слоев без использования клея. Он предназначен для плит, пропитанных специальными составами.
Заключительный этап
На заключительном этапе производства ламината выполняется распиловка, фрезеровка напольного покрытия и вырезание элементов крепления на кромочной стороне доски. Иногда технологией производства ламинированного напольного покрытия предусматривается нанесение воска или парафина на кромочные стороны доски.
Упаковка напольного покрытия механизированным способомПосле прохождения всех этапов производства, материал упаковывается в полиэтиленовую пленку ручным или механизированным способом.
Рекомендуем почитать:
Как ложится ламинат, технология укладки
Ламинат 33 класса лучшее напольное покрытие за разумную цену
Как постелить ламинат своими руками. От первых шагов до результата
Новости: Компания Kastamonu запустила новую линию по производству ламината в Татарстане — Эксперт
Старт состоялся в марте 2021 года. Благодаря открытию третьей линии совокупный объем выпускаемого предприятием ламината составит 45 млн кв. метров в год. Об этом сообщила пресс-служба компании.
«Несмотря на охватившую мир пандемию и сложную экономическую ситуацию, мы решили инвестировать в расширение производства. В рекордно короткие сроки за 4 месяца мы смогли закупить необходимое оборудование, доставить его на завод и запустили производство конечного продукта. Старт третьей производственной линии состоялся в марте 2021 года. Благодаря открытию новой линии совокупный объем выпускаемого предприятием ламината составит 45 млн кв. метров в год. Мы сможем существенно расширить географию поставок по России, кроме того, есть планы по включению новых стран в экспортные поставки», – заявил генеральный директор Kastamonu Россия Али Кылыч.
Завод Kastamonu в Елабуге (Татарстан) Источник: предоставлено пресс-службой компании
Эксперты компании ожидают, что доля Kastamonu в сегменте ламинированных напольных покрытий на российском рынке превысит 30%. Увеличение объема продукции позволит удовлетворить рыночный спрос и запросы дистрибьюторов компании. Расширение производства также позволит в целом увеличить объем продукции на рынке деревообработки РФ и значительно повысит долю импортозамещения.
На новой линии завода Kastamonu будет выпускаться ламинат самых востребованных классов износоустойчивости – 31-го, 32-го, 33-го и высшего — 34-го, который ранее не входил в продуктовый портфель компании. Третья производственная линия завода оснащена оборудованием немецкой компании HOMAG — мирового лидера производственных решений для мебельной и деревообрабатывающей промышленности.
Транспортировка ламината на участок контроля качества Источник: предоставлено пресс-службой компании
Расширение объемов производства значительно усилит позиции и повысит конкурентоспособность компании на рынке деревообрабатывающей отрасли России. Сейчас предприятие сотрудничает с крупнейшими застройщиками, федеральными и региональными торговыми сетями и дистрибьюторами, а также участвует в реализации различных строительных проектов, в том числе программы реновации в Москве. На протяжении многих лет компания регулярно поддерживает экологические инициативы и участвует в природоохранных мероприятиях, сотрудничает с WWF России и Лесным попечительским советом (FSC).
Завод Kastamonu по выпуску плит из древесной стружки (МДФ и ХДФ) и ламинированных напольных покрытий открылся в Татарстане в 2014 году. За время работы предприятие, расположенное в Елабуге, инвестировало в регион более 771,8 млн. долларов, что делает его крупнейшим турецким инвестором республики и вторым среди резидентов ОЭЗ «Алабуга». Компания выпускает ламинат с 31-го по 33-й класс износоустойчивости и различные виды МДФ-плит, включая влагостойкие и огнестойкие. На сегодняшний день мощность производства Kastamonu составляет 1,05 млн куб. метров плит МДФ и 45 млн кв. метров ламината в год. Ламинированные напольные покрытия поставляются в 27 стран Европы, Азии и Латинской Америки.
Ламинат Как это сделано
Все, что вам нужно знать о строительстве из ламината.

Узнать, как производится ламинат, легко и просто. Мы обозначили в основы ниже и попросите вас прочитать их, чтобы лучше понять, как это уникальный продукт создан.
Знание того, как устроен ламинат, дает вам правильные знания о ламинате. с самого начала.Это важная информация, потому что это материалы ты будешь жить и ходить долгие годы, если выберешь это напольное покрытие.
Знание конструкции ламината также поможет вам лучше понять и оценить его аспекты производительности.
Так что читайте дальше, и мы постараемся помочь вам узнать, как производится ламинат, в различные этапы и причины выполнения определенных процессов.
В разделе «Введение в ламинат» мы говорили, что ламинат — это
произведенный продукт, полностью имитирующий паркетный пол, натуральный камень
и многие другие виды напольных покрытий.
Теперь вам может быть интересно, как ламинат может походить на эти другие? продукты так близко?
Ответ кроется в процессе изготовления ламината.
Это сочетание точности современного производства. техники и опыт мужчин и женщин, стоящих за материалами, машинами и методами которые создают ламинат.
Все это работает в гармонии, чтобы создать красивый, функциональный пол, который плотно прилегает к поверхности. имитирует другие красивые, функциональные полы.
Чтобы узнать о ламинате, подумайте о выпечке и четырехслойном торте.
Сегодняшние ламинатные полы доступны во множестве дизайнов, рисунков, и текстуры, но все они состоят из четырех основных компонентов, которые связаны все вместе.
Нижний слой, или основа, представляет собой слой меламинового пластика, который придает объемные размеры. устойчивость к доскам, а также помогает защитить от влаги с пола.
(Влага, попадающая в любой пол, — враг.)
Следующий слой — это основная плита, обычно сделанная из древесноволокнистой плиты высокой плотности или частица картон, который также может содержать меламиновые пластмассовые смолы, которые помогают улучшить влага сопротивление сердечника.
Затем поверх основной плиты наклеивается декоративный слой или пленка для печати. пол выглядит как древесина или плитка.
Этот декоративный слой представляет собой печатную фото-репродукцию дерева с высоким разрешением. зерно, натуральный камень или узор из керамической плитки.(Теперь вы знаете, как выглядит рожд.)
А глазурь? Поверх нашего «торта» — прочный износостойкий слой,
обеспечивает защиту и устойчивость к пятнам.
Теперь многие слои износа также содержат оксид алюминия, а также меламиновую смолу и что обеспечивает исключительную долговечность. Вид, который выдержит большинство активный домашнее хозяйство — даже твое.
Затем все четыре слоя нашего «пирога» объединяются в аппарате высокого давления. процесс.
Теперь мы проведем вас через один шаг процесса производства ламината. вовремя.
Шаг 1: штабелирование с электронной точностью.
Процесс начинается со сборки 4 слоев сырья в большой листы.
Обычно это происходит на производственной линии, где современные технологии позволяют каждый слой накладывается на другой с невероятной точностью и точность.
Насколько точно вы спросите? Большинство производителей используют сложную электронику. калибровка
оборудование и системы цифровых камер для идеального выравнивания листов.
Нижний слой располагается первым на линии, а основная плата размещается непосредственно на вершина того, что.
Затем напечатанный декоративный слой укладывается поверх основной плиты.Финал накладываемый слой — это износостойкий слой.
Шаг 2: теперь давление нарастает.
После того, как 4 слоя уложены, они готовы к прессованию.
Прессы, используемые для создания ламинатных полов, оснащены гидроцилиндрами, которые огромный давление на стеки.
Пакеты слоев прессуются при высоких температурах, достигающих 400 градусов. Фаренгейт,
с давлением до 600 фунтов на квадратный дюйм в течение 20–30 секунд.
Производители тщательно следят за временем и температурой при прессовании слоев. для успешного отверждения и скрепления стопок в один лист готовой декоративный ламинат.
Если производимый ламинат имеет текстурированную поверхность, у пресса есть специальные пластины, которые отпечатывают фактурный узор на листы создание более естественного вида досок или плитки.
Шаг 3: время, чтобы остыть.
После того, как листы прижаты, им дают остыть, чтобы они полностью застыли. и для предотвращения любых дефектов поверхности.
Затем листы складываются и хранятся некоторое время, чтобы они могли продолжать акклиматизироваться тем самым повышая устойчивость досок.
Шаг 4: доски, профилирование и точность.
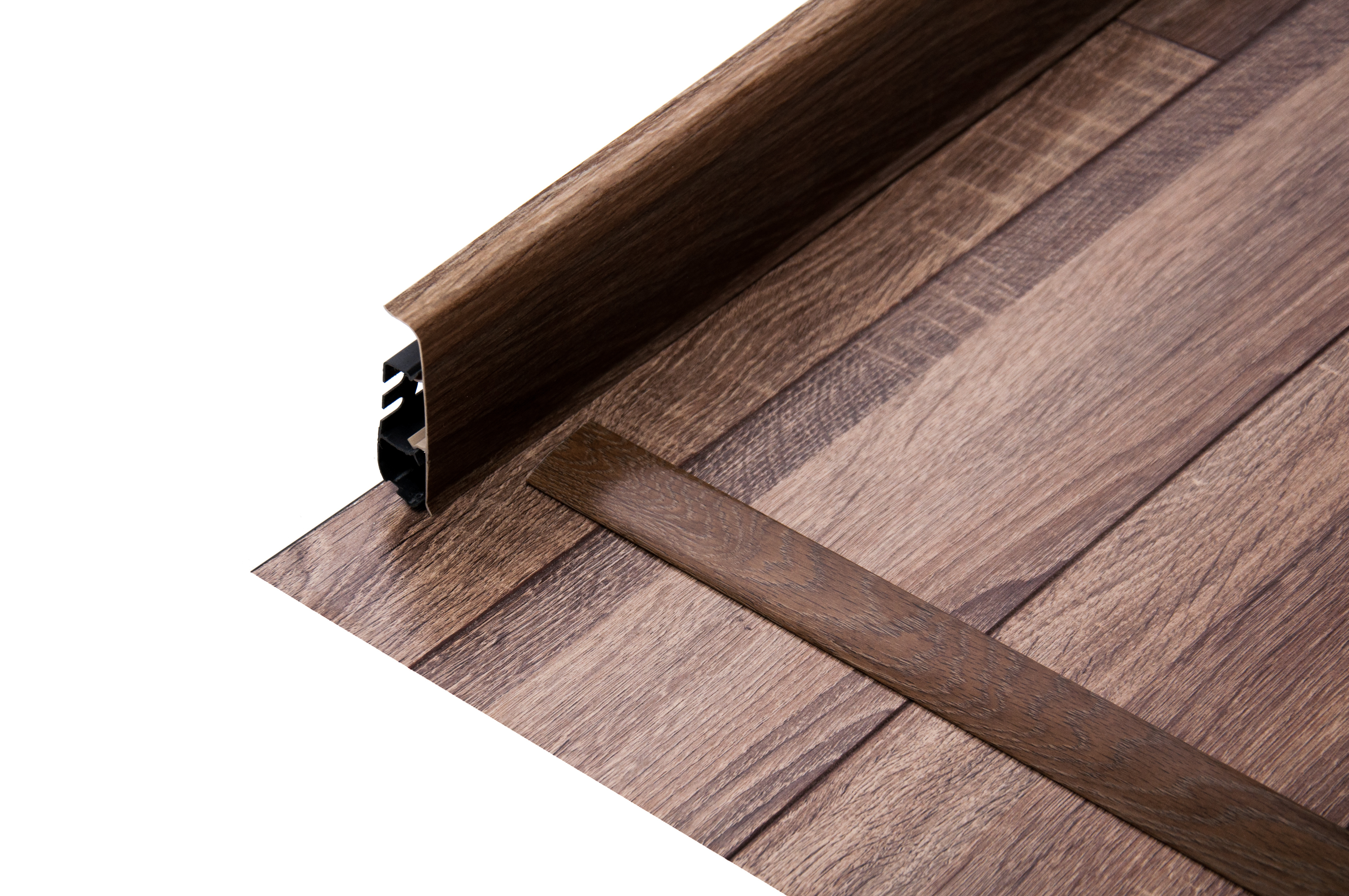
После того, как доски полностью акклиматизируются, их фрезеруют или разрезают на доски.
Свежесрезанные доски затем переходят к профилированию. Многопильные станки для профилирования Создайте края шпунтов и пазов по бокам планок, которые позволяют полу соединить вместе с легкостью.
В полотнах профильных пил используются электронные и лазерные системы, которые производят невероятно аккуратные края для идеальной посадки.Дополнительная гарантия точности вашего пол.
Готовые доски затем проходят проверку качества и проверяются на цвет, текстура, отделка, размер и возможности правильного сцепления.
После утверждения доски складываются, упаковываются и загружаются на грузовики для
распределение.
Теперь, когда вы знаете, как делают ламинат, вы можете понять, почему он красивый, прочный и экономичный вариант напольного покрытия для многих домов, а также домовладельцы, через графство.
Что такое ламинат и как его делают?
Ламинат стал более прочным, легче укладывается и выглядит более реалистично
«У ламината есть много преимуществ. Он прочный. Легко установить. У него конкурентоспособная цена, а визуальные эффекты — одни из самых реалистичных в отрасли ». Так говорит Джессика Шевалье, редактор журнала Floor Focus Magazine , в статье под названием «Ламинат 2013» в выпуске, посвященном индустрии ламината.Для своей статьи Шевалье провела обширные интервью с продавцами напольных покрытий по всей стране, расспрашивая их о ламинате. В статье конкретно адрес:
- Постоянная угроза товаризации категории,
- Конкуренция с розничными торговцами «Big Box»,
- Заблуждение, что все полы из ламината являются «дешевой» альтернативой, и
- Будущее категории ламината.
Вот основные моменты, которые мы нашли особенно интересными и заслуживающими вашего внимания:
Прочность — это прочность ламината
Как говорится в статье Floor Focus : «Среди розничных продавцов, с которыми мы говорили, долговечность ламината казалась наиболее важным аргументом в пользу продажи.Для активных домовладений по прочности он уступает только керамике. Он устойчив к царапинам, вмятинам и пятнам. Другими словами, он способен противостоять насилию со стороны как детей, так и домашних животных ».
Эксперты сходятся во мнении: реалистичный внешний вид ламината невозможно отличить от дерева твердых пород
Вы не сможете превзойти реалистичность высококачественного ламината! Другой отраслевой журнал отметил реализм как важную тенденцию. Floor Focus делится этой чудесной историей:
«Бут (региональный менеджер по продажам другой компании по производству ламината) делится историей с выставки Национальной ассоциации деревянных полов. Пол в одной кабине был сделан из древесины твердых пород и ламината. Некоторые эксперты по древесине лиственных пород на выставке выразили заинтересованность в покупке ламината, не понимая, что это не древесина лиственных пород. Так что на высоком уровне реализм ламината может быть очень убедительным даже для глаза эксперта ».
Печать декоративного слоя ламината становится все лучше и лучше
Основная причина потрясающего реализма изделий из ламината (особенно Swiss Krono) связана с постоянными технологическими улучшениями в печати.Или, как выразился один человек в статье,
«Болдуин (менеджер по продуктам розничной торговли) считает, что ламинат продолжит доминировать в категории DIY, и он прогнозирует, что визуальные эффекты категории будут продолжать улучшаться.« Каждый раз, когда мы думаем, что печать достигает своего пика », — говорит он. «становится еще лучше» »
Ламинированный пол можно укладывать поверх существующего пола
Один дилер, опрошенный для статьи Floor Focus , сделал интересное наблюдение относительно преимущества того, что ламинат может быть установлен поверх существующего пола:
«Он подчеркивает клиентам, что отсутствие необходимости укладывать черный пол означает, что они вкладывают свои деньги в продукт, а не в подготовку продукта, и что сэкономленные деньги можно направить на более качественное напольное покрытие. По словам Донохо, «многие покупатели винила перейдут на ламинат, когда обнаружат, что винилу может потребоваться черновой пол».
Примечание. Для получения дополнительной информации об этом преимуществе прочтите наш «Могу ли я установить ламинат поверх этого?» Справочник советов и советов о том, что можно и нельзя укладывать ламинат.
Ламинированный пол устойчив к появлению пятен
Среди многих характеристик долговечности ламината — устойчивость к пятнам.Вот пятно, которое мы не рассматривали, но оно особенно актуально для владельцев парикмахерских: «Даже краситель для волос не окрашивает (ламинатный пол)!»
Процесс производства декоративных ламинатов
Кинджал Мистри получил степень в области гражданского строительства в 2016 году в Университете Дхармсинх Десаи, Гуджарат. Она является менеджером (гражданский бакалавриат) в SDCPL — Gharpedia. У нее есть страсть к творческому письму. Как автор контента, она любит вести блоги по гражданскому строительству, строительным материалам и т. Д.Кроме того, будучи блоггером, она также занимается оценкой строительства и калькуляцией затрат в SDCPL. Она обладает отличными навыками критического мышления, чтобы выявлять и предлагать решения инженерных проблем. Любит спорт и читает романы. С ней легко связаться в LinkedIn, Twitter и Quora.
Процесс производства декоративных ламинатов включает в себя множество этапов, начиная с пропитки бумаги и кончая термореактивной отделкой.
Процесс производства декоративных ламинатов включает следующие этапы:
Также читайте: Преимущества и недостатки ламинатов
Процесс производства декоративных ламинатов Шаг 1 — Пропитка бумаги:01. Задняя часть ламинатного листа изготовлена из крафт-бумаги, которая может быть пропитанной влажной и рвущейся
- Театр пропитывает ее смолой, содержащей фенол (соединение, полученное из бензола)
- Смола не просто покрывает бумагу.
впитывается прямо через
02. Верх ламината называется декоративным слоем. Это лист бумаги с печатным рисунком или сплошного цвета.
Производственный процесс различается как для однотонной бумаги, так и для печатного дизайнерского слоя:
a) Сплошная цветная бумага:
- Они проходят процесс, который пропитывает их более прочной меламиновой смолой.
- Долговечность важна, потому что декоративный слой должен выдерживать износ.
- Два больших ролика удаляют излишки смолы. Обработка смолой делает бумагу жесткой и хрупкой.
б) Декоративный слой с печатным дизайном:
- Рабочие начинают с того, что разрезают их на листы той же длины, что и крафт-бумага.
- Эти листы бумаги не идут в театр для пропитывания смолами, вместо этого они укладываются, накладывая на каждую из них накладку.
- Накладка — это прозрачный лист бумаги, пропитанный меламиновой смолой.
Пропитанная бумага проходит через сушильный шкаф, где смола сушится горячим воздухом за считанные секунды. Когда смола затвердела, резак разрезает бумагу на листы.
Теперь пропитанная крафт-бумага помещается под каждый декоративный слой. Поверх каждого декоративного слоя укладывается фактурная плита, это предотвратит слипание готовых ламинатов. Однотонная бумага также складывается с этим листом, они не нуждаются в наложении.
Шаг 4 — Термореактивная обработка:Теперь все идет в пресс.
Сильный нагрев и давление сжимают слои.
Накладки связываются с печатной бумагой, а пропитанная крафт-бумага связывается с каждым декоративным слоем, образуя листы ламината. Текстурированные пластины между каждым набором тем временем отпечатывают свой отпечаток на размягченной при нагревании смоле, текстурируя поверхность ламината.
Также читайте: Различные типы ламинатов и их использование
Шаг 5 — Окончательная обработка: На машинах отделочной линии обрежьте лишнюю бумагу по краям и отшлифуйте обратную сторону листов. Это помогает ламинату лучше прилипать к ДСП или другому материалу.
Кинджал Мистри получил степень в области гражданского строительства в 2016 году в Университете Дхармсинх Десаи, Гуджарат. Она является менеджером (гражданский бакалавриат) в SDCPL — Gharpedia. У нее есть страсть к творческому письму. Как автор контента, она любит вести блоги по гражданскому строительству, строительным материалам и т. Д. Помимо того, что она ведет блог, она также занимается оценкой строительства и калькуляцией затрат в SDCPL. Она обладает отличными навыками критического мышления, чтобы выявлять и предлагать решения инженерных проблем.Любит спорт и читает романы. С ней легко связаться в LinkedIn, Twitter и Quora.
Продемонстрируйте свои лучшие разработки
Навигация по сообщениям
Еще из тем
Используйте фильтры ниже для поиска конкретных тем
Процесс производства ламинатных полов — как делают ламинатные полы
Ламинат является самым популярным напольным покрытием на рынке из-за его максимальной вместимости и самой низкой цены. Для его производства нет предела по сырью, он имеет очень ровный цвет и помол.Ламинированные полы просты в уходе, не требуют сложной ежедневной уборки, и их можно быстро заменить, если они повреждены или устарели. Полы из ламината прижимаются многослойным слоем, включая слой износа, балансирующий слой, основу и т. Д.
- Износостойкая бумага: Это оксид алюминия, устойчивый к царапинам, для защиты поверхности пола без больших и глубоких царапин и отсутствия воды. в пол. Бумага делится по весу — 25 г, 38 г (4000 рулонов), 45 г (6000 рулонов) и 58 г.
- Бумага для печати: На этой бумаге будет напечатан цвет напольного покрытия.
- Подложка: Это древесноволокнистая плита высокой плотности, спрессованная из древесного волокна с использованием экологически чистого и нетоксичного клея. База имеет белую сердцевину и зеленый цвет. Зеленая сердцевина водонепроницаема, в отличие от белой, сделана зеленая.
- Баланс: Это могло вызвать изгиб картона при нажатии на износостойкую бумагу и бумагу для печати.
Баланс необходим для баланса прочности 2-х слоев.Кроме того, баланс должен предотвратить подъем влаги из-под земли. Баланс составляет 33 г, 45 г, 90 г и 110 г в целом.
Канавки для ламината: квадратная кромка, V-образная канавка и фасонная канавка
- Квадратная кромка: После установки пол будет очень плоским, без зазоров. Легко чистится, пыль не застревает в щели.
- V-образные канавки: Это совершенно новые канавки в ламинатном полу, которые выглядят как пол из цельного дерева с рифлеными краями.Самая большая проблема с V-образной канавкой — это пыль, застрявшая внутри этого зазора. Его необходимо сразу после установки нанести воском на канавки.
Формованные кромки:
Это запатентованная технология. При нажатии кромки напольного покрытия будут вдавлены в U-образный паз, лучше, чем V-образный паз, V слишком глубокий, U — теневой. Итак, U легче чистить, чем V.
Процесс ламината:
- Печать
- Мы выбираем прядь с десятилетиями и сотнями лет и разрезаем ее на части, а затем сканируем самый четкий и красивый кусок как окончательный цвет напольного покрытия.
Отсканированное изображение с помощью лазерной машины лепим к печатному валику и печатаем на бумаге импортными чернилами.
- Печатная краска очень важна для качества бумаги. Благодаря сильному ультрафиолетовому излучению в течение 12 часов цвет не выцветает, что может гарантировать, что ламинат не выцветет в течение 7 лет на солнце.
- У нас есть 3 печатные линии, импортированные из Германии, производительностью 130 метров в секунду. Это действительно быстрые линии печати.
- Пропитывание клеем
- Отпечатанная бумага, износостойкая бумага и баланс необходимо пропитать клеем для прессования.Клей экологически чистый и не токсичен. Клей — стандарт E1, с низким содержанием летучих органических соединений. Необходимо строго контролировать намокание, иначе на полу могут появиться белые пятна, изгибы и трещины на износостойкой бумаге.
- У нас 10 линий замачивания. Пропитанная бумага также может быть использована для производства дверей, МДФ, компьютерных столов, офисной мебели.
- Прессование
- После замачивания бумага готова к прессованию, и нам нужно последовательно поместить ее между двумя прижимными досками.Прижимные доски изготовлены из нержавеющей стали. Температура прижима 170-210 градусов Цельсия, давление 18-23 МПа. Температура и давление регулируются в зависимости от плотности бумаги.
- В процессе прессования мы изготовим много типов ламината, например. На прижимных досках из нержавеющей стали имеется различный дизайн или зерно.
- Прижим на большинстве заводов составляет 1400 тонн, и у нас есть 8 прижимов на 1800 тонн и 2 прижима на 2400 тонн.
- Смена в дневное время может печатать 700 листов, а смена в ночное время может печатать 800 листов, так что за один день можно прессовать 1500 листов.
Резка доски: После прессования мы разрезаем доски на 2 или 3 части, а затем разрезаем на части полов.
Весы в помещении для кондиционирования: Плиты после резки должны соответствовать заводским температурам и влажности. Половые доски необходимо оставить в комнате кондиционирования в течение 1 недели летом и 3-5 дней зимой. Без баланса ламинатные доски для пола будут иметь проблемы сгибания, коробления и коробления.
- Язычок и паз:
- Мы производим бесклеевую защелкивающую систему Valinge для ламинатных полов на машинах Homag, которые импортируются в Германию.Homag может бегать со скоростью 130 метров в минуту, это самая высокая скорость в мире.
- Полы с квадратными и формованными краями — это конечный продукт после машины Homag. Для полов с U- или V-образными пазами края должны быть покрыты лаком.
Упаковка: Последний этап — упаковка. Полы из ламината будут упакованы в картонные коробки и поддоны.
Производство ламината высокого давления (HPL): производственный процесс, часть 1 — фанера
Фанера HPL (производство Китай, США, Израиль)
25 декабря 2018 г.
Некоторые детали были отредактированы мной в соответствии с производственным процессом China HPL и соответствующей технологией.
1. Ламинат высокого давления — производственный процесс
2. Сырье
3. Производство смолы
4. Пропитка (обработка) бумаги
5. Сборка и сборка
6. Процесс высокого давления
7. Обрезка, шлифование , Инспекция
Многие известные торговые марки, такие как Formica, Arborite, Micarta, Consoweld, Alpikord, Duropal, Weideda, Tianrun, zhenghang и yongwei. В Китае, в основном, из Юнцяо, города Чанчжоу и Хэнань Юнвэй, очень мало из района Линьи. .
HPL — это краткое название ламината высокого давления, производится из специально подобранной крафт-бумаги и декоративной бумаги с печатным рисунком, пропитанной термореактивными синтетическими смолами и сплавленных вместе под действием тепла и высокого давления в контролируемой среде с образованием отдельных листов ламината высокой плотности.
Узоры поверхностей (текстуры и отделка) и цвета ламината пропитаны смолами на основе меламина, чтобы обеспечить более высокую устойчивость к истиранию, ударам и ударам, нагреванию и обесцвечиванию.
Давайте начнем разговор с процесса производства ламината высокого давления, вы сможете лучше понять, что такое настоящий HPL.
Сырье , используемое для изготовления HPL: 1. крартовая бумага, 2. декоративная бумага, 3. верхняя бумага, 4. фенольный / меламиновый клей
- Оверлейная бумага, улучшающая сопротивление истиранию, царапинам и термостойкость
- Декоративная бумага, которая определяет дизайн и состоит из цветной или печатной бумаги
- Крафт-бумага, которая используется в качестве основного материала и контролирует толщину продукта.
Термическое ламинирование — это необратимый процесс , который дает начало HPL: пропитанные листы декоративной и крафт-бумаги подвергаются одновременному прессованию и нагреву процессу при высоких уровнях нагрева и давлении .
Пропитка. В производственном процессе HPL пропитка представляет собой операцию подготовки крафт-бумаги и декоративной бумаги. Их сначала пропитывают (пропитывают) термореактивными смолами, затем сушат.Подготовленная таким образом бумага даст начало листу HPL в процессе термо- ламинирования .
Ламинат высокого давления или HPL является прямым потомком оригинального пластикового ламината. Он считается одним из самых прочных материалов для декоративных поверхностей и обладает особыми характеристиками, включая химическую, огнестойкость и износостойкость. Особые сорта HPL могут быть постформированы вокруг изогнутых краев путем применения тепла и сдерживания.
HPL получают путем пропитывания нескольких слоев крафт-бумаги фенольной смолой.Перед прессованием поверх крафт-бумаги накладывается слой декоративной бумаги с принтом. Полученный бутерброд сплавляется под действием тепла и давления. Поскольку фенольные и меламиновые смолы являются термореактивными пластиками, в процессе отверждения смола преобразуется в пластик за счет процесса сшивания, который превращает бумажные листы в единый жесткий ламинированный лист. Термореактивное покрытие создает прочные необратимые связи, которые способствуют его долговечности.
Ламинат высокого давления приклеивается к композитной панели с использованием различных клеев.ДСП или МДФ являются предпочтительной основой, поскольку они обеспечивают стабильную, прочную, прочную и экономичную основу. Из-за своей прочности ламинат высокого давления часто используется для горизонтальных поверхностей, включая полы, столешницы и рабочие столы.
Производство
После того, как бумага пропитана смолой, три слоя бумаги / смолы помещают в пресс, который одновременно прикладывает тепло и давление. Операция прессования позволяет термореактивным смолам течь в бумагу, а затем отверждаться в консолидированный лист с высокой плотностью.Во время цикла прессования декоративная поверхность также может быть отверждена, находясь в контакте с текстурированной поверхностью, чтобы создать один из множества различных вариантов отделки поверхности.
HPL состоит из более чем 60-70% бумаги, а оставшиеся 30-40% представляют собой комбинацию фенолформальдегидной смолы для внутренних слоев и меламино-формальдегидной смолы для поверхностного слоя. Обе смолы принадлежат к классу термореактивных смол, которые сшиваются во время цикла прессования, образуя необратимые химические связи, в результате чего образуется нереакционноспособный, стабильный материал с характеристиками, отличными от характеристик компонентов.
HPL может производиться как с использованием непрерывных, так и периодических (периодических) производственных процессов. HPL поставляется в виде листов различных размеров, толщины и отделки поверхности.
Ламинат высокого давления — производственный процесс
Декоративный ламинат (ламинаты) высокого давления (HPL)
Лист (ы), состоящий из декоративного поверхностного слоя (ов) и внутренних слоев, соединенных между собой процессом высокого давления. Типичными значениями для процесса высокого давления являются температура ≥ 120 ° C и давление ≥ 5 МПа.
Поверхностный слой
верхний декоративный слой, состоящий из одного или нескольких листов волокнистого материала (обычно бумаги), пропитанных аминопластическими термореактивными смолами (обычно смолами на основе меламина) или другими отверждаемыми смолами или другими декоративными дизайнерскими поверхностями, такими как металлическая фольга, древесный шпон и текстиль и т. д., которые не обязательно обрабатываются термореактивной смолой. Поверхностные слои могут появляться на одной или обеих сторонах ламината (-ов). В случае односторонних ламинатов обратная сторона листа (листов) может быть сделана пригодной для приклеивания к подложке.
Сердцевинный слой
Сердцевинный слой, состоящий из волокнистых материалов (обычно бумаги), пропитанных термореактивными смолами (обычно смолами на фенольной основе) или другими отверждаемыми смолами, в конечном итоге армированный металлическим слоем (слоями) или металлической сеткой (ями) и другими, которые не являются обязательно обработать термореактивной смолой.
Сырье
Крафт-бумага
Пропитывающая крафт-бумага для HPL обладает впитывающей способностью, подходящей для смол. Крафт-бумага может быть изготовлена из первичных и / или переработанных волокон.
Бумага для декора
Бумага для декора — это отбеленная пигментированная бумага, обеспечивающая эстетичный вид. Декоративные слои могут быть пигментированы сплошными цветами или более уникальными узорами с использованием валков глубокой печати или технологий цифровой печати, таких как текстура древесины, каменные узоры и индивидуальные узоры.
Оверлейная бумага
Оверлей представляет собой беленую непигментированную прозрачную бумагу с очень высокой впитывающей способностью для смол. Он используется для повышения стойкости к истиранию.
Меламиновая смола
Меламиновая смола производится из раствора меламина и формальдегида.Меламиновые смолы — это прозрачные, светостойкие, устойчивые к царапинам твердые покрытия, которые лучше всего подходят для поверхностных слоев HPL.
Фенольная смола
Фенольная смола производится из раствора фенола и формальдегида. Фенольные смолы — это коричневатые, относительно эластичные соединения для внутренних слоев HPL.
Производство смол
Обе смолы производятся партиями. В чайниках химические компоненты взаимодействуют вместе в хорошо контролируемых условиях. Формальдегид соединяется с молекулами меламина или фенола и образует реактивные соединения для дальнейшей пропитки и прессования.
Пропитка (обработка) бумаги
Крафт-бумага и декоративная бумага поставляются в больших рулонах. В горизонтальных установках непрерывного действия (т.е. пропиточных машинах) бумагу разматывают, погружают в ванну со смолой, пропитывают смолой и затем сушат. Сухая бумага, заполненная все еще реактивной смолой, разрезается на листы желаемой длины или снова наматывается и хранится в кондиционируемых помещениях для последующего использования.
Сборка и сборка
Обработанные бумаги собираются со склада и собираются в чистых, непыльных помещениях для создания нужного порядка в желаемом цвете, размере, толщине и подложке:
Типичное наращивание HPL
Односторонние ламинаты всегда производятся «спина к спине» с использованием разделительной бумаги.Разделительная бумага (например, специальная бумага с покрытием) или фольга применяются во избежание слипания ламинатов в прессе. В случае прессов с несколькими открываниями (прессы с мультидневным освещением) сборку необходимо повторять много раз, чтобы заполнить пресс. Используются прессы до 45 отверстий. Каждое отверстие заполняется до 24 односторонних ламинатов (обычно толщиной 0,5 — 1,9 мм) или, по крайней мере, одним компактным ламинатом (обычно толщиной от 2 до 20 мм).
Процесс высокого давления
Многодневные прессы загружаются при комнатной температуре, закрываются, настраиваются под гидравлическое давление и нагреваются до температуры более 120 ° C.Тепло вызывает процесс разжижения меламиновых и фенольных смол. Под высоким давлением жидкие смолы вдавливаются между целлюлозными волокнами
и внутрь — плотность увеличивается с последующим завершением химической реакции (поликонденсации), называемой «отверждением». Это образует однородную жесткую, полностью сшитую сеть в виде листа. В результате получается непористый ламинат, который не плавится. Волокна целлюлозы усиливают ламинат. Они химически связаны и полностью интегрированы в новый состав. Структура поверхности (глянцевая, матовая, текстурированная и т. Д.) Формируется пластиной пресса (или шаблонами), прижимаемой к разжиженному, а затем отвержденному слою меламина. После завершения отверждения ламинат охлаждается под давлением, чтобы снять напряжение. Полный цикл прессования может занять до 100 мин. в зависимости от нагрузки пресса и макс. температура.
Обрезка, шлифовка, осмотр
Ламинат выгружается из пресса, и отслаивающийся материал удаляется. По длине и ширине ламинат нарезается на необходимый размер.Односторонние ламинаты шлифуются с обратной стороны для улучшения склеивания. После проверки поверхности и качества на предмет дефектов ламинаты маркируются, упаковываются и хранятся для дальнейшей утилизации.
Изготовление элементов HPL и компактных листов
Односторонние ламинаты обычно приклеиваются к подложкам (например, ДСП, МДФ и т. Д.) Для получения композитных элементов.
Можно нанести кромочные полосы или ламинат можно постформировать (например, для кухонных столешниц).
Компактные ламинаты разрезаются по размеру, и к ним прикрепляется фурнитура, чтобы они были готовы к установке в качестве шкафчиков, боксов, перегородок и т. Д.
Производственный процесс
Рулоны крафт-бумаги и декоративной бумаги сначала помещаются на огромные разматыватели, разматываются и обрабатываются (пропитка в ванне с жидкой смолой с последующей сушкой в печи и обрезкой до определенного размера).
Крафт-бумага, используемая для сердцевины панелей, пропитана фенольными термореактивными смолами, а декоративная бумага, используемая для поверхности, обработана термореактивными меламиновыми смолами. Эта декоративная бумага (которая в основном состоит из пигментов и / или красок и целлюлозной массы) специально разработана таким образом, чтобы поддерживать высокий уровень устойчивости к солнечному излучению (включая УФ-лучи, видимые лучи и ИК-излучение), обеспечивая тем самым хорошую стойкость цвета.
Листы крафт-бумаги укладываются в стопку и соединяются с декоративной бумагой, образуя панель заданной толщины. Приблизительно 50 листов крафт-бумаги и не менее двух листов декоративной бумаги необходимо для изготовления стандартной панели (двусторонней) номинальной толщиной 10 мм.
Пачку пропитанных листов помещают в многодневные прессы и подвергают одновременному воздействию тепла и давления. Происходит реакция поликонденсации, приводящая к образованию химической сшивающей структуры, в которой фенольная и меламиновая смолы прочно химически связаны друг с другом.
Изготовленные таким образом панели затем обрезаются и подвергаются окончательной проверке, чтобы впоследствии они были готовы к отправке.
Части профессиональных технических деталей получены из :
1. https://www.compositepanel.org
2. www.icdli.com
3. https://en.wikipedia.org
4. https://www.panel.com
5. www.decorativesurfaces.org
6. www.arpaindustriale.com
7.www.formica.com
8. https://www.wilsonart.com
Ti-Pure ™ Портфолио продуктов TiO для ламината
Обеспечение индивидуального цвета и дизайна для полов и мебели
Высококачественный диоксид титана (TiO₂) добавляет незаменимую ценность материалам, используемым в производстве ламинатных полов и мебели, особенно для клиентов, которые производят декоративную бумагу высокого и низкого давления, декоративную пленку и материалы для печати.
Производители декоративной бумаги, которые продают ламинат, требуют:
- Эффективность TiO₂ и постоянство качества для оптимальной производительности
- Устойчивость к ультрафиолетовому излучению и отличное формирование
- Бумага с низкой плотностью для максимальной прочности и ровности бумаги
- Хорошая удерживающая способность, обеспечивающая высокий уровень текучести бумаги и максимизирующая время производства и производительность
- Сине-белый оттенок для создания более широкого диапазона ярких цветов
Производители ламината нуждаются в бумаге, фольге и приложениях для печати, которые обеспечивают качество конечного продукта:
- Хорошая непрозрачность и укрывистость
- Светостойкость и сохранение цвета
- Возможности постформинга (придание ламинатным изделиям изогнутой кромки)
- Равномерность и однородность цвета
Ti-Pure ™ Высококачественный TiO₂ в производстве
Непоследовательный TiO₂ дает неравномерное удерживание, что приводит к неравномерности цвета и комковатым отложениям. Даже когда производители добавляют больше TiO2 для компенсации, прочность бумаги и эксплуатационные качества снижаются. Производители бумаги Décor знают, что Ti-Pure ™ TiO₂ производится в соответствии со всеми целями качества и стабильности, обеспечивая:
Стабильность цвета от катушки к катушке
Причина номер один, по которой бумажные фабрики теряют производственное время и рентабельность, — это недостаток однородности цвета от катушки к катушке. Использование правильного TiO₂ позволяет добиться такой однородности цвета, что сокращает время производства и увеличивает прибыль.
Внешний вид и светостойкость
Пигменты TiO₂ помогают принтерам достигать наилучших результатов, обеспечивая сине-белые оттенки, которые создают более широкий диапазон ярких цветов, сохраняя при этом изображение и узор нетронутыми.TiO₂ также позволяет изделиям из ламината сохранять свою яркость и противостоять обесцвечиванию, вызванному воздействием света.
Прочность бумаги
Пропиткам для бумаги или принтерам необходимо постоянное качество, чтобы избежать разрывов, замедляющих производство. Высококачественный TiO₂ позволяет принтеру использовать бумагу с более низкой базовой плотностью для получения большего количества квадратных метров на тонну, что приводит к более высокой рентабельности.
Применения в производстве ламината
Бумага для декора
Декоративная бумага низкого и высокого давления включает однотонную бумагу и бумагу-основу для печати.И то, и другое требует высокой производительности и постоянного качества, особенно потому, что в различных областях применения бумага-основа для печати используется позже в процессе производства ламината.
Другая категория — декоративные пленки — относятся к средней категории, используются для наклеивания и работают только при давлении 1-2 бар.
Максимальная эффективность TiO₂ с Ti-Pure ™ R-796 +
Этот ламинат TiO₂ улучшает непрозрачность и сохраняет цвет. Обработка поверхности также делает Ti-Pure ™ R-796 + совместимым с широким спектром химического состава воды.Учить больше.
Обзор методов производства | LaminateFinder.com
RENOLIT Ламинат можно использовать для плоского ламинирования и оклейки кромок деревянных поверхностей так же, как ламинат высокого давления. Кроме того, ламинаты RENOLIT Alkoren и Covaren 3D могут быть подвергнуты мембранному прессованию для бесшовной инкапсуляции практически любой трехмерной формы, проложенной в основах с деревянным сердечником, и обернуты в профиль для бесшовной поверхности линейных профилей и отделки, как деревянных, так и пластиковых профилей.
Эта универсальность в сочетании с цветами и узорами, которые соответствуют популярным ламинатам высокого давления и меламиновым плитам, позволяет вам смешивать и сочетать методы и материалы покрытия для нескольких компонентов одного и того же конечного продукта в зависимости от конструкции каждого компонента, предпочтительного метода производства и ожидаемый уровень злоупотреблений.
Смешайте наплавочные материалы и методы производства:
- Плоская центральная поверхность стола из меламинового картона в цвете ламината RENOLIT .
- Продолговатая часть с профилем, вырезанным из плиты МДФ, а затем термоформованной с использованием ламината RENOLIT 3D. Обратите внимание на сочетание закругленных и острых граней.
- Юбка стола, полученная путем плоского ламинирования плиты МДФ ламинатом высокого давления, соответствующего цвету Ламинат RENOLIT , затем выпиливанием нескольких вертикальных пропилов на тыльной стороне, позволяя юбке изгибаться.
Ножки, плоско-ламинированные с однотонным покрытием RENOLIT Alkorfol 2D-ламинат, стыкующийся с металлизированным покрытием RENOLIT Alkoren 3D-ламинат, с последующим фальцеванием под углом, с получением имитации металлических накладок для ног.Скошенные углы, полученные с помощью ЧПУ фрезерования угловых канавок под расходящимися углами перед фальцеванием.