Медицинское оборудование — Линия полного цикла для производства одноразовых шприцев и игл
Линия полного цикла для производства одноразовых шприцев и игл
1. Общие положения проекта
1.1. Предмет проекта. Максимальная производительность данной линии составляет 20 000 000 миллионов одноразовых шприцев и игл в год при графике работы 1-3 смены в день. Данные показатели производства могут быть легко увеличены после того, как рабочий персонал приобретет достаточный опыт и частично увеличит кол-во оборудования.
Фото конечного продукта (шприцы на 3 и 5 мл)
2. Краткое описание
2.1.1. Одноразовые шприцы. Шприцы, производимые данной линией, состоят из трех элементов: цилиндра, плунжера и уплотнительной манжеты. Цилиндр представляет собой трубку c двумя отверстиями – большим для плунжера и малым с подыгольным конусом для иглы. Плунжер представляет собой шток поршневого типа со слегка конусообразным наконечником, который обеспечивает надежное соединение с иглой. Объем раствора внутри шприца обозначается градуировкой на цилиндре. Эти линии могут быть в миллилитрах или долях миллилитра в зависимости от емкости шприца. Уплотнительная манжета изготавливается из эластомерных материалов, которые являются полностью безопасными и не содержат латекса. Линия по производству эластомерной манжеты может быть исключена или изменена, если заказчик предпочтет использовать другие материалы. Линия по производству шприцев включает в себя процессы литья под давлением (термопластавтоматы), сборку, упаковку и стерилизацию шприцев. Производственная линия соответствует Международным стандартам с использованием автоматического и полуавтоматического оборудования, а выпускаемая продукция соответствует корейским стандартам KSP3004-1986, KS P3001-1985 и I.S.O. 7886-1: 1993 (для одноразовых шприцев) и 7864-1: 1993 (для одноразовых игл).
2.1.2 Одноразовые иглы. Медицинская игла состоит их трех частей: головки иглы, трубки и защитного колпачка. Один конец иглы заострен, а другой прикреплен к головке для присоединения к шприцу. Трубка иглы представляет собой длинную тонкую металлическую трубку со скошенным и заостренным концом.
Размеры иглы определяется ее длиной и диаметром. Длина иглы измеряется в дюймах или миллиметрах, начиная от стыка головки иглы с трубкой до верхней точки среза. Диапазон длин игл составляет от 1/2 до 2 дюймов (25-50 мм). Некоторые иглы для специального назначения могут быть длиннее или короче. При производстве медицинских игл очень важен процесс заточки, так как качество иглы определяется ее остротой. Введение иглы в вену представляет собой процесс разрезания мягких тканей, эффективность которого определяется остротой и геометрией среза иглы. Существует множество разных видов заточек для игл. Наиболее популярным считается стандартная заточка, которая называется «Lancet Point». Обычно стандартный срез иглы имеет три грани: первая грань, которая сформировывается при заточке трубки под определенным углом и двух боковых граней, которые являются результатом последующей шлифовки с каждой стороны первой грани для получения острия иглы и режущей кромки. Длина среза иглы — это наибольшее расстояние среза, замеренное от верхнего кончика иглы до ближайшей области заточки. Длина бокового скоса иглы измеряется между стыком боковой грани, внешней поверхностью трубки и верхнего кончика иглы. Обычно угол среза составляет 12-15°, который обеспечивает создание острой и режущей кромки. Трубка иглы представляет собой полую тонкую трубку из нержавеющей стали, у которой один конец тупой, а второй заострен. Сборка игл производится путем присоединения трубки к головке иглы.
2.3.1 Описание. Требования к трехкомпонентным одноразовым шприцам: Шприцы и иглы предназначены для одноразового использования и поставляются в собранном виде – игла надета на шприц.
2.3.2 Общие положения:1. Составные элементы. Шприц с надетой иглой должен включать в себя цилиндр, плунжер, уплотнительную манжету и иглу. Игла состоит из трубки, изготовленной из нержавеющей стали, головки и защитного колпачка. Все элементы шприца должны быть выполнены из нетоксичных и не пирогенных материалов, а также не должны иметь каких-либо дефектов.
2. Стерильность. Все шприцы должны быть упакованы в индивидуальную герметичную упаковку.
3. Биологическая безопасность. Все материалы должны пройти биологические испытания.
2.3.3 Цилиндр. Цилиндр должен быть прозрачным, без заусенцев и дефектов на внутренней поверхности.
Маркировка и логотип печатаются на наружной поверхности цилиндра.
2.3.4 Плунжер. Плунжер изготавливается из полипропилена.
2.3.5 Уплотнительная манжета. При выполнении инъекции движение уплотнительной манжеты должно быть плавным и без рывков. Для этого в качестве смазки используется силиконовое масло. Также движение уплотнительной манжеты внутри цилиндра должно пройти испытание на герметичность.
2.3.6 Конусный наконечник шприца. Подыгольная конусность наконечника шприца должна составлять 6%. При испытании шприцев, на стыке наконечника и головки иглы не должно быть никакой протечки.
2.3.7 Трубка иглы. Срез трубки иглы должен быть достаточно острым. Не допускается наличие никаких признаков коррозии. Поверхность трубки должна быть покрыта силиконовой смазкой, чтобы уменьшить сопротивление и увеличить силу проникновения при выполнении инъекции.
2.3.8 Головка иглы. Головка иглы должна иметь конусность 6%.
2.3.9 Прочность соединения между трубкой и головкой иглы. Прочность соединения должна проверяться в соответствии со стандартом ISO 7864.
2.3.10 Защитный колпачок. Защитный колпачок должен быть полупрозрачным и легко сниматься.
2.3.11 Виды шприцев. Существует 2 типа шприцев. Один из них Luer Slip, который имеет стандартный тип наконечника, а другой — Luer Lock (тип винта). Заказчик может выбрать любой из них в соответствии с требованием рынка.
LuerSlip LuerLock
2.3.12 Цвет головки иглы. Головка иглы должна быть равномерно окрашена в соответствии со стандартом ISO или государственным стандартом страны заказчика.
2.3.13 Покрытие иглы силиконом. Трубка иглы должна быть покрыта силиконовым маслом для уменьшения сопротивления при выполнении инъекции.
2.3.14 Индивидуальная упаковка. Все шприцы должны иметь индивидуальную блистерную упаковку из медицинской бумаги и полимерной пленки. Инсулиновые шприцы не имеют индивидуальной упаковки, но каждый шприц для поддержания стерильности, запечатан при помощи двух защитных колпачков. Одна полиэтиленовая упаковка вмещает 10 инсулиновых шприцев.
2.3.15 Диаметр и длина игл. Соотношение длины и диаметра должно соответствовать рыночному спросу. Обычно используется следующее соотношение:
3.1 Конструкция изделия
3.2 Годовая производительность
1. Шприцы
2. Иглы
3. 3 Упаковка
*Упаковка продукции в соответствии с требованиями рынка
3.4 Режим работы
Кол-во смен в день: 1-3 смены
Кол-во рабочих часов в одну смену: 8 часов
Кол-во рабочих часов в день: 8 – 24 часа
Кол-во рабочих дней в месяц/год: 21 день в месяц/250 дней в год
Общее время простоя оборудования формируется из: 1. Предварительного прогрева станков. 2. Запуска производства. 3. Настройки и установки станков. 4. Смены прессформ или вспомогательного оборудования 5. Сбоя в электроснабжении. 6. Выхода станков из строя. 7. Очистки станков от излишков масла и прочих отходов производства
4. Описание технологического процесса и производительности оборудования. Одноразовые шприцы и иглы производятся в соответствии с корейским стандартом, а также стандартом ISO. Цилиндр, плунжер, головка иглы и колпачок изготавливаются из полипропилена. Уплотнительная манжета изготавливается из эластомера. Трубка иглы изготавливается из нержавеющей стали AISI 304 (SUS 304) в соответствии с корейским стандартом и стандартом ISO.
4.1 Производство одноразовых шприцев. Сырье, используемое для производства одноразовых шприцев хранится на складе в гранулированном виде. Гранулы из мешков засыпаются в контейнеры и далее транспортируются в машину для литья под давлением (термопластавтомат). В процессе засыпки сырья, контейнеры полностью защищены от попадания грязи и посторонних предметов.
4.1.1. Литье под давлением. Гранулы засыпаются в бункер термопласт автомата для дальнейшей пластификации. Пластифицированный материал поступает под давлением в закрытые прецизионные прессформы. Система водяного охлаждения, связанная с прессформой, охлаждает пластифицированный материал, который становиться соответствующим элементом шприца — плунжером, головкой иглы или защитным колпачком. По истечению положенного времени охлаждения, прессформа открывается гидравлически и готовые детали извлекаются. Отдельные элементы шприца хранятся в специальных контейнерах в течение 24 часов для последующего охлаждения и сужения до требуемых размеров.
4.1.2. Печать градуировки. После охлаждения цилиндры транспортируются к печатному станку для нанесения градуировочной шкалы, а плунжеры на сборочную линию. Цилиндры помещают на подающий транспортер, который доставляет их к барабану печатающего устройства и далее с помощью калиброванного железного валика шкала наносится на поверхность цилиндра.
4.1.3. Сборочная линия. Цилиндр с градуировочной шкалой, плунжер и уплотнительная манжета автоматически транспортируются и загружаются в сборочную линию. На данном этапе прокладка одевается на плунжер, который вставляется в цилиндр, а затем игла необходимого размера одевается на шприц.
4.1.4. Индивидуальная блистерная упаковка. После сборки готовые шприцы складываются в блистерную упаковку из полимерной пленки, пригодной для термоформования, а также в газопроницаемую бумагу, которая полностью защищена от проникновения бактерий. Полимерная пленка и бумага в виде рулонов устанавливаются на упаковочной машине.
Подготовка к упаковке начинается с размотки и подачи рулонной пленки в прессформу блистерной упаковочной машины, где происходит формовка ячеистых контейнеров с помощью вакуумной вытяжки.
В процессе упаковки шприцы автоматически помещаются в ячеистые контейнеры и накрываются вкладным листом, после чего запечатываются и стерилизуются. После термоформования и герметизации упаковки, печатающее устройство наносит на бумагу все необходимые данные (дату производства, размер шприца, дату истечения срока годности и т.д.). Затем готовая продукция вывозится из стерильного помещения так как она уже полностью герметична.
После этого шприцы помещаются в коробки с уже напечатанной на них информацией: датой изготовления, номером партии, сроком годности и т. д. Внутренние коробки помещаются в коробки для транспортировки, на которых также содержатся все необходимые данные и затем они транспортируются в зону стерилизации.
4.1.5. Стерилизация. Шприцы, упакованные в коробки для транспортировки, транспортируются в камеру стерилизации. Процесс стерилизации осуществляется путем наполнения камеры газом окиси этилена. После того, как камера стерилизации будет загружена шприцами, дверь камеры закрывается и герметизируется. Затем в течение часа пар поступает в камеру, в которой поддерживается необходимый уровень влажности 60-80% и температуры 40-50°С. По истечении этого времени, требуемая влажность и объем газа окиси этилена поступают в камеру стерилизации через испаритель. После заполнения камеры необходимым объемом газа, подводящие патрубки к камере перекрываются и начинается 6-часовой процесс выдержки. Остаток вакуума, в камере обеспечивает полную блокировку двери. В процессе выдержки давление вакуума незначительно увеличивается. По истечении этого времени, с помощью вакуумного насоса камера снова вакуумируется до 0,005 Мпа и удаляется основной объем окиси этилена. Свежий воздух поступает в камеру через фильтр. При достижении необходимого уровня давления остаточный газ удаляется из камеры. Данный процесс повторяется дважды. На третьем этапе в камеру подается свежий воздух до момента нормализации давления. По окончании цикла стерилизации шприцы вывозятся на склад готовой продукции.
4.2. Производство одноразовых игл:1. Связка трубок в обойму и усадка по диаметру. Определенное кол-во трубок из нержавеющей стали собирается в одну связку при помощи полимерной пленки или хомутов.
2. Резка трубок. При помощи автоматического отрезного станка данная связка разрезается на трубки требуемой длины.
3. Удаление заусенцев. Для удаления заусенцев после резки необходима обработка внутренней и внешней поверхностей трубок с использованием вращающейся щетки из нержавеющей стали, которая перемещается в любом направлении и оборудована таймером.
4. Промывка. Посторонние предметы от разрезанных трубок удаляются при помощи моечной машиной высокого давления, затем пленка или пластиковые хомуты удаляются.
5. Заточка трубок (очистка). Разрезанные трубки вместе с керамическими гранулами и чистящим средством помещаются в барабанную машину для очистки и полировки.
6. Разделение. После процесса заточки, при помощи сепаратора происходит разделение трубок и керамических гранул.
7. Подготовка заготовок игл к обмотке лентой. Заготовки игл равномерно раскладываются и подготавливаются для загрузки в машину для оклеивания лентой.
8. Процесс оклеивания заготовок игл липкой лентой. После сушки заготовки игл выравниваются параллельно друг друга и транспортируются в бункер машины для оклеивания лентой и дальнейшей заточки среза будущих игл. Использование мерных барабанов с пазами обеспечивает равномерный забор и дальнейшую выгрузку заготовок игл в блок оклеивания лентой. После этого, на поверхность заготовок игл наклеивается клейкая лента, которая будет удерживать их во время заточки. После чего лента с заготовками игл разрезается на отрезки длиной по 30 см.
9. Заточка заготовок игл. Полученные ленты с заготовками игл транспортируются в бункер загрузки автоматического заточного станка. Один конец заготовки затачивается и отрезается согласно стандартам страны заказчика. Заточка и выполнение среза иглы происходит автоматически. После завершения цикла, координатно-шлифовальный станок возвращается в исходное положение. Станок для автоматической заточки заготовок игл предназначен для трехгранной заточки, используемой для одноразовых игл, катетеров, наборов игл типа «бабочка» и т. д.
10. Шлифование. При использовании измельченных гранул происходит удаление грязи и посторонних примесей с поверхности заготовок игл.
11. Электролиз трубок игл. После завершения процесса шлифования заготовки игл становятся трубками игл. Полировка и промывка поверхности трубок игл осуществляется при помощи электролизной машины. Данная обработка повышает остроту среза, а также полностью устраняет остаточные заусенцы на поверхности трехгранной заточки.
12. Ультразвуковая чистка. Все трубки иглы проходят ультразвуковую чистку, очистку горячей водой, водой под высоким давлением и при необходимости некоторыми химическими жидкостями.
13. Контроль качества. Заточка среза иглы проходит контроль. Некачественные иглы отбраковываются.
14. Сборка игл. Головки игл, трубки и защитные колпачки собираются при помощи машины для автоматической сборки. На этом этапе также выполняется силиконизирование трубки иглы. Далее собранные иглы транспортируются на линию упаковки или сборочную линию шприцев.
4.3 Производительность. 4.3.1 Заточка среза иглы (производство трубки иглы). Игольчатая заточка используется для медицинских комплектующих из нержавеющей стали, в первую очередь игл для подкожных инъекций и режущих инструментов. В процессе заточки иглы ее срез затачивается за один проход. Согласно международным стандартам, медицинские инструменты из высоколегированной и нержавеющей стали должны быть остро заточены. Для выполнения качественной заточки важно не только высокоточное оборудование, но и квалифицированный персонал. После процесса заточки, трубка иглы транспортируется в секцию шлифовки для удаления заусенцев. Срок службы шлифовального диска и отсутствие заусенцев на готовом изделии являются важными критериями процесса заточки. После шлифовки, режущие кромки внутри и снаружи должны быть без заусенцев, в противном случае, это может вызывать болезненные ощущения у пациентов. Устройство для шлифовки закреплено на заточном станке.
Производительность линии заточки игл
Необходимое кол-во машин по заточке игл:
23G: 10 000 000 шт ÷ 432 000 шт = 23.1 смена 22G: 10 000 000 шт ÷ 368 000 шт = 27.2 смена
Итого, общее кол-во рабочих дней: 50.3 смены ÷ 250 дней = 0.20 = 1 машина
4.3.2 Сборка игл. Данная линия позволяет производить иглы различных размеров. Срез игл должен быть без дефектов. Трубка иглы и пластмассовые детали (головка и защитный колпачок) подаются, направляются, собираются, склеиваются, силиконизируются на машине по сборке игл и проходят контроль качества. Бракованные иглы пневматически выбрасываются в мусорный бак, а готовые иглы скапливаются, а затем транспортируются в лотки в качестве конечной стадии сборки.
Производительность линии сборки игл
Необходимое кол-во машин: 20 000 000 шт ÷ 500 000 шт = 40 дней =1 машина
4.3.3 Процесс литья под давлением. Каждый элемент шприца и иглы, т.е. цилиндр, плунжер, уплотнительная манжета, головка иглы и защитный колпачок, изготавливаются методом литья под давлением. Подготовленные расходные материалы (полипропилен и т.д.) подаются в термопластавтомат. Готовые элементы шприца упаковываются в подходящую полимерную тару и транспортируются на склад.
Производительность термопластавтоматов и прессформ
Необходимое кол-во термопластавтоматов и прессформ
Общее кол-во рабочих дней (Цилиндр и плунжер): 216 дней
Общее кол-во рабочих дней (Уплотнительная манжета): 64.4 дня
Общее кол-во рабочих дней (Колпачок и головка иглы): 91.5 дня
Необходимое кол-во термопластавтоматов: 3 машины
1). Усилие смыкания прессформы 170~200 т для производства цилиндра и плунжера; 216 дней÷250 дней = 0.86=1 машина, 4 прессформы. 2). Усилие смыкания прессформы 130~150 т для производства уплотнительной манжеты; 64.4 дня÷250 дней = 0.26=1 машина, 2 прессформы. 3). Усилие смыкания прессформы 130~150 т для производства головки иглы и колпачка; 91.5 дня÷250 дней = 0.37=1 машина, 4 прессформы.
Необходимое кол-во прессформ = 10 шт
Вес прессформ около 5000 кг
Срок службы одной прессформы — при правильном использовании 8-10 лет (5 000 000 выстрелов)
Время замены одной пресс формы: 30 мин
4.3.4 Печать градуировочной шкалы. Градуировочная шкала и логотип печатаются на наружной поверхности шприца с помощью автоматической печатной машины.
Необходимое кол-во машин: 2. При производстве шприцев объемом 2 и 3 мл применяют одни и те же прессформы и машины. В процессе печати шприцы маркируются согласно соответствующей шкале.
4.3.5. Сборка шприцев. Каждый элемент шприца — цилиндр с нанесенной на него шкалой, плунжер, уплотнительная манжета и игла подается на сборочную машину. Каждая деталь собирается автоматически. На данном этапе также выполняется силиконизирование цилиндра.
Производительность машины по сборке шприцев
Необходимое кол-во машин: 2
4.3.6 Индивидуальная блистерная упаковка. Готовые шприцы автоматически подаются в загрузочный бункер блистерной упаковочной машины и затем транспортируются на упаковку в транспортировочные коробки.
Производительность упаковочной машины
Необходимое кол-во упаковочных машин: 3 мл: 10 000 000 шт ÷147 840 шт = 67.6 смен = 1 машина
5 мл: 10 000 000 шт ÷134 400 шт = 74.4 смен = 1 машина
Итого, общее необходимое кол-во машин: 1). Упаковочная машина с системой автоматической подачи шприцев 2/3 мл. 2). Машина для автоматической подачи для шприцев 5 мл.
4.3.7 Стерилизация. Стерилизация шприцев происходит в специальной камере путем ее наполнения газом окиси этилена. После стерилизации шприцы проходят бактериологическим и биологическим испытаниям. Для этого партия образцов берется в соответствии с определенным планом. Если результаты всех испытаний покажут, что готовые шприцы являются стерильными и качественными, то принимается решение о выводе продукции на рынок. Один цикл стерилизации занимает 7~8 часов. За один день проходит два цикла.
Вместимость стерилизационной камеры объемом 6 м³
Необходимое кол-во стерилизационных камер:
1). 2/3 мл: 10 000 000 шт ÷240 000 шт = 41.7 дней. 2). 5 мл: 10 000 000 шт ÷164 000 шт = 61 день
Общее кол-во рабочих дней: 102.7÷250= 0.41 = 1 камера объемом 6 м³
5. Общие требования к организации производства. 5.1 Необходимая площадь. Заводу с производительностью 20 000 000 миллионов шприцев и игл в год необходимо производственное помещение площадью 780 м². Это площадь не включает офис, склад медикаментов, складскую комнату, коридоры, раздевалку, душевую комнату и т. д.
Рекомендуемая площадь для каждого помещения: 1). Площадь помещения для термопластавтоматов: 120 м². 2). Площадь помещения для сборочной линии: 300 м². 3). Площадь помещения для упаковки готовой продукции: 100 м². 4). Площадь помещения для стерилизации: 100 м². 5). Площадь помещения по производству линии трубок игл: 160 м².
5.2 Производственное помещение. Производственное помещение должно быть полностью стерильным. Необходимый уровень стерильности помещения: помещение для сборочной линии: стерильное помещение, класс cтерильности 100,000~10,000 в соответствии со стандартом ISO 14644-1 и помещение для термопластавтоматов: стерильное помещение, класс cтерильности 100 000 в соответствии со стандартом ISO 14644-1.
5.3 Энергопотребление и расход
Напряжение: 220/380В, 3 фазы
Компрессор: 8м³/мин. при давлении 6 кгс/см² (0,58 МПа)
Расход воды: не менее 2 т в день (исключая циркулирующую воду)
Максимальное потребление энергии
6. Стоимость расходов на оборудование и обслуживание
6.1 Помещение для термопластавтоматов
6.2 Помещение сборки и упаковки
6.3 Линия по производству трубки иглы
7. Необходимое кол-во персонала
8. Схема производственного процесса. Сырье: полипропилен (для шприца и плунжера), эластомеры (для уплотнительной манжеты), чернила для печати, силиконовое масло, газ окиси этилена, упаковочные материалы и т. д.
9. Расчет расхода и стоимости сырья для производства 1000 шт шприцев
Цены на сырье актуальны на сентябрь 2018
Одноразовые шприцы
Расчет расхода и стоимости сырья для производства 1000 шт игл
Цены на сырье актуальны на сентябрь 2018
10. Технические характеристики оборудования
towarkitai.com
Оборудование для производства одноразовых шприцев
Описание
Для производства одноразовых шприцов широко используемых в сфере медицины, предлагается к поставке оборудование для производства одноразовых медицинских шприцев. Одноразовый шприц обладает огромным спектром применения в таких процедурах как различные инъекции, забор крови и т.д.
Характеристики и состав оборудования по производству одноразовых шприцев
В зависимости от видов изделий планируемых к выпуску и общей производительности определяется основной ряд оборудования, входящий в комплектацию линии производства одноразовых шприцев.
Термопластавтомат для производства одноразовых шприцев
На производство одного объема шприца требуется два термопластавтомата, на изготовление цилиндра шприца и изготовление поршня.
Модель термопластавтомата серво и энергосберегающей серии BTW2600-S
Модель по международному стандарту 1200/2600
Технические характеристики А/В/С
Инжекторная установка
Диаметр шнека, мм 50/55/60
Отношение, длина/диаметр 20/20/20
Теоретический объём впрыска, см³ 540/653/778
Инжекторный вес, г 491/ 595/708
Инжекторный ход, oz 17.3/21.0 /25.0
Инжекторное давление, бар 2240/1851/1556
Инжекторный ход, мм 275/275/275
Тип Ⅰ
Максимальная инжекторная скорость, мм/сек 98/98/98
Инжекторная ставка, см³/сек 191/232/275
Способность пластикации, г/сек 32/50/71
Максимальная скорость вращения шнека, оборотов 210/210/210
Тип Ⅱ
Максимальная инжекторная скорость, мм/сек 120/120/120
Инжекторная ставка, см3/сек 239/290/344
Способность пластикации, г/сек 40/62/89
Максимальная скорость вращения шнека, оборотов 265/265/265
Силовая энергия
Давление гидравлической системы, бар 175/175/175
Мощность мотора насоса, Квт Тип Ⅰ 29 и Тип Ⅱ 36.7
Мощность электрического нагревателя, Квт 16.5/20.9/25.7
Кол-во температурного зона, шт N+4
Установка для смыкания формы
Усилие смыкания формы, кн 3200
Ход перемещения прессформы, мм 610
Расстояние между тягами, мм 660*660Максимальная высота прессформы, мм 680
Минимальная высота прессформы, мм 250
Ход выталкивания, мм 180
Усилие выталкивания, кн 77
Кол-во толкателя, шт 13
Прочие характеристики
Объём топливного бака, л 600
Габариты машины, м 7*1.96*2.3
Вес машины, кг 13000
Объём бункера, кг 50
Расход охлаждающей воды, л/мин 193
Пресс-формы для одноразовых шприцов
Пресс-формы (горячий проходной канал)
Кожух для шприцев 5мл., 64 гнезд, полость и стержень выполнены из пресс-формы из S136, цикл 2 миллиона раз
Стержень для шприцев 5мл., 64 гнезд, полость и стержень пресс-формы из S136, 2 миллиона раз
Кожух для шприцев 10мл., 64 гнезд, полость и стержень пресс-формы из S136, 2 миллиона раз
Стержень для шприцев 10мл., 64 гнезд, полость и стержень пресс-формы из S136, 2 миллиона раз
Кожух для шприцев 5мл., 48 гнезд, каркас из Р20Н, твёрдости после улучшения HRC28-32, полость и стержень пресс-формы из 60Si2Mn твёрдость поверхности после закалки и хромирования HRC 55-58; каркас стержня из стали 60#, полость из Cr12MoV твёрдость после закалки HRC 55-58, 1 миллион раз
Стержень для шприцев 5мл., 56 гнезд, каркас из Р20Н, твёрдости после улучшения HRC28-32, полость и стержень пресс-формы из 60Si2Mn твёрдость поверхности после закалки и хромирования HRC 55-58; каркас стержня из стали 60#, полость из Cr12MoV твёрдость после закалки HRC 55-58, 1 миллион раз
Кожух для шприцев 10мл., 24 гнезд, каркас из Р20Н, твёрдости после улучшения HRC28-32, полость и стержень пресс-формы из 60Si2Mn твёрдость поверхности после закалки и хромирования HRC 55-58; каркас стержня из стали 60#, полость из Cr12MoV твёрдость после закалки HRC 55-58, 1 миллион раз
Стержень для шприцев 10мл., 24 гнезд, каркас из Р20Н, твёрдости после улучшения HRC28-32, полость и стержень пресс-формы из 60Si2Mn твёрдость поверхности после закалки и хромирования HRC 55-58; каркас стержня из стали 60#, полость из Cr12MoV твёрдость после закалки HRC 55-58, 1 миллион раз
Пресс-формы (горячий проходной канал)
Кожух для шприцев 5мл., 48 гнезд, каркас выполнен из P20, гнездо и шишель из S136, цикл 2 миллиона раз
Стержень для шприцев 5мл., 48 Каркас из P20, гнездо и шишель из Cr12, 2 миллиона раз
Кожух для шприцев 10мл., 32 Каркас из P20, гнездо и шишель из S136, 2 миллиона раз
Стержень для шприцев 10мл., 28 Каркас из P20, гнездо и шишель из Cr12, 2 миллиона раз
Печатный станок для нанесения рисунка шкалы одноразовых шприцев
Машина для сборки шприца
Машина для сборки шприца объем 5 мл
Машина для сборки шприца объем 10 мл
Упаковочная машина для шприцев
Упаковочная машина для шприца объем 5 мл
Упаковочная машина для шприца объем 10 мл
Шкаф для стерилизации одноразовых шприцев
Дробилка для утилизационного сырья
Смеситель для утилизационного сырья
Представленное оборудование для производства одноразовых медицинских шприцев является самым современным, высокотехнологичным, делая технологический процесс максимально автоматизированным минимизируя возникновение брака. Производительность данной технологической линии по производству одноразовых шприцев 25 млн/год.
Шприц одноразовый медицинский
В недавнем времени использовались исключительно многоразовые медицинские шприцы, которые подвергались обязательному процессу стерилизации. На сегодняшний день все поменялось. Компании производят одноразовые шприцы, имеющие большую область применения, а также долговечны и удобны.
В настоящий период на территории РФ выпускают одноразовые шприцы двух вариантов: двухкомпонентные и трехкомпонентные шприцы, объем которых составляет 1, 2, 5, 10 и 20 мл. Производственные предприятия работают довольно прочно, и исходя из этого нет смысла запускать новое производство или же увеличивать размах старого.
Потребность покупателя на одноразовые шприцы в последнее время остается почти неизменной, и по прогнозам крутых перемен не ожидается.
Производство одноразовых шприцов
Для производства одноразовых шприцов требуется специальное помещение. Первостепенным должно быть оборудование, предназначенное для производства поршня и цилиндра. В производственном цехе требуется разделить складские строения, предназначенные для хранения и приемки сырья.
При производстве одноразовых шприцов для выпуска поршней и цилиндров необходим полипропилен или полиэтилен. Составляющие медицинских одноразовых шприцов изготавливают методом литья. На осуществление этого производственного процесса потребуются специализированные агрегаты, которые оснащены пресс-формами. Технология производства одноразовых шприцов является простой. Сначала происходит заполнение специального бункера сырьем. Далее на оборудовании происходит плавление полученной массы и создание требуемых элементов изделия. После того, как изделие остынет с применением способа шелкографии или офсетной печати на цилиндр наносится измерительная разметка. На заключительной стадии на поршни нанизывают наконечники и совмещают их с цилиндрами. Одноразовый шприц полностью готов. В самом конце готовое изделие проходит стерилизацию и упаковывается в блистер.
taixinasia.com
Производство шприцев и игл
На сегодняшний день в нашей стране производится только 28% от потребности одноразовых шприцев. Остальные 72% шприцев представленных на Российском рынке являются импортными. Спрос на шприцы будет всегда, и с уверенностью можно сказать, что будет только возрастать.
Но всем понятно, что шприцем без иглы инъекцию не сделать. А что же с производством медицинских игл для шприцов в России? Ситуация еще более критическая чем со шприцами. По медицинским иглам Россия почти полностью зависит от импортных поставок.
Планируя начать производство медицинских игл важно знать обо всех возможных вариантах. Одним из способов удешевить производство медицинских игл — это использовать в качестве исходного материала:
- металлическую ленту (штрипс) — 12,7*0,2 мм;
- готовую металлическую трубку — 2,05*0,12 мм.
При таком варианте уменьшается количество необходимого оборудования и соотвественно цена. Например, из одного метра трубки можно получить около 1000 игл, диаметром 0,45, но нужно учитывать длину иглы.
Скачать — Перечень и краткие технические характеристики оборудования для производства медицинских игл..
Скачать — Спецификация на оборудование при годовом объеме производства 2 млрд инъекционной иглы. Дополнительная информация и цены предоставляются на отдельный запрос по данным приведенным в контактах.
В недалеком прошлом шприцы были только многоразовыми. Их подвергали обязательной стерилизации. Однако в настоящее время все изменилось. Производители предлагают одноразовые шприцы, которые обладают большим спектром применения, надежны и удобны.
Своим возникновением одноразовые шприцы обязаны новозеландскому ветеринару и фармацевту Колину Мердоку. За свою жизнь он получил более сорока пяти патентов. Однако наиболее значимым изобретением Мердока стал одноразовый медицинский шприц. По задумке ветеринара, изобретение предполагало ускорение и упрощение процедуры вакцинации животных. Для этого в шприц должно было заранее запаиваться лекарство.
Несколько позднее в его голову пришла гениальная идея о том, что, используя одноразовые изделия во врачебной практике, можно свести к минимуму риск передачи инфекции. Производство одноразовых шприцов в промышленных масштабах было налажено в 1961 г.
В настоящее время в медицинских целях используются шприцы только одноразового применения. Они крайне необходимы для больных диабетом. С их помощью проводят вакцинацию, делают внутримышечные, подкожные, а также внутривенные инъекции.
Однако семьдесят процентов этого востребованного в медицинской практике инструмента изготавливается за пределами нашей страны. Следовательно, стоимость этих изделий гораздо выше той, за которую можно было бы реализовывать аналогичную продукцию отечественного производства.
Не секрет, что спрос на одноразовые шприцы есть и будет всегда, ведь инъекции пока еще никто ничем не заменил. Именно поэтому производство одноразовых шприцов является перспективной бизнес-идеей. Это дело способно приносить неплохой доход.
В медицинской практике инъекции, забор крови, а также отсасывание из полостей патологического содержимого производится при помощи специального инструмента. Им является одноразовый шприц. При этом по строению выделяют двухкомпонентные шприцы, состоящие из поршня и цилиндра; трехкомпонентные инструменты, составной частью которых (кроме поршня и цилиндра) является также смазанный специальной жидкостью резиновый наконечник, предназначенный для более гладкого скольжения по цилиндру.
Одноразовые шприцы могут отличаться расположением наконечника. У одних медицинских инструментов оно концентрическое, или коаксиальное. Это означает его расположение в центральной верхней части цилиндра. Обычно такое строение характерно для шприцов, имеющих объем от одного до одиннадцати миллилитров. Производятся инструменты для инъекций с боковым расположением наконечника (эксцентрическим). Обычно это шприцы большого объема (от двадцати двух миллилитров).
В одноразовых шприцах могут быть и различные типы крепления игл. Различают луер, когда игла просто надевается сверху на цилиндр; луер-лок – иглу вкручивают в цилиндр; и несъемный тип, когда иглу интегрируют в корпус цилиндра.
Размеры одноразовых шприцев.
Одноразовые шприцы отличаются и своими объемами. Это позволяет использовать их для различных целей.
- Малого объема – 0,3 и 0,5, а также 1 миллилитр. Такие шприцы находят применение в эндокринологии (для инсулиновых инъекций), во фтизиатрии (шприцы туберкулиновые), а также в неонатологии (для взятия внутрикожных проб аллергологического характера, а также проведения вакцинации).
- Стандартного объема – 2, 3, 5 и 10, а также 20 миллилитров. Как правило, такие шприцы служат медицинским инструментом при выполнении внутримышечных, подкожных, а также внутривенных инъекций.
- Большого объема – 30, 50, 60 и 100 миллилитров. Такие шприцы необходимы для проведения процедур отсасывания жидкости, а также для промывания полостей и введения веществ.
Технологический процесс.
Производство одноразовых шприцов потребует наличия специального помещения. Прежде всего, должна быть линия, предназначенная для изготовления поршня и цилиндра. На производственном участке также необходимо отгородить складские помещения для приема и хранения сырья.
Для изготовления поршней и цилиндров потребуется полипропилен или полиэтилен. Части одноразовых шприцов получают методом литья. Для реализации этого процесса понадобятся специальные машины, оснащенные пресс-формами.
Технология изготовления одноразовых шприцов проста. Прежде всего, производится засыпка сырья в специальный бункер. После этого машиной осуществляется плавка массы и формирование нужных частей изделия. После охлаждения при использовании метода шелкографии или офсетной печати на цилиндры наносится мерная шкала. На следующем этапе на поршни надевают наконечники и соединяют их с цилиндрами. Шприц готов. Его стерилизуют и производят упаковку в блистеры.
Необходимое оборудование.
Линии по производству шприцов должны состоять из определенного набора машин. Среди них следующие:
- Термопластавтомат. Это машина, предназначенная для литья
- Прессформы
- Машина, предназначенная для охлаждения
- Вакуум-формовочная или пневмоформовочная машина, предназначенная для упаковки готовых изделий
- Станок для офсетной печати
- Машина, с помощью которой производится сборка одноразовых шприцов
- Стерилизатор
Медицинские иглы для шприцов существуют во многих вариантах: маленькие, большие, полые, хирургические, длинные, короткие, одноразовые, многоразовые… Но объединяет все медицинские иглы для шприцов – острый кончик. Насколько безболезненным будет укол зависит и от иглы шприца. Конечно, и конструкция самого шприца играет большую роль, какой используется поршень. Если используют для инъекций трехкомпонентные шприцы, то болезненные ощущения будут снижены к нулю.
Тот пластиковый одноразовый шприц, который мы знаем, появился пятьдесят лет назад. До этого 160 лет подряд в Европе пользовались многоразовыми шприцами. Переход на одноразовые шприцы во многом снизил риск заражения инфекциями.
Медицинские иглы для шприцов поступили в продажу именно с изобретением пластиковых одноразовых шприцов. Один только вид шприца и острой иглы пугает и детей, и взрослых. Но, не смотря на это, медицинская игла спасла жизнь многим людям.
Как же происходит сам процесс изготовления медицинской иглы для шприцев?.
Материал для изготовления иглы для шприцов – медицинская сталь. Используются небольшие пластины стали, которые специальный станок сворачивает в трубочку. Чтобы не было стыковочных швов, используют луч лазера для качественной запайки. Затем заготовки игл закаливают, что делает их прочнее. Но чтобы эта трубочка была хоть немного похожа на иглу, уходит несколько дней. Затем весь процесс сосредотачивается на заточке самой иглы.
cn-redbridge.ru
Оборудование для производства одноразовых шприцев — СМД-Групп
Наша компания предлагает подбор, а также поставку «под ключ» оборудования для производства любых видов одноразовых медицинских шприцев, в т.ч. самоблокирующихся (саморазрушающихся) шприцев третьего поколения.
О безопасных шприцах 3-го поколения читайте здесь >
Безопасный шприц 3 поколения
Работа по заявкам ведется только в рамках платных консалтинговых услуг, информация прорабатывается индивидуально по каждой заявке.
При подаче заявки на подготовку информации о линии производства одноразовых шприцев заказчику необходимо определиться с требованиями к производству и ответить на следующие основные вопросы:
- Какие виды шприцев планируется производить — двухсоставные, трехсоставные, безопасные третьего поколения…
- Применение шприцев — общего назначения, инсулиновые, для животных…
- Объемы шприцев в мл.
- Тип иглы составная (из частей), односоставная (уни-боди)…
- Тип наконечника Люэра — смещен в сторону, по центру.
- Требуемая производительность по каждому виду продукции — годовой объем производства.
- Количество рабочих часов в смену, количество смен.
- Комплектация линии — например, только сборка шприца, либо производство всего, кроме игл, либо полное производство с иглами…
- Прочие детали, требуемые для подготовки информации.
Также заказчик может выбрать страну производства оборудования — Корея, Китай, Европа…
При необходимости подберем оборудование для производства шприцев под заданный бюджет.
Наша компания окажет полную поддержку Вашего проекта по производству одноразовых шприцев в любом требуемом объеме — подбор оборудования, помощь в расчете производства, поиск сырья, поставка в адрес заказчика «под ключ», решение прочих вопросов.
Наше участие в проекте: В Калмыкии создадут производство шприцев третьего поколения
Видео — одноразовый шприц 3 поколения:
smd-group.com
Переработка одноразовых шприцов — часть 2
Переработка отходов медицинского назначения, в частности одноразовых шприцев, остается на сегодняшний день весьма актуальной проблемой. Во многих областях России сложилась критическая обстановка по сбору и сортировке медицинских изделий [2,4].
Медицинские отходы составляют около 2% от общего объема твердых бытовых отходов. В России в настоящее время образуется 0,6-1 млн. тонн медицинских отходов в год. Система сбора, удаления, переработки и обезвреживания медицинских отходов в нашей стране пока несовершенна, при этом количество их имеет устойчивую тенденцию к интенсивному росту [3].
В городе Магнитогорске ежегодно образуется до 130 тонн медицинских одноразовых шприцев.
В таблице 1.2 указаны медицинские учреждения города и сколько тонн в год приходится на каждое учреждение.
Таблица 1.2 Отходы одноразовых шприцев в городе Магнитогорске
На полигонах ТБО уничтоженные механическим путем фармацевтические препараты резко увеличивают токсичность образующегося фильтрата, что создает риск загрязнения не только почвы, но и подземных водоносных горизонтов.
ВОЗ декларирует следующие положения, касающиеся переработки медицинских отходов:
использование всеми производителями одной и той же пластмассы для изготовления шприцев и других изделий однократного применения, чтобы облегчить их утилизацию;
преимущественное использование медицинских устройств, не содержащих поливинилхлорид [6,8].
Сегодня на отечественном фармацевтическом рынке широко представлены стерильные изделия медицинского назначения. Производители постоянно совершенствуют и расширяют их ассортимент. Особое место среди них занимают шприцы инъекционные одноразового применения. В первую очередь это определяется их использованием как медицинскими специалистами для оказания помощи больным с тяжелыми патологическими процессами, так и далекими от медицины людьми для оказания помощи себе или своим близким и знакомым.
Шприц состоит из цилиндра и шток — поршня (разборного или неразборного). Цилиндр имеет наконечник-конус типа «Луер», упор для пальцев и градуированную шкалу. Узел шток-поршень состоит из штока с упором, поршня с уплотнителем и линией отсчета [3,5].
Материалы, из которых изготовляют шприцы, зависят от их конструкции, назначения и метода стерилизации. Материалы должны быть совместимы с инъекционными препаратами.
Для изготовления цилиндров рекомендуются в основном определенные сорта полиэтилена высокой плотности, полистирола и сополимера стирола и акрилонитрила, отвечающие фармакопейным требованиям. Поршни изготовляют из высококачественной натуральной (натуральный каучук) и искусственной (силиконовый каучук) резины. Для штоков и уплотнителей, неразборных шток-поршней используется полипропилен [4].
В таблице 1.3 представлена классификация одноразовых шприцев.
Таблица 1.3 — Классификация шприцев
На сегодняшний день существуют различные способы переработки одноразовых шприцев, схема которых представлена на рисунке 1.2
Рисунок 1.2 — Способы переработки одноразовых шприцев
1) Термические методы
а) Инсинерация (Сжигание)
Термический метод уничтожения отходов, а попросту, их сжигание уже не является оптимальным решением проблемы медицинских отходов. Установки, предназначенные для сжигания отходов (инсинераторы) были широко распространены в мире еще 10-15 лет назад. Но с тех пор многое изменилось. В частности, выяснилось, что сжигание не так уж и безобидно и при всех своих достоинствах обладает такими неприятными особенностями, как, например, образование диоксинов. Диоксины — это загрязнители, выделяющиеся при сжигании отходов, вызывающие ряд заболеваний, включая рак, повреждения иммунной системы, нарушение деятельности репродуктивной и других систем организма. Кроме того, они обладают свойством биокумуляции, то есть способны перемещаться по пищевым цепям от растений к животным, концентрируясь в мясе и молоке и, как результат, в теле человека. Диоксины являются предметом особого беспокойства, так как повсеместно распространяются в окружающей среде человека на тех уровнях, на которых способны вызвать нарушения жизнедеятельности живых организмов. Поэтому целые популяции уже сейчас страдают от пагубных последствий воздействия диоксинов. Инсинераторы также вносят свой «вклад» в загрязнение окружающей среды ртутью, сильнодействующим нейротоксином, ослабляющим двигательные, сенсорные и ряд других функций [4].
Инсинераторы — источник поступления в окружающую среду значительных количеств тяжелых металлов, таких, как свинец, кадмий, мышьяк и хром, а также галогенсодержащих углеводородов, кислотных паров («предшественников» кислотных дождей, частиц, приводящих к заболеванию дыхательной системы), парниковых газов.
Сегодня проблема распространения загрязнителей не решается должным образом: они просто перемещаются из одной среды (воздуха) в другую (почву или воду).
Зола из инсинераторов крайне токсична, на что часто не обращают должного внимания. Захоронение фильтров и золы на полигонах ТБО также не безопасно, поскольку есть вероятность попадания токсинов в грунтовые воды; в некоторых местах зола просто рассеивается и попадает в населенные или сельскохозяйственные районы.
Большинство специалистов приходят к мнению, что сжигание — это неустойчивая и устаревшая форма обращения с медицинскими отходами [4,9].
б) Пиролиз
Альтернативой обычным методам термической переработки твердых отходов являются технологии, предусматривающие предварительное разложение органической фракции отходов в бескислородной атмосфере (пиролиз), после чего образовавшаяся концентрированная парогазовая смесь (ПГС) направляется в камеру дожигания, где в режиме управляемого дожига газообразных продуктов происходит перевод токсичных веществ в менее или полностью безопасные.
К принципиальным положительным особенностям бескислородных пиролизных технологий уничтожения органических материалов, позволяющих обеспечить экологическую безопасность выбросов, в том числе и хлорсодержащих, относятся:
mirznanii.com
С 2006 года ООО «Эскулап», расположенное в Курске, занимается изготовлением трехкомпонентных одноразовых шприцев. Предприятие оснащено современным южнокорейским оборудованием, применение которого обеспечивает оптимальное соотношение качества и стоимости производимой продукции. Проектная мощность производственного цеха составляет 200 млн шприцев в год. Характеристики изделий ООО «Эскулап»Конструкция шприцев детально продумана:
Производство разделено по участкам и осуществляется в один поток. Срок годности шприцев – 5 лет с даты стерилизации (даты изготовления). Основное оборудование цеха ШОП:
Основное полимерное сырье, используемое для изготовления деталей шприцев (цилиндров и штоков-поршней), – полипропилен (марки: «БАЛЕН», «КАПЛЕН»). Термопластавтоматы для литья цилиндров и штоков-поршней отличаются только пресс-формами и некоторыми режимными параметрами, связанными с особенностями свойств исходных полимеров. Пресс-формы оснащены сложной системой каналов, организующих зоны с различными температурными режимами водой с постоянной температурой 15±30С. Охлаждение пресс-формы обеспечивает получение чистого цвета, прозрачного блестящего цилиндра без прилипания к форме, отсутствие нитеобразования расплава при размыкании пресс-формы. Сборка готового изделия осуществляется в следующем порядке:
Первичная упаковка производится на автомате (линии)(BLISTER) фирмы COA INTERNATIONAL. Собранные шприцы загружают в бункер упаковочной линии в ячейку из термоформуемой (полиэтилен-полиамидной или полиолефиновой) пленки и газопроницаемой бумаги с нанесением маркировки. Стерилизация осуществляется газовым методом (окисью этилена). |
eskulap.su
Линии по производству медицинских шприцов и игл
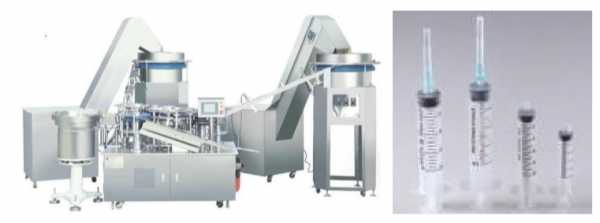
Линии по производству шприцов и игл
- Автоматические машины для производства одноразовых шприцов
- Сборочные машины для производства 2-х компонентных и 3-х компонентных шприцов
- Машина для нанесения шкал на шприцы
- Машины для производства инсулиновых шприцов
- Автоматическая иглосборочная линия
- IV Катетеры
- IV решения
- Формовочные машины (Molding machines)
- Блистерные упаковочные машины
- Этилен оксид стерилизаторы
Jeesung Corporation — одна из ведущих инженерных компаний в Корее, которая с 1989 года профессионально проектирует и производит машины для автоматической сборки изделий медицинского назначения.
Компания успешно реализовала проекты заводов по производству шприцов, игл и катетерных решений в Египте, Узбекистане, Индии, Иране, Мьянме, Бангладеше, Пакистане, а также на внутреннем рынке Южной Кореи. Высоко профессиональные инженерные решения позволяют частично или полностью автоматизировать производство медицинских изделий, при этом сократить издержки и повысить производительность завода. При проектировании линий учитываются все требования и пожелания заказчика, внимательно изучаются планы и чертежи помещения, расположение комнат, «чистых» комнат, залы стерилизации. Период монтажа курируется высокопрофессиональными инженерами из Кореи, которые следят за четким размещением и установкой оборудования согласно технологической карте. После финальной инспекции проводится обучение местных тех. специалистов.
Сборочные машины Jeesung Corp. отлично себя зарекомендовали и имеют высокий срок службы.
kotrakz.com