Технология изготовления резины. Вулканизация — Технарь
Процесс изготовления резины и резиновых деталей состоит из приготовления сырой резиновой смеси, получения из нее полуфабрикатов или деталей и их вулканизации. Этот процесс включает в себя следующие операции: вальцевание, каландрирование, получение заготовок, формование и вулканизацию, обработку готовых деталей.
Для приготовления сырой резины каучук разрезают на куски и пропускают через вальцы (рис. 7.1) для придания пластичности. Затем в специальных смесителях каучук смешивают с порошкообразными компонентами, входящими в состав резины (вулканизирующими веществами, наполнителями, ускорителями вулканизации и т.д.), вводя их в резиновую смесь точно по весовой дозировке. Перемешивание можно производить и на вальцах. Таким образом, получают однородную, пластичную и малоупругую массу – сырую резину. Она легко формуется, растворяется в органических растворителях и при нагревании становится клейкой.
Провальцованная сырая резина поступает на каландр (рис. 7.2), где получают листы заданной толщины. Из каландрованных листов заготовки деталей получают: вырезкой по шаблонам, вырубкой шанцевыми ножами, формованием на шприц-машине.
Для изготовления резиновых деталей формовым способом используют гидравлические вулканизационные прессы с электрообогревом. Прессование производят в пресс-формах методами прямого и литьевого прессования. Литье под давлением применяют для изготовления деталей сложной конфигурации.
Для получения прочных высокоэластичных изделий (покрышек, трансмиссионных лент, ремней, рукавов) резиновую смесь наносят на высокопрочные ткани (корд, бельтинг) из хлопчатобумажного, полиамидного или полиэфирного волокна. Для сцепления резины с тканью применяют способы напрессования или пропитывания. В первом случае тонкие листы каландрованной резины на специальных дублировочных каландрах напрессовывают на ткань. Во втором случае ткань пропитывают раствором резиновой смеси (резиновым клеем) и сушат для удаления растворителя. Прорезиненную ткань раскраивают, собирают в пакеты и прессуют в изделия.
Многие резиновые изделия армируют металлическими деталями. Металлические детали (за исключением латунных) не обладают адгезией к резине, поэтому легко вырываются из изделия. Чтобы увеличить адгезию металлической арматуры к резине, на металл наносят клеевую пленку или осуществляют латунирование.
Наиболее высокой прочности сцепления металла с резиной достигают нанесением на металлическую поверхность пленки изоционатного клея «лейконат».
Любой процесс формования заканчивается процессом вулканизации (нагревания с серой). Каучук состоит из линейных молекул. При нагревании с серой происходит укрупнение молекул и образование сетчатой структуры молекул, при этом каучук превращается в резину. В резине, кроме линейных, есть двух- и трехмерные молекулы.
Усложнение и укрупнение молекул приводит к тому, что вещество приобретает упругость, без снижения эластичности, а, кроме того, и стойкость к термическим и химическим воздействиям. Кроме того, в резину добавляют сажу, которая увеличивает его прочность.
Длительность и температура вулканизации зависит от рецептуры резиновой смеси (от типа каучука и эффективности введенного ускорителя). Обычно вулканизацию проводят при температуре 120 – 150 °С.
При формовании деталей вулканизация их производится в пресс-формах на вулканизационных гидравлических прессах с паровым или электрическим обогревом. Формовой метод вулканизации дает более плотную, однородную структуру, более точные размеры и более гладкую поверхность резинового изделия. При невозможности вулканизации в пресс-форме, особенно изделий, полученных на шприц-машине накатыванием и дублированием, вулканизацию проводят в вулканизационном котле.
Почти все синтетические каучуки получают методом эмульсионной полимеризации в водных средах. Размеры образующихся в этих условиях частиц полимера получаются близкими к размерам коллоидных частиц. В присутствии специально вводимых веществ (эмульгаторов) частицы полимеров образуют устойчивую эмульсию полимера в воде, которая называется латексом.
В настоящее время выпускается большое количество латексов, из которых можно непосредственно изготавливать резиновые изделия. Латексы применяются для получения фрикционных изделий, для пропитки корда, для изготовления шлифовальных камней, резиновых нитей, эластичных волосяных подушек, перчаток, воздушных шаров, тонкостенных изделий, для замены клеев эластичными пастами, для получения резиновых пеноматериалов. Для получения резиновых изделий толщиной не более 0,2 мм форму (обычно стеклянную) несколько раз погружают в латекс. После каждого погружения на форме остается слой латекса, из которого высушиванием удаляют воду.
Процесс изготовления изделий из латексов состоит из следующих операций: смешивания латекса с вулканизирующими агентами и другими компонентами резиновой смеси; высаживания резины на форму в виде пленки; вулканизации.
Метки: Вулканизациявысокоэластичных изделийгидравлические вулканизационные прессы с электрообогревомКаучукПровальцованная сырая резинарезинарезиновой смесиТехнология изготовления резиныФормовой метод вулканизацииэластичными пастамиэмульсионной полимеризации
Производство резины из каучука
Резина (в пер. с лат. смола) представляется собой эластичный материал — продукт вулканизации синтетических и натуральных каучуков.
Важнейшим свойством резины является эластичность материала, то есть способность резины к значительным обратимым деформациям в расширенном температурном интервале — это свойства резины обусловило широчайшую область применения данного материала. Резина сегодня используется во всех отраслях промышленности, в вагоностроении, авиастроении, автомобилестроении, судостроении и так далее.
Высокий спрос на резинотехнические изделия привел к расширению предложения. Производители резины в России, стремясь предложить своим клиентам лучшее из лучшего, ищут новые решения, совершенствуют технологии производства.
Качественное производство резины делает нашу компанию одним из лидеров в данной области. Мы не ограничены рамками собственного завода, производство резины из каучука осуществляется также и на зарубежных предприятиях — так что мы готовы предложить вам максимально широкий ассортимент резинотехнической продукции безупречного качества по доступной стоимости.
Мы не просто предлагаем вам производство каучука и резины высокого качества по низкой цене, но мы предлагаем широчайший выбор РТИ с различными эксплуатационными характеристиками. У нас вы найдете и типовые, простые уплотнительные профили резиновые различных сечений, и резинотехнические изделия более сложных конфигураций, свойств — неформовые РТИ, судовая резина, производство деталей из резины и так далее.
Несколько слов отдельно стоит сказать о производстве судовой резины. В сфере отечественного судостроения и судоремонта сегодня активно используется особо мягкая резина уплотнительная судовая, отличающаяся уникальными эксплуатационными характеристиками: речь идет о светоозоностойкости, стойкости к морской воде, влажному морскому воздуху, к бензину и минеральным маслам (при температуре +15°…+25°), рабочие характеристики резины поддерживаются в широчайшем температурном диапазоне:
−30°…+70°С. Такая резина может активно использоваться для уплотнения дверей, люков, иллюминаторов на судах.
О тонкостях процесса производства резины
Производство резины и каучука подразумевает изменение свойств исходного материала — увеличивается прочность, эластичность и иные эксплуатационные характеристики, за которые так ценятся резинотехнические изделия. При достижении наиболее оптимального сочетания суммы механических и физических свойств создаваемой резины можно говорить об оптимуме вулканизации.
Условно производство резины можно разделить на несколько этапов. На первом этапе осуществляется подготовка ингредиентов, каучука, а также их смешивание. Затем проводят шприцевание резиновой смеси, чтобы получить заготовки. Следующие этапы — непосредственно вулканизация и заключительная механическая обработка деталей.
Различные РТИ могут характеризоваться различными свойствами. Многое зависит от процесса производства.
Соблюдение технологий производства резины предполагает использование при вулканизации не чистого каучука, а смеси этого материала с различными модификаторами, добавками, позволяющими добиваться получения как раз нужных свойств резины. К таким добавкам и модификаторам относятся мел, сажа, разнообразные смягчители и так далее.
Катализаторам при производстве резины уделяется особое внимание, так как катализаторы отвечают и за существенное ускорение самого процесса вулканизации. Как уже было сказано выше, в качестве катализаторов могут выступать различные вещества, но нужно понимать, что от разновидности катализатора, от количества вещества, участвующего в процессе вулканизации будет напрямую зависеть скорость протекания процесса и, разумеется, свойства, характеристики готового материала.
Виды вулканизации
Как правило, процесс вулканизации осуществляется при высоких температурах, которые могут достигать 140°–300°С («горячая вулканизация»), однако, если речь идет о производстве герметиков, температура может составлять и около 20°С (такой процесс называют «холодной вулканизацией»).
Нагревается каучук также и при использовании обычной серы — серая вулканизация является оптимальным выходом из положения, если в качестве исходного сырья выступают диеновые каучуки. Данная технология применяется при создании камер для автомобилей, определенных видов обуви, а также при создании различных резиновых изделий.
И еще один интересный момент: вулканизация может осуществляться также и благодаря ионизирующей радиации. В сочетании с серной вулканизацией эта технология позволяет получать не просто резину, но материал, характеризующийся повышенной степенью термостойкости.
Этапы производства РТИ и оборудование
Итак, на первом этапе, стадии подготовки ингредиентов и каучука, снимается первичная упаковка с каучука, затем материал режется на куски и укладывается на поддон. Участвующие в производстве твердые составляющие растариваются и отправляются на взвешивание.
Затем идет этап смешения. Резиновая смесь готовится на смесительных вальцах — на вальцы подаются ингредиенты, где они и смешиваются. В процессе смешивания в смесь вводятся активаторы, противостарители, вулканизаторы, пластификаторы и так далее. В виде листов резиновая смесь подается на шприц-машину. Если изготавливаются формовые изделия методом прессования, заготовки шприцуются в червячной машине, после чего разрезаются на определенной длины отрезки на станке. Заготовки отправляются в приемный бункер, и уже отсюда они периодически выгружаются и отправляются в вулканизационный пресс.
В процессе вулканизации участвуют вулканизационный пресс верхнего давления и вулканизационный котел. Котлы представляют собой обечайку с 2мя днищами. Резиновая смесь находится на тележке: с помощью подъемного моста рельсы совмещают и тележка закатывается в котел, закрывается крышка и начинается процесс вулканизации с повышением температуры и давления. После окончания процесса давление снижается, в байонетном затворе поворачивается ключ, позволяя открыть днище.
При производстве РТИ сложной формы с высокой плотностью обычно используют формовой метод вулканизации в прессах, сочетающий в себе одновременно формование с помощью метода компрессионного прессования и последующую вулканизацию под давлением.
Гидравлические вулканизационные прессы оснащаются контрольно-измерительными приборами — регуляторами давления и терморегуляторами. Прессом можно упрапвлять при помощи специальной коробки в автоматическом или полуавтоматическом режиме.
Виды РТИ и особенности их производства
Резинотехнические изделия в зависимости от способа производства делятся на две большие группы: формовые РТИ и неформовые.
Формовые резинотехнические изделия производятся в специальных формах с помощью вулканизации резиновой смеси, могут такие изделия получаться и методом литья под давлением. Область использования формовых изделий очень широка — они применяются во всех существующих сегодня видах промышленности.
Что касается производства неформовых резинотехнических изделий, то оно осуществляется в два этапа. На первом этапе осуществляется экструзия резиновой смеси в специальной пресс форме, затем проводится вулканизация суррогата. Неформовые резинотехнические изделия активно используются в автомобильной и судовой промышленности, в вагоностроении, авиастроении в качестве уплотнителей или средств герметизации стыков.
Мы не только предлагаем своим клиентам различные марки активно используемых в современной промышленности резин и производство резины пористой, но также готовы разработать рецептуры по техническому заданию заказчика. Обращаясь к нам, вы можете рассчитывать на оперативность, высокое качество, полное соответствие вашим требованиям, доступную стоимость. Мы ждем вас!
ТЕМА: ТЕХНОЛОГИЯ ИЗГОТОВЛЕНИЯ РЕЗИНОВЫХ ИЗДЕЛИЙ Лекция 23 23.1. Технология изготовления резиновых изделий Резины — пластмассы с редкосетчатой структурой, в которых связующим выступает полимер, находящийся в высокопластическом состоянии. В резинах связующим являются каучуки натуральные (НК) или синтетические (СК). Каучукам присуща высокая пластичность, обусловленная особенностями строения их молекул. Линейные и слаборазветвленные молекулы каучуков имеют зигзагообразную или спиралевидную конфигурацию и отличаются Чистый каучук ползет при комнатной температуре особенно при повышенной, хорошо растворяется в органических растворителях. В процессе эксплуатации под воздействием внешних факторов (свет, температура, озон, кислород, радиация и др.) резины изменяют свом свойства — стареют. Старение резин оценивают коэффициентом старения. Определяют, выдерживая стандартизованные образцы в термостате при температуре -70 °С в течение 144 ч, что соответствует естественному старению резины в течение 3 лет: 23.2. Технология приготовления резиновых смесей и формообразования деталей из резины Помимо основы — каучуков — в состав резин вводят: вулканизирующие вещества, ускорители вулканизации, наполнители, пластификаторы и красители. Вулканизирующие вещества (сера, оксиды цинка или магния и нитросоединения) непосредственно участвуют в образованна связей между макромолекулами. Их содержание в резинах составляет 5—7%, а в твердых резинах, например эбоните, — до 30%. Наполнители по воздействию на каучуки подразделяют на активные и инертные. Активные наполнители (сажа, оксид кремния) повышают твердость и прочность резины и увеличивают ее сопротивление истиранию. Инертные наполнители (тальк, мел и др.) вводят в состав резин с целью их удешевления. Пластификаторы (вазелин технический, парафин, стеариновая кислота, минеральные и растительные масла и т. д.), присутствуя в составе резин (8—30%), облегчают их переработку, увеличивают эластичность и морозостойкость. Противостарители замедляют процесс старения резни, препятствуют присоединению кислорода. В результате макромолекулы каучука разрываются на части, укорачиваются. Это приводит к потере эластичности, охрупчиванию и появлению сетки трещин на поверхности. Красители (охра, ультрамарин) выполняют не только декоративные функции, но в задерживают световое старение, поглощая коротковолновую часть света. Решающая роль в формировании основных свойств резин принадлежит каучукам. Натуральный каучук получают из сока (латекса), извлекаемого из стволов каучуковых деревьев. В латексе содержится 30 — 37% каучука, частицы которого имеют округлую форму диаметром 0,14 — 0,6 мкм. Каучук из латекса выделяют коагуляцией с помощью органических кислот (муравьиной или уксусной). Затем рыхлый сгусток промывают водой, раскатывают в листы и сушат. Наибольшее распространение получили сорта натурального каучука смокед шит янтарного цвета и светлого крена. Натуральный каучук — мягкий эластичный материал плотностью 0,91—0,94 г/см . При температуре -70 °С натуральный каучук утрачивает эластичность и становится хрупким. Нагрев натурального каучука выше 70 °С делает его пластичный, а при температуре выше 200 °С он разлагается. Резины на основе натурального каучука имеют высокую прочность и эластичность, высокие электроизоляционные свойства. Более широкое применение в производстве резин получили синтетические каучуки, отличающиеся разнообразием свойств. Синтетические каучук получают из спирта, нефти, попутных газов нефтедобычи, природного газа и т., Бутадиеновый каучук. Это некристаллизующийся каучук, отличающийся пониженной прочностью при растяжении, растворимый в неорганических растворителях. Морозостойкость бутадиенового каучука невысокая и находится в пределах от -40 до -50 °С. СКБ каучук чаще идет на изготовление специальных резин. Бутадиеннитрильный каучук. 23.3. Приготовление резиновых смесей и формообразование деталей из резины Технология приготовления резиновых смесей состоит из ряда операций выполняемых в определенной последовательности. Основные операции- подготовка ингредиентов, их смешивание и получение полуфабриката требуемой формы. Перед смешиванием ингредиентов каучук нарезают на куски и пластифицируют путем многократного пропускания через нагретые до 40—50 °С валки. Таким образом улучшают способность каучука смешиваться с другими составляющими. При смешивании строго соблюдают не только отленные пропорции, но и последовательность смешивания ингредиентов. Первым обычно вводят в смесь противостарители, а последними —вулканизаторы (серу или оксиды цинка, магния) и ускорители вулканизации. Процесс смешивания проводят в резиносмесителях закрытого типа или на вальцовочных машинах. Каландрование резиновых смесей проводят на специальных машин каландрах — и получают в результате сырую резину в виде листов или лент определенной толщины. По конструкции каландры представляют трехвалковую клеть листопрокатного стана. Два валка, верхний и средний, имеют температуру 60—90 °С, а нижний — 15 °С. Резиновая масса, проходя в между верхними валками, нагревается, обволакивает средний валок и выходит через зазор между средним и нижним валками. Листы каландреванной сырой резины (не вулканизированной) наматывают на деревянные бобины, предварительно разделив прокладочной бумагой и тем самым предотвращая их слипание. В таком виде сырая резина сохраняться при 5—20 °С до трех месяцев, а отдельные виды резин шести месяцев. 23.4. Формообразование деталей из резины Из сырой резины методами прессования и литья под давлением изготавливают детали требуемой формы и размеров. Каждый метод имеет ему присущие технологические возможности и применяется для изготовления определенного вида деталей. Прессование. Детали из сырой резины формуют в специальных пресс-формах на гидравлических прессах под давлением 5—10 МПа. Заготовка укладывается в пресс-форму, если необходимо, то с армирующим материалом, и под действием давления принимает необходимую форму. В случае, если прессование проходило в холодном состоянии, отформованное изделие затем подвергают вулканизация. При. горячем прессовании с формовкой протекает вулканизация. Изготавливают уплотнительные кольца, муфты, клиновые ремни. Литье под давлением — более прогрессивный истод, В этом случае форма заполняется предварительно разогретой пластичной сырой резиновой смесью под давлением 30—150 МПа. Резиновая смесь приобретает форму, соответствующую рабочей полости формы. Прочность резиновых изделий увеличивается при армировании их стенок стальной проволокой, сеткой, капроновой или стеклянной нитью. Сложные изделия — автопокрышки, гибкие бронированные шланги и рукава — получают методом последовательной намотки на полый металлический стержень слоев резины и изолирующих и армирующих материалов (ткань, металлическая проволоках). Вулканизация. Горячую вулканизацию проводят в котлах, в прессах-автоматах, на непрерывного действия под давлением при строгом температурном режиме в пределах 130—150 «С. Вулканизационной средой могут быть горячий воздух, водяной пар, горячая вода, расплав соли. При вулканизации имеет место химическое взаимодействие каучука с вулканизирующим веществом (серой, пероксидными или ми соединениями) по месту двойной связи: Вулканизацию возможно проводить при комнатной температуре. В этом случае сера отсутствует в составе сырой резины, а изделие обрабатывают в растворе или рарах дихлорида серы или в атмосфере сернистого газа. Осуществлять вулканизацию можно с помощью сверхвысокочастотного или у-излучения, В результате вулканизации увеличиваются прочность и упругость резины, сопротивление старению, действию различных органических растворителей, изменяются электроизоляционные свойства. Резинам свойственна большая обратимая деформация, достигающая 1000%, при сравнительно низких напряжениях. Нагрев, как правило, снижает прочностные свойства резин. При низких отрицательных температурах резины практически полностью утрачивают высокоэластичные свойства и переходят в стеклообразное состояние. |
Что такое натуральный каучук и почему мы ищем новые источники? · Frontiers for Young Minds
Abstract
Что такое каучук и откуда он берется? Каучук — это натуральный продукт, производимый растениями, и он присутствует во многих товарах, используемых в нашей повседневной жизни. Каучук играл важную роль в истории человечества на протяжении всего развития человеческих цивилизаций. Он по-прежнему играет важную роль, поэтому нам необходимо искать новые источники каучука. В настоящее время 99% натурального каучука, который мы используем, добывается из дерева под названием 9.0005 Гевея бразильская . В этой статье мы даем некоторые подробности о лучших альтернативных источниках каучука, доступных в настоящее время.
Что такое натуральный каучук?
Натуральный каучук производится из растений и классифицируется как полимер . Полимер — это химическое соединение, в котором большие молекулы состоят из множества меньших молекул того же типа. Некоторые полимеры существуют в природе, а другие производятся в лабораториях и на заводах.
Натуральный каучук является одним из наиболее важных полимеров для человеческого общества. Натуральный каучук является важным сырьем, используемым при создании более 40 000 продуктов. Он используется в медицинских приборах, хирургических перчатках, авиационных и автомобильных шинах, пустышках, одежде, игрушках и т. д. Натуральный каучук получают из латекс , жидкость молочного цвета, присутствующая либо в латексных сосудах (протоках), либо в клетках растений, производящих каучук. Около 20 000 видов растений производят латекс, но только 2 500 видов содержат каучук в своем латексе. Биологическая функция каучука для растений до конца не известна. Однако было показано, что каучук может помочь растениям зажить после их повреждения, покрывая раны и останавливая кровотечение. Это блокирует проникновение вредоносных бактерий и вирусов в растения.
К свойствам каучука относятся высокая прочность и способность многократно растягиваться без разрыва. Натуральные каучуковые смеси обладают исключительной эластичностью, хорошими электроизоляционными свойствами и устойчивы ко многим коррозионно-активным веществам [1].
Синтетический (искусственный) каучук можно производить с помощью химического процесса, но люди не смогли произвести синтетический каучук, обладающий всеми свойствами натурального каучука. Таким образом, натуральный каучук не может быть заменен синтетическим каучуком в большинстве его применений. Вот почему натуральный каучук по-прежнему очень важен для человеческого общества [2].
История натурального каучука
Еще в 1600 г. до н.э. народы Мезоамерики в Мексике и Центральной Америке использовали жидкий каучук для изготовления лекарств, в ритуалах и для рисования. Только после завоевания Америки использование каучука достигло западного мира. Христофор Колумб был ответственен за поиск каучука в начале 1490-х годов. Туземцы с Гаити играли в футбол мячом из резины, а позже, в 1615 году, Фрай Хуан де Торквемада писал о коренных и испанских поселенцах Южной Америки, которые носили обувь, одежду и головные уборы, сделанные путем погружения ткани в латекс, что делало эти предметы более прочными и водонепроницаемыми. . Но у резины были некоторые проблемы: в теплую погоду она становилась липкой, а в холодную — твердела и трескалась.
Столетие спустя, в 1734 году, Шарль Мари де ла Кондамин отправился в путешествие по Южной Америке. Там он нашел два разных дерева, содержащих латекс: Hevea brasiliensis (рис. 1B) и Castilla elastica
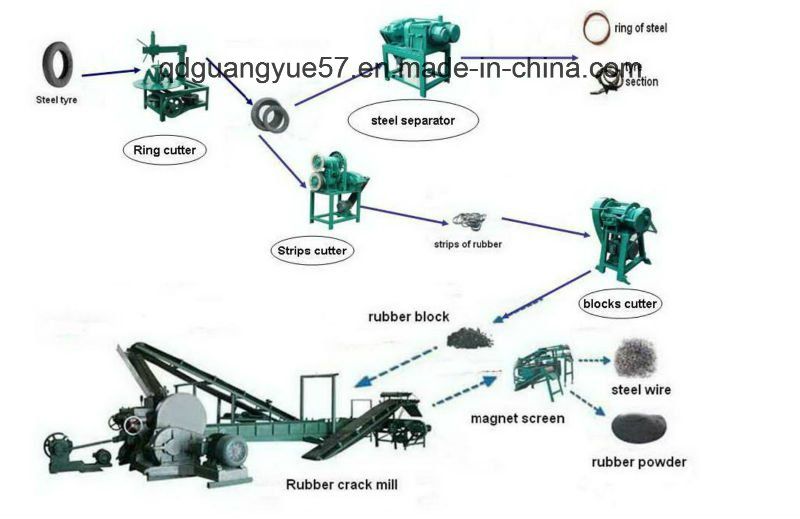
- Рисунок 1 — (A) Hevea brasiliensis срез ствола и увеличение продольного среза соединенных трубок.
- (B) A Плантация Hevea brasiliensis и рисунок листьев, цветов и плодов этого растения.
- Рисунок 2 — Hevea brasiliensis со специальным разрезом для извлечения латекса.
В 1839 году Чарльз Гудиер изобрел вулканизацию , решающий многие проблемы, связанные с резиной. Вулканизация — это процесс обработки каучука серой и теплом для его упрочнения при сохранении эластичности. Предотвращает плавление резины летом и растрескивание зимой. Через несколько лет после этого важного открытия, в 1888 году, Данлоп изобрел резиновую шину, наполненную воздухом, что сделало резину чрезвычайно важным сырьем во всем мире. Резина стала важным материалом для промышленной революции.
С 1850 по 19 гг.20 марта бизнесмены подталкивали предпринимателей и торговцев к увеличению количества каучука, добываемого из амазонских деревьев. В этот период бразильская Амазонка была единственным источником каучука, и они контролировали цены, что делало каучук дорогим. В то же время, по мере развития промышленности в Европе и США, каучуку находили все больше применений [4]. Каучук был настолько важным материалом для бразильцев, что они запретили экспорт семян или саженцев каучука. Однако в 1876 году Х. А. Уикхему удалось контрабандой переправить 70 000 семян каучука, спрятанных в банановых листьях, и привезти их в Англию. Из тех семян только 1,900 саженцев выжили и были отправлены в Малайзию, чтобы начать первые плантации каучука в Азии. Это стало началом конца Бразилии как основного производителя каучука в мире. Спустя 12 лет производство каучука на новых плантациях в Малайзии стало таким же конкурентоспособным, как и на Амазонии, и вскоре эти плантации стали основным мировым поставщиком натурального каучука (рис.
- Рисунок 3 — (A) Hevea brasiliensis возникла на Амазонке и попала в Малайзию, основного производителя натурального каучука.
- (B) Гевея бразильская . (C) Альтернативный источник каучука, гваюла ( Parthenium argentatum ). (D) Альтернативный источник каучука, казахский одуванчик ( Taraxacum koksaghyz ).
Генри Николас Ридли был ученым, который стал директором Сингапурского ботанического сада в 1888 году. Работая там, он обнаружил первые 11 каучуковых деревьев, посаженных в Малайзии, и начал продвигать создание плантаций каучуковых деревьев. Некоторое время спустя он разработал революционный метод сбора латекса из Дерево гевеи путем непрерывного постукивания. Выстукивание — это процесс удаления латекса с дерева. Это открытие позволило достичь гораздо более высокого выхода латекса, и каучук стал важным материалом в развитии Сингапура. Новые плантации были более конкурентоспособны по цене, поэтому с конца девятнадцатого века до Первой мировой войны сбор каучука из диких источников в тропической Америке резко сократился. Во время войны поставки каучука были прекращены. США, Германия и Россия начали поиск альтернативных источников каучука, натурального или синтетического, поскольку амазонские деревья не давали достаточного количества каучука для своих нужд [3]. В этих странах было запущено несколько исследовательских программ, но после войны поставки каучука с малайзийских плантаций возобновились, и усилия по поиску новых источников каучука почти прекратились.
В настоящее время около 90% натурального каучука производится в Азии, при этом Таиланд и Индонезия являются наиболее важными поставщиками каучука (поставляют более 60% натурального каучука в мире).
Почему мы ищем новые источники каучука?
В последние годы снова начался поиск альтернативных источников каучука. Этому есть три основные причины:
1. Угрозы Hevea brasiliensis дереву и его производству каучука
Во-первых, каучуковые деревья подвержены нескольким заболеваниям, а поскольку азиатские каучуковые плантации начинались всего с нескольких семян, все деревья генетически очень похожи. Меньшая генетическая изменчивость означает более низкую способность бороться с болезнями растений. Если одно дерево заболевает, болезнь может быстро распространиться на всю плантацию. На сегодняшний день наиболее важным и опасным заболеванием, от которого страдает Hevea brasiliensis , называется южноамериканская пятнистость листьев. Это заболевание может привести к опустошению целой плантации. Он по-прежнему ограничен тропической Америкой, но если он прибудет в Азию, это может означать конец каучуковых плантаций. В естественных условиях каучуковые деревья обычно растут с большим пространством между ними. В природе серьезные повреждения до Hevea от южноамериканской пятнистости листьев является необычным, поскольку другие виды деревьев, растущие между каучуковыми деревьями, не восприимчивы к болезни и действуют как барьеры. Но на плантациях, где каучуковые деревья растут очень близко друг к другу, он может стать смертельным.
Во-вторых, серьезной угрозой для рынка натурального каучука является очень конкурентный и быстрорастущий рынок пальмового масла и его побочных продуктов. Растет спрос как на каучук, так и на пальмовое масло, но в Малайзии площади, на которых выращивается бразильская гевея, не уменьшаются, однако площади, предназначенные для выращивания масличной пальмы, увеличиваются. Если непрерывный рост плантаций масличной пальмы не остановится, либо естественный лес, либо Плантации гевеи должны уменьшиться, чтобы освободить место для новых культур масличных пальм.
И последнее, но не менее важное: врезка резины – малооплачиваемая и трудная работа. Молодые люди, как правило, выбирают более привлекательную работу, что может привести к нехватке квалифицированных сборщиков каучука.
2. Каучук из Hevea brasiliensis может вызвать серьезную аллергию
Протеины латекса в каучуке, изготовленном из Hevea brasiliensis может вызвать сильную аллергию у некоторых людей, даже если они подвергаются воздействию очень малых количеств. Белки латекса очень трудно отделить от каучука в процессе очистки. Поскольку эти аллергии могут быть очень опасными, альтернатива каучуку, которая не содержит эти латексные белки, была бы выгодной.
3. Hevea brasiliensis производится только в одном районе
Условия, необходимые для выращивания этих каучуковых деревьев, очень специфичны и встречаются только в определенных регионах мира. Большая часть нашего натурального каучука производится в небольшом регионе Азии, что делает поставки уязвимыми к повреждениям. Если азиатские плантации не смогут производить достаточно каучука, мировых запасов каучука может не хватить. Было бы полезно найти другие растения, производящие каучук, которые можно было бы выращивать в других регионах мира.
Существуют ли альтернативные источники каучука?
Не все каучукосодержащие заводы производят качественный каучук. Некоторые растения, которые рассматривались в качестве альтернативных источников каучука, включают гваюлу, русский одуванчик, каучуковую щетку, золотарник, подсолнечник, смоковницу и салат. Два из этих растений кажутся лучшими альтернативами Hevea brasiliensis : гваюла и русский одуванчик.
Guayule ( Parthenium argentatum ) — местный кустарник северного плоскогорья Мексики, который обычно растет на известняковых почвах в районах с очень малым количеством осадков (рис. 3C). Гуаюла лучше всего растет при температуре от 18 до 49 градусов.0,5°С. В этих условиях он может прожить 30–40 лет. Каучук содержится в стеблях и корнях гваюлы, а также в отдельных клетках растения, а не в латексных сосудах или трубках. Содержание каучука в гваюле увеличивается в течение нескольких лет. Менее 1% каучука в мире производится из гваюлы. Каучук этого растения изучается для биомедицинских применений, поскольку он не вызывает аллергии. Чтобы извлечь каучук из растения, ткань гваюлы необходимо тщательно размягчить и раздробить, чтобы освободить частицы каучука, содержащиеся в отдельных клетках. Качество каучука из гваюлы недостаточно для всех целей, потому что в нем больше примесей, чем в каучуке из Гевея бразильская .
Другой хороший вариант каучука, русский или казахский одуванчик ( Taraxacum koksaghyz ), быстрорастущее растение с высококачественным каучуком, которое было обнаружено в 1931 году в Казахстане (рис. 3D). Казахский одуванчик растет очень близко к земле, его можно выращивать в регионах с умеренными температурами, и он дает желтые цветочные головки (они выглядят как цветок, но представляют собой плотную группу маленьких цветков без стебля). Казахский одуванчик содержит каучук в листьях, цветках и корнях, но только каучук в корнях пригоден для экстракции из-за его более высокого качества и количества. Для Экстракт каучука , Российские одуванчики должны быть либо прессованы, либо смешаны [5]. У казахских одуванчиков есть еще одно преимущество — они также производят углевод, называемый инулином, который представляет собой вещество, которое можно использовать в пищевых продуктах, а также для производства лекарств от рака, биотоплива или даже биопластиков (пластиков, изготовленных из натуральных продуктов). На данный момент добывать каучук из казахских одуванчиков все еще слишком дорого. Мы надеемся, что благодаря исследованиям можно будет разработать растение с более крупным корнем и более высоким содержанием каучука.
Заключение
Несмотря на то, что каучуковое дерево является лучшим доступным на сегодняшний день источником каучука, оно сталкивается с некоторыми серьезными угрозами. Каучук производится только из растений, выращенных в определенных уникальных районах. Чтобы расширить источники натурального каучука и избежать опасностей ограниченного производства, мы должны искать новые каучукосодержащие заводы и совершенствовать уже известные, чтобы попытаться сделать их экономически конкурентоспособными.
Глоссарий
Полимер : ↑ Химическое соединение с большими молекулами, состоящими из множества меньших молекул того же вида. Некоторые полимеры существуют в природе, а другие производятся в лабораториях и на заводах.
Латекс : ↑ Беловатая молочная жидкость, содержащая белки, крахмал, алкалоиды и т. д., вырабатываемая многими растениями. В некоторых растениях он также содержит каучук.
Hevea Brasiliensis : ↑ Это дерево произрастает на Амазонке. Это очень важно с экономической точки зрения, потому что латекс, собранный с дерева, является основным источником натурального каучука.
Вулканизация : ↑ Процесс обработки каучука серой и теплом для его упрочнения при сохранении его эластичности.
Выстукивание резины : ↑ Процесс сбора латекса с каучукового дерева. Перед восходом солнца в коре дерева делают сборную бороздку, а латекс собирают ближе к вечеру.
Извлечение каучука : ↑ Действие по получению или отделению каучука от ткани корня.
Заявление о конфликте интересов
Авторы заявляют, что исследование проводилось при отсутствии каких-либо коммерческих или финансовых отношений, которые могли бы быть истолкованы как потенциальный конфликт интересов.
Благодарности
Мы хотели бы поблагодарить Наталью Карреро, Лауру Баркер и Марселя Принса за их вклад в рецензирование текста.
Проект AIR получил финансирование от исследовательской и инновационной программы Horizon 2020 Европейского Союза в рамках соглашения о гранте Марии Склодовской-Кюри № 7529.21.
Каталожные номера
[1] ↑ Виджаярам, Т. Р. 2009. Технический обзор резины. Междунар. Дж. Дес. Произв. Тех. 3:25–36.
[2] ↑ Ван Бейлен, Дж., и Пуарье, Ю. 2007. Гуаюла и русский одуванчик как альтернативные источники натурального каучука. Крит. Преподобный Биотех. 27:217–31. дои: 10.1080/07388550701775927
[3] ↑ Whaley, WG 1948. Каучук — основной источник производства в Америке. Экон. Бот. 2: 198–216. дои: 10.1007/BF02859004
[4] ↑ Уллан де ла Роса, FJ 2004. Эпоха каучо в Амазонасе (1870–1920): modelos de explotación y relaciones sociales de producción. Анал. Мус. Являюсь. 12:183–204.
[5] ↑ ван Бейлен, Дж., и Пуарье, Ю. 2007. Создание новых культур для производства натурального каучука. Тенденции биотехнологии. 25:522–9. doi: 10.1016/j.tibtech.2007.08.009
Процесс производства резины
В конце 1930-х годов Соединенные Штаты использовали более половины мировых запасов натурального каучука. Сегодня натуральный каучук можно найти в более чем 50 000 промышленных товаров в Соединенных Штатах, и США ежегодно импортируют более 3 миллиардов фунтов натурального каучука. Однако более 70 процентов каучука, используемого в современных производственных процессах, представляет собой синтетический каучук.
Фон из натурального каучука
Натуральный каучук начинается с латекса. Латекс состоит из полимера, называемого полиизопреном, взвешенного в воде. Молекулы с длинной цепью, состоящие из множества (поли) отдельных звеньев (меров), соединенных вместе, образуют полимеры. Резина — это особая форма полимера, называемая эластомером, что означает, что молекулы полимера растягиваются и изгибаются.
Более 2500 заводов производят латекс, материал, похожий на молочный сок. Молочай может быть самым знакомым растением, производящим латекс, для многих людей, но коммерческий латекс получают из одного тропического дерева, Hevea brasiliensis. Как следует из названия, каучуковое дерево родом из тропиков Южной Америки. Более 3000 лет назад мезоамериканские цивилизации смешивали латекс с соком ипомеи для создания каучука. Изменение соотношения латекса и сока ипомеи изменило свойства каучука. От надувных мячей до резиновых сандалий жители Мезоамерики знали и использовали каучук.
До 1900 года большая часть натурального каучука производилась из диких деревьев в Бразилии. В начале 20-го века спрос и предложение опережали производство с ростом популярности велосипедов и автомобилей. Семена, вывезенные контрабандой из Бразилии, привели к появлению плантаций каучуковых деревьев в Юго-Восточной Азии. К 1930-м годам использование натурального каучука варьировалось от шин на транспортных средствах и самолетах до 32 фунтов, используемых в солдатской обуви, одежде и снаряжении. К тому времени большая часть поставок каучука в США поступала из Юго-Восточной Азии, но Вторая мировая война отрезала США от большей части его поставок.
Процесс производства натурального каучука
Процесс производства натурального каучука начинается со сбора латекса из каучуковых деревьев. Сбор латекса с каучуковых деревьев начинается с надрезания или разрезания коры дерева. Латекс стекает в чашу, прикрепленную к нижней части выреза в дереве. Латексный материал многих деревьев накапливается в больших резервуарах.
В наиболее распространенном методе извлечения каучука из латекса используется коагуляция – процесс, при котором полиизопрен свертывается или сгущается в массу. Этот процесс осуществляется путем добавления в латекс кислоты, такой как муравьиная кислота. Процесс коагуляции занимает около 12 часов.
Вода выдавливается из сгустка резины с помощью ряда роликов. Полученные тонкие листы толщиной около 1/8 дюйма сушат на деревянных стеллажах в коптильнях. Процесс сушки обычно занимает несколько дней. Полученная темно-коричневая резина, которая теперь называется ребристым дымовым листом, складывается в тюки для отправки на переработку.
Однако не вся резина дымится. Каучук, высушенный горячим воздухом, а не копчением, называется листом воздушной сушки. Этот процесс приводит к более качественному каучуку. Каучук еще более высокого качества, называемый светлым креп-каучуком, требует двух стадий коагуляции с последующей сушкой на воздухе.
Создание синтетического каучука
За прошедшие годы было разработано несколько различных типов синтетического каучука. Все они являются результатом полимеризации (связывания) молекул. Процесс, называемый аддитивной полимеризацией, связывает молекулы в длинные цепи. Другой процесс, называемый конденсационной полимеризацией, удаляет часть молекулы, поскольку молекулы связаны друг с другом. Примеры аддитивных полимеров включают синтетические каучуки, изготовленные из полихлоропрена (неопренового каучука), маслостойкой и бензостойкой резины, а также бутадиен-стирольный каучук (SBR), используемый для изготовления неотскакивающей резины в шинах.
Первые серьезные поиски синтетического каучука начались в Германии во время Первой мировой войны. Британская блокада не позволила Германии получить натуральный каучук. Немецкие химики разработали полимер из звеньев 3-метилизопрена (2,3-диметил-1,3-бутадиена), [CH 2 =C(CH 3 )C(CH 3 )=Ch3], из ацетона. . Хотя этот заменитель, метилкаучук, уступал натуральному каучуку, к концу Первой мировой войны Германия производила 15 тонн в месяц.
Непрерывные исследования привели к созданию синтетических каучуков более высокого качества. Наиболее распространенный тип синтетического каучука, используемый в настоящее время, Buna S (стирол-бутадиеновый каучук или SBR), был разработан в 1929 немецкой фирмы I. G. Фарбен. В 1955 году американский химик Сэмюэл Эмметт Хорн-младший разработал полимер, состоящий на 98% из цис-1,4-полиизопрена, который ведет себя как натуральный каучук. Это вещество в сочетании с бутадиен-стирольным каучуком используется для изготовления шин с 1961 года.
Резина для переработки
Каучук, натуральный или синтетический, поступает на перерабатывающие заводы в больших тюках. Как только каучук поступает на завод, обработка проходит четыре этапа: компаундирование, смешивание, формование и вулканизация. Состав резиновой смеси и метод зависят от предполагаемого результата процесса изготовления резины.
Компаундирование
В компаундирование добавляются химикаты и другие добавки, чтобы настроить резину для предполагаемого использования. Натуральный каучук меняется в зависимости от температуры, становясь ломким от холода и липким, липким от жары. Химические вещества, добавляемые во время компаундирования, реагируют с каучуком во время процесса вулканизации, стабилизируя полимеры каучука. Дополнительные добавки могут включать армирующие наполнители для улучшения свойств каучука или неармирующие наполнители для расширения каучука, что снижает стоимость. Вид используемого наполнителя зависит от конечного продукта.
Наиболее часто используемым армирующим наполнителем является технический углерод, получаемый из сажи. Углеродная сажа повышает прочность резины на растяжение и устойчивость к истиранию и разрыву. Углеродная сажа также повышает устойчивость резины к разрушению ультрафиолетом. Большинство резиновых изделий имеют черный цвет из-за наполнителя сажи.
В зависимости от планируемого использования каучука другие используемые добавки могут включать безводные алюмосиликаты в качестве армирующих наполнителей, другие полимеры, переработанный каучук (обычно менее 10 процентов), соединения, снижающие усталость, антиоксиданты, химические вещества, устойчивые к озону, красящие пигменты. , пластификаторы, смягчающие масла и смазки для форм.
Смешивание
Добавки должны быть тщательно смешаны с каучуком. Высокая вязкость (сопротивление течению) каучука затрудняет смешивание без повышения температуры каучука достаточно высоко (до 300 градусов по Фаренгейту), чтобы вызвать вулканизацию. Для предотвращения преждевременной вулканизации смешивание обычно происходит в две стадии. На первом этапе в каучук вмешиваются такие добавки, как сажа. Эта смесь называется маточной смесью. Когда каучук остынет, в него добавляют химические вещества для вулканизации и смешивают с каучуком.
Формование
Формование резиновых изделий происходит с использованием четырех основных методов: экструзии, каландрирования, нанесения покрытия или формования и литья. В зависимости от конечного продукта можно использовать более одной техники формования.
Экструзия заключается в продавливании высокопластичной резины через ряд шнековых экструдеров. При каландрировании резина проходит через ряд все более узких зазоров между валками. Роликовый процесс сочетает в себе экструзию и каландрирование, производя продукт лучшего качества, чем любой из этих процессов по отдельности.
При нанесении покрытия используется процесс каландрирования для нанесения слоя резины или вдавливания резины в ткань или другой материал. Шины, водонепроницаемые тканевые палатки и плащи, конвейерные ленты, а также надувные плоты изготавливаются путем обмазки материалов резиной.
Резиновые изделия, такие как подошвы и каблуки для обуви, прокладки, уплотнители, присоски и пробки для бутылок, отливают с использованием форм. Формование также является этапом изготовления шин. Три основных метода формования резины — это компрессионное формование (используемое, среди прочего, при производстве шин), трансферное формование и литье под давлением. Вулканизация каучука происходит в процессе формования, а не как отдельный этап.
Вулканизация
Вулканизация завершает процесс производства каучука. Вулканизация создает перекрестные связи между полимерами каучука, и процесс варьируется в зависимости от требований к конечному резиновому изделию. Меньшее количество перекрестных связей между полимерами каучука делает резину более мягкой и податливой. Увеличение количества поперечных связей снижает эластичность резины, в результате чего резина становится более твердой. Без вулканизации резина оставалась бы липкой в горячем состоянии и ломкой в холодном состоянии и гнила бы гораздо быстрее.
Вулканизация, первоначально открытая в 1839 году Чарльзом Гудиером, требовала добавления серы в каучук и нагревания смеси до 280 F в течение примерно пяти часов. Современная вулканизация, как правило, использует меньшее количество серы в сочетании с другими химическими веществами, чтобы сократить время нагрева до 15-20 минут. Были разработаны альтернативные методы вулканизации, в которых не используется сера.
каучук | Тропические растения, нефть и природный газ
грузовые шины извлекаются из форм
Посмотреть все СМИ
- Ключевые люди:
- Тан Ченг Лок Пол В. Личфилд Генри Николас Ридли Джованни Баттиста Пирелли Карл Дитрих Харрис
- Похожие темы:
- полиизопрен латекс вулканизация гуттаперча поролон
Просмотреть весь связанный контент →
Резюме
Прочтите краткий обзор этой темы
каучук , эластичное вещество, полученное из выделений некоторых тропических растений (натуральный каучук) или полученное из нефти и природного газа (синтетический каучук). Из-за своей эластичности, устойчивости и прочности резина является основным компонентом шин, используемых в автомобильных транспортных средствах, самолетах и велосипедах. Более половины всего производимого каучука идет на автомобильные шины; остальное идет на механические детали, такие как крепления, прокладки, ремни и шланги, а также на потребительские товары, такие как обувь, одежда, мебель и игрушки.
Основными химическими компонентами каучука являются эластомеры, или «эластичные полимеры», большие молекулы, похожие на цепи, которые могут растягиваться на большие длины и при этом восстанавливать свою первоначальную форму. Первым распространенным эластомером был полиизопрен, из которого изготавливают натуральный каучук. Натуральный каучук, образующийся в живом организме, состоит из твердых частиц, взвешенных в жидкости молочного цвета, называемой латексом, которая циркулирует во внутренних частях коры многих тропических и субтропических деревьев и кустарников, но преимущественно 9. 0338 Hevea brasiliensis , высокое дерево хвойных пород, происходящее из Бразилии. Натуральный каучук был впервые научно описан Шарлем-Мари де Ла Кондамин и Франсуа Френо из Франции после экспедиции в Южную Америку в 1735 году. Английский химик Джозеф Пристли дал ему название «каучук» в 1770 году, когда обнаружил, что им можно стирать карандаши. Метки. Большой коммерческий успех пришел к нему только после того, как в 1839 году Чарльз Гудиер изобрел процесс вулканизации.
Натуральный каучук и сегодня продолжает занимать важное место на рынке; его устойчивость к накоплению тепла делает его ценным для шин, используемых на гоночных автомобилях, грузовиках, автобусах и самолетах. Тем не менее, он составляет менее половины промышленно производимого каучука; остальное — каучук, полученный синтетическим путем с помощью химических процессов, которые были частично известны в 19 веке.го века, но не применялись в коммерческих целях до второй половины 20 века, после Второй мировой войны. К наиболее важным синтетическим каучукам относятся бутадиеновый каучук, бутадиен-стирольный каучук, неопрен, полисульфидные каучуки (тиоколи), бутилкаучук и силиконы. Синтетические каучуки, как и натуральные каучуки, могут быть усилены вулканизацией, улучшены и модифицированы для специальных целей путем армирования другими материалами.
Основные свойства полимеров, используемых для производства основных товарных каучуков, приведены в таблице.
Викторина «Британника»
Строительные блоки предметов повседневного обихода
Из чего сделаны сигары? К какому материалу относится стекло? Посмотрите, на что вы действительно способны, ответив на вопросы этого теста.
тип полимера | температура стеклования (°C) | температура плавления (°С) | маслостойкость* | сопротивление изгибу* | типичные продукты и области применения | |
---|---|---|---|---|---|---|
*E = отлично, G = хорошо, F = удовлетворительно, P = плохо.![]() | ||||||
полиизопрен (натуральный каучук, изопреновый каучук) | −70 | 25 | п | п | Е | шины, пружины, обувь, клеи |
стирол-бутадиеновый сополимер (стирол-бутадиеновый каучук) | −60 | п | п | грамм | протекторы шин, клеи, ремни | |
полибутадиен (бутадиеновый каучук) | −100 | 5 | п | п | Ф | протекторы шин, обувь, конвейерные ленты |
акрилонитрил-бутадиеновый сополимер (нитриловый каучук) | от −50 до −25 | грамм | грамм | Ф | прокладки топливных шлангов, ролики | |
изобутилен-изопреновый сополимер (бутилкаучук) | −70 | −5 | Ф | п | Ф | покрышки, оконные рейки |
этилен-пропиленовый мономер (EPM), этилен-пропилен-диеновый мономер (EPDM) | −55 | Ф | п | Ф | гибкие уплотнения, электрическая изоляция | |
полихлоропрен (неопрен) | −50 | 25 | грамм | грамм | грамм | шланги, ремни, пружины, прокладки |
полисульфид (тиокол) | −50 | Ф | Е | Ф | уплотнения, прокладки, ракетное топливо | |
полидиметилсилоксан (силикон) | −125 | −50 | грамм | Ф | Ф | уплотнения, прокладки, хирургические имплантаты |
фторэластомер | −10 | Е | Е | Ф | Уплотнительные кольца, уплотнения, прокладки | |
полиакрилатный эластомер | от -15 до -40 | грамм | грамм | Ф | шланги, ремни, уплотнения, ткани с покрытием | |
полиэтилен (хлорированный, хлорсульфированный) | −70 | грамм | грамм | Ф | Уплотнительные кольца, уплотнения, прокладки | |
стирол-изопрен-стирол (SIS), стирол-бутадиен-стирол (SBS) блок-сополимер | −60 | п | п | Ф | автомобильные детали, обувь, клеи | |
Смесь EPDM-полипропилен | −50 | Ф | п | Ф | обувь, гибкие чехлы |
Каучуковое дерево
В промышленных масштабах натуральный каучук получают почти исключительно из Hevea brasiliensis, дерево, произрастающее в Южной Америке, где в диком виде оно достигает высоты 34 метра (120 футов). Однако выращиваемое на плантациях дерево вырастает только до 24 метров (80 футов), потому что углерод, необходимый для роста, также является важным компонентом каучука. Поскольку только атмосферный углекислый газ может поставлять растению углерод, этот элемент необходимо распределять между двумя потребностями, когда дерево находится в активном производстве. Кроме того, с листвой, ограниченной верхушкой дерева (для облегчения постукивания), потребление углекислого газа меньше, чем у дикого дерева. Другие деревья, кустарники и травянистые растения производят каучук, но поскольку ни одно из них не сравнится по эффективности с Hevea brasiliensis, Промышленные ботаники сосредоточили свои усилия исключительно на этом виде.
При выращивании гевеи, соблюдаются естественные контуры земли, деревья защищены от ветра. Покровные культуры, посаженные рядом с каучуковыми деревьями, удерживают дождевую воду на склоне и помогают удобрять почву, фиксируя атмосферный азот. Также используются стандартные методы садоводства, такие как выращивание в питомниках выносливых подвоев и прививка к ним, ручное опыление и вегетативное размножение (клонирование) для получения генетически однородного продукта.