мокрый и сухой способ производства цемента
Сухой цемент представляет собой искусственное вещество, которое поставляется в формате порошка и используется в качестве вяжущего в процессе замешивания разного типа бетонных растворов. В момент смешивания с водой цемент провоцирует прохождение химической реакции с изменением структуры материала, который застывает и превращается в камень, обеспечивая монолиту должные характеристики прочности, стойкости, способности выдерживать механические нагрузки.
Состав цемента может быть разным, что напрямую зависит от вида вяжущего и возложенных на него функций, требуемых свойств материала. Классический цемент делают из клинкера (обожженные и спаянные в куски известняк и глина, взятые в определенной пропорции), смешанного с гипсом и различными минеральными добавками.
Что входит в состав цемента:
- Известь (оксид кальция) – около 60%.
- Кремниевый диоксид – до 20%.
- Алюминий (глинозем) – 4%.
- Гипс, оксиды железа – до 2%.
- Магния оксид – 1%.
Данное процентное соотношение актуально для портландцемента – самого распространенного вида материала. Пропорции могут меняться, в соответствии с классном и технологией производства цемента. Ввиду существования большого числа марок и видов цемента точного рецепта его производства (и химической формулы) не существует – тут все зависит от показателей минералогического состава.
Производство цемента осуществляется из клинкера – продукта обжига глины и известняка, взятых в пропорции 1:3. Клинкер представляет собой полуфабрикат для создания цемента. После обжига при высокой температуре (до 1500 градусов) клинкер мелко измельчают до гранул величиной около 6 сантиметров. Потом клинкер измельчают до порошкообразного вида, вводя различные добавки.
Что входит в состав клинкера при измельчении:
- Гипс, который регулирует длительность схватывания.
- Корректирующие добавки для улучшения определенных характеристик цемента (присадки, пластификаторы и т.
д.).
В качестве основного исходного сырья в производстве цемента используют различные горные породы – карбонатного типа (могут быть с кристаллической либо аморфной структурой, определяющей уровень эффективности взаимодействия материала с остальными компонентами состава в процессе обжига) и осадочного происхождения (глинистое сырье с минеральной базой, которое при сильном увлажнении разбухает и становится пластичным, увеличиваясь в объеме; материал вязкий, применяется при производстве сухим способом).
Основные способы производства цемента:
- 1 Мокрая технология производства цемента
- 1.1 Преимущества
- 1.2 Недостатки
- 2 Сухая технология производства
- 2.1 Плюсы технологии
- 2.2 Минусы технологии
- 3 Отличия мокрой технологии производства от сухой
- 4 Особенности полусухого способа
- 5 Комбинированный метод производства
Мокрая технология производства цемента
Производство цемента мокрым методом начинается так же, как и в любом другом случае: с добывания твердого известняка из карьеров, который потом дробят на куски разной величины. Потом куски измельчают в специальных дробильных агрегатах до тех пор, пока фракция известняка не будет равна максимум 8-10 миллиметрам.
Потом на завод доставляют глину из карьера, ее обрабатывают в вальцевых дробилках до тех пор, пока размер кусков не будет равен максимум 100 миллиметрам. Измельченную смесь глины отмачивают в болтушках до момента получения глиняного шлама влажностью в пределах 70%. Потом шлам отправляют в мельницу, где его смешивают и размалывают вместе с известняком.
Далее шлам, влажность которого находится уже на уровне 40%, отправляют в вертикальный бассейн, где осуществляется окончательный процесс корректировки. Данная операция чрезвычайно важна, так как именно тут формируется и обеспечивается правильная химическая формула состава шлама.
После проверки качества шлама его транспортируют для реализации последующих этапов: цементную массу из вертикального бассейна транспортируют в горизонтальный, где смесь хранят до того, как отправить в печь для обжига. Сырье в горизонтальном бассейне постоянно перемешивается механически с использованием сжатого воздуха. Это не позволяет шламу выпадать в осадок и дает возможность полностью гомогенизироваться.
Далее шлам отправляют на обжиг в печь, где он превращается в клинкер. Клинкерная основа, полученная в итоге, отправляется в промышленный холодильник и там охлаждается. Потом клинкер дробят, подают в емкости мельниц, повторно измельчают до состояния порошка.
В случае, когда процесс обжига шлама требует применения твердого топлива, необходимо позаботиться о строительстве дополнительного помещения (где будет храниться, готовиться уголь). Если технологическая схема производства цемента требует применения газообразного/жидкого топлива, процесс обжига клинкера упрощается.
На завершающем этапе производства цемент из бункеров мельниц направляют в специальные помещения, где он хранится. Здесь лаборанты исследуют качество продукции, определяют марку. Только по завершении проверки цемент может отправляться на упаковочные аппараты.
Преимущества
Рассматривая мокрый способ производства цемента, стоит учитывать его плюсы и минусы. Как и любой технологический процесс, данный обладает своими особенностями.
Ключевые достоинства мокрого метода производства цемента:
- Понижение технологических затрат на измельчение сырьевой базы – глина и мел прекрасно намокают в воде в бассейне при первичной обработке, в связи с чем измельчаются легче и проще.
- Транспортировка, усреднение, корректировка шлама осуществляются проще, безопаснее с точки зрения экологии, особенно в сравнении с аналогичными процессами при производстве цемента сухим способом.
- Намного меньше образуется пыли.
- Печи обжига по конструкции простые, надежные, обладают высоким коэффициентом использования пространства (варьируется в пределах 0.89-0.91).
- Есть возможность использовать в производстве компоненты с достаточно «пестрым» (разным) химическим составом, а также обеспечена хорошая гомогенизация шлама.
Недостатки
Недостатков в мокром методе производства цемента мало, но они есть и не учитывать их нельзя.
Основные минусы мокрого метода производства цемента:
- Высокий удельный расход тепловой энергии в процессе обжига сырья. Сырье, которое поступает для обжига, обладает в среднем влажностью до 45%. И для испарения влаги, правильного прогрева компонентов необходимо до 6800 кДж/кг тепловой энергии либо 35% тепловой мощности печи. В связи с такими расчетами часть обжиговой печи функционирует в качестве сушильного агрегата с последующими сложностями.
- Высокий уровень материалоемкости печей для обжига наряду с не очень большой производительностью.
Указанные недостатки приводят к достаточно низкой производительности труда, существенным эксплуатационным и технологическим расходам, что обуславливает высокую стоимость всего производства.
Сухая технология производства
Сухой способ производства цемента использует другую технологическую схему. Известняк и глина, которые добывают из карьера, дробятся и отправляются в сепараторную мельницу. Тут они смалываются, смешиваются, сушатся. Полученную смесь доставляют в смесительные аппараты, окончательно перемешивают с использованием сжатого воздуха. Сейчас же корректируется и химический состав цемента.
При применении глинистого компонента сырье подают для смешивания в шнеки, где частично увлажняют водой. Создаются прочные гранулы со влажностью максимум 14%, потом они поступают для обжига в печь.
Обжиг сырья при сухом методе может осуществляться в разных печах – в данном случае особое внимание обращают на приготовление сырья. А дальнейшие этапы производства сходны с мокрым методом.
Плюсы технологии
В сравнении с мокрым, сухой метод обладает некоторыми преимуществами, которые обязательно нужно учитывать при расчетах (когда планируется организовать бизнес по производству цемента, к примеру).
Главные достоинства сухого метода:
- Сравнительно невысокий удельный расход энергии тепла на обжиг клинкера – в пределах 2900-3700 кДж/кг.
- Объем печных газов меньше на 30-40%, их можно вторично применять для сушки сырья и значительно снизить энергозатраты на создание клинкера, уменьшить затраты на обеспыливание.
- Значительно меньшая металлоемкость печей для обжига при повышенной производительности в сравнении с мокрой технологией. Мощность печей при «сухом» методе составляет 3000-5000 тонн в сутки, что больше в 1-2 раза аналогичного оборудования мокрого метода.
- Нет необходимости в мощных источниках воды.
Минусы технологии
Несмотря на явные преимущества, есть у технологии и свои минусы.
Какие недостатки есть у сухого метода производства цемента:
- Значительно больше выделяется пыли, что усложняет соблюдение санитарных норм, правил охраны окружающего пространства.
- Сложность конструкции печей для обжига и их требовательность в плане колебаний химического состава сырья, его степени влажности, дисперсности.
- Сравнительно низкий коэффициент использования печей – где-то 0.
7-0.8.
Отличия мокрой технологии производства от сухой
Обе технологии производства цемента обладают своими нюансами, плюсами и минусами. Но есть ключевые особенности, которые необходимо учитывать в первую очередь при планировании бизнеса и просчете расходов, прибыли. Главный недостаток мокрого метода производства цемента – существенная энергоемкость всего процесса, которая отражается соответствующим образом на цене конечного продукта в сторону повышения.
Сухая же технология менее экологична и опасна для окружающей среды, в связи с чем требует значительных расходов на устранение этого фактора. При этом, сам процесс производства обходится дешевле по всем пунктам, позволяет понизить цену конечного продукта.
Особенности полусухого способа
Полусухой метод производства цемента достаточно схож с сухим, но предполагает некоторые отличия. Фракция сырья, что проходит стадию гранулирования, равна примерно 10-20 миллиметрам, уровень влажности 11-16%. Сначала сырье обжигают в печах Леполь, потом создавшиеся гранулы отправляют в конвейерный кальцинатор.
Из печи выходят газы, проходящие сквозь гранулы, находящиеся на решетке. Таким образом сырье нагревается до 900 градусов, полностью высушиваясь в процессе. Такая термообработка способствует декарбонизации смеси примерно на 25-30%, что нужно для производства. После сырье отправляют в печь – это завершающий этап производства цемента.
Гранулированный цемент может обжигаться и в шахтных печах – в таком случае гранулирование осуществляется с частицами угля, после чего цемент уходит на хранение.
Комбинированный метод производства
Данный способ базируется на подготовке компонентов сырья по мокрому методу, а вот их обжиг осуществляется по схеме полусухого метода. Шлам, полученный в сырьевой мельнице, обладает влажностью в диапазоне 30-45%, он отправляется в фильтр: тут обезвоживается до уровня влажности в 15-20%, потом сырье смешивают с пылью, влажность доводят до показателя в 12-14%.
На следующем этапе смесь отправляется на обжиг, который осуществляется в печах полусухого способа изготовления цемента. Все остальные операции ничем не отличаются от аналогичных этапов мокрого метода производства.
Подходящий метод производства цемента выбирают в соответствии с технологическими и технико-экономическими факторами – качеством и типом сырья, влажностью и однородностью смеси, наличием соответствующего оборудования, возможностей и т.д. В Москве заводы работают по всем трем схемам и поставляют на рынок цемент высокого качества.
Способы производства цемента — Завод строительных смесей «ВосЦем»
Процесс производства цемента состоит из следующих основных технологических операций: добычи сырьевых материалов; приготовления сырьевой смеси, обжига сырьевой смеси и получения цементного клинкера; помола клинкера в тонкий порошок с небольшим количеством некоторых добавок.
В зависимости от способа подготовки сырья к обжигу различают мокрый, сухой и комбинированный способы производства цементного клинкера.
При мокром способе производства измельчение сырьевых материалов, их перемешивание, усреднение и корректирование сырьевой смеси осуществляется в присутствии определенного количества воды. А при сухом способе все перечисленные операции выполняются с сухими материалами. Мокрый способ приготовления сырьевой смеси применяют, когда физические свойства сырьевых компонентов (пластичной глины, известняка, мела с высокой влажностью и т.д.) не позволяют организовывать экономичный технологический процесс производства сырьевой смеси по сухому способу производства. При комбинированном способе сырьевую смесь приготовляют по мокрому способу, затем ее максимально обезвоживают (фильтруют) на специальных установках и в виде полусухой массы обжигают в печи. Каждый из перечисленных способов имеет свои достоинства и недостатки.
Способ производства цемента выбирают в зависимости от технологических и технико-экономических факторов: свойств сырья, его однородности и влажности, наличия достаточной топливной базы и др.
Мокрый способ производства цемента.
Сухой способ производства цемента.
Комбинированный способ производства цемента.
Производство цемента складывается в основном из следующий операций: добыча сырья; приготовления сырьевой смеси, состоящего из дробления и ее гомогенизации; обжига сырьевой смеси; помола обожженного продукта (клинкера) в тонкий порошок.
Существуют два основных способа производства – мокрый и сухой. При мокром способе производства сырьевую смесь измельчают и смешивают сырьевые материалы с водой. Получаемая сметанообразная жидкость – шлам – содержит 32-45% воды. По сухому способу сырьевые материалы предварительно высушивают, а затем измельчают и смешивают. Полученный тонкий порошок называют сырьевой мукой.
В зависимости от физических свойств исходных материалов и ряда других факторов при получении цемента по мокрому способу применяют разные схемы производства. Схемы эти отличаются одна от другой только способом приготовления сырьевой смеси. Приводим схему производства цемента по мокрому способу из твердого материала — известняка — и мягкого — глины.
При трехкомпонентной сырьевой смеси корректирующую добавку дробят, после чего она попадает в бункер, откуда вместе с известняком поступает в мельницу. Глину до болтушки пропускают через валковую дробилку. Сырьевые материалы дозируют перед мельницей специальными питателями.
Если при производстве по мокрому способу сырьевую смесь составляют из одних твердых материалов — известняка, мергелей и глинистых сланцев, то их дробят в дробилках без добавки воды и размалывают совместно в мельнице, куда добавляют воду. В том случае в схеме отсутствует болтушка. При изготовлении цемента из одних мягких материалов (мела, глины, мягких мергелей) сырье измельчают в болтушках, после чего размалывают в более коротких шаровых мельницах. В этом случае воду добавляют в первой стадии процесса и материалы дозируют перед ,поступлением в болтушки.
При сухом способе производства выбор схемы зависит от рода поставляемого топлива, физических свойств сырья, мощности завода и ряда других факторов. При использовании для обжига клинкера угля с большим содержанием летучих обжиг ведут во вращающихся печах, — если же применяют топливо с малым содержанием летучих — то в шахтных.
Так как при соприкосновении мелкого порошка, образующегося при помоле, с влагой материала образуется пластичная масса, которая налипает на внутреннюю поверхность агрегата и препятствует дальнейшему помолу, то дробленые сырьевые материалы с естественной влажностью размалывать нельзя. Поэтому после выхода из дробилки сырьевые материалы высушивают и затем направляют в мельницу, где перемалывают в тонкий порошок. Однородные по физическим свойствам материалы можно дробить и сушить в одних и тех же аппаратах. В случае применения гранулированного шлака его подсушивают без предварительного дробления. Помол и сушку сырьевой смеси целесообразно вести одновременно в одном аппарате-мельнице — в том случае, если влажность сырьевых материалов не превышает 8-12%, например, при использовании известняков и глинистых сланцев. Если в качестве сырья используется непластичный глинистый компонент, то при сухом способе производства обжиг ведут только во вращающихся печах. При пластичном глинистом компоненте можно вести обжиг, как во вращающихся печах, так и в шахтных печах. В последнем случае сырьевую смесь вначале увлажняют в смесительных шнеках водой до 8-10%-ной влажности. Затем массу подают в грануляторы, где она вместе с дополнительно подводимой водой превращается в гранулы с влажностью 12-14%. Эти гранулы и поступают в печь.
При обжиге клинкера на газообразном или жидком топливе схема производства упрощается, так как отпадает необходимость в приготовлении угольного порошка.
В ряде случаев может оказаться целесообразным комбинированный способ производства, при котором сырьевая смесь в виде шлама, полученного при обычном мокром способе производства, подвергается обезвоживанию и грануляции, а затем обжигается в печах, работающих по сухому способу.
Выбор сухого или мокрого способа производства зависит от многих причин. Как тот, так и другой способ имеют ряд преимуществ и недостатков. При мокром способе легче получить однородную (гомогенизированную) сырьевую смесь, обуславливающую высокие качества клинкера. Поэтому при значительных колебаниях в химическом составе известнякового и глинистого компонента он целесообразнее. Этот способ используется и тогда, когда сырьевые материалы имеют высокую влажность, мягкую структуру и легко диспергируются водой. Наличие в глине посторонних примесей, для удаления которых необходимо отмучивание, также предопределяет выбор мокрого способа. Размол сырья в присутствии воды облегчается, и на измельчение расходуется меньше энергии. Недостаток мокрого способа — больший расход топлива. Если используют сырьевые материалы с большой влажностью, то расход тепла, затрачиваемого на сушку и обжиг, при сухом способе будет мало отличаться от расхода тепла на обжиг шлама при мокром способе. Поэтому сухой способ производства целесообразнее при сырье со сравнительно небольшой влажностью и однородным составом.
Он же практикуется в случае, если в сырьевую смесь вместо глины вводят гранулированный доменный шлак. Его же применяют при использовании натуральных мергелей и тощих сортов каменного угля ,с малым содержанием летучих, сжигаемых в шахтных печах.
При изготовлении сырьевой смеси по любому способу необходимо стремиться к наиболее тонкому помолу, теснейшему смешению сырьевых материалов и к возможно большей однородности сырьевой смеси. Все это гарантирует однородность выпускаемого продукта и является одним из необходимых условий нормальной эксплуатации завода. Резкие колебания химического со·става сырьевой смеси нарушают ход производственного процесса. Высокая тонкость помола и совершенное смешение необходимы для того, чтобы химическое взаимодействие между отдельными составными частями сырьевой смеси прошло до конца в возможно более короткий срок.
При выборе той или другой схемы производства особое внимание следует обращать на рентабельность работы предприятия и возможность снижения себестоимости продукции. Основными мероприятиями, ведущими к снижению себестоимости являются: интенсификация производственных процессов, повышение коэффициента использования оборудования, рост выпуска цемента, повышение его качества (марки), снижение расхода топлива и электроэнергии, механизация производственных процессов и всех вспомогательных работ, автоматизация управления производственными процессами и некоторые другие.
Мощность цементных заводов устанавливают в зависимости от сырьевой базы и потребности района в цементе. На новых заводах она равна обычно 1-2 млн. т цемента в год. Характерным показателем производительности труда на цементных заводах является выпуск цемента на одного рабочего в год, который в 1963 г. составил 915 т. Выработка на одного работающего была 7-62 т. На заводах, оснащенных высокопроизводительным оборудованием, выработка цемента достигла соответственно 2000 и 1600 т.
На цементных заводах, а также на заводах по производству других вяжущих материалов приходится перемещать от одного аппарата к другому большие массы кускового порошкообразного и жидкого материала. Для транспортирования их применяют ковшовые элеваторы, шнеки, ленточные, пластинчатые и скребковые транспортеры, транспортные желоба, насосы, краны с грейферами. Для транспортирования порошкообразных материалов широко используют пневмовантовые и камерные насосы, а также пневмотранспортные желоба.
Транспортирование шлама имеет ряд особенностей, так как он представляет собой сметанообразную текучую массу, содержащую 32-45% воды. Чтобы уменьшить расход топлива на обжиг, стремятся снизить влажность шлама, а чтобы улучшить его транспортабельность, необходимо увеличить содержание воды. По условиям транспортабельности шлам должен течь по желобу, имеющему уклон в 2-4 %. Чем пластичнее сырьевые материалы, тем больше приходится добавлять воды для получения шлама нужной текучести. Обычно шлам транспортируется центробежными насосами.
На заводы сырьевые материалы доставляют из карьера в виде кусков размерами до 1000-1200 мм. Иногда сырьевые отделения расположены непосредственно на карьерах, откуда шлам поступает на заводы. Так, на Балаклейском цементном заводе отделение болтушек размещено на карьере. Сырьевые материалы в виде мела и глины поступают в дробилки, а затем в болтушки. Полученный глиняно-меловой шлам нормальной влажности перекачивается по шламопроводам на завод.
При выпуске цемента обычных марок сырьевые материалы и клинкер размалываются до остатка на сите №008 порядка 8-10%. Для получения цемента более высоких марок материалы размалываю тоньше — до остатка на том же сите около 5% и даже меньше. Измельчать сырьевые материалы до получения тонкого порошка в одном аппарате невозможно. Поэтому сначала материал подвергают в дробилках двyx — тpex стадийному дроблению до величины кусков, не превышающей 8-20 мм, а затем измельчают в мельницах в гонкий порошок с размерами зерен не более 0,06-0,10 мм, глину поступающую из карьера в кусках размером до 500 ММ, измельчают в валковых дробилках до кусков не больше 100 мм, а затем отмучивают в болтушках до получения глиняного шлама с влажностью 60-70%. Этот шлам и подают в сырьевую мельницу.
Удельный расход сырья зависит от его химического состава и зольности топлива и составляет 1,5-2,4 т на 1 т клинкера. Расход электроэнергии на 1 т выпускаемого цемента составляет 80-100 квт/ч.
Чем мокрый способ производства цемента отличается от сухого?
Так называемые «мокрая» и «сухая» технология производства цемента являются самыми распространенными способами получения этого незаменимого строительного материала.
СодержаниеСвернуть
- Отличия мокрой технологии производства цемента от сухой
- «Мокрая» технология производства связующего
- Преимущества «мокрой» технологии
- Недостатки
- «Сухая» технология производства связующего
- Преимущества «сухой» технологии
- Недостатки
Российские цементные заводы используют преимущественно «мокрый» метод, в то же время практически все зарубежные производители связующего работают по «сухой технологии».
Отличия мокрой технологии производства цемента от сухой
Обе технологии имеют свои преимущества и свои недостатки. Основной недостаток, которым отличается мокрый способ производства цемента – значительная энергоемкость процесса, отражающаяся на себестоимости конечного продукта. Сухая технология отличается большей экологической опасностью и соответственно большими капитальными затратами на устранение данного фактора. Рассмотрим оба способа производства цемента подробнее.
«Мокрая» технология производства связующего
Технологическая схема мокрого способа предусматривает раздельную первичную обработку компонентов клинкера. Измельченные «ингредиенты» загружаются в специальное оборудование для кратковременной выдержки под слоем воды. После этого компоненты клинкера, мокрыми, попадают в специальные мельницы, где их перемалывают до состояния порошка и тщательно перемешивают.
Подготовленный таким образом шлам подается в вертикальные и горизонтальные «шлюмбассейны» на корректировку необходимого соотношения «ингредиентов». Следующей технологической операцией идет печной обжиг откорректированного шлама и охлаждение промышленными холодильными установками. Полученный таким образом клинкер измельчается до мелкодисперсного порошка – цемента. Далее производятся: лабораторный анализ на соответствие цемента требованиям ГОСТ, фасовка и отправка потребителю.
Преимущества «мокрой» технологии
- Меньшие технологические затраты на измельчение сырья. Такие компоненты как мел и глина хорошо размокают в воде при первичной обработке в бассейнах. Соответственно процесс их измельчения происходит намного проще и легче;
- Транспортировка, усреднение и корректировка шлама происходит проще и экологически безопаснее, чем аналогичные операции при сухой технологии;
- В разы меньшее пылеобразование;
- Конструкция печей обжига шлама проста, надежна и имеет высокий Коэффициент Использования пространства – от 0,89 до 0,91;
- Имеется принципиальная возможность использовать сырьевые компоненты «пестрого» химсостава и хорошей гомогенизации шлама.
Недостатки
- Большой удельный расход тепловой энергии на обжиг сырья для производства цемента.
Сырье поступающее на обжиг, имеет среднюю влажность 35-45%. Соответственно для испарения влаги и прогрев компонентов требуется порядка 5 450-6 800 кДж/кг тепловой энергии или 35% тепловой мощности печи. Поэтому часть обжиговой печи работает как сушильный агрегат со всеми вытекающими «неприятностями»;
- Высокая материалоемкость обжиговых печей при небольшой производительности.
Указанные недостатки выливаются в относительно низкую производительность труда, значительные технологические и эксплуатационные расходы, обуславливающие относительно высокую себестоимость производства.
«Сухая» технология производства связующего
В этом случае основное производственно-технологическое оборудование аналогично мокрому способу. Изменения заключаются в принципиально иной технологической схеме производства клинкера. После предварительного измельчения компоненты клинкера подаются в сушильные барабаны, причем каждый компонент подается в отдельный барабан. После сушки «ингредиенты» перемешиваются и поступают в общую мельницу для дальнейшего измельчения и ввода присадок.
Следующая операция обусловлена видом и влажностью глины. Все остальные компоненты корректируются по указанным параметрам глины. Суть операции заключается в незначительном увлажнении (не более 13% влажности) шлама и последующую подачу на обжиг. Соответственно небольшой влажности энергетические затраты на обжиг небольшие, а печи менее металлоемки и менее габаритны. Операции, следующие после обжига шлама, аналогичны предыдущему способу производства цемента.
Преимущества «сухой» технологии
- Относительно невысокий удельный расход тепловой энергии расходуемой на обжиг клинкера – 2 900-3 700 кДж/кг;
- Меньший на 30-40% объем печных газов при аналогичной производительности и возможность их вторичного использования для сушки компонентов. Это позволяет существенно снизить энергозатраты на производство клинкера и требует меньших капиталовложений на обеспыливание;
- Относительно меньшая металлоемкость обжиговых печей при большей производительности по сравнению с «мокрой» технологией.
Производственная мощность печей при «сухом» способе – от 3 000 до 5 000 тонн продукта в сутки, что на 100-200% мощнее аналогичного оборудования работающего по «мокрой» технологии;
- Отсутствует необходимость в наличии мощных источников технологической воды.
Недостатки
- В разы большее пылевыделение, обуславливающее сложность обеспечения санитарных норм и охрану окружающего пространства;
- Относительная сложность конструкции обжиговых печей;
- «Капризность» обжиговых печей по отношению колебаний химсостава сырья, его дисперсности и степени важности;
- Относительно низкий Коэффициент Использования печей – от 0,7 до 0,8;
Более высокая трудоемкость энергоемкость на помол компонентов, обусловленные их низкой влажностью.
Производство цемента с помощью сухого и влажного процесса
Содержание
- Производство цемента с помощью сухого и влажного процесса
- Производство цемента
- Process
- Смешивание сырья:
- Dry Process
Производство цемента
При производстве цемента выполняются следующие три важные и различные операции :
- Смешивание Сырье .
- Сжигание
- Шлифовка
Процесс производства цемента зависит от метода смешивания сырья. Следовательно, на основе смешивания сырья процессы могут быть классифицированы как:
- ВЛАЖНЫЙ ПРОЦЕСС
- СУХОЙ ПРОЦЕСС
Обычно используется мокрый процесс.
Сырье, используемое для производства цемента, содержит следующие материалы:
- ИЗВЕСТЬ ( т.е. мел состоит из известняка.)
- ГЛИНИСТЫЕ ( т.е. глина состоит из силикатов глинозема.)
Производство цемента мокрым способом
МОКРЫЙ ТЕХНОЛОГКогда сырье мягкое, предпочтительно использовать мокрый способ. Цемент производится по следующей процедуре:
Смешивание сырья:- В мокром процессе используются два сырья e. известняковые и глинистые. Первоначально известковые материалы измельчаются с помощью дробилок, а глинистые материалы промываются водой в контейнере.
- После пересечения линии камни хранятся в силосах, так же глина после промывки хранится в тазах.
- Измельченные материалы из различных силосов и резервуаров направляются в правильных пропорциях в канал, называемый мельницами мокрого измельчения. Оба материала тщательно смешиваются в присутствии воды с образованием тонкой тонкой пасты, известной как суспензия
- Затем навозная жижа хранится в другом бункере, который можно назвать бункером для навозной жижи, где она постоянно перемешивается. Состав сырья еще раз проверяется и при необходимости корректируется добавлением глины или меловых материалов по желанию.
Обжиг: В этой операции шлам напрямую подается в длинный наклонный стальной цилиндр, называемый вращающейся печью. В этой печи есть 3 различные зоны, показанные на рис. ниже
Блок-схема процесса производства цемента
(i) Зоны сушки: При мокром процессе зона сушки сравнительно больше, чем при сухом процессе. Это связано с тем, что сырье в виде суспензии подается непосредственно в печь, в которой больше воды. Как показано на рисунке, это верхняя часть печи. В этой зоне вода испаряется при температуре 100-400°С.
(ii) Формирование модулей : По мере того как шлам постепенно опускается в печь, двуокись углерода из шлама испаряется и образуются небольшие комки, которые можно назвать модулями.
(iii) Зона обжига:- Модули поступают в эту зону, где поддерживается температура около 1400-1500°C. Модули превращаются в темно-зеленоватые шарики, а продукт, получаемый в печи, известный как клинкер, имеет различные размер от 5 до 20 мм. Клинкер выходит из этой зоны очень горячим.
(iv) Охлаждение клинкеров:- Как показано на рисунке, в противоположном направлении установлена еще одна вращающаяся печь, которая также наклонена. Используется для охлаждения клинкеров примерно до 90°С.
Измельчение: Охлажденные клинкеры тонко измельчаются в шаровых или трубчатых мельницах.
Также при помоле добавляется гипс около 2-4%. Гипс действует как замедлитель схватывания и, таким образом, позволяет цементу смешиваться с песком или заполнителем и укладываться на нужное место. т.е. увеличивает начальное время схватывания цемента.
Хранение и упаковка: По мере выхода цемента из мельниц он собирается в бункер и подается в ковшовый элеватор для хранения в силосах.
Цемент из силосов упаковывается машинами в мешки. Каждый мешок цемента содержит 50 кг или 0,035 м 3 цемента.
Теперь давайте рассмотрим производство цемента сухим способом
СУХОЙ ПРОЦЕСС
Этот процесс используется, когда доступное сырье достаточно твердое. Цемент по этому способу можно приготовить, используя следующие операции:
- Смешивание сырья
- Выжигание и шлифовка
Смешивание сырья: Сырье , т.е. глинистые и известняковые материалы, проходят следующие этапы:
- Дробление: Сырье, прежде всего, дробят в дробилках на мелкие фрагменты, различающиеся по размеру.
размер.
- Сушка: Измельченные материалы сушат нагреванием при достаточно высокой температуре. Это может быть сделано в сушильных печах.
- Уменьшение размера: Материалы для сушки затем измельчаются с помощью шаровых мельниц и трубчатых мельниц, чтобы уменьшить размер материалов для получения порошка.
- Смешивание в правильной пропорции: Тонко высушенные материалы смешиваются в точных пропорциях. Смешивание может производиться либо механическим, либо пневматическим способом (, например, , нагнетаемым под давлением).
Обжиг и измельчение: Эти операции такие же, как и при мокром способе. За исключением смешивания сырья. При сухом процессе сырье смешивают, измельчают и затем подают в печь, тогда как при мокром процессе сырье измельчают отдельно, а затем непосредственно смешивают в правильной пропорции в присутствии воды, чтобы получить тонкую жидкую пасту, известную как Суспензия.
пройти тест
Обязательно прочтите Другие полезные статьи
- Свойства цемента
- Типы цемента
- Состав цементного клинкера
- Гидратация цемента
- Продукты гидратации цемента
- Что такое цемент?
- Различные испытания цемента
- Обыкновенный портландцемент (OPC)
- Производство цемента сухим и мокрым способами
- Сырье для цемента
- История цемента в строительстве
- Состав цементного клинкера
- Обыкновенный портландцемент (OPC)
- Что такое бетон с определением и историей
Производство портландцемента – материалы и процесс
🕑 Время чтения: 1 минута
Производство цемента включает в себя различные виды сырья и процессы. Каждый процесс объясняется химическими реакциями для производства портландцемента.
Цемент представляет собой порошок зеленовато-серого цвета, изготовленный из прокаленных смесей глины и известняка. При смешивании с водой становится твердым и прочным строительным материалом. История цемента восходит к Римской империи. Современный цемент. То есть портландцемент впервые был произведен британским каменщиком Джозефом Аспдином в 1824 году, который варил цемент на своей кухне. Он нагрел смесь известняка и глиняного порошка на своей кухне и измельчил смесь в порошок, создав цемент, который затвердевает при смешивании с водой. Название Портленд было дано изобретателем, так как оно напоминает камень, добытый на острове Портленд.
Первое использование современного портландцемента было при строительстве туннеля на реке Темзе в 1828 году.
Состав:
- Процесс производства цемента
- 1. Смешивание сырья
- Сравнение сухого и мокрого процессов производства цемента
- 2. Обжиг сырья 90 0 9 0 8 Измельчение клинкеров Хранение и упаковка
Процедуры производства портландцемента описаны ниже.
- Смешивание сырья
- Сжигание
- Шлифовка
- Хранение и упаковка
1. Смешивание сырья
Основным сырьем, используемым в производстве цемента, являются кальций, кремний, железо и алюминий. Эти полезные ископаемые используются в различной форме согласно доступности полезных ископаемых. В таблице представлено сырье для производства портландцемента. Процедура смешивания при производстве цемента осуществляется 2 методами,
- Сухой процесс
- Мокрый процесс
Как известняковое, так и глинистое сырье сначала измельчают в гирационных дробилках, чтобы получить отдельные куски размером 2-5 см. Измельченные материалы снова измельчают, чтобы получить мелкие частицы в шаровой или трубчатой мельнице.
Каждый мелкоизмельченный материал хранится в бункере после просеивания. Теперь эти порошкообразные минералы смешиваются в необходимой пропорции, чтобы получить сухую сырьевую смесь, которая затем хранится в силосах и готовится к отправке во вращающуюся печь. Теперь сырье смешивают в определенных пропорциях, чтобы средний состав конечного продукта сохранялся должным образом.
Рис. Производство цемента сухим способом
b) Мокрый способСырье сначала измельчают, превращают в порошок и хранят в силосах. Затем глину промывают в промывочных мельницах для удаления прилипших органических веществ, содержащихся в глине. Порошкообразный известняк и промытая водой глина направляются в каналы и передаются в мельницы, где они полностью смешиваются и образуется паста, т. е. известная как шлам. Процесс измельчения может осуществляться в шаровой или трубчатой мельнице или даже в обеих. Затем суспензия направляется в сборный бассейн, где можно регулировать состав. Шлам содержит около 38-40% воды, которая хранится в резервуарах для хранения и хранится готовой к отправке во вращающуюся печь.
Рис. Производство цемента мокрым способом
Сравнение сухого и мокрого способов производства цемента
Критерии | Сухой процесс | Мокрый процесс |
Твердость сырья | Довольно твердый | Любой вид сырья |
Расход топлива | Низкий | Высокий |
Время обработки | Малый | Высшее |
Качество | Низкое качество | Высшее качество |
Себестоимость | Высокий | Низкий |
Общая стоимость | Дорого | Дешевле |
Физическое состояние | Сырая смесь (твердая) | Шлам (жидкий) |
2.
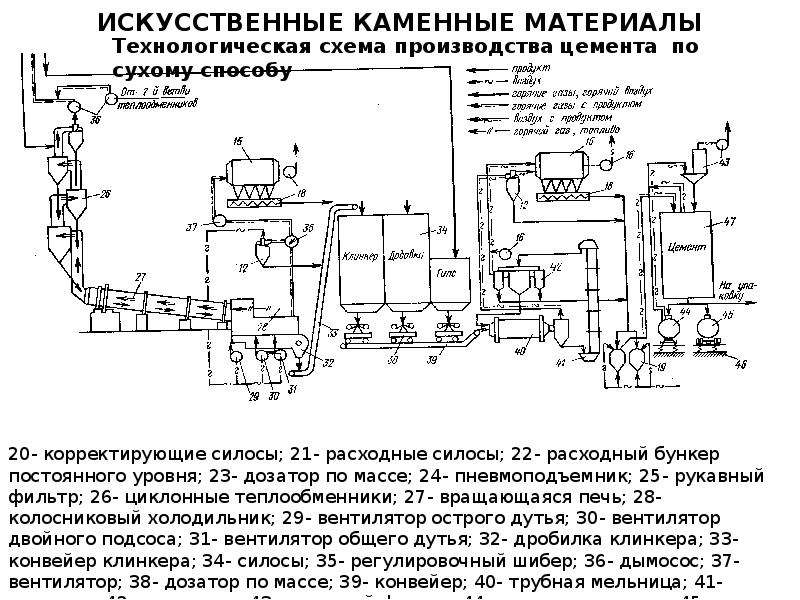
Процесс обжига осуществляется во вращающейся печи, при этом сырье вращается со скоростью 1-2 об/мин вокруг своей продольной оси. Вращающаяся печь состоит из стальных труб диаметром 2,5-3,0 метра и длиной от 90 до 120 метров. Внутренняя сторона печи облицована огнеупорным кирпичом.
Печь опирается на колонны из каменной кладки или бетона и опирается на подшипник качения в слегка наклонном положении с уклоном от 1:25 до 1:30. верхний конец. Печь нагревается с помощью порошкообразного угля или масла или горячих газов из нижнего конца печи, так что образуется длинное горячее пламя.
Поскольку положение печи наклонно и она медленно вращается, материал, загружаемый с верхнего конца, перемещается к нижнему концу со скоростью 15 м/ч. В верхней части вода или влага из материала испаряется при температуре 400°C, поэтому этот процесс известен как зона сушки.
Центральная часть, т.е. зона прокаливания, температура около 10000С, где происходит разложение известняка. Остальной материал находится в форме небольших комочков, известных как узелки после CO 2 освобожден.
CaCO 3 = CaO + CO 2
Нижняя часть (зона спекания) имеет температуру 1500-17000°С, где известь и глина реагируют с образованием алюминатов кальция и силикатов кальция. Эти алюминаты и силикаты кальция сплавляются, образуя мелкие и твердые камни, известные как клинкеры. Размер клинкера варьируется от 5 до 10 мм. Нижняя часть, т.е. зона клинкера, имеет температуру около 1500-1700°С. В этом районе известь и глина реагируют с образованием алюминатов кальция и силикатов кальция. Эти продукты алюминатов и силикатов кальция сплавляются вместе, образуя твердые и мелкие камни, известные как клинкеры. Размер мелких и твердых клинкеров варьируется от 5 до 10 мм.
2CAO + SIO 2 = CA2SIO 4 (DECKEAM SILICET (C 2 S)
3CAO + SIO 2 = CA3SIO 5 (TRAL LILES 3CAO + AL 2 O 3 = CA 3 AL 2 O 6 (DICALCIUM ALUMINIT O 3 = Ca 4 Al 2 Fe 2 O 10 (алюмоферрит тетракальция (C 4 AF))
Клинкер, поступающий из зоны обжига, очень горячий. Для снижения температуры клинкеров воздух поступает в противотоке у основания вращающейся печи. Охлажденные клинкеры собираются в небольшие тележки.
3. Измельчение клинкеров
Охлажденные клинкеры получают из охладителей и отправляют на мельницы. Клинкер тонко измельчают в порошок в шаровой или трубчатой мельнице. Порошкообразный гипс добавляется в количестве 2-3% в качестве замедлителя схватывания во время окончательного измельчения. Конечным продуктом является цемент, который не оседает быстро при контакте с водой. После начального времени схватывания цемента цемент становится жестким, а гипс замедляет растворение трехкальциевых алюминатов, образуя трехкальциевый сульфоалюминат, который является нерастворимым и предотвращает слишком ранние дальнейшие реакции схватывания и твердения.
3CAO.AL 2 O 3 + XCASO 4 .7H 2 O = 3CAO.AL 2 O 3 . XCASO 4 O 3 . Хранение и упаковка
Измельченный цемент хранится в силосах, откуда он продается либо в контейнерах, либо в мешках по 50 кг.
2 Процесс производства цемента – мокрый и сухой процессы производства цемента
Производство цемента осуществляется путем гомогенного смешивания сырья и его обжига при высоких температурах клинкера, после чего клинкер измельчается в мелкий порошок, т.е. обычный портландцемент.
Содержание
- Сырье для производства цемента
- Технологическая схема производства цемента
- Производство цемента сухим способом
- Процедура производства цемента сухим способом
- Технологическая схема производства цемента сухим способом
- 8 90 производства цемента
- Недостатки сухого способа производства цемента
- Химические реакции при производстве цемента:
- Производство цемента путем влажного процесса
- Процедура влажного процесса производства цемента
- Блок -схема из производства цемента путем влажного процесса
- Преимущества влажного процесса изготовления цемента
- Disvantage of Process of Cement Muppence
- Добавление Влажно — Гипс при производстве цемента
- Упаковка портландцемента
- Сравнение сухого и мокрого процессов производства цемента
- Ключевые выводы
- Часто задаваемые вопросы
Сырье для производства цемента
Два основных сырья, используемых для производства обычного портландцемента.
Поскольку силикат кальция является основным компонентом цемента, материалы, содержащие кремнезем и кальций, требуются в больших количествах.
- Глинистые материалы – силикаты глинозема в виде глины, сланца, сланца, доменного шлака и т. д.
- Известняковые материалы – горная порода, известняк, мергель, мел, морская ракушка и т. д.
- Вторичные материалы – бокситы, железная руда (иногда)
В глинистых минералах также присутствуют глинозем, окись железа и щелочи. Наличие этих дополнительных компонентов необходимо для образования цемента при сравнительно более низких температурах. Следовательно, если эти составляющие отсутствуют в глине, их добавляют отдельно.
Производство цемента Технологическая схема
Производство цемента сухим способом
Сухой способ производства цемента используется, когда сырье является твердым.
Дробление, измельчение и смешивание сырья осуществляются для гомогенизации компонентов перед их сжиганием.
Процедура производства цемента сухим способом
Ниже описаны различные этапы производства цемента сухим способом:
1. Измельчение и хранение
- дробилки.
- Затем измельчается в мелкий порошок в шаровых и трубчатых мельницах.
- Процесс дробления и измельчения осуществляется отдельно для каждого материала.
- После измельчения каждый из материалов хранится в бункерах.
2. Смешивание и хранение
- Затем сырье смешивается в правильных пропорциях в виде сухого порошка с помощью сжатого воздуха.
- Этот тонкоизмельченный порошок сырья называется сырьевой смесью.
- Сырьевая смесь хранится в резервуарах для хранения.
3. Обжиг и охлаждение
Прокаливание происходит во вращающейся печи, и образующийся конечный продукт называется клинкером.
- Затем сырьевая смесь подается во вращающуюся печь, состоящую из стальных труб.
- Сырьевая смесь подается в верхнюю часть печи, которая называется сухой зоной.
- Через нижний конец печи горячие газы и пламя проходят в печь.
- Вода из водной суспензии испаряется в самой сухой зоне.
- По мере того, как сырьевая смесь опускается во вращающуюся печь, температура продолжает расти. Поглощение влаги снижает схватывание цемента.
- Углекислый газ испаряется в следующей секции, образуя небольшие конкреции. Поглощение CO 2 увеличивает схватывание цемента.
- Затем конкреции достигают самой нижней части печи – зоны обжига. Здесь температура около 1500-1700°С. Прокаливание происходит в зоне обжига.
- Конкреции превращаются в твердые камни, называемые клинкерами, в зоне обжига.
- Эти клинкеры имеют размер около 5-10 мм и очень горячие, когда выходят из вращающейся печи.
- В противоположном направлении проложена небольшая вращающаяся печь для охлаждения для быстрого охлаждения клинкеров с сохранением метастабильных соединений и их твердых растворов.
Охлаждение клинкеров осуществляется в контролируемых условиях.
- Охлажденные клинкеры затем складируются.
4. Измельчение
- Клинкеры измельчают в шаровых и трубных мельницах после контролируемого охлаждения.
- Скорость охлаждения клинкеров влияет на набор прочности цемента.
- Около 3-5 % гипса добавляют во время помола к охлажденным клинкерам для предотвращения мгновенного схватывания.
- Измельчение в замкнутом цикле производится на трубных мельницах. Циклонный сепаратор обеспечивает правильное распределение частиц по размерам.
- После измельчения цемента в мелкий порошок он хранится в бункерах.
- Затем с помощью автомата цемент взвешивается и упаковывается в мешки по 50 кг.
- Объем 1 мешка цемента, т. е. 50 кг цемента имеет объем 0,035 м 3 .
Скорость охлаждения клинкеров влияет на прирост прочности цемента, что можно отметить из приведенной ниже таблицы:
Цемент Тип | Условия охлаждения | Прочность на сжатие МПа | ||
3 дня | 7 дней | 28 дней | ||
Нормальный цемент | Быстрый | 9,9 | 15,3 | 26 |
Умеренный | 9,7 | 21.![]() | 27 | |
Медленно | 9,7 | 19,3 | 24 | |
Очень медленно | 8,7 | 18,7 | 23 | |
Цемент высокой ранней прочности | Быстрый | 10.2 | 18,8 | 907:10 29|
Умеренный | 14.![]() | 26,7 | 33 | |
Медленно | 10.2 | 21.0 | 29 | |
Очень медленно | 9.1 | 18.1 | 28 |
Технологическая схема производства цемента сухим способом
Преимущества сухого способа производства цемента
- Повышение производительности труда
- Требуются небольшие капиталовложения
- Уменьшается потребление топлива
- Современные технологии могут помочь в надлежащем смешивании материалов в сухом виде
Недостатки сухого способа производства цемента
- медленный процесс
- Это дорого
- Производимый цемент имеет худшее качество, чем цемент, полученный мокрым способом
Химические реакции при производстве цемента:
Вышеуказанные четыре продукта являются основными составляющими цемента, а именно. трехкальциевый силикат, двухкальциевый силикат, трехкальциевый алюминат и четырехкальциевый алюмоферрит. Эти соединения известны как Bogues Compounds . Чтобы узнать, как эти соединения влияют на цемент и их свойства, ПРОЧИТАЙТЕ Основные компоненты цемента .
Производство цемента мокрым способом
Шлам, используемый в мокром процессе производства цемента, содержит 30-50% воды. Это увеличивает потребность в топливе.
Процедура мокрого процесса производства цемента
Ниже описаны различные стадии производства цемента мокрым способом:
Дробление и хранение
- Известняк и другие известняковые материалы измельчают и хранят в силосах или резервуарах для хранения.
- Глину и другие глинистые материалы тщательно смешивают с водой в промывочной мельнице и хранят в тазах.
- Известняковый щебень из бункера и влажная глина из бассейна затем падают в канал в определенных пропорциях.
- Каналы переносят эти материалы в мельницу, где они вступают в тесный контакт для образования суспензии. (Измельчение в трубчатой или шаровой мельнице)
- Шлам подается в корректировочный бассейн, где производится непрерывное перемешивание и корректировка химического состава. Постоянное перемешивание гарантирует, что суспензия останется однородной.
- Затем суспензия хранится в резервуарах для хранения при постоянном перемешивании, а затем подается во вращающуюся печь.
Обжиг, охлаждение и измельчение осуществляется так же, как и при сухом способе производства цемента. Они описаны здесь.
Технологическая схема производства цемента мокрым способом
Преимущества мокрого способа производства цемента
- Низкие затраты на выемку и измельчение сырья
- Можно получить точный контроль состава шлама
- 9000 можно сделать однородным
- Отдельная операция сушки не требуется
Недостатки мокрого способа производства цемента
- Высокий общий расход топлива
Добавление гипса при производстве цемента около 2-3%.

Гипс добавляется при производстве портландцемента для предотвращения мгновенного схватывания цемента. Гипс –
- Регулирует начальное время схватывания цемента
- В отсутствие гипса цемент схватывается сразу после контакта с водой.
- Таким образом, гипс действует как замедлитель схватывания цемента.
Упаковка портландцемента
Мелкоизмельченный цемент размером около 5-30 микрон, хранящийся в силосах, затем упаковывается. Фасовка производится в количестве 50 кг, что эквивалентно 0,035 м 3 объема.
В США один мешок цемента содержит 94 фунта, что эквивалентно 1 футу 3 .
Фасовка цемента производится в мешки:
- Мешки тканые из ПНД (полиэтилена высокой плотности)
- Мешки полиэтиленовые джутовые
- Бумажные четырехслойные мешки в зависимости от места хранения цемента срок службы цемента. Срок годности OPC обсуждается ЗДЕСЬ .
- Аргиллеозные материалы
- .
Цемент :
- Измельчение известняка и глины в дробилках и хранение в бункерах
- Измельчение измельченных материалов и хранение в бункерах
- Смешивание материалов сжатым воздухом в нужных пропорциях для образования сырьевой смеси
- Обжиг сырьевой смеси во вращающейся печи для образования клинкеров
- Контролируемое охлаждение горячих клинкеров в другой вращающейся печи
- Измельчение клинкеров в шарах и трубах мельницы после добавления 3-5 % гипса
- Цементный порошок хранится в силосах и транспортируется на упаковочные предприятия
Мокрый процесс Производство цемента :
- Измельчение известняка и глины в дробилках и хранение в силосах
- Смешивание глины с водой производится в промывочных мельницах и хранится в бассейнах
- Образование шлама в шаровой мельнице или трубной мельнице путем тщательного перемешивания обводненной глины с измельченным известняком
- Хранение шлама осуществляется в резервуарах для хранения при постоянном перемешивании
- Сжигание шлама во вращающейся печи с образованием клинкеров
- Контролируемое охлаждение горячих клинкеров в другой вращающейся печи
- Измельчение клинкера в шаровых и трубчатых мельницах после добавления 3-5 % гипса
- Цементный порошок хранится в силосах и транспортируется на упаковочные предприятия
Часто задаваемые вопросы
Что такое обычный портландцемент?
Когда глинистые и известняковые материалы измельчаются и тщательно смешиваются друг с другом путем их обжига при высоких температурах спекания с образованием клинкеров.
Затем клинкеры измельчают в мелкий порошок, который называется обычным портландцементом.
Чтобы узнать больше об использовании и применении OPC, НАЖМИТЕ Приложения OPC .
Какие два основных вида сырья используются для производства цемента?
- Известковые материалы
- Глинистые материалы
Что такое мокрый способ производства цемента?
- Сырье, глинистые и известняковые материалы сначала смачивают в промывочной мельнице и смешивают с водой в надлежащих пропорциях для образования суспензии.
- Затем суспензию направляют в корректировочный бассейн, где регулируют химические пропорции и постоянно перемешивают суспензию.
- Затем суспензия подается во вращающуюся печь при очень высокой температуре, где поглощаются вода и CO2.
- Образуются горячие клинкеры, которые затем быстро охлаждаются.
- После добавления гипса клинкер тонко измельчается.
- Мелкодисперсный порошкообразный портландцемент, хранящийся в бункерах.

На площадке цемент следует хранить с соблюдением нескольких мер предосторожности, иначе цемент станет непригодным для использования. Чтобы избежать потерь цемента из-за неправильного хранения, ПРОЧТИТЕ Меры предосторожности при хранении цемента .
Сравнение сухого и мокрого процессов производства цемента
СИ. № | Сухой процесс | Мокрый процесс |
1 | Материалы смешиваются в сухом виде | Материалы смешиваются во влажном виде (с добавлением воды) |
2 | Сырьевая смесь образуется после смешения материалов | Шлам образуется после смешивания материалов |
3 | Для производства 1 тонны цемента требуется 100 кг угля | Для производства 1 тонны цемента требуется 350 кг угля |
4 | Материалы должны быть высушены перед использованием | Сушка материала не требуется |
5 | Можно использовать более твердое сырье | Можно использовать любой тип материала |
6 | Высокая себестоимость производства | Понесена низкая себестоимость продукции |
7 | Качество производимого цемента сравнительно ниже | Цемент высшего качества выпускают |
Сходство | ||
1 | Шлам подается во вращающуюся печь для обжига | |
2 | Выполняется обжиг и охлаждение, а также измельчение |
Ключи на вынос
Сырье для Производство цемента :