Титан
Титан особо ценится за низкую плотность в сочетании с высокой прочностью и отличной стойкостью к коррозии. Максимальный показатель прочности на разрыв чистого титана может достигнуть 740 Н/мм2, а показатель такого сплава как LT 33, содержащего алюминий, ванадий и олово, достигает 1200 Н/мм2. Температурный коэффициент расширения металла составляет около половины от температурного коэффициента расширения нержавеющей стали и меди, и одну третью часть от данного коэффициента алюминия. Его плотность составляет около 60% от плотности стали, одну вторую от плотности меди и в 1.7 раз больше, чем у алюминия. Его модуль упругости составляет половину от модуля упругости нержавеющей стали, что делает его стойким и прочным к ударам.Авиакосмическая промышленность остается самым крупным потребителем этого металла. Титановые сплавы, способные к функционированию при температурах от 0°С до 600°С, используются в авиадвигателях для дисков, лопастей, валов и корпусов.
Начало
Хотя о существовании титановых минералов известно более 200 лет, серийное производство титана и пигмента диоксида титана для продажи началось не раньше 1940 года. В.Дж.Кроли запатентовал метод производства титана методом угле-хлорирования титанового диоксида в 1938году. Этот элемент был назван в честь Титанов из греческой мифологии немецким химиком МТ.Клапрот, который успешно отделил диоксид титана от рутила в конце восемнадцатого века.
Американское Геологическое управление подсчитало, что добыча ильменита в мире в 2004 году в целом составила 4. 8 млн тонн, в то время как добыча рутила в мире в целом составила 400 000 тонн. Ильменит обеспечивает потребность в титановых минералах в мире на 90%. По подсчетам Американского Геологического управления мировые ресурсы анатаза, рутила и ильменита в общем составляют более двух миллиардов тонн.
Производство
Первый этап в производстве титана заключается в изготовлении губки путем хлорирования руды рутила. Хлор и кокс соединяют с рутилом для создания тетрахлорида титана, который затем в замкнутой системе соединяют с магнием для производства титановой губки и хлорида магния. Магний и хлорид магния извлекают для переработки путем использования вакуумного дистилляционного процесса или технологического процесса выщелачивания, создателем которого является Кроль. Основными производителями титановой губки являются США, Россия, Казахстан, Украина, Япония и Китай.
Метод вакуумно-дугового переплава или электронно-лучевая холодная подовая печь используются для плавки губки со скрапом и/или легирующими элементами, такими как ванадий, алюминий, молибден, олово и цирконий для производства переплавленных электродов. Данные электроды можно вновь переплавить методом вакуумно-дугового переплава для производства материала по наиболее строгим спецификациям в авиакосмической сфере и в сфере высоких технологий, или их можно отлить прямо в слябы.
Слитки ВДП имеют цилиндрическую форму и могут весить до 7.94 тонн. Их куют для изготовления слябов или биллетов или используют для прецизионного литья. Методом прокатки производят плиты, листы прутки, стержни и проволоку. Трубы производят из нарезанных из листов штрипсов.
Применение
В повседневной жизни титан обычно ассоциируется с ценными изделиями, такими как наручные часы, оправы для очков, спортивные товары и ювелирные изделия, но кроме этого он широко используется в авиации, а также в других областях, в которых титан, благодаря сочетанию своих физических свойств и био-совместимости, имеет преимущества перед другими металлами. В зависимости от непосредственного назначения, титан конкурирует с никелем, нержавеющей сталью и циркониевыми сплавами.
Многообещающие признаки роста показывает автомобильный сектор. В системах подвесок, например, замена стальных пружин на титановые дает преимущество в виде уменьшения веса на 60%. Также титан применяют в производстве коленчатых валов, соединительных тяг и выхлопных систем. Электростанции и заводы по опреснению морской воды также являются важными областями для роста применения титана. В то же время идет развитие производства титановых подложек для компьютерных жестких дисков.
Крупнейший производитель титана в России может полностью остановить работу | 17.06.20
Крупнейший в мире производитель титана «ВСМПО-Ависма» (Свердловская область, входит госкорпорацию «Ростех») может приостановить работу предприятия в сентябре, сообщил и. о. гендиректора «ВСМПО-Ависма» Максим Кузюк в видеозаписи, опубликованной на официальной странице компании в соцсети «ВКонтакте» в среду.
Корпорация из-за снижения потребления в условиях пандемии коронавируса пересматривает собственные производственные программы, сокращая объемы товарной титановой продукции в 2020 году с запланированных 39 000 тонн в год до 26 500 тонн, производство титана губчатого снижается с 44 000 тонн до 35 000 тонн в год. Также сокращаются все непроизводственные расходы, откладываются инвестиционные проекты, а фонд оплаты труда приводится в соответствие с актуальной производственной программой.
«Мы рассматривали август на остановку. Сегодня приняли решение, что не будем останавливаться. Рассматриваем сентябрь, но решение будет принято в зависимости от того, сколько заказов мы реально в систему внесем. Мы посмотрим загрузку, потому что работать на очень маленькой загрузке это еще хуже, чем остановка», — сказал он, добавив, что перед коммерческим блоком стоит задача по поиску заказов.
Кузюк отметил, что ранее клиентов компании не устраивал длительный срок выполнения заказа, доходивший до 12 месяцев, с падением объемов у компании появляется возможность обрабатывать заказы быстрее.
И. о. гендиректора добавил, что сокращения в компании не коснутся инженерного состава, оптимизация штата будет проводиться только в руководящем составе и вспомогательном персонале. «Массовых сокращений не планируем», — резюмировал Кузюк.
Назначенный 6 мая и. о. гендиректора Кузюк лично возглавляет процесс адаптации одного из крупнейших в мире производителей титана к изменившимся экономическим условиям. Прилетевшая команда топ-менеджеров будет контролировать работу компании в режиме реального времени, что позволит ей преодолеть сложный период и заложить фундамент для роста в долгосрочной перспективе, сообщала ранее пресс-служба предприятия.
О компании
«ВСМПО-Ависма» входит в госкорпорацию «Ростех» и является монополистом в отечественной титановой отрасли, выпуская треть всего мирового титана для авиапрома. Контрольный пакет акций (около 60%) принадлежит менеджменту корпорации, блокпакет — 25% плюс одна акция — Ростеху. Корпорация производит титан, слитки и все виды полуфабрикатов из титановых сплавов, а также прессованные крупногабаритные изделия из алюминия, полуфабрикаты из легированных сталей и жаропрочных сплавов на никелевой основе.
Информационное агентство России ТАССНебесный металл. Как работает единственный в России титановый завод | Промышленность
Эксперимент века
Рождением салдинского титана можно считать 1957 год. Тогда, в феврале, на заводе №95 (с 1982 года – Верхнесалдинское металлургическое производственное объединение) выплавили первый четырёхкилограммовый слиток. Кусок тусклого металла стал настоящим подарком для советского авиастроения и космонавтики.
Путь к первому слитку был непростым, но удачным. Салдинцы во главе со знаменитым металлургом Владиславом Тетюхиным, ставшим впоследствии руководителем комбината, экспериментировали с титановой губкой. Её делали (и делают до сих пор) на магниево-титановом комбинате АВИСМА (аббревиатура от «АВИаСтроительные МАтериалы») в Березниках (Пермский край) из ильменитового концентрата. Так или иначе, но дерзкий эксперимент 60-летней давности развился в огромный механизм, больше похожий на часы. В 2005 году две площадки, синхронно работающие на расстоянии сотен километров, объединились в одну структуру.
Интересная деталь: сырьё для ильменитового концентрата приходится импортировать. Этот факт удивителен ещё и потому, что основа для титановой губки – очень распространённый элемент, он есть везде. Например, несколько лет назад месторождение пытались разработать в Тамбовской области, но сырьё оказалось таким, что покупать за рубежом было выгоднее. До сих пор шутят, что на той инициативе успел заработать политические очки лишь кандидат в местные губернаторы. Впрочем, стоимость сырья в себестоимости готовой продукции невелика – не более 5%, поэтому возить его можно хоть из Австралии.
Титановый механизм
На часах 10:30 утра. По дороге из Екатеринбурга в Верхнюю Салду мы чуть-чуть задерживаемся и… рассинхронизируемся с заводом – не успеваем на загрузку губки и титановой стружки. Её уже спрессовали в большой электрод и по правилам электрометаллургии переплавили в «свечу» высотой больше трёх метров. Искрящийся и переливающийся всеми цветами радуги слиток мы успели увидеть до того, как его откуют, отштампуют, прокатают, обточат и рассверлят на станках.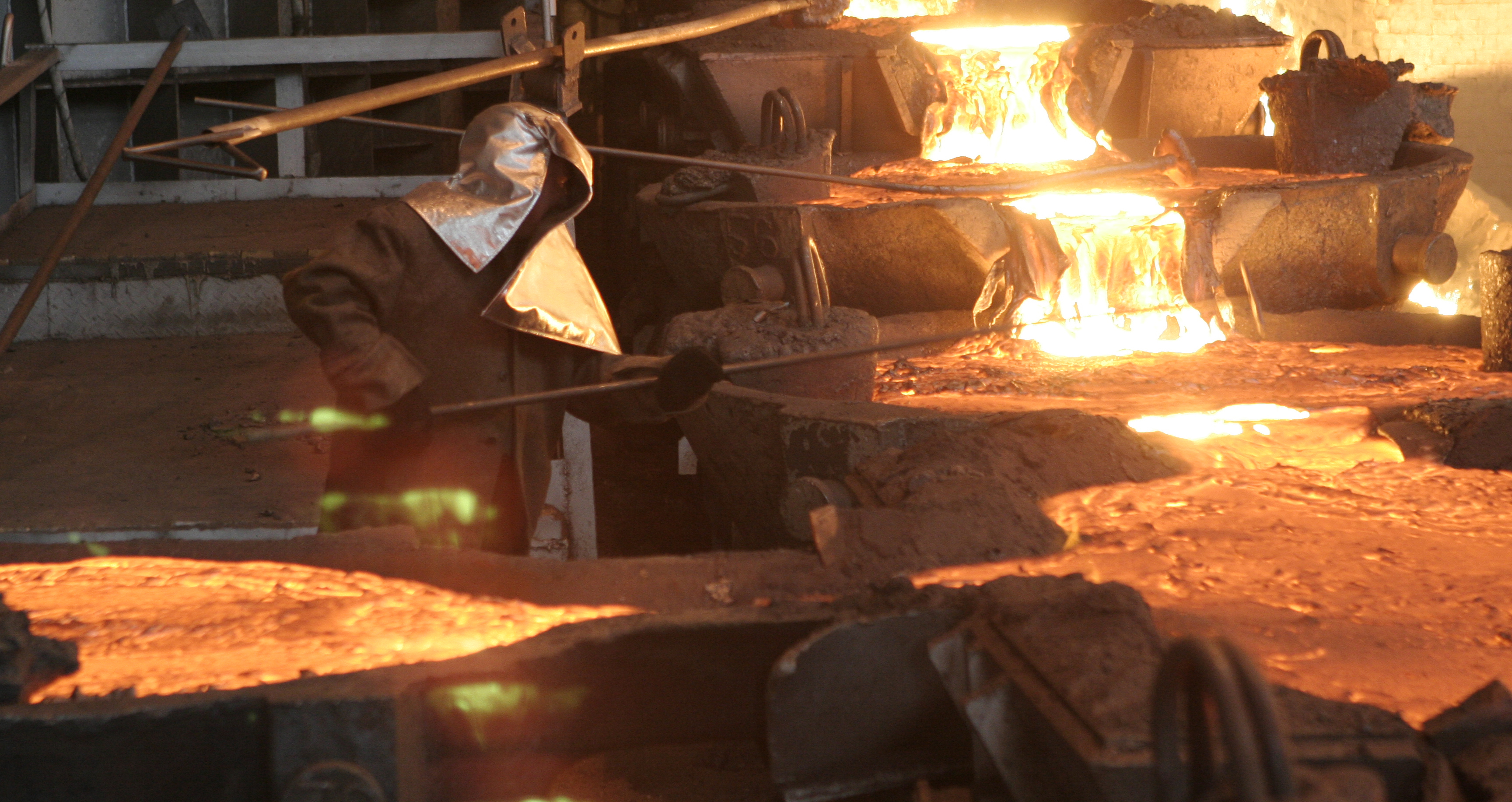
Обработка заготовок похожа на пекарню, по которой нас водит начальник цеха Андрей Лазутин. Он рассказывает, что на титановой «кухне» биллеты на прессе вытягивают, раскатывают, нарезают и ягко снимают с них фаску. На наших глазах один из прутков режут на куски, нагревают и везут на очередной пресс, где под давлением создаются шайбы – «бублики». А то, что буквально выдирается из куска, на цеховом жаргоне так и называется – «выдра». Шайбу раскатывают на кольцераскатном стане, где важен диаметр. Чем он больше, тем выше потенциал производителя, его возможности. В данном случае раскатывают кольцо диаметром более 3 метров. А вообще, тут делают 1,5-метровые кольца для турбин известных марок самолётов. Заказы на детали подвески поступали и от команд «Формулы-1».
Пресс конкурентов
«Семидесятка» – так с любовью в Салде называют один из двух самых больших в мире гидравлических штамповочных прессов (второй такой установлен на Самарском заводе). Эту многотонную гордость уральского предприятия сделали на НКМЗ – Новокраматорском машиностроительном заводе – и установили в этой кузнице ещё в 1961 году.
35-метровый жёлто-зелёный гигант сильно напоминает живого трансформера, который с лёгким усилием в 75 000 тонн виртуозно и почти бесшумно штампует бесшовные детали для самолётов. Заводской любимчик за почти шесть десятков лет службы успел отличиться не раз: именно на нём в 1974 году была изготовлена переходная втулка стыковочного узла советско-американского проекта «Союз-Аполлон», а в 2003 году произведена самая большая и тяжёлая штамповка в мире – балка шасси для Airbus A380 весом почти 3,5 тонны и длиной около 5 метров.
На наших глазах выдавливается очередной тракбим – деталь для стойки шасси нового самолёта. Рядом лежат уже отштампованные будущая балка крепления фюзеляжа и другие силовые – их тут называют «ответственными» – детали лайнеров. Фото: «АиФ-Урал»/ Дмитрий ШевалдинНа наших глазах выдавливается очередной тракбим – деталь для стойки шасси нового самолёта. Рядом лежат уже отштампованные будущая балка крепления фюзеляжа и другие силовые – их тут называют «ответственными» – детали лайнеров. По аналогии с кольцераскатным станом, где важна способность дать больший диаметр, прессу важно давление – от него зависит качество, однородность металла заготовки. В этом уральцы пока первые, но, говорят, не так давно появился 85 000-тонный соперник в Китае. Во всяком случае, о нём пишет китайская пресса, правда, без подробностей. Пока же защитой от потенциального конкурента может стать отсутствие у китайцев сертификатов, без которых отправлять титан в небо – никак.
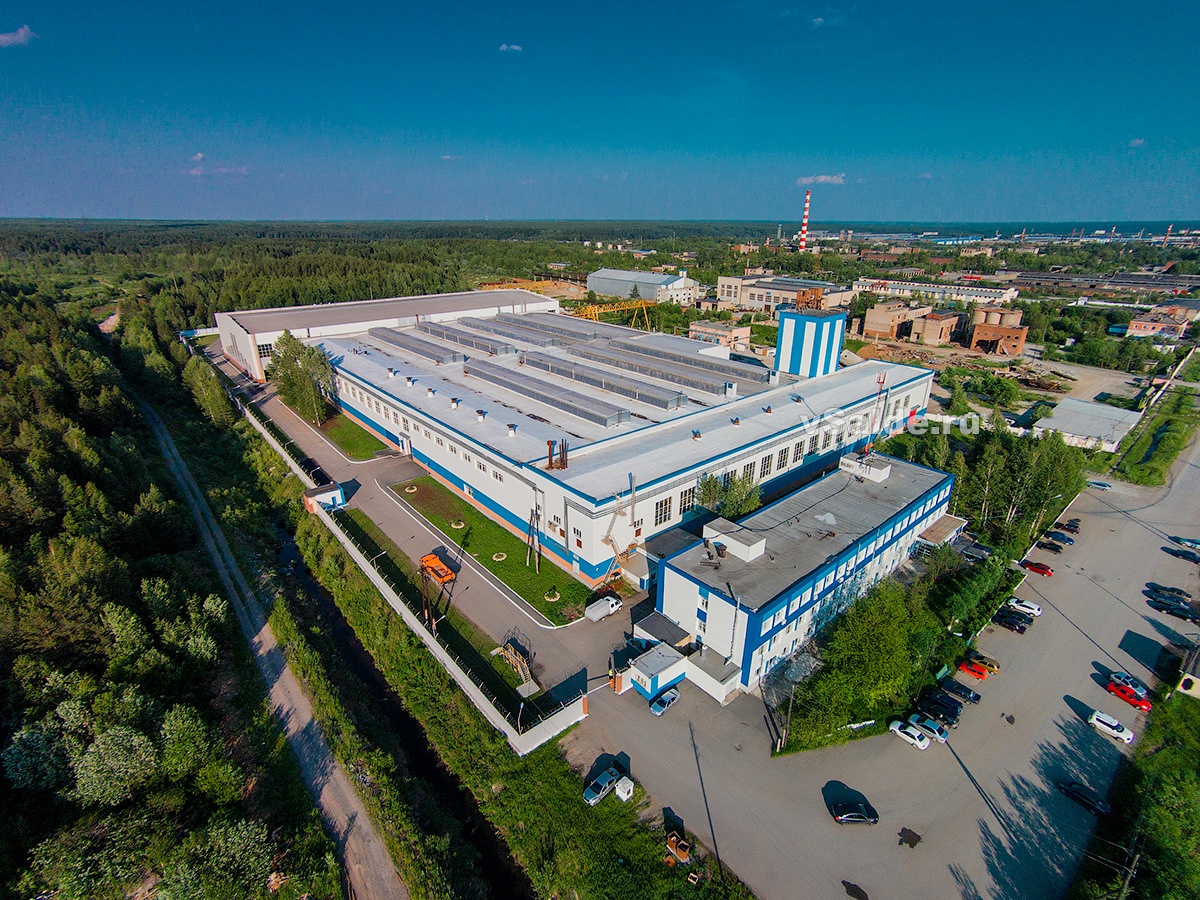
Политическая страховка
Продукция высокого уровня передела – мантра, которую наизусть знали министры «росселевского призыва». Со времён первого постсоветского руководителя Свердловской области промышленная политика региона настраивалась на производство не просто заготовок, а полноценных деталей. Ведь если – условно – штамповка для стойки шасси стоит как две «Тойоты Королла», то готовая деталь стоит – тоже условно – как восемь.
Цех механообработки – гордость предприятия. Здесь титановые заготовки приводят в надлежащий вид и готовят к отправлению. Фото: «АиФ-Урал»/ Дмитрий ШевалдинНа выполнение сверхзадачи работает цех механической обработки, где станки рассверливают титановые штамповки сразу в пяти координатных плоскостях, превращая их в черновые детали для самолётов. «Заготовка на станках протачивается, просверливается, а затем подвергается термообработке. Пять координат – это вдоль, поперек, вверх и по двум диагоналям», – объясняет начальник цеха Сергей Таланцев. Впрочем, и тут видна глубина европейской и американской кооперации: один станок – из США, ещё одна линия итальянского производства монтируется на помощь чешской.
В завершение остается добавить, что работает и платит налоги товаропроизводящее подразделение корпорации ВСМПО-АВИСМА на Урале, в городе с населением 42 тысячи, из которых каждый второй дееспособный житель работает на ВСМПО и справедливо считает себя титанщиком.
Сегодня российским титаном «ответственного применения» закрывается около 50% всей потребности Airbus, 35% — Boeing. Среди заказчиков ВСМПО-АВИСМА 50 компаний из 350 стран мира, среди них не только вышеперечисленные гиганты самолетостроения, но ещё и Embraer, Rolls Royce, General Electric, Honeywell, MTU и другие.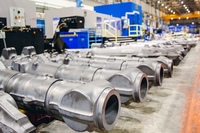
| |||||||
Адрес склада: Москва, ул. Байкальская, д.7, стр 4. Телефон: (495) 772-07-39Телефон/Факс: |
| ||||||
Copyright © ООО НПО «ТИТАН», 2007—2021 7720739@mail. ![]() |
Перспективы освоения титанового сырья в России
Титан относится к широко используемым в промышленном производстве элементам. Важнейшими видами титановой продукции являются пигментный диоксид титана (мировое производство около 3 млн.т TiO2 в год) и металлический титан (60-70 тыс.т Ti в год). Почти 90% диоксида титана используется в качестве наполнителя резины, бумаги, пластмасс, при матировании искусственного волокна, как усилитель силиконового каучука, в полупроводниковой керамике и т.д. Металлический титан и его сплавы, обладающие высокой коррозионной стойкостью и хорошим сочетанием механических и технологических свойств, применяются в самых различных отраслях промышленности: авиационной, космической, химической, металлургической, в машиностроении, судостроении.
Главными производителями пигментного диоксида титана являются США, Германия, Япония, Англия, Франция (около 70% мирового производства). Металлический титан производится в США, Японии, Великобритании, Казахстане, Украине и Китае.
В странах СНГ ведущее место по разведанным запасам титановых руд занимает РФ (58.5%) и Украина (40.2%). Однако в России в основном находятся неосвоенные месторождения, титановый концентрат из которых не производится. Главным же производителем титанового сырья (ильменита, рутила) в СНГ является Украина. В целом в СНГ известно большое число месторождений титана, которые относятся к различным промышленно-генетическим типам (табл. 1) По условиям образования они делятся на магматические, коры выветривания (остаточные), россыпи и метаморфизованные месторождения. В СНГ ведущую роль в получении титановых концентратов играют древние прибрежно-морские (ильменит, рутил, циркон и др.), а также аллювиальные и аллювиально-делювиальные россыпи ильменита и остаточные его месторождения, сосредоточенные в основном на Украине. Из большого числа титаносодержащих минералов главное промышленное значение имеют ильменит, рутил, лейкоксен, анатаз. Перспективны – перовскит, сфен и титаномагнетит.
В промышленных рудах содержится 0.5-35% TiO2, во вкрапленных рудах магматических месторождений обычно 7-10% TiO2. Россыпи часто характеризуются более низкими содержаниями титана. Однако относительно простое получение титановых концентратов из россыпей делают рентабельной их эксплуатацию. Добытый материал перерабатывается на обогатительных фабриках, где получают самостоятельные концентраты: ильменитовый, рутиловый, цирконовый, ставролитовый и др. Большинство из получаемых титановых концентратов содержат целую группу элементов-примесей (Sc, V, Ta, Nb, TR, Ga и др.), представляющих промышленную ценность. Особую ценность среди них представляет дорогостоящий скандий, который постоянно содержится в ильмените (до 0.02%) и рутиле (до 0.01%). В 1995 г. в США 1 г Sc2O3 (99.9%) стоил 63.2 долл., а 1 г металлического скандия (99.99%) – 125 долл. (по данным коммерческого каталога).
В настоящее время на территории СНГ титановые концентраты из руд коренных месторождений не получают. За рубежом главными производителями ильменитового концентрата из руд коренных месторождений являются Канада и Норвегия. Суммарно они дают около 30% ежегодной мировой титановой продукции.
На территории России все наиболее важные месторождения титана находятся в девяти металлогенических провинциях. Основными титанорудными провинциями России, в которых сосредоточено 81.6% ее запасов и 52.4% ресурсов титана являются: Тиманская (Ягерское и др. месторождения), Оклемо-Становая (Кручининское, Большой Сейим и др.), Уральская (Медведевское, Копанское и др.) (рис.1). Среди указанных провинций особняком стоит Тиманская, характеризующаяся уникальным генетическим типом титановых месторождений, представленных нефтеносными лейкоксеновыми песчаниками. Запасы руд значительные, превышающие на отдельных объектах десятки миллионов тонн. Содержание лейкоксена в них от десятков до нескольких сотен кг/м3 (Ярегское и др.). Содержание TiO2 в песчаниках в среднем 10.5%. Содержание лейкоксена в тяжелой фракции до 80-90%. В качестве важных примесей редких металлов присутствуют ниобий, тантал, цирконий. Получаемый после обогащения концентрат, содержащий 45-55% TiO2, 34-40% SiO2 и 5-35% нефти, после отделения нефти пригоден для производства пигментного диоксида титана.
Другим перспективным для России типом титановых месторождений является магматический (месторождения Коларского, Джугджурского, Баладекского анортозитовых массивов). Интерес может представить месторождение Большой Сейим (Амурская обл.), титаномагнетит-ильменитовые руды которого содержат 5-15% TiO2. Из них получен кондиционный ильменитовый концентрат (46% TiO2), магнетитовый (63% Feобщ., 0.7% V2O5), апатитовый (40% P2O5). Запасы TiO2 на месторождении 23 млн.т. Заслуживают внимания апатит-титаномагнетитовые руды Джугджурского анортозитового массива, где выделяются три главных рудных поля: Богидесское, Гаюмское и Маймаканское. Эти руды содержат: 10-90% апатита, 50-70% титаномагнетита, до 10% ильменита. Концентрация TiO2 в титаномагнетите составляет 5. 4-15.5%. Выполнен комплекс технологических работ по получению ильменитового концентрата из руд Медведевского, Копанского и Маткальского месторождений (Урал), из которого принципиально возможно получение титанового шлака, пригодного для производства пигментного TiO2. Эти же месторождения обладают существенными запасами ванадия, получение которого также возможно.
Перспективны в РФ на титан древние морские россыпи, которые расположены на Русской плите (Лукояновское, Центральное), а также некоторые россыпи Сибири (Туганское, Тулунское месторождения). В целом по России возможно заметное расширение минерально-сырьевой базы титана за счет значительных прогнозных его ресурсов, которые превосходят запасы по категориям А+В+С1+С2 примерно в два раза (рис.1).
В качестве существенного потенциального сырья для титана выделяются довольно многочисленные месторождения титаномагнетита (табл. 2). Они приурочены к целому ряду магматических мафит-ультрамафитовых формаций. Встречаются указанные месторождения в европейской части РФ, на Урале, в Сибири. Среднее содержание TiO2 в титаномагнетитовом концентрате некоторых месторождений может достигать 15-20% (Пудожгорское и др.) Кроме того, титаномагнетитовые руды отдельных месторождений уже сейчас являются главным источником получения ванадия в России (Гусевогорское, Первоуральское месторождения). В перспективе из них возможно получение титана, скандия, марганца, галлия. Запасы титаномагнетитовых руд некоторых месторождений могут достигать нескольких миллиардов тонн. Их доля в запасах железа СНГ на 1990 г. составляла 7.7%, а добыча 8.3%. При плавке содержащейся в титаномагнетите титан переходит в шлак, откуда его извлечение возможно. Повышение комплексности использования титаномагнетита для РФ существенно, и содержащийся в нем титан может играть далеко не последнюю роль. Даже относительно невысокие по титанистости титаномагнетиты Гусевогорского месторождения (в среднем 3.3% TiO2) дают доменные шлаки, которые содержат 9.
4% TiO2.
Конверторный шлак, остающийся после передела ванадистого чугуна также характеризуется повышенной титанистостью. Возможно, что в будущем окажется целесообразным получение из конверторного шлака не только V2O5, но и диоксида титана, глинозема и марганца.
Перспективно производство титана, а также Al, TR, Nb из шлаков, которые образуются в результате плавки концентратов, полученных из перовскит-титаномагнетитовых руд (месторождение Африканда и др. Кольского п-ва). В этих шлаках содержится, % масс: 39.9-42.2 TiO2; 5.8-6.6 Al2O3; 1.6-2.1 TR2O3; 0.4 Nb2O5. Значительные масштабы перовскит-титаномагнетитовых руд позволяют рассчитывать на широкие возможности их комплексного использования.
Важным направлением в развитии производства титанового сырья является получение искусственного рутила из природных ильменитовых концентратов и титановых шлаков (рис. 2). В настоящее время в мире производится ~830 тыс.т синтетического рутила, богатого по содержанию TiO2 продукта, пригодного для производства пигментного диоксида титана хлорным методом.
Ценность титанового сырья в значительной степени (~50%) еще определяется присутствующими в нем редкими металлами. При хлорном методе переработки титановых концентратов редкие металлы накапливаются в хлоридных возгонах в таких количествах, существующими технологическими методами могут быть в качестве товарной продукции получены трехокись скандия, хромовый концентрат, железооксидные пигменты, соли марганца, коагулянты для очистки сточных вод и др. (рис. 3).
Таким образом, ресурсы титанового сырья в России значительные и в состоянии обеспечить потребности в титане на многие десятилетия. Однако в результате распада СССР Россия осталась как без освоенных месторождений, так и без ведущих перерабатывающих предприятий. Действующий Березниковский титано-магниевый комбинат в настоящее время не в состоянии обеспечить будущее развитие титановой промышленности РФ, потребности которой оцениваются в 300-675 тыс.т TiO2/год (Быховский, Зубков, 1996). Такие крупные месторождения, как Ярегское, Медведевское, Большой Сейим и др. не подготовлены к эксплуатации. При этом существуют значительные сложности и недоработки в технологии получения диоксида титана из их концентратов.
В этой связи развитие собственной титановой промышленности России (помимо наращивания запасов) должно определяться технологией комплексной переработки концентратов крупных титановых месторождений, расположенных в регионах с развитой инфраструктурой. Проблема комплексности решается в случае внедрения хлорной технологии, которая позволяет извлекать из сырья кроме титана, такие ценные металлы, как скандий, ванадий, хром, ниобий и др. и может быть практически безотходной и экологически чистой.
Журнал «Горная Промышленность» №4 1996, стр.23
Производство титана | Металлургический портал MetalSpace.ru
Для получения титана применяют магниетермический способ, который включает операции:
- получение титановых концентратов;
- производство титанового шлака;
- производство четыреххлористого титана;
- восстановление четыреххлористого титана магнием;
- вакуумная сепарация реакционной массы;
- плавка титановой губки в вакуумных печах.
Получение титановых концентратов
Титановые руды подвергают обогащению, в результате которого получают концентраты с повышенным содержанием TiO2 . Наиболее распространенным сырьем для получения титана является титано-магнетитановые руды, из которых выделяют ильменитовый концентрат, содержащий 40 – 45% TiO2, 30% FeO, 20% Fe2O3 и 5 – 7% пустой породы.
Производство титанового шлака
Основное назначение этого процесса – отделение оксидов железа от оксида титана. Для этого ильменитовый концентрат плавят в смеси с древесным углём и антрацитом в электропечах, где оксиды железа и часть титана восстанавливаются по реакции:
3(FeO·TiO2) + 4C = 3Fe + Ti3O5 + 4CO
Восстановленное железо науглероживается, образуя чугун, который собирается на дне ванны печи, отделяясь от остальной массы шлака вследствие различия их удельных весов. Чугун и шлак разливают отдельно в изложницы. Полученный титановый шлак содержит 80 – 90% TiO2.
Производство четырёххлористого титана
Для получения металлического титана используют хлорид титана, полученный путём хлорирования титанового шлака. Для этого титановый шлак измельчают, смешивают с углем и каменноугольным пеком, так как процесс хлорирования может проходить успешно только в присутствии восстановителя, и брикетируют при нагреве до 800 °С без доступа воздуха. Полученные брикеты подвергают хлорированию в специальных печах. В нижней части печи располагается угольная насадка, нагревающаяся при пропускании через неё электрического тока. В печь подают брикеты титанового шлака, а через фурмы – хлор.
При температуре 800 – 1250 °С в присутствии углерода образуются четыреххлористый титан по реакции:
TiO2 + 2C + 2Cl2 = TiCl4 + 2CO
В качестве побочных продуктов получаются также хлориды других металлов (FeCl2, MnCl2 , CrCl3 CaCl2 и др. ).
Благодаря различию температур кипения образующихся хлоридов, четыреххлористый титан отделяется и очищается от остальных хлоридов методом ректификации в специальных установках.
Восстановление четыреххлористого титана магнием
Восстановление осуществляется в специальных реакторах при температуре 950 – 1000 °С. В реактор загружают чушковый магний и после откачки воздуха и заполнения полоти реактора аргоном внутрь его подают парообразный четыреххлористый титан. Процесс восстановления титана идёт по реакции:
TiCl4 + 2Mg = Ti + 2MgCl2
Металлический титан оседает на стенках, образуя губчатую массу, а хлористый магний в виде расплава выпускают через лётку реактора. В результате восстановления образуется реакционная масса, представляющая собой губку титана, пропитанную магнием и хлористым магнием, содержание которых достигает 35 – 40%.
Вакуумная сепарация реакционной массы
Сепарацию проводят с целью отделения титановой губки от магния и хлористого магния. Процесс отделения состоит в том, что реакционную массу нагревают до 900 – 950 °С в герметичном устройстве электронагревательной печи, в котором создаётся вакуум. При этом часть хлористого магния удаляется в жидком виде, а остальная часть хлористого магния и магний испаряются. Титановая губка после очистки направляется на плавку.
Плавка титановой губки в вакуумнодуговых печах. Плавка губки методом вакуумно-дугового переплава является основным способом переработки её в слитки. Вакуум печи предохраняет титан от окисления и способствует очистке его от примесей. Полученные слитки титана переплавляют вторично для удаления дефектов, используя как расходуемые электроды. После этого чистота титана составляет 99,6 – 99,7%. После вторичного переплава слитки используют для обработки давлением (ковка, штамповка, прокатка).
ПОДЕЛИСЬ ИНТЕРЕСНОЙ ИНФОРМАЦИЕЙ
Мировой рынок диоксида титана
По материалам «Института исследования товародвижения и конъюнктуры оптового рынка» («ИТКОР»), 2004-2007 г.
Минеральными источниками для производства диоксида титана обычно служат титансодержащие руды: рутилы, ильмениты и люкоксены (в русской транскрипции — лейкоксены). Наиболее богатыми являются рутилы (rutile): в них содержится от 93 до 96% двуокиси титана (TiO2), в ильменитах (ilmenite) — от 44 до 70%, а концентраты люкоксенов (leucoxene) могут содержать до 90% TiO2.
Из всей добываемой титановой руды лишь 5% идет непосредственно на производство титана. Остальные 95% используются в производстве красок, пластмасс, каучука, бумаги и т. д. (Белый оксид титана обладает высокими преломляющими свойствами и рассеивающей способностью.)
В настоящее время в мире выявлено более 300 месторождений титановых минералов, в т. ч. магматических — 70, латеритных — 10, россыпных — более 230. Из них разведано по промышленным категориям 90 месторождений, преимущественно россыпных.
В коренных (магматических) месторождениях содержится около 69%, в корах выветривания карбонатитов — 11,5%, в россыпных месторождениях — 19,5% мировых (без России) запасов титана. Из них запасов в ильмените более 82%, в анатазе— менее 12%, в рутиле — 6%.
Ильменит-магнетитовые и ильменит-гематитовые руды коренных месторождений составляют основу минерально-сырьевой базы титановой промышленности Канады, Китая и Норвегии. Месторождения в корах выветривания карбонатитов известны и разрабатываются только в Бразилии. В остальных странах основные запасы титановых минералов заключены в россыпных, преимущественно комплексных месторождениях.
Наибольшее промышленное значение имеют современные и древние прибрежно-морские и сопровождающие их дюнные россыпи. Протяженность каждой россыпи невелика — от сотен метров до нескольких километров. Однако они часто образуют прослеживаемые на десятки и сотни километров серии россыпей, разделенных небольшими участками безрудных отложений. Такие серии россыпей заключают в себе большую часть запасов титанового сырья Австралии (на западном и восточном побережьях континента), Индии (западное и восточное побережья), США (Атлантическое побережье полуострова Флорида), ЮАР и Кении, значительную часть запасов Бразилии (побережье Атлантического океана).
Наиболее высококачественным сырьем для производства пигментного диоксида титана являются рутил и анатаз, содержащие соответственно 92–98% и 90–95% диоксида титана. В отличие от ильменита (43–53% TiO2) они не требуют предварительного обогащения путем передела в промежуточные продукты.
Мировые (без России) подтвержденные запасы диоксида титана составляют около 800 млн т. Основными источниками получения диоксида титана являются ильменитовый концентрат и природный рутил. Структура источников получения диоксида титана приведена на рисунке.
Как уже отмечалось выше, львиная доля — 90% — ежегодно добываемых титановых минералов используется для производства пигментного диоксида титана. Первоначально для этого использовали сульфатный процесс. Затем был разработан более экономичный и менее экологически опасный хлоридный способ.
Хлоридный метод позволяет решить проблему утилизации сульфата железа, однако выдвигает дополнительные требования к качеству титановых концентратов. В этом случае используются природный рутиловый концентрат, либо синтетический рутил, либо титановый шлак с содержанием TiO2 от 55 до 60% (для сульфатного способа — не менее 42% TiO2).
В 2001 г., по оценке американской компании IBMA, мировое потребление диоксида титана составило 4062 тыс. т. При этом на долю лакокрасочной промышленности приходилось 59%, производства пластмасс — 20%, ламинированной бумаги — 13%.
В ближайшие годы наиболее высокими темпами будет расти потребление диоксида титана в производстве ламинированной бумаги — на 4–6% в год, а также в производстве пластмасс — на 4% в год. Рост потребления диоксида титана в лакокрасочной промышленности будет менее быстрым — не более 1,8–2% в год.
Структура потребления диоксида титана, по оценкам европейских экспертов, такова. 58–62% произведенного в мире диоксида титана используется в лакокрасочной промышленности, где постепенно вытесняются из производства краски на основе цинка, бария и свинца. Среднее содержание TiO2 в красках составляет 25%.
Около 12–13% диоксида титана используется как пигмент при производстве бумажных изделий в виде рутила (высокосортная бумага) или анатаза (низкосортная бумага, картон). В среднем при изготовлении 1 т бумаги используется 1,4 кг TiO2.
На производство пластмасс расходуется около 18–22% диоксида титана. Незначительные количества химиката потребляются в производстве каучука, косметики и искусственных волокон.
Удельный вес США и стран Западной Европы в мировом потреблении диоксида титана составляет по 33%, Азии — около 25%.
Следует отметить, что в разных странах в одной и той же отрасли промышленности диоксид титана используется по-разному. В качестве примера возьмем Северную Америку и Западную Европу. Эти регионы — основные потребители диоксида титана в целлюлозно-бумажной промышленности.
В Северной Америке этот сектор рынка диоксида титана уже достаточно хорошо развит: до 96% всего объема титанового пигмента, потребляемого в целлюлозно-бумажной промышленности, расходуется в производстве печатной и писчей бумаги. И только около 4–6% идет на изготовление ламинированной бумаги.
В Западной Европе за последние 10 лет потребление диоксида титана в целлюлозно-бумажной промышленности выросло на 50%, причем темпы роста более чем в 2 раза превышали мировые. По оценке компании DuPont, до 90% диоксида титана, потребляемого бумажным производством, расходуется на изготовление ламинированной бумаги. Секторы рынка печатной и писчей бумаги, а также производство специальных сортов, например, обойной бумаги, развиты недостаточно.
По прогнозам экспертов, в Западной Европе потребление диоксида титана в целлюлозно-бумажной промышленности будет и дальше развиваться ускоренными темпами, в т. ч. в секторе неламинированных сортов бумаги, но не исключены временные спады.
В производстве неламинированных сортов бумаги диоксид титана будет постепенно вытеснять традиционный белый пигмент — каолин. Эта замена ведет к существенному улучшению таких качеств бумаги, как белизна, однородность поверхности, внешний вид. Снижение содержания пигмента — с 6% для каолина до 2% для диоксида титана —ведет к повышению прочностных свойств бумаги (на разрыв, растяжение и т. д.). Это позволит снизить расход упрочняющих волокон, что отразится на себестоимости конечной продукции. Кроме того, уменьшится толщина, но при этом сохранится непрозрачность бумаги.
По данным компании Millennium Inorganic Chemicals Inc., в 2000 г. спрос на диоксид титана на мировом рынке превысил все ожидания: мировое потребление этого продукта выросло примерно на 5,5–5,6%, в т. ч. в Северной Америке — на 3–3,5, странах Западной Европы — на 7–8, Азии — на 10–11%. В связи с высоким спросом на диоксид титана и закрытием некоторых производств в середине года на западноевропейском рынке ощущалась нехватка диоксида титана.
Согласно данным фирмы Articol, мировой спрос на диоксид титана в 2005 г. составил 4,5 млн т.
В настоящее время диоксид титана производится на 53 заводах в 26 странах мира. Загрузка мощностей на предприятиях–производителях в среднем составляет 92%, в т. ч. в США и Европе — 96%, в странах Азиатско-Тихоокеанского региона — 85–91%.
Крупнейшим продуцентом пигментного диоксида титана является компания E.I. du Pont de Nemours & Co. Inc. (DuPont). Компания владеет заводами в США (3 завода), Мексике и Тайване суммарной мощностью 1000 тыс. т/год, которые работают по хлоридной технологии.
Рассматривалась возможность строительства в Европе завода по выпуску диоксида титана мощностью 120–150 тыс. т/год, однако руководство компании пришло к выводу о неэкономичности такого строительства. По мнению DuPont, новые заводы целесообразнее строить в Китае.
Заводы компании Millennium Inorganic Chemicals Inc. расположены в США (2 завода), Великобритании, Франции (2 завода) и Австралии. В производстве используется как сульфатная (суммарная мощность 182 тыс. т/год), так и хлоридная технология (350 тыс. т/год).
В январе 1998 г. компания ввела в строй два новых завода с сульфатным процессом во Франции, затем закончила модернизацию завода с хлоридным процессом в г. Сталлингбараф (Великобритания), мощность которого увеличена с 109 до 150 тыс. т/год.
В настоящее время компания Millennium Chemicals рассматривает проект увеличения на 10–20% мощностей по производству сверхтонкого диоксида титана на своем заводе в г. Тан (Франция). Сравнительно недавно на этом предприятии завершилась реализация инвестиционной программы на сумму 11,6 млн евро. В результате удалось увеличить выпуск диоксида титана на этом заводе с первоначальных 3,4 до 10 тыс. т/год.
Капиталовложения осуществлялись в рамках стратегии наращивания выпуска дорогого и высокоприбыльного TiO2в форме наночастиц за счет сокращения производства обычных марок этого продукта (под сверхтонкими частицами следует понимать частицы размером от 1 до 150 нанометров). Появление нового проекта по наращиванию мощностей на заводе в Тане* объясняется исключительно большим спросом на сверхтонкий диоксид титана на мировом рынке.
Вице-президент компании Джек Вон Охлен заявил, что планируемые изменения на заводе в Тане сделают Millennium Chemicals компанией № 1 в производстве сверхтонкого диоксида титана. Ей будет принадлежать от 35 до 40% мирового рынка этого продукта. Общий объем продаж компании по данным 2005 года составляет 116 млн евро в год.
Компания Tioxide (дочерняя компания Huntsman Corp. ) владеет 6 заводами с сульфатной технологией (суммарная мощность — 456 тыс. т/год), расположенными в Великобритании, Испании, Италии, Малайзии и ЮАР, и одним заводом с хлоридной технологией (100 тыс. т/год) в Великобритании — в г. Грейтхем.
В IV квартале 2002 г., после увеличения мощности установки по производству диоксида титана в г. Уэльва (Испания) на 17 тыс. т/год, на рынки поступила дополнительная продукция компании Tioxide. (Инвестиции в реализацию этого проекта составили 40 млн долл.)
Компания Kronos Inc. (дочерняя компания NL Industries Inc.) владеет 4 заводами с сульфатной технологией в Германии, Канаде и Норвегии суммарной мощностью 24 тыс. т/год и 3 заводами с хлоридной технологией в Германии, Канаде и Бельгии суммарной мощностью 230 тыс. т/год.
Компания Kemira Pigments OY производит пигментный диоксид титана на трех заводах: в США, Финляндии и Нидерландах. В 1998 г. компания инвестировала 6 млн долл. в увеличение до 120 тыс. т/год мощности завода с сульфатной технологией в г.Пори (Финляндия), 20 млн долл. — в модернизацию производства на заводе в г.Саванна (штат Джорджия, США) и планирует строить третий блок на фабрике хлоридного производства диоксида титана в г. Роттердам (Нидерланды).
Компания Kerr-McGee эксплуатирует два своих предприятия в г.Гамильтон (США), которые работают по хлоридной технологии, а также пользуется производственными мощностями компании Bayer в Германии и Бельгии.
В 1999 г. завершилась работа по расширению мощностей завода в Гамильтоне, в результате которой они увеличились со 150 до 178 тыс. т/год.
Совместно с компанией TiWest компания эксплуатирует предприятие в г.Квиана (штат Западная Австралия) мощностью 83 тыс. т/год и совместно с компанией Cristal Pigment — завод в г.Янбо (Саудовская Аравия).
Kerr-McGee в середине 2001 г. завершила расширение мощностей (на 10%) предприятия в Австралии. Кроме того, компания проводит работы по снижению издержек производства на своих заводах, в первую очередь, на предприятиях в г. Ботлек (Нидерланды) и г. Саванна (США). Эти заводы она приобрела в 2000 г. у компании Kemira.
По данным японской Japanese Titanium Dioxide Industry Association, в 1998 г. в Японии было произведено 253 тыс. т диоксида титана. Крупнейшим продуцентом является Ishihara Sangya Kaisha Ltd., эксплуатирующая заводы в Японии и Сингапуре. Диоксид выпускают и другие японские компании, в т. ч. Tayca, Sakai Chemical, Furukawa, Fuji Titanium Titan Kogyo и Tohkem.
Компания Sachtleben Chemie, дочерняя структура Metallgesellschaft AG, эксплуатирует фабрику в г. Дуйсбург (Германия) и производит в основном анатазовую форму диоксида титана для синтетического стекловолокна, а также диоксид титана для пищевой и фармацевтической промышленности.
Польская компания Zaklady Chemiczne эксплуатирует единственное предприятие по производству рутилового пигментного диоксида титана по сульфатной технологии мощностью 36 тыс. т/год, используя норвежский ильменитовый концентрат и канадский титановый шлак.
Чешская компания Precheza AS эксплуатирует предприятие мощностью 27 тыс. т/год в г. Превов (Чехия), выпуская анатазовый диоксид титана.
В Словении имеется единственное предприятие по производству рутилового диоксида титана мощностью 34 тыс. т/год, принадлежащее компании Cinkarna Metalursko Kemicna Industrija Celje.
В Украине компания «Агрохим» в г. Сумы и «Крымский титан» в г. Армянск производят пигментный диоксид титана по сульфатной технологии на двух заводах мощностью 20 и 40 тыс. т/год соответственно.
Австрийская торговая компания ITA Privest GmbH профинансировала реконструкцию Крымского титаномагниевого комбината в г. Армянске для увеличения мощности предприятия. В результате к 2002 г. мощности комбината выросли до 80 тыс. т/год.
Структура производства диоксида титана крупнейшими компаниями мира |
Около 90% производимого в Украине диоксида титана поступает на экспорт. Основным импортером является Россия: она покупает примерно 60% всего украинского продукта.
В Республике Корея компания Hankook Titanium Industry Co. Ltd. эксплуатирует два предприятия по производству анатазового диоксида титана мощностью около 30 тыс. т/год в г. Каявадон и недавно открыла новую фабрику мощностью 20 тыс. т/год в г. Онсан.
В Индии компании Kerala Minerals и Metals Ltd. производят рутиловый диоксид титана по хлоридной технологии. Три другие компании — Travancore Titanium Products Ltd., Kolmak Chemicals Ltd. и Kilburn Chemicals Ltd. — производят анатазовый пигмент по сульфатной
технологии.
Суммарные мощности заводов Китая оцениваются в 130 тыс. т/год. Все предприятия работают по сульфатной технологии и перерабатывают местные ильменитовые концентраты.
Структура производства диоксида титана крупнейшими фирмами-производителями представлена на рисунке.
Страны — производители диоксида титана являются и его основными потребителями. В равной мере это относится и к США, и к Западной Европе в целом. Причем США заметно опережают все страны мира по душевому потреблению этого продукта, которое оценивается примерно в 3,5 кг. В Западной Европе этот показатель составляет около 2 кг.
На рисунке представлена структура потребления диоксида титана в мире, основанная на оценках компании IBMA.
Структура потребления диоксида титана в мире |
Немного подробнее о некоторых крупнейших фирмах — потребителях пигментного диоксида титана.
Крупнейший производитель пигментного диоксида титана компания DuPont одновременно является и его потребителем. Другие фирмы закупают диоксид титана на рынке.
DuPont является крупнейшим химическим концерном США и одним из 5 крупнейших в мире. В структуру компании входят пять производственных подразделений: химикаты, волокна, полимеры, нефть, другие производства. 175 производственных и перерабатывающих мощностей компании расположены
в 125 городах США и примерно в 70 странах Европы, Южной Америки и других частей света. На предприятиях компании DuPont занято более 100 тыс. человек.
Фирма ICI — крупнейшая химическая компания Великобритании. В сферу ее интересов входит почти весь мир. Три четверти продаж компании примерно равными долями распределяются между Великобританией, Центральной Европой и Америкой. Остальные продажи приходятся на Азиатско-Тихоокеанский регион.
Подразделение компании ICI — ее дочерняя компания Tioxide Group Ltd является производителем пигментов на основе диоксида титана и связанных с ними химических продуктов. Это второй крупнейший производитель пигментов на основе диоксида титана в мире и самый крупный в Европе.
Основные потребители титанового сырья |
Выпускаемые компанией пигменты на основе диоксида титана используются для получения самых разных продуктов, от которых требуется светонепроницаемость или
белизна. Основными потребителями пигментов являются предприятия по производству красок (основной потребитель), пластиков, бумаги и печатных паст.
Tioxide имеет производства в Великобритании, Франции, Италии, Испании, Канаде, Австралии и Малайзии.
Rhone-Poulenc — это многонациональная промышленная фирма, которая занимается исследовательской деятельностью, разработкой, производством, сбытом органических и неорганических полупродуктов, специализированных химических продуктов, волокон, полимеров, химикатов для фармацевтической промышленности и сельского хозяйства.
В структуру Rhone-Poulenc входят четыре подразделения: косметическая продукция, химическая продукция, волокна и полимеры, агрохимическая продукция. Штаб-квартира Rhone-Poulenc, а также центральные офисы подразделений химической продукции, волокон и полимеров расположены в г. Курбевуа (Франция). Штаб-квартира подразделения агрохимикатов находится в г. Лионе (Франция). Дочерняя североамериканская фирма Rhone-Poulenc Inc. находится в г. Принстоне (штат Нью-Джерси, США).
Представительства фирмы имеются в 50 странах на пяти континентах. Основные предприятия по производству химических полупродуктов и торговые офисы расположены в Европе и США, в меньшей степени — в Бразилии, Корее и Японии. Специализированные химические продукты выпускаются главным образом во Франции, Великобритании и США. Предприятия по производству волокон и полимеров работают преимущественно в Европе и Северной Америке. Часть продукции выпускается в Азии, где фирма пытается расширить
свое присутствие на местных рынках. Агрохимикаты производятся в Западной Европе, Северной Америке, Мексике, Южной Америке, Азии и Австралии.В фирме работает около 9000 человек.
Представительство корпорации действует в Москве, Киеве и в столицах других республик бывшего СССР.
Dow Chemical Company — одна из крупнейших химических компаний. Она имеет 94 предприятия в 30 странах, в т. ч. в США — 4, в Канаде и Германии – по 2, по одному — во Франции, Нидерландах, Испании и Бразилии. Принадлежащие ей заводы работают примерно на 92% от имеющихся мощностей.
Внимание компании направлено на индустриальные и индустриально развивающиеся страны. В ней работает около 40 тыс. служащих. Продукты, которые выпускает компания, реализуются на рынке в основном через ее торговые подразделения. На некоторых зарубежных рынках их продают дистрибьюторы.
Ведущим предприятием по производству красок на европейском рынке является Akzo Nobel. Штаб-квартира компании находится в Нидерландах, а производственные предприятия и коммерческие представительства — в 75 странах мира. Общий штат компании — 68 000 работников. Годовой оборот в 1999 г. составил 13 млрд долл. США.
Вся продукциякомпании сертифицирована по стандарту ISO 9000. Компания хорошо известна на российском рынке.
Sigma Coatings — один из крупнейших в Европе производителей красок и покрытий. Эта компания является составной частью Petrofina — объединенного международного нефтехимического концерна со штаб-квартирой в Брюсселе. Ее головной офис находится в г. Уитхорне, близ Амстердама (Нидерланды). В штате компании насчитывается около 4000 человек. Sigma специализируется на разработке, производстве и внедрении новых технологий нанесения красок и покрытий.
Широко известный в России концерн Tikkurila входит в десятку крупнейших производителей лакокрасочных материалов в Европе. Его продукция выпускается в 13 странах и продается практически по всему миру.
Вся продукция сертифицирована на соответствие международному стандарту качества ISO 9001 и имеет экологический сертификат Европейского сообщества.
Для правильного понимания тенденций на этом рынке необходимо учитывать следующее. Диоксид титан можно отнести к стандартизированной продукции, которая производится в условиях олигополии, поскольку на этом товарном рынке работает относительно малое число фирм–производителей. Доля четырех компаний — DuPont, Millennium, Kerr-McGee, Huntsman (Tioxide) — составляет более 65% от мирового производства этого продукта.
Спрос на диоксид титана подвержен периодическим подъемам и спадам, что связано с общемировой экономической конъюнктурой, однако в длительной перспективе прослеживается тенденция к его росту. Если в 1993–1996 гг. мировое потребление оценивалось в 2,9–3,3 млн т, в 2000 г. – 3,9 млн т, то в 2004 г. оно, по прогнозам, составит 4,5 млн т, а в 2005 г. — 5,1 млн т.
В настоящее время имеется небольшой резерв для наращивания производства диоксида титана, поскольку загрузка мощностей по его производству в мире составляет в среднем 92%.
Таким образом, можно прогнозировать увеличение объема мирового рынка диоксида титана в ближайшие 5–10 лет на 12–15% при ежегодном росте цен на этот продукт примерно на 5–7%.
Мировой рынок диоксида титана характеризуется стремительным развитием в первую очередь из-за возможности широкого употребления диоксида в различных промышленных сферах. В мире производится 85-90% диоксида титана рутильной модификации и 10-15% — анатазной. На европейском рынке в последние 2-3 года происходит стабильный рост цен. До этого на протяжении 20 лет цены имели тенденцию к снижению, что негативно отразилось на вводе новых производств.
Еще в начале 2007 года некоторые рудники для добычи титаносодержащего сырья в Западной Европе были закрыты, из-за чего увеличилась стоимость исходных материалов. Цены на диоксид титана в Европе колеблются от $2,1 за кг (украинское производство) до 4,5 $ (немецкий и финский диоксид титана). Отдельные производители начали внедрять политику повышения цен еще с 4 квартала 2007 года.
Рынок диоксида титана в Азии также расширяется в связи с экономическим развитием стран. Потребление диоксида возрастает, и пропорционально увеличиваются цены. Так, стоимость тонны диоксида превышает среднемировые цены практически на $50. Здесь расширяется производство, налаживаются тесные контакты, к примеру, между Россией и Индией, Китаем и КНДР.
Удельный вес США и стран Западной Европы в мировом потреблении диоксида титана составляет по 33%, Азии — около 25%. Наблюдается тенденция что страны, в которых потребление диоксида титана наименьшее в мире (Аргентина, Малайзия, Польша, Пакистан, Россия и пр.), в скором времени расширят внутренние рынки. Предполагаемый рост – от 4 до 9% ежегодно.
Титановые подводные лодки [Подводная Лодка — ПЛ]
В начале 1950-х годов военно-политические доктрины сверхдержав обосновывали создание двух основных систем: воздушно-космической для достижения превосходства в воздухе и космосе, а также морской, обеспечивающей ракетный щит. Предпосылкой для решения первой задачи стал прорыв в области создания материалов с высокой удельной прочностью для всех типов самолетов. Ведущим направлением в этой области была технология производства изделий из титановых сплавов.
Промышленное производство титана было налажено в Советском Союзе в начале 1950-х годов. В течение нескольких десятилетий Советский Союз использовал титан для производства нержавеющей стали, но только с 1952 года в советской прессе были опубликованы статьи об исследованиях в области разработки и использования металлического титана. СССР уделял большое внимание расширению производства титана из-за растущих потребностей и, в меньшей степени, из-за почти полного эмбарго на поставки титана из Свободного мира в коммунистические страны [страна с наибольшими известными запасами была Советский Союз].Советское производство губчатого титана увеличилось примерно на 70 процентов с 1958 по 1962 год, но в сентябре 1962 года советский журнал сообщил, что производство титана «все еще отстает от требований». Использование титана включает детали для производства самолетов и космических аппаратов, а также для производства коррозионно-стойкого оборудования, используемого в некоторых отраслях химической обработки.
В соответствии с планами развития народного хозяйства и научных работ в СССР с начала 1950-х гг. Проводились большие исследования в области металлургии титана, теории титановых сплавов; разработаны многие составы для титановых сплавов и технологические процессы для промышленности; велись работы по проектированию и созданию уникальных промышленных машин, установок, аппаратуры, а также испытания и серийные эксплуатационные испытания.Продемонстрирована технико-экономическая эффективность использования титана и его сплавов в ряде отраслей промышленности.
В течение нескольких лет производство титана было освоено в СССР, причем на более высоком уровне. На Украине, Урале и в Казахстане созданы производственные мощности по производству титановых концентратов и губчатого титана марок ТГ-1, ТГ-2. При этом советские специалисты, как правило, шли оригинальным путем. В Гиредмете (ныне ОАО «Гиредмет» ГНЦ РФ — ведущая научно-исследовательская и проектная организация по профилю материаловедения) и на Подольском химико-металлургическом заводе на Подольском химико-металлургическом заводе с его помощью были разработаны различные технологии производства слитков. ученых из ЦНИИ Прометея.К середине 1955 года специалисты пришли к окончательному выводу: плавить титан следует в дуговых печах, предложенных Прометеем. Затем эта технология была передана на Верхне-Салдинский металлообрабатывающий завод (ВСМОЗ) в городе Верхняя Салда на Урале.
В 1958 году началась коренная реструктуризация титановой промышленности страны. Соответствующее подразделение появилось в ЦНИИ химического машиностроения «Прометей» — сначала отдел №8, а затем отделы №1.18, 19. Коллектив выдающихся ученых создал научное направление морских титановых сплавов. Коллективы титано-магниевых заводов Запорожского (ЗТМК) и Березниковского (БТМК) совместно со специалистами Всесоюзного алюминиево-магниевого института (ВАМИ), Гиредмет и при активном участии ученых НИИ «КМ» Прометей »проделал большую работу по совершенствованию технологии изготовления губчатого титана. Отечественная промышленность могла производить большие слитки весом от четырех до шести тонн для подводных лодок.Это была большая победа. Решили проблему получения бездефектных слитков высокого качества.
Источников дефектов очень много — неправильный режим плавки, включения карбидов (карбиды вольфрама, окисленная губка, высокое содержание отходов в электродах и др.), Усадочная рыхлость и появление раковин. Все эти трудности в больших массах переложили на металлургов из «авиаторов». После реорганизации отрасли объемы производства, размер и вес слитков увеличились.Их масса достигала четырех и более тонн.
Эту огромную работу проделали многие научные и производственные коллективы научно-исследовательских институтов и заводов ряда министерств (цветная металлургия, авиационная и судостроительная промышленность, общее машиностроение, химическое и нефтяное машиностроение, химическая промышленность и другие). Институты Академии наук СССР творчески участвуют в исследованиях в области металлургии, металлургии, металлохимии титана, а также в разработке новых титановых сплавов, их испытаниях и внедрении в промышленность.
Директивами XXIII съезда Коммунистической партии Советского Союза в связи с пятилетним планом развития народного хозяйства СССР на 1966-1970 годы предусматривалось дополнительно резкое увеличение производства новых прогрессивных материалов и их материалов. широкое внедрение в хозяйство. Эти материалы включают титан.
Титан — Фон
В 1789 году, изучая химический состав магнитного песка из деревни Манаккан, английский ученый В.Грегор нашел новые земли, которые он назвал манакканитовой землей. В 1795 г. М. Клапрот обнаружил в минерале рутил неизвестный до сих пор металл и назвал его титаном; два года спустя он сам установил тождество рутила и манакканитовой земли. В 2910 году М. Хантер изготовил относительно чистый и пластичный титан. Еще в 1948 году титан все еще описывался как хрупкий металл, используемый в основном для легирования и диоксидирования сталей.
Руда химически восстанавливается до высокопористой хрупкой массы, известной как титановая губка. Для создания годного к употреблению металла губка должна быть сжата и обычно дважды плавится в электрической печи. Небольшое количество чистого скрапа и при желании легирующих элементов смешивают со спрессованной губкой перед процессом плавления. Полученный слиток можно использовать в процессе изготовления отливок, но по большей части он перерабатывается различными процессами прокатного стана в деформируемые формы, такие как заготовка, плита, лист, полоса, пруток, стержень, проволока, труба и трубы. Последующая обработка различных продуктов необходима для их окончательного использования.
Научно-технической основой широкого использования титана являются следующие свойства титана и особенно его сплавов: низкий удельный вес, высокая прочность, коррозионная стойкость во многих агрессивных средах, пригодность для промышленного производства, свариваемость, устойчивость к коррозии под нагрузкой, на концентрированный стресс и многие другие. Металлический титан и его сплавы являются желательными материалами для корпусов судов и других конструкций из-за их высокой прочности, легкого веса и коррозионной стойкости. Если бы они были построены из титана, корабли ВМФ имели бы меньший вес при тех же размерах, что позволяло бы иметь большую полезную нагрузку и практически без коррозии.
Но поскольку титан стоит до девяти раз больше, чем сталь, и его технически сложно и дорого производить для изготовления корпусов морских судов, судостроительная промышленность обычно его избегает. Для титана нужен совершенно другой производственный процесс; рабочие верфи должны пройти переподготовку; строительные залы необходимо перенастроить; гибка и формовка толстых листов из титанового сплава намного сложнее, чем из стали.С титаном оказалось очень сложно работать. Его чрезвычайная твердость вызвала проблемы при механической обработке и формовании материала. Сломались сверла и сломались инструменты, и пришлось изобретать новые. Титан также был очень чувствителен к загрязнителям, таким как хлор и кадмий.
американских просмотров
На Западе ЦРУ еще в 1971 году опубликовало анализ использования титана советской судостроительной промышленностью, который решительно поддержал оценку того, что в остальном консервативные Советы проводили серьезные, длительные исследования по формованию и сварке тяжелых титановых пластин и они фактически развили эту способность.
Другие западные аналитики были настроены скептически. Они думали, что формование и сварка тяжелых секций корпуса из титана, особенно в обычно грязной атмосфере верфи, было непрактичным, если не невозможным. Это тоже была вполне разумная оценка, потому что титан нельзя сваривать на воздухе; сварные швы должны быть защищены, обычно газообразным аргоном. Все пришли к единому мнению, что Советы могли сваривать небольшие детали из титана, например, для самолетов или ракет, в герметичных камерах, но невозможно было сваривать огромные секции герметичного корпуса подводных лодок.
В выпуске журнала American Metal Market от 27 января 1956 года на странице 3 была опубликована статья, озаглавленная «Советское производство титана может быть больше нашего». Далее в статье говорилось, что «правительственные чиновники заявили, что есть веские доказательства того, что российское производство титана может быть больше, чем наше, и на самом деле может достичь максимальной цифры от 90 000 до 95 000 тонн в год». ЦРУ через Оперативное управление запросило, кто такие правительственные чиновники, но безуспешно.В любом случае, учитывая, что США произвели только 7200 тонн металлического титана в 1955 году после вложений миллионов долларов в исследования и разработки и наличия доступа к большим объемам рутила, а также учитывая, что никаких доказательств применения металлического титана в СССР не поступало. Как выяснилось, ЦРУ сочло такое сообщение необоснованным.
Иногда политика отходит на второй план, даже когда речь идет об экспорте. Таким образом, поскольку Советский Союз нуждался во все большем количестве твердой валюты, казалось, что он счел целесообразным экспортировать продукты, которые обычно он предпочел бы хранить дома.Таким образом, Советский Союз экспортировал титановую губку, хотя титан имеет очень важное стратегическое значение. По иронии судьбы Соединенные Штаты запретили продажу титана Советскому Союзу, хотя они продавали его США. В некотором смысле необходимость Советского Союза зарабатывать твердую валюту, которая становится возможной благодаря продаже таких стратегических предметов, предполагает, что временами Советы были готовы продать нам веревку, которая когда-нибудь может быть использована для их подвешивания.
Американский импорт из СССР начался в 1965 году.В период 1965-1966 гг. Такой импорт составлял 2% от всего импорта губки. В 1967 году они составляли 19 процентов всего такого импорта, и были предприняты попытки продавать 10 миллионов фунтов стерлингов в год, что равнялось бы 68 процентам всего импорта губки в 1967 году, или почти четверть объема губки, потребляемой в Соединенных Штатах. в 1967 г.
23 апреля 1968 года Тарифная комиссия получила уведомление от Министерства финансов о том, что титановая губка из СССР продавалась или могла быть продана в Соединенных Штатах по цене ниже справедливой по смыслу Антидемпингового закона 1921 года. с изменениями, внесенными.Соответственно, 24 апреля 1968 года Комиссия возбудила расследование № AA1921-51 в соответствии с разделом 201 (a) этого Закона, чтобы определить, является ли отрасль в Соединенных Штатах или может быть повреждена, или препятствует ее созданию. по причине ввоза таких товаров в Соединенные Штаты. На основании расследования Комиссия определила, что промышленность в Соединенных Штатах страдает от импорта губчатого титана из США. С.С.Р.
28 августа 1968 года Министерство финансов опубликовало антидемпинговые заключения по титановой губке из Союза Советских Социалистических Республик (СССР) (33 FR 12138). В декабре 1991 года СССР разделился на пятнадцать независимых государств. Чтобы соответствовать этим изменениям, Департамент изменил первоначальный антидемпинговый вывод на пятнадцать выводов, применимых к странам Балтии и бывшим республикам СССР (57 FR 36070, 12 августа 1992 г.).
В 1995 году Министерство торговли провело административную проверку антидемпингового заключения по титановой губке из России.В обзоре участвовали четыре производителя / экспортера: ВИЛС — Всесоюзный институт легких сплавов (ВИЛС), Верхнесалдинское металлургическое производственное объединение (ВСМПО), В / О Техснабэкспорт (Техснабэкспорт), Березниковский титано-магниевый завод (АВИСМА) и экспорт. рассматриваемых товаров в США в период с 1 августа 1992 г. по 31 июля 1993 г. Департамент предварительно установил, что респонденты не экспортировали титановую губку в США в течение периода проверки.
Титановая скульптура
Единственная сохранившаяся титановая скульптура в мире — это хорошо известная скульптура 42.Памятник первому космонавту Юрию Гагарину высотой 5 метров в Москве. 12 апреля 1961 года Юрий Гагарин начал свое эпическое космическое путешествие на космическом корабле «Восток-1». Гагарин, погибший в авиакатастрофе 1968 года, отмечен рядом памятников, скульптур, бюстов и обелисков. Памятник его достижению, расположенный на площади Гагарина в Москве (до 1968 года площадь Калужская застава), был открыт 4 июля 1980 года, когда в Москве проходили Олимпийские игры. Памятник создан скульптором П.И. Бондаренко, архитекторы Я.Б. Белопольский, Ф. Гажевский, конструктор — А.Ф. Судаков. Памятник Гагарину отличается вдохновляющим дизайном: Гагарин в его скафандре с частично поднятыми руками, как будто он собирался прыгнуть в небо. Один из самых высоких памятников Москвы, памятник находится именно в том месте, откуда его следует видеть даже с МКАД.
В Свердловской области находится крупнейший в мире производитель титана — металла, широко используемого в авиационной и других отраслях промышленности. Зона Титановой долины была создана для привлечения российских и международных промышленных групп, заинтересованных в доступе к уникальным промышленным ресурсам, а также готовых инвестировать в российскую экономику. Особая экономическая зона «Титановая долина» — это поддерживаемый российским правительством проект, направленный на привлечение крупных международных промышленных групп путем предоставления им налоговых льгот и доступа к российским горнодобывающим, перерабатывающим и производственным предприятиям.
НОВОСТИ ПИСЬМО |
Присоединяйтесь к GlobalSecurity.список рассылки org |
Титан
Твердый серебристо-серый металл, титан встречается в природе как соединение во многих минералах, но в первую очередь в ильмените (FeTiO3) и рутиле (TiO2), которые чаще встречаются в песке или почве, чем в твердых породах. Другие титансодержащие минералы включают перовскит, титанит, анатаз и брукит. Основные месторождения титановых минералов находятся в Австралии, Канаде, Индии, Норвегии, Южной Африке, Украине и США.
Титан особенно ценится за его низкую плотность в сочетании с высокой прочностью и отличной коррозионной стойкостью. Чистый титан может достигать предела прочности на разрыв до 740 Н / кв. Мм, а сплав, подобный LT 33, содержащий алюминий, ванадий и олово, достигает 1200 Н / кв. Мм. Коэффициент теплового расширения металла примерно вдвое меньше, чем у нержавеющей стали и меди, и на одну треть меньше, чем у алюминия. Его плотность составляет около 60% от плотности стали, вдвое меньше плотности меди и в 1,7 раза больше плотности алюминия.Его модуль упругости вдвое меньше, чем у нержавеющей стали, что делает его прочным и ударопрочным.
Авиакосмическая промышленность по-прежнему является крупнейшим потребителем металла. Титановые сплавы, способные работать при температурах от минусовой до 600 ° C, используются в авиационных двигателях для изготовления дисков, лопастей, валов и кожухов. Высокопрочные сплавы используются в самых разнообразных конструкциях планеров — от небольших крепежных элементов весом несколько граммов до шасси шасси и больших балок крыла весом до 1 тонны.На титан может приходиться 10% разгруженного веса некоторых коммерческих пассажирских самолетов.
Большая часть титана фактически потребляется в форме диоксида титана — нетоксичного белого пигмента, используемого в красках, бумаге, пластике и косметике.
Происхождение
Хотя о существовании минералов титана известно уже более 200 лет, коммерческое производство металлического титана и пигмента на основе диоксида титана началось только в 1940-х годах. W.J. Kroli запатентовал метод получения металлического титана путем карбохлорирования диоксида титана в 1938 году.Первоначально элемент был назван в честь титанов из греческой мифологии немецким химиком М. Клапрот, который в конце восемнадцатого века успешно отделил диоксид титана от рутила.
По оценкам Геологической службы США (USGS), мировая добыча ильменита в 2004 году составила 4,8 миллиона тонн, в то время как мировая добыча рутила составила 400 000 тонн. Ильменит обеспечивает около 90% мировой потребности в минералах титана. По оценкам Геологической службы США, мировые ресурсы анатаза, рутила и ильменита составляют более 2 млрд тонн.
Производство
Первым шагом на пути к производству металлического титана обычно является производство губки путем хлорирования рутиловой руды (см. Технологическую схему). Хлор и кокс объединяются с рутилом с образованием тетрахлорида титана, который затем реагирует с магнием в замкнутой системе с образованием губчатого титана и хлорида магния. Магний и хлорид магния удаляются для повторного использования с использованием процесса вакуумной перегонки или процесса выщелачивания Кролла. США, Россия, Казахстан, Украина, Япония и Китай являются крупными производителями губчатого титана.
Вакуумно-дуговая восстановительная печь (VAR) или электронно-лучевая печь с холодным подом используется для плавления губки с ломом и / или легирующими элементами, такими как ванадий, алюминий, молибден, олово и цирконий, для производства переплавленных электродов, которые можно плавить с помощью VAR. для производства строгих спецификаций для аэрокосмической и других высокотехнологичных областей или непосредственно отливки в плиты.
Слитки VAR имеют цилиндрическую форму и могут весить до 17 500 фунтов (7,94 тонны). Их выковывают для изготовления слябов или заготовок или используют для литья по выплавляемым моделям.Вращение производит лист, лист, пруток, пруток и проволоку. Труба и труба формируются из полосы, вырезанной из листа.
Области применения
В повседневной жизни титан чаще всего ассоциируется с такими дорогостоящими продуктами, как наручные часы, оправы для очков, спортивные товары и ювелирные изделия, но, помимо его широкого использования в самолетах, он имеет много других применений, в которых сочетаются его физические свойства. а биосовместимость превосходит другие материалы. В зависимости от конкретной области применения титан может конкурировать с никелем, нержавеющей сталью и сплавами циркония.
Автомобильный сектор демонстрирует многообещающие признаки роста. Например, в системах подвески замена стальных рессор на титановые дает преимущество в весе на 60%. Другие области применения включают коленчатые валы, шатуны и выхлопные системы. Электростанции и установки по опреснению морской воды также продолжают оставаться важными областями роста для металла, в то время как для компьютеров титановые подложки для жестких дисков находятся в стадии разработки.
Boeing расширяет возможности обработки титана в России
U.В марте механические мастерские и другие производители заказали новое капитальное оборудование на сумму 404,6 миллиона долларов, что на 11,7% меньше, чем в марте, но все же на 72,3% больше, чем в апреле 2020 года. «В апреле 2020 года было самое низкое количество заказов за десятилетие, но предыдущие три месяца были обычным делом, поэтому рост на 40% по сравнению с предыдущим годом показывает реальную силу отрасли в 2021 году», — прокомментировал Дуглас К. Вудс, президент АМТ — Ассн. для производственных технологий.
AMT предоставила данные в ежемесячном U.S. Отчет о заказах на производственные технологии. Отчет USMTO представляет собой прогнозный индекс производственной активности, отслеживающий капитальные вложения производителей в ожидании будущих заказов на работу. Он включает в себя фактические данные о новых заказах металлорежущего и металлообрабатывающего оборудования по всей стране и в шести географических секторах на основе информации, предоставленной участвующими производителями и дистрибьюторами этого оборудования.
На текущий год с начала года общая сумма заказов USMTO составляет 1 доллар США.57 млрд, что на 40,1% больше, чем за январь-апрель 2020 года, отметил президент АМТ.
«Детали, которые обычно идут в мастерские, теперь производятся на месте более крупными производителями, чтобы увеличить свои производственные мощности», — заметил Вудс. «Это не означает, что производство уходит от мастерских; они по-прежнему работают почти на полную мощность и ежемесячно увеличивают заказы на оборудование, но возросший потребительский спрос потребовал увеличения мощности, и уверенность в устойчивости этого спроса оправдала капитальные вложения крупных OEM-производителей. В результате наши участники стали свидетелями возрождения заказов на несколько станков вблизи уровней 2018 года. Новые заказы производителей на капитальное оборудование в апреле составили 404,6 млн долларов, что на 11,7% меньше, чем в марте, но на 72,3% больше, чем в апреле 2020 года, на что негативно повлиял простой бизнес в связи с пандемией. Отчет о заказах на производственные технологии в США показывает, что в январе-апреле 2021 года спрос на станки составил 1,57 миллиарда долларов, что на 40,1% выше, чем за аналогичный период 2020 года.по производственным технологиям
Вудс описал несколько положительных факторов, способствующих спросу на металлорежущее и формовочное оборудование, включая изменения конструкции автомобилей для изготовления пресс-форм; новые усилия по разведке энергоресурсов и горнодобывающая деятельность; и высокий спрос на потребительские товары.
«Однако из-за ограничений предложения новые заказы добавляются к уже растущему портфелю заказов», — сказал он. «Спрос на производственные технологии есть, и поставщики, которые могут выполнять заказы, в ближайшем будущем смогут обойти своих конкурентов.
Что касается уменьшения объема заказов с марта по апрель, только в одном из шести регионов отмечен рост новых заказов: в Южно-Центральном регионе производители заказали новое металлорежущее оборудование на сумму 33,35 миллиона долларов, что на 9,9% больше, чем в период. В марте и на 80,3% больше, чем в апреле 2020 года. За текущий год с начала года объем заказов Южно-Центрального региона составил 110,8 млн долларов, что на 34,0% больше, чем объем заказов за январь-апрель 2020 года.
Спрос на новые металлорежущие станки упал до 74 долларов.0 млн в Северо-восточном регионе, или -8,3% с марта, что на 20,8% больше, чем в апреле 2020 года. На Юго-Востоке новые заказы на металлорежущее оборудование упали на -10,1% с марта до 42,75 млн долларов, что на 17,0% больше, чем в апреле 2020 года. результат.
В Северо-Центрально-Восточном регионе новые заказы на металлорежущие станки в апреле составили 100,99 млн долларов, хотя этот показатель на 13,1% ниже результата марта и на 199,5% больше показателя апреля 2020 года. Новые заказы на металлорежущее оборудование в Северо-Центрально-Западном регионе упали -9.0% в апреле до 81,65 миллиона долларов, но это на 134,4% больше, чем в апреле 2020 года.
В Западном регионе новые заказы на металлорежущие станки составили 66,31 млн долларов, что на 13,6% больше, чем в марте, и на 53,3% больше, чем в апреле 2020 года.
Титан играет жизненно важную роль для Boeing и России
ВЕРХНАЯ САЛДА, Россия — Boeing нужно сделать свои авиалайнеры легче, а для этого ему нужен титан. И за этим легким и прочным металлом американский авиастроитель приезжает в этот небольшой город на Урале.
На титановом заводе в Ависме, некогда секретном заводе, который производил детали для ядерных ракет во время холодной войны, титановые нервюры для самолетов Boeing сложены штабелями, как бревна. В приложении совместное предприятие Boeing и Avisma под названием Ural Boeing Manufacturing производит шлифовку кованых деталей, предназначенных для Америки. Треть всех узлов реактивного шасси Boeing производится с использованием титановых балок из России.
Русские производят титановые детали, которые невидимы, но не менее важны для таких самолетов, как новый 787 Dreamliner и обычный пригородный самолет 737.
Boeing покупает у России так много титана (производитель самолетов планирует закупки на 18 миллиардов долларов в ближайшие десятилетия), что теперь он исследует новые сплавы вместе с русскими. В Москве, в тысяче миль к западу, группа из 1400 аэрокосмических инженеров проектирует планеры и крылья, частично используя российские титановые компоненты.
Рост титана — яркое пятно для находящейся в затруднительном положении аэрокосмической отрасли России. Это как приветствие для Боинга. С новым самолетом Dreamliner компания Boeing сделала рывок к новым технологиям и расширила глобальную сеть поставщиков.Эта стратегия резко пошла по пути с новой литий-ионной батареей, сделанной в Японии. Опасность возгорания батарей вынудила Boeing на месяцы заземлить весь флот.
Но российская титановая стратегия приносит свои плоды. Опора на российский титан, которая связана с геополитическими рисками, учитывая напряженность в отношениях между США и Россией, делает легкий металл более экономичным, поэтому Boeing использует больше. Уменьшение веса самолетов делает их более экономичными в эксплуатации и, следовательно, более привлекательными для авиакомпаний.Завод «Ависма», расположенный глубоко в сосновом лесу, производит 35 процентов всего титана для гражданских самолетов Boeing.
«Есть детали, которые производим только мы. Больше никого », — сказал директор завода, совладелец завода Михаил Васильевич Воеводин.
Титановые детали чертовски сложно сделать. В кузнице литейного цеха гигантские круглые печи возвышаются вдоль стен главного плавильного цеха, как трубы какого-то вулканического органа в адском соборе высотой в шесть этажей. Электричество плавит металл в этих вакуумных трубках.
Гигантские стойки, столбы и листы нагреваются до красного цвета и погружаются в водяную баню, где по ним ударяют гидравлическими молотами весом пять тонн. Они выходят на удивление сильными.
«Россия является важным партнером для 787 титановых деталей», — сказал Сергей Кравченко, директор представительства Boeing в России, в письменном ответе на вопросы. «Завод имеет самый большой в мире пресс для штамповки титана, и Boeing в полной мере использует эту уникальную возможность», — написал он.
Русские начали использовать титан на Востоке, космической капсуле Юрия Гагарина, в которую летал в 1961 году. К 1970-м годам советские генералы стали довольными. Началась секретная программа, требующая невероятных ресурсов. В дополнение к самолетам Советы будут делать подводные лодки из титана.
По данным музея на заводе, полдюжины ударных подводных лодок классов «Альфа», «Майк» и «Папа» имели корпуса, на 30% состоящие из титана. На каждую требовалось более 2000 тонн металла.Легкие и мощные подводные лодки, называемые «золотой рыбкой», могли двигаться под водой со скоростью 44 узла или 50 миль в час.
Ежедневный бизнес-брифинг
Эта история позволила Boeing быть уверенным в стабильных поставках в Россию. Помимо России и других бывших советских республик, только четыре страны производят его в промышленных объемах: США, Германия, Япония и Китай.
Опыт «холодной войны» дал «Ависме» поразительные знания и способности.Когда-то он производил 90 000 тонн в год — больше, чем весь остальной мир вместе взятый в 1970-х годах. Сейчас завод производит около 32 тысяч тонн, правда более высокого сорта. В целом Avisma производит 45 процентов мирового аэрокосмического титана.
Сотрудничество между Boeing и россиянами стало более тесным после 2007 года, когда российские технологии, государственный конгломерат, захватили литейный завод. «Ростехнологии» стремились возродить российскую военную промышленность, находя гражданских покупателей на продукцию двойного назначения.Он стремился продать свою продукцию Boeing, а также Airbus, главному конкуренту Boeing. Завод также поставляет Embraer, Bombardier и производителей двигателей.
Для Boeing альянс с российской аэрокосмической промышленностью выходит за рамки закупок титана. При поддержке правительства Соединенных Штатов, обеспокоенного тем, что безработные российские аэрокосмические и ракетные инженеры работают на государства-изгои, Boeing в 1990-х годах открыл конструкторский центр в Москве. В этом центре работают инженеры, находящиеся в краткосрочном отпуске из российских компаний «Ильюшин», «Сухой» и «Хруничева», производителя космических капсул и спутников.
Большая часть стоимости создается при плавке сплавов. Чистый титан стоит около 7 долларов за фунт. Однако, смешанный с цирконием, никелем и другими сплавами для деталей авиакосмической промышленности, он может стоить более 150 долларов за фунт. У Московского техцентра есть три патента на такие сплавы.
Ависма — редкий прибыльный российский производитель. В прошлом году «Ростехнологии» продали управляющим контрольный пакет акций; Акции Avisma торгуются на российской фондовой бирже Micex. Его рыночная капитализация составляет около 2 миллиардов долларов.
Ависма до сих пор работает на российских военных. На складе ракет и деталей самолетов огромные титановые кольца корпуса для ракеты «Булова», новейшей межконтинентальной баллистической ракеты России, сложены большой неровной кучей, как порция луковых колец на конец света. (Большинство потребительских товаров из титана, таких как клюшки для гольфа и альпинистские ледорубы, производятся в Китае из более дешевого нелегированного металла.)
Три года назад Avisma начала производство медицинского титана для имплантатов, которое быстро расширилось и охватило около четверть этого специализированного рынка во всем мире.
Для завода все равно, — сказал директор Воеводин. Тот же процесс создает штампованные детали. Единственная разница в том, что как только он выходит из этой гигантской русской кузницы в горах, «он входит в человека, а не в самолет».
Россия создаст «Титановую долину»
ВЕРХНАЯ САЛДА, Россия (Рейтер) — Россия создаст экономическую зону Титановой долины вокруг крупнейшего в мире производителя ВСМПО-АвисмаВСМО.РТС, чтобы привлечь иностранные компании, заявил премьер-министр Владимир Путин. в четверг.
Премьер-министр России Владимир Путин (справа) посетил титановый завод ВСМПО-Ависма в городе Верхняя Салда на Урале, 18 ноября 2010 г. REUTERS / Алексей Другинын / РИА Новости / Pool
Путин во время поездки на Урал В горах, где находится компания, сказал, что через две недели он подпишет указ о создании зоны, которая будет включать в себя не менее 40 миллиардов рублей (1,29 миллиарда долларов) инвестиций.
ВСМПО-Ависма мало известна за пределами России, несмотря на то, что она является ключевым поставщиком как для Boeing, так и для EADS.
Он производит 25 процентов мирового титана, высокопрочного металла, используемого в аэрокосмической и оборонной промышленности, а также в клюшках для гольфа, медицинском оборудовании и ядерной энергии.
Титановая долина является частью стремления к ускорению экономического роста и созданию рабочих мест с упором на природные ресурсы, основной экспорт России.
«Это даст предприятиям возможность разрабатывать и производить продукцию с добавленной стоимостью, а также привлекать сюда наших партнеров», — сказал Путин на основном заводе «ВСМПО-Ависма» в Верхней Салде, примерно в 1700 км к востоку от российской столицы.
Глава Ростехнологий Сергей Чемезов сообщил, что авиакосмическая компания Rolls Royce and Goodrich может открыть производство в Титановой долине. Государственной технологической компании принадлежит более 70 процентов ВСМПО-Ависма.
Схема, которая рассчитывает создать 20 000 рабочих мест в городе, отражает широко разрекламированный российский центр «Сколково», где Кремль надеется разместить местные технологические компании в центре, созданном по образцу Силиконовой долины в Калифорнии.
Ряд лидеров отрасли, в том числе финская Nokia, уже присоединились к нам.
КЛЮЧЕВЫЙ ЗАКАЗЧИК BOEING
Путин посетил завод «ВСМПО-Ависма» и похвалил руководство за инвестиции в производство.
«Я посмотрел, как работает предприятие — оно стабильно, много денег вкладывается в модернизацию», — сказал Путин, добавив, что в течение следующих трех лет будет инвестировано 700 миллионов долларов.
ВСМПО-Ависма, не имеющая листинга на международной фондовой бирже, сообщила, что 70 процентов ее авиационного титана продается Boeing, а остальное покупает Airbus EADS.
Американская аэрокосмическая компания уже имеет значительное присутствие в Верхней Салде через совместное предприятие Ural Boeing Manufacturing (UBM), созданное в 2009 году. Путин также посетил этот завод.
Современное предприятие производит титановые поковки для проблемного самолета Boeing 787 Dreamliner, а также самолетов 777 и 737.
Когда UBM открылся в прошлом году, Boeing заявила, что планирует потратить до 27 миллиардов долларов на российский титан в течение следующих трех десятилетий.
В августе ВСМПО-Ависма заявила, что ожидает, что выручка за 2010 год превысит ранее запланированный план в 976 миллионов долларов.
В январе-октябре было произведено 24 400 тонн губчатого титана, что на 7 процентов больше, чем в прошлом году.
Русский титан
Ситуация с титаном парадоксальна. С одной стороны, титан в изобилии встречается в естественной среде обитания: с точки зрения естественного присутствия в земной коре этот элемент является третьим среди всех металлов, сразу после железа и алюминия. В промышленности, особенно в металлургии, он используется очень редко, примерно в сто раз меньше алюминия.
Это происходит, несмотря на выдающиеся свойства титана: он легкий, быстрый, термостойкий и химически устойчивый. Но это слишком дорого, так как добыть его из полезных ископаемых очень сложно, а сырье для его производства чрезвычайно дорого.
Дело дошло до закупки диоксида титана за границей. Его используют в качестве основы для титанового белила, а также для производства пластмасс, бумаги и даже косметики.В России достаточно месторождений; Проблема в том, что в России до сих пор не удалось наладить производство качественного титана-сырца.
Этот камень преткновения, вероятно, скоро будет устранен с помощью технологии, разработанной в Институте металлургии и материаловедения им. А.А. Байкова РАН, в лаборатории профессора Резниченко Г.Б. Садыхов, доктор технических наук.
Минерал рутил встречается в природе, в основном состоит из диоксида титана.Исследователи предлагают выделять рутил из так называемых лейкоксеновых нефтеносных песчаников Ярегского месторождения, которые ранее считались абсолютно бесперспективными для получения диоксида титана.
Способ производства следующий: сначала необходимо избавиться от минерального масла, которым пропитан песчаник. Это минеральное масло было получено из ярегского песчаника путем нагревания без воздуха. Затем песчаник снова нагревают; это меняет его структуру.Песчаник изначально более чем наполовину состоит из обычного песка, то есть диоксида кремния — кварца. Последний распределен неравномерно: есть крупные агломераты, а некоторые агломераты как бы врастают в структуру рутила, от них сложнее всего избавиться. В результате термической обработки структура диоксида кремния изменяется, и он становится намного активнее.
Как ни странно, рутил приобретает ферромагнитные свойства и начинает притягиваться к магниту. Исследователи пока точно не знают причину этого, пока есть только гипотеза, что это связано с незначительными добавками железа.Выяснение причин этого явления — предмет дальнейших исследований. Однако явление устойчиво подтверждено экспериментально и позволяет отделить рутил от кварца. Что касается диоксида кремния, остающегося с рутилом в виде тонкого сгустка, то его гораздо легче удалить — он вымывается из рутила раствором щелочи.
В результате исследователям удается (пока только в лабораторных условиях) выделить из руды практически весь диоксид титана, то есть от 90 до 95 процентов исходного содержания, и такой синтетический рутил оказывается практически чистым: он содержит более 90 процентов диоксида титана и менее трех процентов диоксида кремния.Получать из такого рутила титановый белила одно удовольствие.
Источник: Информнаука.
Откажитесь от звуковой панели с новыми динамиками Amazon Echo
Ссылка : Русский Титан (29 июля 2005 г.) получено 15 июня 2021 г. с https: // физ.org / news / 2005-07-russian-titanium.html
Этот документ защищен авторским правом. За исключением честных сделок с целью частного изучения или исследования, никакие часть может быть воспроизведена без письменного разрешения. Контент предоставляется только в информационных целях.
обработка титана | Технологии, методы и факты
Обработка титана , извлечение титана из его руд и подготовка титановых сплавов или соединений для использования в различных продуктах.
Титан (Ti) — мягкий, пластичный серебристо-серый металл с температурой плавления 1675 ° C (3047 ° F). Благодаря образованию на его поверхности оксидной пленки, которая является относительно инертной химически, он имеет превосходную коррозионную стойкость в большинстве природных сред. Кроме того, он легкий и по плотности (4,51 г на кубический сантиметр) находится где-то посередине между алюминием и железом. Сочетание низкой плотности и высокой прочности обеспечивает наиболее эффективное соотношение прочности к массе среди обычных металлов при температурах до 600 ° C (1100 ° F).
металлический титанМеталлический титан высокой чистоты (99,999%).
Alexander C. WimmerПоскольку его атомный диаметр подобен диаметру многих обычных металлов, таких как алюминий, железо, олово и ванадий, титан можно легко легировать для улучшения его свойств. Как и железо, металл может существовать в двух кристаллических формах: гексагональной плотноупакованной (ГПУ) при температуре ниже 883 ° C (1621 ° F) и объемно-центрированной кубической (ОЦК) при более высоких температурах вплоть до точки плавления. Такое аллотропное поведение и способность легироваться со многими элементами приводят к получению титановых сплавов, которые обладают широким диапазоном механических и коррозионно-стойких свойств.
Хотя титановые руды широко распространены, высокая реакционная способность металла с кислородом, азотом и водородом в воздухе при повышенных температурах требует сложных и, следовательно, дорогостоящих процессов производства и изготовления.
Получите подписку Britannica Premium и получите доступ к эксклюзивному контенту. Подпишитесь сейчасИстория
Титановая руда была впервые обнаружена в 1791 году на песчаных пляжах Корнуолла английским священником Уильямом Грегором. Фактическая идентификация оксида была сделана несколько лет спустя немецким химиком М.Х. Клапрот. Клапрот дал металлической составляющей этого оксида название титан в честь титанов, гигантов греческой мифологии.
Чистый металлический титан был впервые произведен в 1906 или 1910 году М.А. Хантером в Политехническом институте Ренсселера (Трой, Нью-Йорк, США) в сотрудничестве с General Electric Company. Эти исследователи полагали, что титан имел температуру плавления 6000 ° C (10800 ° F) и, следовательно, был кандидатом для нити накаливания, но, когда Хантер произвел металл с температурой плавления, близкой к 1800 ° C (3300 ° F), усилия были прекращены.Тем не менее, Хантер указал, что металл обладает некоторой пластичностью, и его метод получения его путем взаимодействия тетрахлорида титана (TiCl 4 ) с натрием в вакууме был позже коммерциализирован и теперь известен как процесс Хантера. Металл значительной пластичности был получен в 1925 году голландскими учеными А.Э. ван Аркелем и Дж. де Бур, который диссоциировал тетраиодид титана на горячей нити накала в вакуумированной стеклянной колбе.
В 1932 году Уильям Дж. Кролл из Люксембурга произвел значительное количество пластичного титана, объединив TiCl 4 с кальцием.К 1938 году Кролл произвел 20 килограммов (50 фунтов) титана и был убежден, что он обладает превосходными коррозионными и прочностными свойствами. В начале Второй мировой войны он бежал из Европы и продолжил свою работу в Соединенных Штатах в Union Carbide Company, а затем в Горном бюро США. К этому времени он сменил восстановитель с кальция на металлический магний. Kroll теперь признан отцом современной титановой промышленности, а процесс Kroll является основой для большинства современных производств титана.
Исследование ВВС США, проведенное в 1946 году, показало, что сплавы на основе титана были конструкционными материалами, имеющими потенциально большое значение, поскольку возникающая потребность в более высоких отношениях прочности к весу в конструкциях и двигателях реактивных самолетов не могла быть эффективно удовлетворена ни сталью, ни алюминий. В результате Министерство обороны предоставило производственные стимулы для запуска титановой промышленности в 1950 году. Аналогичные производственные мощности были созданы в Японии, СССР и Великобритании.После того, как аэрокосмическая промышленность дала этот импульс, доступность металла открыла возможности для новых применений на других рынках, таких как химическая обработка, медицина, производство электроэнергии и обработка отходов.
Титан — четвертый по распространенности структурный металл на Земле, уступая только алюминию, железу и магнию. Обрабатываемые месторождения полезных ископаемых разбросаны по всему миру и включают участки в Австралии, США, Канаде, Южной Африке, Сьерра-Леоне, Украине, России, Норвегии, Малайзии и некоторых других странах.
Преобладающими минералами являются рутил, который на 95 процентов состоит из диоксида титана (TiO 2 ), и ильменит (FeTiO 3 ), который содержит от 50 до 65 процентов TiO 2 . Третий минерал, лейкоксен, представляет собой разновидность ильменита, из которого часть железа была выщелочена естественным путем. В нем нет определенного содержания титана. Минералы титана встречаются в аллювиальных и вулканических образованиях. Месторождения обычно содержат от 3 до 12 процентов тяжелых минералов, состоящих из ильменита, рутила, лейкоксена, циркона и монацита.
Горно-обогатительная промышленность
Хотя известные полезные запасы рутила уменьшаются, месторождения ильменита многочисленны.