Как делают столешницы из искусственного акрилового камня
Подробнее о композите, его свойствах вы можете прочитать здесь: Технология изготовления и производство искусственного камня. А в этой статье посмотрите наши советы: какую столешницу выбрать кварцевую или акриловую.
Технология изготовления столешницы из акрилового камня включает следующие этапы
- Снятие замеров для точного чертежа;
- Раскрой деталей — учитывая заданный размер каждой;
- Склеивание деталей;
- Изготовление подложки;
- Сборка рамы;
- Технологические вырезы;
- Поэтапная обработка;
- Поэтапная шлифовка;
- Упаковка, доставка;
- Монтаж;
- Окончательная шлифовка, полировка.
В этой статье мы рассмотрим все этапы производства по шагам.
Точный чертеж изделия
Первый шаг в изготовлении столешницы из композита — это составление чертежа будущего изделия. К вам домой приезжает замерщик с образцами камня — в Москве замер и конечная доставка обойдутся бесплатно. Мастер составляет точнейший чертеж, учитывая возможные неровности и расположение мебельных блоков. Показывает образцы акрилового камня, советует наилучший для вашего случая материал для изготовления столешницы. Это важный этап, так как от точности замеров будет зависеть качество вашего заказа – полученные чертежи, только уже в электронном варианте, передаются на производство специалистам.
Нарезка камня
Изначально искусственный камень формуют в виде слэбов — у разных брендов их размеры отличаются. На нашем производстве, в основном, мы используем плиты 3070 х 760 мм, 3680 х 760 мм, которые в толщину примерно 10-12 мм. Форматно-раскроечный станок нарезает листы пилами и фрезами на заготовки.
Большое влияние на прочность будущего шва и на скорость склеивания деталей оказывают температура, влажность и чистота воздуха. При высокой температуре клей схватывается слишком быстро, а при низкой, наоборот, слишком медленно. Для надежного и прочного соединения деталей самой лучшей будет температура от +18 до +26 °С. Поэтому в помещениях на производстве эти показатели поддерживаются на среднем оптимальном уровне. Очистка воздуха от пыли – еще один важный фактор.
Сложные по форме вырезы делают на вертикальном фрезерном станке с числовым программным управлением (ЧПУ). Это же оборудование для производства сложных деталей подходит для выпиливания пазов для стока воды. На нем же делают четверти – они необходимы для стыковки горизонтальной поверхности с бортиками, кромками.
Склеивание деталей
Угловая столешница из искусственного камня при неправильной сборке дает трещину, поскольку на стыке появляется концентратор напряжения. Чтобы этого избежать, важно грамотно раскраивать слэбы для угловых столешниц: стык полотен не должен приходиться угол изделия. Перед склеиванием детали фрезеруют, наносят клей и стягивают струбцинами. На шов с обратной стороны накладывается дополнительное усиление.
Кромка вырезается отдельно и крепится специальным акриловым клеем. Перед тем, как соединить детали, на горизонтальной поверхности вырезается четверть. При комнатной температуре для реакции полимеризации и полного застывания клея нужно около 40 минут, при более низкой температуре — например, ниже +11 °С — полимеризация вообще может даже не начаться. Для лучшего схватывания клея, швы стягиваются зажимами или теми же струбцинами через каждые 10 см. После высыхания клея бортик шлифуется. В радиусе кромка получается 3, 6, 9 или 12 мм.
Изготовление подложки
С учетом того, что средняя толщина акрилового слэба, который используют в производстве столешниц, примерно 10-12 мм, а сама рабочая поверхность обладает толщиной как минимум, 40 мм, возникает логичный вопрос: что внутри столешницы из искусственного камня, из чего ее делают? Для утолщения и жесткости конструкции, под акриловый спил подклеивают основу. К ее изготовлению приступают после раскройки всех композитных деталей. Обрешетка своей формой повторяет акриловую заготовку.
Основу небольшого размера делают цельной. Если в конструкции есть скругления, то они также выполняются единым цельным фрагментом. Чтобы подложка плотно легла на кухонный модуль, еще на первом этапе, когда делаются замеры для чертежа, учитывается расположение всех мебельных блоков.
Обрешетка изготавливается из ДСП, МДФ или фанеры. Опытным путем мы пришли к выводу, что подложку лучше делать из влагостойкого МДФ. Так как фанера многослойна, то при попадании влаги она расслаивается, в отличие от цельного крепкого МДФ.
Для рабочих поверхностей большого размера, в качестве подложки лучше использовать ДСП, так как такая основа способна выдержать большую нагрузку.
Как сделать столешницу из акрила сложной формы
Акриловый камень обладает чудесным качеством – при нагревании он хорошо гнется. Можно использовать это свойство для изготовления столешниц под заказ, оригинальной выгнутой формы. В специальной печи композит нагревают и придают необходимую форму. Этим же приемом можно воспользоваться для закругления краев.
Сборка рамы
Поверхность из акрилового камня и ее готовую обрешетку соединяют между собой силиконовым герметиком. Он надежно скрепляет детали, обладает определенной степенью подвижности, что не дает столешнице деформироваться в случае перепадов температуры. Такой клей хорошо противостоит влаге.
Технологические вырезы
Отверстия под варочную панель под мойку (если это кухня) и под раковину (если ванная комната) называются технологическими вырезами и делаются фрезером по шаблону уже на месте. По углам таких вырезов, чтобы не создавать концентраторы напряжения, вклеиваются усиления – закладные. Такие закладные будут являться своего рода гарантией того, что по столешнице при эксплуатации не пойдут трещины. Во время работы, чтобы не было пыли, мастер пользуется профессиональным пылесосом.
Поэтапная обработка
Когда столешница собрана, поверхности необходимо придать финальный завершенный вид. Для начала требуется обработка фрезером — она делается вручную, достаточно грубыми движениями. Следом — постепенная шлифовка и окончательная полировка. Очень важно в первую очередь обработать кромку: убрать припуск на высоту фрезером, а потом уже придать ей необходимую форму. Аналогичным образом обрабатываются все вырезы и углы.
Шлифовка и полировка
Обработка поверхности включает в себя шлифовку столешницы и ее полировку. Шлифуют поверхность орбитальными шлифмашинами (их также называют эксцентривыми) по определенной траектории в разных направлениях. Это делается «ступенчато»и поэтапно, с заменой предыдущих абразивов на всё более мелкие. Последний шаг – полировка изделия. Обычно для кухонь и ванных комнат делают матовую или полуглянцевую обработку.
Полировку до зеркального глянца используют редко, особенно на кухне — ведь на такой поверхности будут видны брызги, отпечатки и все царапинки, даже самые мелкие и незначительные.
Упаковка столешницы
После окончания работ столешница тщательно упаковывается. Для лучшей сохранности вся отполированная поверхность оклеивается прозрачной пленкой. Потом идет защитный слой вспененного материала, а углы изделия укрываются картонными уголками.
Лист ДВП кладется с двух сторон — снизу и сверху. Упакованную столешницу скрепляют скотчем и пластиковой лентой. Сверху крепится наклейка с логотипом фирмы, номером заказа и адресом доставки.
Монтаж
Это последний этап работы. При монтаже склеиваются отдельные детали, делаются технологические вырезы под варочную панель или мойку, а в конце работы проводится окончательная шлифовка изделия и его полировка.
Подробную информацию о том, где заказать столешницу из акрилового камня и как оформить заказ, вы можете узнать у нашего менеджера.
Столешница из искусственного камня своими руками
Для мебели в кухне и в ванной очень важна надежность и функциональность. А еще требуется легкость уборки — за чистотой следить нужно обязательно. Многим из этих критериев отвечает столешница из искусственного камня. Но нужно правильно выбрать материал, чтобы не оказалось, что дорогая вещь не оправдала ожиданий.
Содержание статьи
- 1 Виды искусственного камня
- 1.1 Столешницы из акрила
- 1.2 Агломерат
- 1.3 Листовой искусственный камень
- 2 Какую технологию проще освоить самостоятельно
- 3 Столешница из литьевого акрила своими руками
- 3.1 Подготовка
- 3.2 Изготовление столешницы
- 3.3 Установка на каркас и полировка
- 4 Из листового камня
Виды искусственного камня
В последнее время все четче прослеживается тенденция к использованию в отделке более натуральных материалов. Та же столешница в кухню или ванную. Пусть МДФ может быть и неплохой вариант, но хочется чего-то более надежного и солидного. Самый оптимальный выбор — натуральный камень. Но такой вариант слишком дорог. Более бюджетна столешница из искусственного камня, хотя натуральной ее назвать очень сложно. Только один из видов, и то с натяжкой.
Столешница из искусственного камня смотрится хорошо. Важно, чтобы она еще и в эксплуатации была удобной и «долгоиграющей»При знакомстве с темой оказывается, что искусственный камень может быть разным. Причем разным кардинально — из различных материалов с разными свойствами. Или используют разные технологии, например, литьевую. Так изготавливаются бесшовные столешницы любой формы. Или наклеивают листовой материал на основу, но тут без швов не обойтись.
Но не торопитесь с выводами. Кажется, что столешница без швов лучше. Возможно. Но при литьевой технологии применяют пластик, а он склонен к появлению царапин. Так что лучше уж хорошо обработанные швы. При высоком качестве выполнения работ они на сложность уборки не влияют, а заметны только с близкого расстояния. В общем, разбираемся с технологиями производства столешниц из искусственного камня.
Столешницы из акрила
Бесшовные столешницы делают из акрилового камня. Это пластик, который продают в жидком виде. В состав могут подмешивать натуральные камни или песок, но основная масса — это, все-таки, пластик со всеми его достоинствами и недостатками. Могут такой материал называть жидкий камень, жидкий мрамор и т.д. Суть не меняется. Разве что под этим наименованием скрывается агломерат. Но тут надо уточнять процент минеральной составляющей. Если он меньше 90%, а в качестве связующего используется акрил, то, как ни крути, это акриловая столешница, а не каменная.
Достоинства — самые разные цвета, варианты композиции, невысокая цена (это если без бешеных накруток). Недостатки — поверхность царапается, боится горячего. После того как появляются царапины, их можно отполировать, но это недешевая услуга. Вид после восстановления на некоторое время восстановится. Но на некоторое время — это до появления новых царапин.
Из акрилового камня столешницы выглядят очень неплохоТехнология изготовления столешниц из акрилового камня проста. По заданным размерам и форме делают опалубку. В нее заливают акрил, выжидают время до окончательного твердения. Опалубку снимают. Далее, по идее, надо выждать, пока процессы твердения окончательно закончатся. Это порядка двух недель. За это время из пластика испарятся все летучие составляющие, он наберет максимальную прочность. Но фирмы, которые производят литые столешницы, чаще всего, этап выдержки пропускают. Это и время, и затраты — хранение на складах готовой продукции, когда уже можно получить деньги.
Этот вариант самый недорогой, привлекательный внешне, но и самый ненадежный. Уже через месяц появляются царапины, которые очень портят внешний вид и настроение обладателей.
Агломерат
Это каменная крошка и немного связующего (4-6%). Большая часть каменной крошки (в идеале 96%) — прочный кварц или гранит. В качестве связующего применяют полиэфир. В состав могут «для цвета и разнообразия» добавлять различные натуральные и не очень камни/вещества. Это может быть мраморная крошка, цветное стекло, блестки и т.д.
Внешне агломерат не отличить от акрила, а вот по эксплуатационным характеристикам они очень могут различатьсяКварцевый или гранитный агломерат намного прочнее. По сути, это камень с небольшим добавлением пластика. Он устойчив к механическим воздействиям. Поцарапать можно, но приложить придется солидные усилия. Если царапины, все-таки появились, их можно заполировать. Процесс этот долгий и нудный. Зато столешница выглядит отлично длительное время.
Продавцы акрила говорят, что кварц и гранит «фонят». Это правда. Многие натуральные камни — тот же мрамор, кварц, гранит — имеют определенный природный радиационный фон. Но основное тут — природный. Он не вредный и на здоровье в таких дозах оказывать влияние не может. Второй «минус», который приписывается натуральным камням — их хрупкость. Ну да. Они раскалываются, если по ним очень сильно ударить. Но действие должно быть приложено точечно и такой силы, что его на кухне просто создать невозможно. В общем, если есть возможность, лучше для столешницы выбрать агломерат.
Листовой искусственный камень
Эта технология применяется, если нужна столешница значительной толщины. Тот же агломерат большой толщины — очень тяжело и дорого. А смысла в применении массива особого нет. Цельный агломерат делают при толщине не более 2-3 см. Если нужна более толстая плита на кухонных шкафах, дешевле облицевать основание.
На основание — влагостойкий МДФ, ДСП или фанеру (фанера — самый лучший вариант) — наклеивают слой «камня». Проклеивают плоскость и торцы. Используют специальный сверхпрочный и быстротвердеющий клей. Клей тонируют в тон с покрытием. После застывания швы, стыки, перепады шлифуют. При хорошо выполненной работе такие столешницы очень долговечны и практичны.
Листовой «камень» существует различный. Это может быть один из видов акрила или агломерат. С агломератом все понятно. Он действительно прочный и надежный. Просто в данном случае чаще применяют более дорогие сорта, например, с мрамором. Листовой акрил — более дешевый вариант. Несмотря на то, что это пластик, по эксплуатационным характеристикам он лучше литьевого собрата.
Строит сказать, что и агломерат может быть «не очень». Если в нем применяют крошащийся заполнитель, если связующее недостаточно качественное, будут и царапины, и пятна, и сколы. Если решите заказывать в какой-то фирме, лучше найти тех, кто уже использует их продукцию. И спрашивать о гарантиях. Но учтите, что в наших реалиях, часто одно юридическое лицо закрывают, открывают другое. И все. Все гарантии от юрлица сгорели. Более надежны в этом плане гарантии от частника.
Какую технологию проще освоить самостоятельно
Если говорить о самостоятельном изготовлении, то проще всего сделать столешницу из литьевого акрила. Правда если использовать готовые смеси, цена получится практически такой же, как при заказе на фирме. Следующий по сложности процесс изготовления столешницы — из агломерата. Так как связующего немного, добиться гладкой лицевой поверхности не так просто. Если не пугает длительная шлифовка для получения нормального результата, можно попытаться освоить и эту технологию. Столешница из искусственного камня на основе агломерата — самый лучший выбор в плане долговечности и внешнего вида.
Последняя «по легкости» технология изготовления столешницы — из листового камня. Очень много точной подрезки, склеивания частей и шлифовки. Нужны профессиональные инструменты — дисковая пила с направляющими, лобзик, дисковая шлифовальная машинка с набором дисков для полировки. Еще требуется много струбцин для притягивания и фиксации приклеенных фрагментов.
Столешница из литьевого акрила своими руками
Многим кажется, что цельная столешница без швов — лучший из возможных вариантов. Проще в уходе, не может быть протечек. Это так, но сам материал (акрил) не везде хорош в эксплуатации. Сам акрил — отличный материал. Для ванной столешница из искусственного камня — хороший выбор. Тут очень мало возможностей поцарапать поверхность, нет высоких температур. А влага, пар, мыло и другие моющие средства пластику не страшны. Если вы решили освоить технологию литья акриловой столешницы, можно пробовать сделать ее для ванной комнаты.
Подготовка
Для заливки акрила делают форму. Для ее изготовления используют ламинированный ДСП или МДФ. Если поверхность столешницы должна быть гладкой, материал для опалубки тоже должен быть гладким. Если нужна фактура — она должна быть на форме. После снятия с формы акриловый камень повторит все выемки и бугорки. Поэтому к подбору материала для формы относимся скрупулезно.
Вырезанную заготовку обрамляем бортиками, отверстия под варочную поверхность и мойку закрываем технологическими заглушкамиИз того же материала делают бортики. Края планок шлифуют сначала более грубым полотном, потом все более тонким наждачным диском. Используют все более уменьшающуюся зернистость. Помним, что все дефекты затем будут отлиты в акриле. И они очень заметны, если камень выбрали однотонный, без вкраплений. Швы герметизируются, выравниваются. Конструкция тщательно очищается, высушивается, затем изнутри покрывается воском.
Изготовление столешницы
К акрилу добавляют наполнители — каменную или мраморную крошку, пигмент, декоративные составляющие. Все перемешивается. В последнюю очередь заливается отвердитель. Заливают акрил в несколько слоев, поэтому добавляют отвердитель только в часть состава.
Состав распределяется по плоскостиВ готовую опалубку заливается акриловый состав. Распределяют его равномерно по все площади. Он должен растечься по всем элементам формы. При этом нельзя допустить появление пузырей — воздух надо удалять. После того как состав распределили, сверху укладывается лист ДСП, который тоже смазан воском. На ДСП устанавливают груз. Его надо подбирать аккуратно, чтобы состав не выдавило по бокам. Груз оставляют на полчаса. Потом его снимают, подымают ДСП. В форму заливают вторую порцию пластика и оставляют на сутки. За это время акрил отвердеет. Можно снимать опалубку.
Установка на каркас и полировка
После того как сняли плиту из пластика с опалубки, ее крепят на каркас. Акрил — эластичный материал. Даже при толщине в 20-30 мм, он гнется. Чтобы обеспечить стабильность формы и собирают каркас. Его делают из древесины (брус толщиной 50 мм или больше) или из влагостойкой фанеры (толщина 27 мм). Каркас — это планки вдоль передней и задней стойки, поперечные перемычки, установленные с шагом 40-50 см. Также планки ставят в местах опирания на мебельный каркас. Нужны еще усиления в местах наибольшей нагрузки. Это там, где будет устанавливаться варочная поверхность или мойка.
Каркас делают при толщине акрила больше 10 мм. Для более тонкого слоя требуется сплошное основание. То есть, из той же фанеры надо вырезать повторение вашей столешницы и эти два листа склеить между собой. Толщина фанеры — 27 мм или около того. Можно склеить два более тонких листа. Получается дешевле. Для нормальной склейки листы фиксируют струбцинами.
Финальная отделка — шлифовка. Сначала дисками с мелким зерном — от 320 и выше, в финале — насадкой для полировки. Этот этап важен для внешнего вида. Можно убрать большую часть огрехов. Но можно и навредить.
Из листового камня
Казалось бы, из листового пластика или, как его называют, искусственного камня, сделать что-либо не проблема.
Собранную конструкцию либо наклеивают на сплошное основание (при толщине камня до 10 мм), либо делают каркас из древесины или фанеры. Вроде все несложно. За исключением того, что:
- Лист материала весит много, ворочать его — то еще удовольствие.
- Резы должны быть идеальными, подгонка деталей тоже. Для этого требуется профессиональное оборудование и умение с ним обращаться.
- Стыки проклеиваются и фиксируются струбцинами. Их ставят примерно каждые 20-30 см. Даже для постепенной неспешной работы количество струбцин — порядка десяти.
- Для шлифовки стыков нужна хорошая шлифмашинка. Можно обойтись и шлифовальными дисками на болгарку. Но инструмент при этом должен быть с возможностью регулировки оборотов.
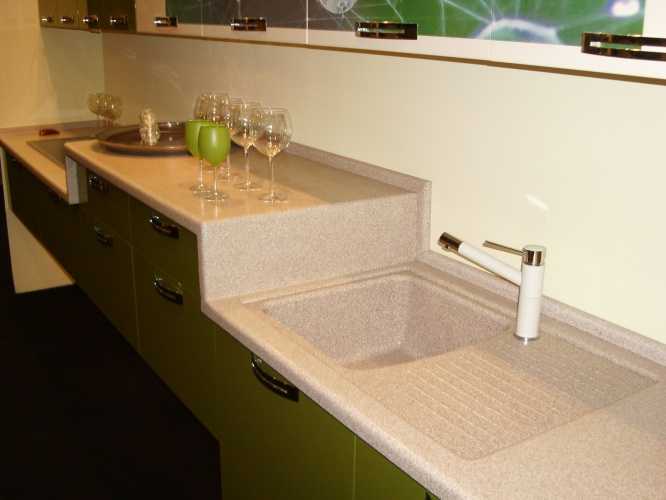
А так да. Можно сделать столешницу из листового искусственного камня своими руками. Чтобы иметь представление о том, как и о чем идет речь, смотрите видео. Пояснений практически нет, но технология работ прослеживается. Вот только для лучшего соединения деталей (при приклеивании кромки) в основном листе лучше выбрать четверть. Так и шов будет не так заметен, да и соединение более надежное.
Столешница из искусственного камня своими руками: технология изготовления
Красота натурального камня ни с чем несравнима. Издревле этот строительный материал использовался при отделке помещений и мебели. Петь о нем дифирамбы можно долго. Но есть у природного камня один большой недостаток – слишком дорогое это удовольствие. Добыча в карьере, перевозка, распил, формовка и шлифовка – слишком затратные процессы, который только увеличивают стоимость изделий. Заменить его раньше можно было лишь деревом, но оно не имело тех качеств, которые бы увеличивали срок эксплуатации.
Но научно-технический прогресс подарил людям возможность иметь у себя в домах дешевую каменную отделку. Это камень искусственный, который обладает всеми теми же качествами и свойствами, что и натуральный, только его цена во много раз ниже. Нас же в этой статье будет интересовать один вопрос – изготовление столешницы из искусственного камня своими руками.
Что такое искусственный камень
Начнем с того, что искусственный камень – это в первую очередь раствор из различных ингредиентов, в состав которых обязательно входит связующий материал. Именно после его застывания композит (а по-другому раствор назвать нельзя) становится прочным, как камень. Поэтому классификация каменного раствора делится по используемому связующему элементу. В настоящее время для этого используется или цемент, или разного вида смолы.
Цементная основа для искусственного камня используется уже давно. Если правильно соблюсти пропорции всех компонентов, то изделие получится очень прочным. В качестве наполнителей для этого используются каменные частички (гранулы). После заливки раствора в форму и затвердевания его производится шлифовка каменной поверхности до зеркального состояния.
Необходимо отметить, что цементная столешница – это большой вес, впрочем, и прошлый век. Сегодня такие крышки для стола уже не изготавливаются. Слишком они тяжелые, долго происходит высыхание изделия, да и на ударные нагрузки такие столешницы испытание не прошли.
Вторая категория – это изделия из акрила. Что можно сказать об этом варианте? Начнем с достоинств.
- Небольшой вес, даже можно сказать, малый в сравнении с цементными.
- Приличная прочность, не уступающая цементным конструкциям.
- Влагостойкость на уровне 100%.
- Срок эксплуатации практически бессрочный, если правильно эксплуатировать изделие.
- Широчайшая гамма расцветок, которую обеспечивают пигменты.
- Искусственный камень не является радиоактивным, что нельзя сказать о природном. В любом камне всегда присутствует малая доза радиационного фона.
- Говоря о ремонте столешницы из искусственного камня своими руками, необходимо отметить, что данный процесс совершенно несложный. Зная правила и нюансы проведения ремонтных работ, столешницу можно привести в порядок в домашних условиях, не затрачивая больших денежных средств.
Всем хорошо искусственный камень, но и у него есть свои недостатки.
- Акриловая столешница не выдерживает больших температур, поэтому ставить на нее горячую посуду не рекомендуется. Максимально она может выдержать температуру до +180С. Кстати, материалы с полиэфирной смолой выдерживают температуру до +600С.
- В зависимости от используемой смолы изделия через несколько лет эксплуатации могут стать потертыми или на них могут образоваться царапины.
Что касается наполнения искусственного камня, то здесь могут быть использованы гранулы любых каменных пород.
Изготовление столешницы
Существует несколько технологий изготовления столешницы из искусственного камня. Но в любом случае все начинается с подготовки и определения формы изделия, которая должна вписаться в интерьер кухни. То есть, надо взять бумагу и набросать на нее эскиз для столешницы из камня. Форма определяется вкусовыми пристрастиями хозяина дома, а размеры определяются из габаритов кухонного пространства. Все это и надо перенести на бумагу.
Конечно, проще всего каменную столешницу изготовить прямоугольной без всяких изгибов и скругленностей. С этим справится даже начинающий домашний мастер. Сложнее, если форма изделия будет разноплановой с разными размерами. Непросто также изготовить столешницу П-образной конструкции, в которой дополнительно необходимо сделать отверстия под мойку и варочную панель.
Поэтому начинать изготавливать столешницу из искусственного камня своими руками надо с разметки. Оптимальная ширина – 60 см, длина зависит от собранной мебели, на которую столешница будет устанавливаться.
Изготовление из акрилового камня
Начнем с того, что в продаже есть два варианта данного типа искусственного камня. Это готовые листы размерами 3,66х0,76 м, толщиною 3-12 мм, и так называемый жидкий камень, который можно сформировать самому.
Рассмотрим первый вариант. Итак, перед вами лист, который надо подогнать под размеры эскиза, предварительно нанесен вами на бумагу. Очень важно точно перенести на камень форму и размеры столешницы. Теперь отрезным алмазным диском надо провести по линиям надрезы, придавая заготовке полуфабрикат, но уже практически с точными размерами. Если в столешнице необходимо просверлить отверстия, то это надо сделать именно сейчас.
Теперь при помощи фрезы (хорошего качества) необходимо отшлифовать торцы полученной заготовки. Это также касается и торцов срезанных отверстий. Конечно, толщина листа в этом случае играет немаловажную роль. Но даже 12 мм – это не гарантия высокой прочности, потому что установке на мебельные стойки получится провис, который может стать причиной излома. Поэтому под столешницу надо обязательно установить основу. Для этого обычно используется влагостойкая фанера, потому что кухня – помещение влажное. Не стоит в этом случае использовать такие материалы, как ДСП или ДВП.
Теперь из фанерного листа надо вырезать точно такое же изделия с отверстиями и размерами. После чего оба материала приклеиваются друг на друга двухкомпонентным клеевым составом и стягиваются струбцинами. В таком состоянии они должны пролежать около 7 часов.
Внимание! Если для производства столешницы используется толстый лист заготовки, то основу можно делать не сплошной. Для этого из фанеры можно нарезать полоски шириною 7-8 см, которые равномерно распределяются и приклеиваются к обратной стороне листа из акрилового камня.
Обратите внимание, что с торца лицевой стороны и с боков будет видна фанера, поэтому ее надо закрыть полосками искусственного камня. Для чего они нарезаются из того же листа. Ширина определяется опять-таки вкусовыми пристрастиями, но есть стандартные размеры – 3-4 см. Задний торец надо будет закрыть готовым профилем или плинтусом. Все эти элементы приклеиваются по своим местам тем же клеевым составом. Обращайтесь с клеем аккуратно. Он быстро высыхает, так что здесь придется поспешать, но с должной осторожностью.
И еще один момент. Если изготавливают Г-образную столешницу своими руками, то необходимо в месте стыка двух частей снизу установить полоску фанеры прямо по линии соединения. Она будет играть дополнительное ребро жесткости, что увеличит прочность изделия.
И последний завершающий этап – это шлифовка фанеры каменной столешницы своими руками. Сделать это можно шлифмашинкой.
Изготовление из жидкого камня
Какие материалы необходимы, чтобы приготовить в домашних условиях жидкий камень. Давайте перечислим их.
- Ацетон в качестве растворителя.
- Отвердитель, она же смола.
- Кальцинит – это кальциевая сода или нитрат кальция, который хорошо растворяется в воде.
По сути, это удобрение.
- Эпоксидный гелькоут – это эластичный материал пигментированного типа. Изготавливается на основе смол.
- Каменные наполнители.
В принципе, основа жидкого камня – это гелькоут, наполнители, отвердитель. Пропорции такие: гелькоут около 60%, отвердитель до 40%, остальное наполнитель. При смешивании должна получиться жидкая пастообразная субстанция. Теперь к вопросу, как сделать столешницу из искусственного камня? Есть две технологии.
Первая заключается в том, что сначала надо подготовить шаблон с формой и размерами. Для этого можно использовать фанеру, ОСП, ДСП или ДПВ. На него слоем 2-4 мм наносится жидкий материал. После высыхания он шлифуется с лицевой стороны.
Вторая технология производства столешниц называется обратной. В ней используются разные материалы, которых нет в предыдущем списке, но они необходимы именно при заливке.
- Необходимо сделать шаблон из фанерного листа, можно использовать ДСП. Главное, чтобы выбранный лист не был тонким, потому что здесь необходима прочность материала, чтобы выдерживать вес заливаемого раствора.
Размер шаблона должен быть больше оригинала на 5 мм с каждой стороны.
- Вырезаются из фанеры полоски шириною 5 см, и приклеиваем их на шаблон по периметру, используя термоклей. Ставят их на ребро.
- Если в столешнице будут отверстия, то их надо вырезать и по периметру наклеить на ребро все те же полоски.
- Для герметичности конструкции стыки бортиков и шаблона можно обмазать пластилином.
- Теперь полученную форму изнутри надо обмазать воском или любым другим разделительным составом.
- Все готово, можно заливать жидкий камень.
- Выдерживаем его полчаса, затем сверху накладываем стеклоткань. Она будет выполнять функции армирующего каркаса для увеличения прочности изделия.
- Теперь сверху надо залить грунт. Это смесь из кальцита (80%), отвердителя (1%), смолы (8%) и пигментов.
- Сверху грунтовочного слоя надо уложить еще один шаблон, с помощью которого он равномерно распределиться по нижней форме. То есть, его надо будет заранее вырезать из фанерного листа.
Оптимально, если на верхний шаблон уложить небольшой груз, он выдавит излишки грунта, который надо тут же удалить.
- В таком состоянии конструкция должна простоять полтора часа.
- После чего груз и шаблон снимаются, и верхняя поверхность шлифуется до зеркального блеска.
Некоторые мастера рекомендуют грунт заливать в два слоя. Это увеличит прочностные характеристики столешницы, изготовленной из жидкого камня своими руками. При этом первый слой заливается из расчета 5 кг на 1 м² поверхности, второй – 3 кг. Учитывайте, что самого жидкого камня уйдет 3-4 кг/м².
Сделанные таким способом столешницы намного прочнее, чем по первой технологии. А соответственно у них и больший срок эксплуатации. Конечно, по времени данная операция занимает много времени, но это стоит того.
Ремонт столешницы из искусственного камня
В принципе, ремонт столешницы из акрила делается по очень простой технологии. К примеру, если на поверхности появилась трещина или царапина. Для этого потребуется все тот же клей, которым к изделию приклеиваются плинтус и бортики.
Необходимо в первую очередь трещину расшить, то есть, увеличить ее ширину. Затем в нее заливается клеевой состав, который после высыхания шлифуется. Все, ремонт закончен.
Если на поверхности появилось вздутие или пятно, то данный участок надо вырезать на глубину 1-2 мм. Это делается фрезой, насаженной на болгарку. Затем из куска такого же готового жидкого камня вырезается меньший кусок, по форме и размерам совпадающий с отрезанным участком. Теперь этот кусок надо приклеить к вырезанному участку. После застывания клея границы заплатки надо расшить, заполнить их клеевым составом, а после высыхания зашлифовать.
Заключение по теме
Необходимо отметить, что технология изготовления столешницы из данного материала является не самой сложной в виду простоты формы самого изделия. К примеру, сделать мойку из искусственного камня своими руками куда сложнее. Ведь это уже объемная конструкция, требующая использования более сложного шаблона. К тому скругления мойки создают определенные трудности в их формировании. Поэтому по понятным причинам ее изготавливают только из жидкого камня.
Процесс производства кварцевого камня: все, что вам нужно знать
Введение
В течение долгого времени натуральные камни, такие как мрамор и гранит, использовались как в жилых, так и в коммерческих зданиях для улучшения их внешнего вида. Однако использование этих камней имеет много недостатков, что делает кварцевый камень фабричного производства лучшей заменой этим камням. Некоторые из основных недостатков включают
- Натуральные камни восприимчивы к пятнам
- Имеют естественные черты, проявляющиеся в виде трещин
- Они менее гладкие
- Имеют недостаточную эластичность
- Они не бесшовные и, следовательно, трудно обеспечить точность длины
Натуральные камни веками использовались из-за их долговечности и прочности и другими сильными характеристиками, но кварцевый камень представляет собой лучшую альтернативу этим камням, поскольку он прочнее и не обладает нежелательными качествами природных камней.
За последнее десятилетие продажи и потребление кварцевых столешниц в Индии и во всем мире значительно выросли. Это связано с падением цен на кварцевые камни из-за повышения эффективности процесса производства кварцевых камней.
Прежде чем углубляться в производственный процесс, мы дадим вам краткую информацию о кварцевом минерале и кварцевом камне.
Обзор минералов кварца
Кварц — это вид минерала, который превращается в кристаллы из-за сильного давления. Как химическое соединение, он состоит из одной части кремния и двух частей кислорода. Он считается самым распространенным минералом, который можно найти на поверхности Земли. Благодаря своим уникальным свойствам он стал одним из самых полезных минералов.
Между тем, этот минерал бывает разных цветов, прозрачности и разновидностей. Аметист, розовый кварц, оникс и тигровый глаз — одни из самых популярных разновидностей кварца. Его очень много в осадочных, метаморфических и магматических породах. Известно, что он обладает высокой устойчивостью к химическому и механическому воздействию.
Цвет, прозрачность и блеск кварца делают его идеальным драгоценным камнем, а также для производства стекла. Поскольку он обладает термостойкостью и электрическими свойствами, этот минерал используется в электронных продуктах.
Искусственный кварц
В отличие от гранита, кварц не образует каменных блоков и в природе существует в виде скоплений. Хотя некоторые люди заинтересованы в том, чтобы этот минерал стал частью дизайна их кухни, естественное состояние кварца считается непригодным для столешниц и любых других больших плит.
Однако, чтобы сделать кварц пригодным для использования в плитах, его можно преобразовать в другие формы, такие как искусственный камень, созданный открытым способом. Искусственный кварц также обычно называют реконструированным или реконструированным камнем. Производственный процесс включает в себя смесь кварцевой крошки, пигментов, добавок и связующих смол.
Искусственный кварцевый камень для плит и столешниц представлен в широком спектре цветов, текстур и рисунков. В зависимости от производственного процесса текстура может быть грубой или мелкой. Затем его можно комбинировать со стеклом и любыми другими отражающими материалами для достижения сверкающей отделки. Когда непористая природа кварца сочетается с долговечностью гранита, можно достичь высококачественных и надежных применений.
Процесс производства кварцевого камня
В то время как мы рассмотрим процесс производства кварцевого камня, мы также рассмотрим процесс производства необработанного кварца и поймем, как производится необработанный кварц перед его поставкой на предприятия по производству кварцевого камня.
Производство необработанного кварца
Благодаря своей полезности и основным свойствам кварц входит в число лучших продуктов B2B, которые добываются и перерабатываются для поставок на местный рынок и экспорта. В рамках производственного процесса этот минерал будет подвергаться процессу добычи вплоть до фактической производственной обработки.
1) Добыча кварца
Кварц можно добывать открытым способом. Есть несколько редких случаев, когда шахтерам приходится использовать взрывчатые вещества, когда им необходимо вскрыть глубокий пласт минерала. Но это делается редко, потому что, несмотря на свою твердость, ее можно легко повредить при резком изменении температур.
При добыче полезных ископаемых обычно используют экскаваторы-погрузчики и бульдозеры, чтобы эффективно избавиться как от глины, так и от почвы, окружающей минерал. После этого в породе обнажатся кристаллические жилы кварца. Оказавшись на поверхности, команда будет использовать кирки, долота и другие небольшие ручные инструменты для извлечения кварца прямо из карьера.
Компания Unique Crystal Minerals использует экскаваторы-погрузчики JCB для добычи кварца в большинстве горнодобывающих регионов Раджастхана.
2) Обработка кварца
После процесса добычи посредством добычи кварц необходимо подвергнуть тщательной и тщательной очистке. То есть убрать все химические примеси и физические недостатки. После тщательной очистки специальная команда будет отвечать за проверку кварца. Затем он будет измельчен до разных размеров, которые будут зависеть от его будущего использования.
С помощью дробилки кварц подвергается процессу дробления, а для его разделения используется вибрационный грохот. Затем следует использовать шаровую мельницу для измельчения кварца. Наконец, квалифицированный классификатор классифицирует минералы по размерам. Что касается кварцевого порошка, то для измельчения чистого кускового кварца в мелкий порошок используется мельница.
3) Поставка кварца
После обработки кварц может быть доставлен в больших морских контейнерах при транспортировке по морю. При транспортировке по суше используются большие грузовики или поезда по железной дороге. Если типы кварца относятся к полудрагоценным камням, необходимо принять дополнительные меры предосторожности, чтобы гарантировать, что они не повреждены.
Компания Unique Crystal Minerals, производитель кварца самого высокого качества в Индии, поставляет кварцевый песок, кварцевые гранулы и другие кварцевые продукты B2B, которые затем перерабатываются в полезные промышленные и потребительские товары. Мы также являемся одним из крупнейших поставщиков кварца в Индии. Мы поставляем кварцевые изделия различным оптовым дистрибьюторам и отраслям промышленности по всей Индии и экспортируем их по всему миру.
Производство кварцевого камня
1) Сырье
Процесс производства искусственного кварцевого камня начинается с выбора изготовленных кварцевых материалов. Это может быть любой кварцевый продукт, такой как кварцевый песок или кварцевые гранулы. Как объяснялось выше, необработанный кварц выбирается после завершения производственного процесса на предприятии по производству кварца, таком как Unique Crystal Minerals.
2) Смешивание
Отобранный необработанный кварц измельчается, а затем смешивается в соотношении 93% кварцевых заполнителей до 7% смоляного связующего вместе с другими добавками.
3) Прессование плит
Кроме того, смесь будет уплотняться для формирования плит с использованием метода вакуума и вибрации в течение примерно 100 секунд при давлении 100 тонн. Используя этот вид процесса, он может минимизировать пористость при одновременном снижении водопоглощения.
4) Нагрев
После этого плиты будут подвергаться процессу отверждения в печи при температуре 85 градусов в течение примерно получаса. То есть достичь всех необходимых свойств по стойкости к пятнам и ударам. Для ускорения процесса отверждения можно использовать пар или печь. После завершения этого процесса произведенные плиты проходят калибровку, калибровку, полировку, а затем готовятся к процессу упаковки.
5) Охлаждение
После отверждения плиты удерживают в вертикальном положении с помощью зажима и охлаждают в течение 24-36 часов.
6) Обрезка
Кромки обрезаны и выровнены.
7) Проверка качества
С помощью процесса производства инженерного кварца будет достигнута согласованность и однородность оттенка и размера. В результате экономится время в процессе строительства. Хотя инженерная версия напоминает узоры натурального камня, она предлагает более однородный цвет, рисунок и текстуру, а также однородный внешний вид. Кроме того, поскольку они созданы руками человека, их можно легко изготовить в больших размерах, что может привести к лучшей эстетике и меньшему количеству стыков.
Заключение
Рынок кварцевого минерала становится все шире, поэтому неудивительно, что процесс добычи и производства также прогрессирует. Прелесть кварца в том, что он очень гибкий и может использоваться в различных областях: от дизайна интерьера до ювелирных изделий и более крупной промышленности. Таким образом, каждый может рассчитывать на высококачественное использование и отдельные преимущества, поскольку кварц подвергается тщательному и тщательному производственному процессу.
Влияние на производство: натуральный камень или искусственный кварц
Существует множество строительных материалов, из которых можно выбирать при проектировании или реконструкции проекта. Искусственный кварц — это один из материалов, который часто используется в интерьерах, особенно для столешниц. Он бывает разных цветов, узоров и текстур. Продукт изготовлен путем сочетания природных и искусственных материалов, включая кварц, смолы, пигменты и другие ингредиенты. Это твердый, плотный и непористый материал , но его можно использовать только внутри помещений, поскольку смолы не устойчивы к УФ-излучению для наружного применения. Искусственный кварц часто изготавливается для имитации популярных натуральных камней, особенно белого мрамора, но, как правило, имеет меньше вариаций или прожилок, чем натуральный камень. Искусственный кварц иногда продается как устойчивый природный материал из-за содержащегося в нем кварца. Однако, как показывает приведенный ниже процесс производства искусственного кварца, это не так.
- Большое количество машин и энергии используется для отделки и резки искусственного кварца на плиты.
- Фотографии предоставлены Стефани Вьерра.
Процесс производства искусственного кварца
Процесс производства искусственного кварца включает в себя множество энерго- и ресурсоемких этапов, что оказывает большее воздействие на окружающую среду. Сначала кварц добывают или добывают из-под земли, затем дробят. Требуется несколько других добавок, таких как полиэфиры, смолы, кислоты, спирты, стирол, пероксид и другие химические вещества, чтобы создать ряд химических реакций. Все эти добавочные материалы должны быть изготовлены, а затем доставлены на производственный завод, где они будут смешаны и помещены в формы, уплотнены и часто нагреты и отверждены для создания плит. В зависимости от производителя полученные плиты будут различаться по размеру, толщине и внешнему виду. Поскольку инженерный кварц изготавливается и устанавливается в виде плит, швы будут видны на большой столешнице. Кроме того, в то время как искусственный кварц производится с некоторой термостойкостью, он не такой термостойкий, как натуральный камень. Например, его нельзя использовать в качестве напольного покрытия над лучистым теплом из-за возможного повреждения от длительного теплового воздействия.
Производственные воздействия искусственного кварца.
Проблемы устойчивого развития
Для сравнения, натуральный камень можно использовать в большинстве областей применения, и для этого требуется только добыча, изготовление, отделка и транспортировка. Для создания натурального камня не требуются дополнительные материалы или химикаты. Земля естественным образом формирует материал с течением времени. Это означает, что натуральный камень действительно является натуральным материалом и обладает многими другими свойствами, в том числе широким спектром эстетики, долговечностью и возможностью вторичной переработки. Натуральный камень не содержит летучих органических соединений (ЛОС), то есть не выделяет вредных газов, что делает его безопасным для здоровья материалом.
Производство ударов из природного камня.
Используемые материалы и многоэтапный процесс, необходимый для производства инженерного кварца, также приводят к более высокому потенциалу глобального потепления, как показано ниже. С точки зрения общей устойчивости природный камень оказывает гораздо меньшее воздействие на окружающую среду, чем искусственный кварц, из-за минимальных ресурсов, используемых для его добычи, изготовления, изготовления, отделки и транспортировки. Воздействие этих процессов было задокументировано и систематически сравнивалось с другими материалами с использованием тех же экологических критериев. Эта информация является ценным ресурсом при выборе устойчивого материала для проекта.
Потенциал глобального потепления
На диаграмме сравнивается потенциал глобального потепления (выраженный в кг эквивалента CO2) на этапе производства продукта (A1-A3), задокументированный в результатах ОЖЦ, опубликованных в EPD для различных продуктов. Данные усреднены при использовании нескольких EPD. Все функциональные узлы переведены на 1 тонну.
Эти характеристики и атрибуты также делают натуральный камень отличным выбором при поиске сертификата рейтинга экологичного строительства в рамках программы «Лидерство в энергетическом и экологическом проектировании» Совета США по экологическому строительству (LEED) или программы Living Building Challenge (LBC) Международного института будущего. Чтобы еще больше решить эти проблемы, индустрия натурального камня на протяжении многих лет усердно работала над постоянными улучшениями в каждой области и на каждом этапе процесса. Это включает в себя сокращение потребления воды и энергии, повышение эффективности транспортировки природного камня, надлежащее управление и адаптивное повторное использование карьеров и многое другое.
Промышленность по производству природного камня также создала систему сертификации, которая определяет, соответствует ли карьер или производитель определенным стандартам устойчивого развития в ключевых важных областях. Это облегчает поиск и использование натуральных камней, соответствующих стандарту, упрощая процесс выбора правильного материала, который не только хорошо выглядит и работает, но и оказывает минимальное воздействие на окружающую среду. Стандарт также принят в LBC, что еще больше гарантирует его использование в проектах устойчивого строительства. Даже если натуральный камень еще не сертифицирован по стандарту, эту информацию можно использовать для проверки поставщиков камня и задать важные вопросы, чтобы помочь выбрать оптимальный натуральный камень для вашего проекта. Для получения дополнительной информации посетите веб-сайт Института натурального камня по адресу: www.naturalstoneinstitute.org/sustainability.
Серия «Воздействие на производство»: Подробнее
Взгляд на историю искусственного камня
|